Introduction to PCB Surface Finishes
Printed Circuit Boards (PCBs) are essential components in modern electronics, providing a platform for mounting and connecting electronic components. One crucial aspect of PCB design and manufacturing is selecting the appropriate surface finish. The surface finish on a PCB serves multiple purposes, including protecting the copper traces from oxidation, enhancing solderability, and improving the overall reliability of the board.
In this comprehensive article, we will delve into the world of PCB surface finishes, exploring the various options available, their characteristics, advantages, and disadvantages. By the end of this article, you will have a solid understanding of how to select the right surface finish for your specific PCB application.
The Importance of Choosing the Right PCB Surface Finish
Selecting the appropriate surface finish for your PCB is crucial for several reasons:
-
Solderability: The surface finish plays a vital role in ensuring good solderability, which is essential for reliable component attachment during the assembly process.
-
Protection: Surface finishes protect the exposed copper traces on the PCB from oxidation and contamination, thus maintaining the board’s integrity and performance over time.
-
Electrical Performance: Different surface finishes have varying electrical properties, such as conductivity and resistance, which can impact the overall performance of the PCB.
-
Compatibility: The choice of surface finish must be compatible with the components and assembly processes used in your specific application.
-
Cost: Surface finishes vary in cost, and selecting the most cost-effective option that meets your requirements is essential for maintaining budget constraints.
Common Types of PCB Surface Finishes
There are several types of surface finishes available for PCBs, each with its unique properties and advantages. Let’s explore some of the most common options:
1. Hot Air Solder Leveling (HASL)
HASL is one of the most widely used surface finishes in the PCB industry. In this process, the PCB is dipped into a molten solder bath, and then hot air is used to blow off the excess solder, leaving a thin, uniform layer on the exposed copper surfaces.
Advantages of HASL:
- Cost-effective
- Excellent solderability
- Good shelf life
- Compatible with a wide range of components
Disadvantages of HASL:
- Uneven surface due to solder dipping process
- Not suitable for fine-pitch components
- Potential for thermal shock during the dipping process
2. Electroless Nickel Immersion Gold (ENIG)
ENIG is a popular choice for high-reliability applications. In this process, a layer of nickel is deposited on the copper surfaces, followed by a thin layer of gold. The nickel layer provides a barrier against copper migration, while the gold layer offers excellent solderability and protection against oxidation.
Advantages of ENIG:
- Flat and uniform surface finish
- Excellent solderability
- Good shelf life
- Suitable for fine-pitch components
Disadvantages of ENIG:
- Higher cost compared to HASL
- Potential for “black pad” issue due to improper plating processes
- Gold layer may wear off over time
3. Immersion Silver (IAg)
Immersion silver is a cost-effective alternative to ENIG, offering similar benefits. In this process, a thin layer of silver is deposited directly onto the copper surfaces through a chemical reaction.
Advantages of IAg:
- Cost-effective compared to ENIG
- Good solderability
- Flat and uniform surface finish
- Suitable for fine-pitch components
Disadvantages of IAg:
- Shorter shelf life compared to ENIG
- Potential for silver migration and tarnishing over time
- Not suitable for applications exposed to sulfurous environments
4. Organic Solderability Preservative (OSP)
OSP is a non-metallic surface finish that involves applying a thin, organic compound layer to the exposed copper surfaces. This layer acts as a barrier against oxidation and provides good solderability.
Advantages of OSP:
- Cost-effective
- Flat and uniform surface finish
- Suitable for fine-pitch components
- Environmentally friendly
Disadvantages of OSP:
- Limited shelf life (typically 3-6 months)
- Not suitable for multiple reflow cycles
- Potential for inconsistent solderability
5. Electroless Nickel Electroless Palladium Immersion Gold (ENEPIG)
ENEPIG is an advanced surface finish that combines the benefits of ENIG and ENEP (Electroless Nickel Electroless Palladium). In this process, a layer of nickel is deposited, followed by a layer of palladium and a thin layer of gold. The palladium layer enhances the durability and wire bonding capabilities of the surface finish.
Advantages of ENEPIG:
- Excellent solderability
- Suitable for fine-pitch components
- Good shelf life
- Compatible with wire bonding
- Improved durability compared to ENIG
Disadvantages of ENEPIG:
- Higher cost compared to other surface finishes
- Complex plating process
- Potential for “black pad” issue if not processed correctly
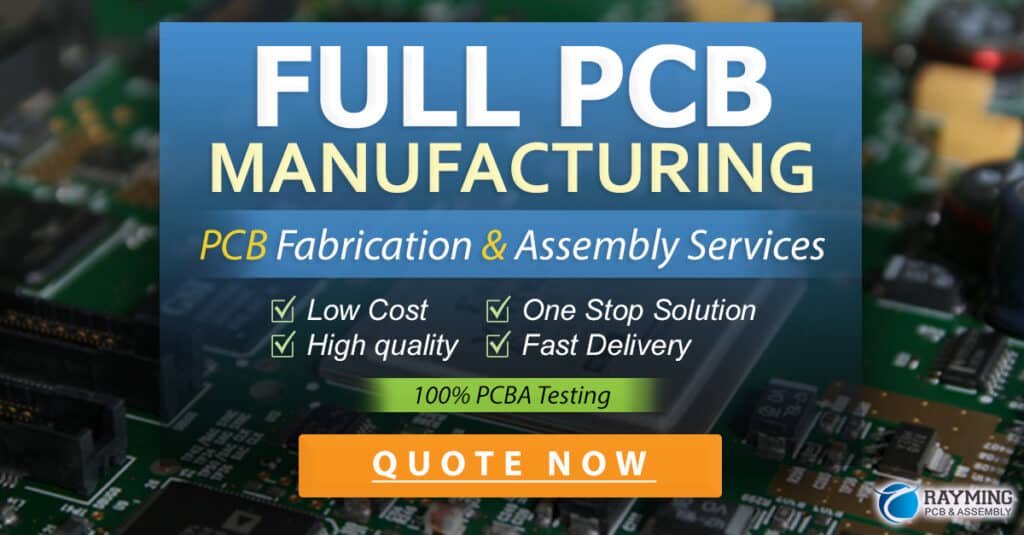
Selecting the Right Surface Finish for Your Application
When choosing the appropriate surface finish for your PCB, consider the following factors:
-
Application Requirements: Evaluate the specific requirements of your application, such as the operating environment, expected lifespan, and performance demands.
-
Component Compatibility: Ensure that the chosen surface finish is compatible with the components used in your design, especially for fine-pitch and BGA components.
-
Assembly Process: Consider the assembly processes involved, such as reflow soldering, wave soldering, or wire bonding, and select a surface finish that is suitable for these processes.
-
Cost: Assess the cost implications of each surface finish option and determine the most cost-effective solution that meets your requirements.
-
Shelf Life: If your PCBs will be stored for an extended period before assembly, choose a surface finish with a longer shelf life, such as ENIG or ENEPIG.
-
Environmental Considerations: Take into account any environmental factors that may impact the performance of the surface finish, such as exposure to harsh chemicals or high humidity.
Surface Finish Comparison Table
Surface Finish | Solderability | Shelf Life | Fine-Pitch Compatibility | Cost |
---|---|---|---|---|
HASL | Excellent | Good | Limited | Low |
ENIG | Excellent | Excellent | Excellent | High |
IAg | Good | Limited | Excellent | Moderate |
OSP | Good | Limited | Excellent | Low |
ENEPIG | Excellent | Excellent | Excellent | High |
Frequently Asked Questions (FAQ)
-
Q: What is the most cost-effective surface finish for PCBs?
A: HASL and OSP are generally the most cost-effective surface finish options for PCBs. However, it’s essential to consider other factors such as application requirements and component compatibility when making a decision. -
Q: Which surface finish is best suited for fine-pitch components?
A: ENIG, IAg, OSP, and ENEPIG are all suitable for fine-pitch components due to their flat and uniform surface finish. HASL, on the other hand, may not be ideal for fine-pitch components because of its uneven surface. -
Q: How does the shelf life of different surface finishes compare?
A: ENIG and ENEPIG offer the longest shelf life, typically exceeding 12 months. HASL and IAg have a good shelf life, while OSP has a limited shelf life of 3-6 months. -
Q: Can I use HASL for applications that require multiple reflow cycles?
A: HASL is suitable for applications that involve a limited number of reflow cycles. For applications requiring multiple reflow cycles, surface finishes like ENIG or ENEPIG are more appropriate. -
Q: What is the “black pad” issue associated with ENIG and ENEPIG?
A: The “black pad” issue is a potential problem that can occur during the plating process of ENIG and ENEPIG surface finishes. It is characterized by a dark appearance of the nickel layer, which can lead to poor solderability and reduced reliability. Proper process control and monitoring can help prevent this issue.
Conclusion
Selecting the right surface finish for your PCB is a critical decision that impacts the manufacturability, reliability, and performance of your electronic device. By understanding the characteristics, advantages, and disadvantages of various surface finish options, you can make an informed choice that best suits your specific application requirements.
Consider factors such as solderability, shelf life, component compatibility, assembly processes, cost, and environmental factors when evaluating surface finish options. Consult with your PCB manufacturer and assembly partner to ensure that your chosen surface finish aligns with their capabilities and recommendations.
By selecting the appropriate PCB surface finish, you can enhance the quality, reliability, and longevity of your electronic products, ultimately contributing to their success in the market.
Leave a Reply