Introduction to PCB Surface Finishes
When designing and manufacturing printed circuit boards (PCBs), one of the crucial decisions to make is choosing the appropriate surface finish. The surface finish not only protects the exposed copper traces from oxidation and corrosion but also plays a vital role in ensuring reliable solderability, enhancing the assembly process, and improving the overall performance and longevity of the PCB. With a variety of surface finish options available, it is essential to understand their characteristics, advantages, and limitations to make an informed decision based on your specific project requirements.
In this comprehensive article, we will delve into the world of PCB surface finishes, exploring the most common types, their properties, and their suitability for different applications. We will also discuss the factors to consider when selecting a surface finish and provide guidance on how to choose the best option for your PCB project.
Common Types of PCB Surface Finishes
1. Hot Air Solder Leveling (HASL)
Hot Air Solder Leveling (HASL) is one of the most widely used and cost-effective surface finishes in the PCB industry. The process involves immersing the PCB in a molten solder bath, typically consisting of a tin-lead alloy, and then using hot air to level the surface and remove excess solder. The resulting finish provides excellent solderability and protection against oxidation.
Advantages of HASL:
– Cost-effective and readily available
– Good solderability and wettability
– Suitable for through-hole components and wave soldering
– Provides a thick, durable coating
Disadvantages of HASL:
– Uneven surface due to the leveling process
– Not suitable for fine-pitch components or high-density designs
– Potential for solder bridging or shorts
– Contains lead, which may be restricted in certain applications
2. Electroless Nickel Immersion Gold (ENIG)
Electroless Nickel Immersion Gold (ENIG) is a popular choice for high-reliability and advanced PCB applications. The process involves depositing a layer of nickel onto the copper surface through an auto-catalytic chemical reaction, followed by a thin layer of gold deposited via immersion. ENIG offers excellent solderability, flatness, and durability.
Advantages of ENIG:
– Flat and uniform surface finish
– Excellent solderability and wettability
– Suitable for fine-pitch components and high-density designs
– Good shelf life and resistance to oxidation
– RoHS compliant (lead-free)
Disadvantages of ENIG:
– Higher cost compared to HASL
– Potential for “black pad” issue due to nickel corrosion
– Thinner gold layer may wear off over time
– Not ideal for press-fit connectors or insertion mount applications
3. Immersion Silver (IAg)
Immersion Silver (IAg) is a lead-free surface finish that offers a cost-effective alternative to ENIG. The process involves depositing a thin layer of silver onto the copper surface through a chemical displacement reaction. IAg provides good solderability and is compatible with a wide range of soldering processes.
Advantages of IAg:
– Cost-effective compared to ENIG
– Good solderability and wettability
– Suitable for fine-pitch components and high-density designs
– Efficient process with short immersion time
– RoHS compliant (lead-free)
Disadvantages of IAg:
– Limited shelf life due to silver tarnishing
– Potential for silver migration and dendrite growth
– Not recommended for high-sulfur environments
– May require additional handling and packaging precautions
4. Organic Solderability Preservative (OSP)
Organic Solderability Preservative (OSP) is a thin, organic coating applied to the copper surface to prevent oxidation and maintain solderability. OSP is a cost-effective and environmentally friendly option, as it eliminates the need for metallic coatings.
Advantages of OSP:
– Low cost and simple application process
– Environmentally friendly and RoHS compliant
– Suitable for fine-pitch components and high-density designs
– Good wettability and solderability
– Enables easy visual inspection of the copper surface
Disadvantages of OSP:
– Limited shelf life and susceptible to humidity
– May require additional cleaning steps before assembly
– Not recommended for multiple reflow cycles or rework
– Potential for inconsistent coating thickness
Factors to Consider When Selecting a PCB Surface Finish
When choosing the right surface finish for your PCB, several factors should be taken into account to ensure optimal performance, reliability, and compatibility with your manufacturing process and end-use application.
-
Solderability and Assembly Process: Consider the type of components and the soldering techniques used in your assembly process. Some surface finishes, such as HASL, are better suited for through-hole components and wave soldering, while others, like ENIG and IAg, are ideal for surface mount technology (SMT) and fine-pitch components.
-
Environmental Regulations and RoHS Compliance: If your PCB needs to comply with the Restriction of Hazardous Substances (RoHS) directive, lead-free surface finishes like ENIG, IAg, and OSP are preferable over HASL, which contains lead.
-
Shelf Life and Storage Conditions: Different surface finishes have varying shelf lives and storage requirements. For example, IAg and OSP are more sensitive to humidity and may require additional packaging and handling precautions compared to ENIG and HASL.
-
Cost and Budget Constraints: The choice of surface finish can significantly impact the overall cost of your PCB. HASL and OSP are generally more cost-effective options, while ENIG and IAg come with a higher price tag due to the use of precious metals and more complex processes.
-
Electrical Performance and Signal Integrity: For high-speed and high-frequency applications, the surface finish can affect signal integrity and impedance control. ENIG and IAg provide a smooth, uniform surface that minimizes signal loss and reflections.
-
Mechanical Properties and Durability: Consider the mechanical stress and wear that your PCB will be subjected to during its lifetime. ENIG and HASL offer better durability and resistance to mechanical damage compared to IAg and OSP.
-
Compatibility with Other Processes: Some surface finishes may have limitations or compatibility issues with certain processes, such as press-fit connectors or wire bonding. Ensure that the chosen surface finish is suitable for all the processes involved in your PCB Assembly and end-use application.
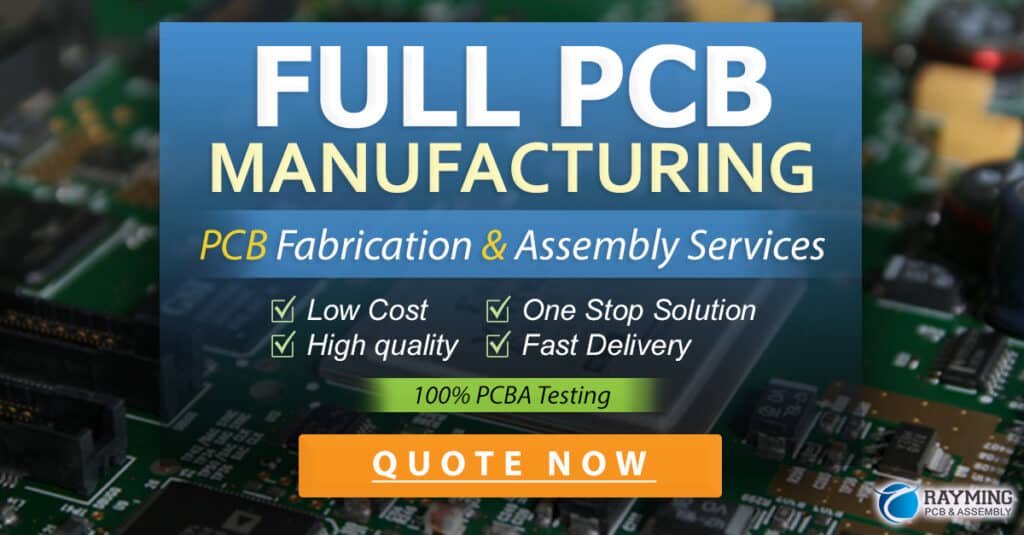
Comparison of PCB Surface Finishes
To help you make an informed decision, here is a comparison table of the four common PCB surface finishes discussed in this article:
Surface Finish | Solderability | RoHS Compliance | Shelf Life | Cost | Suitable for SMT |
---|---|---|---|---|---|
HASL | Good | No (contains lead) | Long | Low | Limited |
ENIG | Excellent | Yes | Long | High | Yes |
IAg | Good | Yes | Limited | Moderate | Yes |
OSP | Good | Yes | Limited | Low | Yes |
Frequently Asked Questions (FAQ)
-
Q: Can I mix different surface finishes on the same PCB?
A: While it is possible to use different surface finishes on the same PCB, it is generally not recommended. Mixing surface finishes can lead to compatibility issues, uneven soldering, and potential reliability problems. It is best to choose a single surface finish that meets all your requirements. -
Q: How does the surface finish affect the lead time of my PCB?
A: The choice of surface finish can impact the lead time of your PCB order. Some surface finishes, such as HASL and OSP, have shorter processing times compared to ENIG and IAg, which require additional steps and have longer processing times. However, the actual lead time depends on various factors, including the PCB manufacturer’s capacity and workload. -
Q: Can I apply a surface finish to a PCB with gold fingers?
A: Yes, you can apply a surface finish to a PCB with gold fingers. However, it is essential to mask the gold finger areas during the surface finish application process to prevent any contamination or alteration of the gold plating. The surface finish should be applied only to the exposed copper areas of the PCB. -
Q: How do I choose between ENIG and IAg for my high-density PCB?
A: Both ENIG and IAg are suitable for high-density PCBs and fine-pitch components. ENIG offers better durability, longer shelf life, and resistance to oxidation, making it a preferred choice for high-reliability applications. IAg, on the other hand, is more cost-effective and provides good solderability. The choice between the two depends on your specific requirements, budget, and end-use environment. -
Q: Can I rework or repair a PCB with an OSP surface finish?
A: Reworking or repairing a PCB with an OSP surface finish can be challenging. OSP is sensitive to heat and multiple reflow cycles, which can degrade the organic coating and affect solderability. If rework is necessary, it is recommended to remove the OSP coating from the affected area and reapply it after the repair is complete. However, it is always best to consult with your PCB manufacturer or assembly provider for specific guidance on reworking OSP-coated PCBs.
Conclusion
Selecting the right surface finish for your PCB is a critical decision that impacts the manufacturability, reliability, and performance of your electronic device. By understanding the characteristics, advantages, and limitations of common surface finishes like HASL, ENIG, IAg, and OSP, you can make an informed choice based on your project requirements, budget, and end-use application.
Remember to consider factors such as solderability, RoHS compliance, shelf life, cost, electrical performance, mechanical properties, and compatibility with other processes when evaluating surface finish options. Consult with your PCB manufacturer and assembly provider to discuss your specific needs and obtain recommendations tailored to your project.
By choosing the appropriate PCB surface finish, you can ensure the success of your PCB assembly, improve the reliability and longevity of your electronic device, and optimize your manufacturing process for better results.
Leave a Reply