What is PCB Assembly?
PCB assembly, also known as printed circuit board assembly or PCBA, is the process of soldering or assembly of electronic components onto a printed circuit board (PCB). It is a crucial step in the manufacturing process of electronic devices, as it involves the placement and connection of various components such as resistors, capacitors, integrated circuits (ICs), and connectors onto the PCB to create a functional electronic assembly.
PCB assembly can be categorized into two main types:
-
Through-hole assembly (THA): This involves inserting component leads through holes drilled in the PCB and soldering them to pads on the opposite side of the board.
-
Surface mount assembly (SMA): This involves placing components directly onto pads or lands on the surface of the PCB and soldering them in place.
The PCB Assembly Process
The PCB assembly process typically involves the following steps:
-
Solder Paste Application: Solder paste, a mixture of tiny solder particles and flux, is applied to the PCB’s pads using a stencil or screen printing process. The solder paste helps to form a strong electrical and mechanical connection between the components and the PCB.
-
Component Placement: The electronic components are placed onto the PCB using automated pick-and-place machines or by manual placement for low-volume or complex assemblies. The machines use computer-aided design (CAD) files to precisely place the components on the correct pads.
-
Reflow Soldering: The PCB with the placed components is passed through a reflow oven, which heats the board to a specific temperature profile. This melts the solder paste, forming a permanent connection between the components and the PCB pads.
-
Inspection and Testing: After the soldering process, the assembled PCB undergoes visual inspection and automated optical inspection (AOI) to detect any defects or misaligned components. Electrical testing, such as in-circuit testing (ICT) or functional testing, is also performed to ensure the proper functioning of the assembled board.
-
Conformal Coating and Potting: Depending on the application and environmental requirements, the assembled PCB may be coated with a protective layer of conformal coating or potted with a resin compound to shield the components from moisture, dust, and other environmental factors.
-
Final Assembly and Packaging: The tested and coated PCB is then integrated into the final product or packaged for shipment to the customer.
Benefits of Professional PCB Assembly Services
Outsourcing PCB assembly to professional service providers offers several advantages:
-
Cost Savings: Professional PCB assembly companies have the necessary equipment, expertise, and economies of scale to produce high-quality PCB assemblies at a lower cost compared to in-house assembly.
-
Quality Assurance: PCB assembly service providers adhere to strict quality control processes and industry standards to ensure consistent and reliable PCB assemblies. They invest in state-of-the-art equipment and skilled technicians to minimize defects and improve overall quality.
-
Faster Turnaround Time: With their streamlined processes and automated assembly lines, professional PCB assembly companies can deliver assembled boards faster than in-house assembly, reducing time-to-market for electronic products.
-
Access to Expertise: PCB assembly service providers have experienced engineers and technicians who can provide valuable input on design for manufacturability (DFM), component selection, and assembly processes to optimize the PCB design and improve manufacturing efficiency.
-
Scalability and Flexibility: Outsourcing PCB assembly allows companies to scale their production up or down based on demand, without investing in expensive equipment or hiring additional staff. This flexibility is particularly beneficial for companies with fluctuating production requirements or those focusing on core competencies.
Choosing the Right PCB Assembly Service Provider
When selecting a PCB assembly service provider, consider the following factors:
-
Technical Capabilities: Ensure that the service provider has the necessary equipment, expertise, and experience to handle your specific PCB assembly requirements, such as surface mount technology (SMT), through-hole assembly, or mixed-technology assembly.
-
Quality Management: Look for a provider with a robust quality management system, such as ISO 9001 certification, and a proven track record of delivering high-quality PCB assemblies. Inquire about their quality control processes, testing capabilities, and defect rates.
-
Industry Experience: Choose a service provider with experience in your specific industry or application, as they will have a better understanding of the unique requirements and challenges associated with your product.
-
Turnaround Time: Consider the provider’s typical turnaround times and their ability to meet your production deadlines. Some providers offer expedited services for time-sensitive projects.
-
Customer Support: Evaluate the level of customer support offered by the service provider, including communication channels, responsiveness, and their willingness to address your concerns or requirements.
-
Cost and Value: While cost is an important factor, it should not be the sole deciding factor. Consider the overall value provided by the service provider, taking into account their quality, reliability, and the additional services they offer.
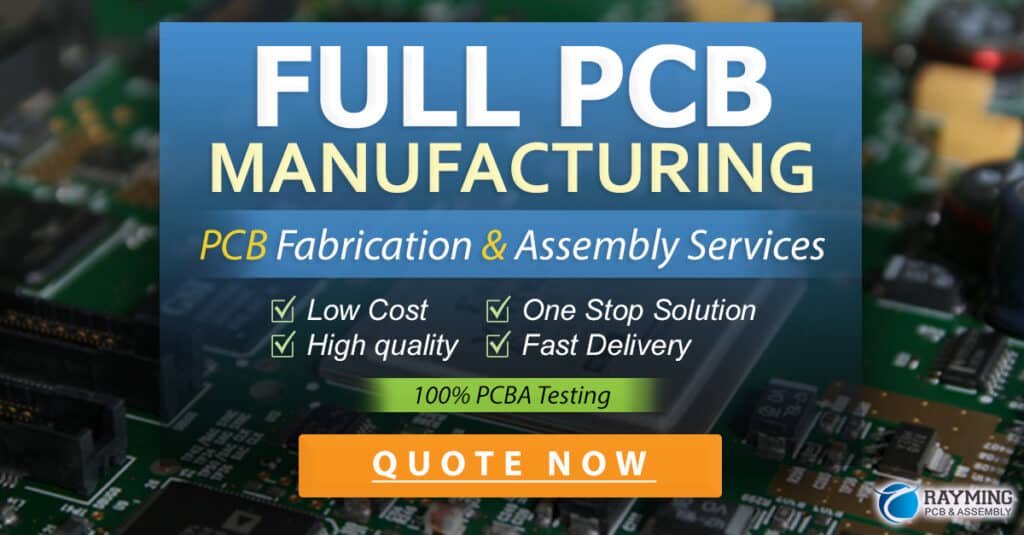
The Importance of Design for Manufacturing (DFM) in PCB Assembly
Design for Manufacturing (DFM) is a crucial aspect of PCB assembly that involves designing the PCB with manufacturing processes and limitations in mind. By considering DFM principles during the design phase, companies can improve the manufacturability, reliability, and cost-effectiveness of their PCB assemblies.
Some key DFM considerations for PCB assembly include:
-
Component Selection: Choose components that are readily available, have standard packaging, and are compatible with the intended assembly processes. Avoid using obsolete or hard-to-source components that may delay production or increase costs.
-
PCB Layout: Design the PCB layout with proper spacing between components, traces, and pads to facilitate efficient assembly and minimize the risk of defects. Follow the recommended design guidelines for the specific assembly processes, such as minimum trace width, hole size, and clearances.
-
Solder Mask and Silkscreen: Use a clear and accurate solder mask and silkscreen to help guide the assembly process and prevent errors. Ensure that the solder mask openings are properly sized and positioned to avoid solder bridging or poor solder joint formation.
-
Panelization: Consider panelizing multiple PCBs onto a single panel to optimize manufacturing efficiency and reduce handling costs. Incorporate proper panelization techniques, such as tab routing or V-scoring, to facilitate easy depanelization without damaging the individual boards.
-
Testing and Inspection Points: Include test points and inspection fiducials on the PCB to facilitate automated testing and inspection processes. This helps to identify and resolve any issues early in the assembly process, reducing the risk of costly rework or delays.
By collaborating closely with your PCB assembly service provider and incorporating DFM principles into your PCB design, you can optimize the assembly process, reduce manufacturing costs, and improve the overall quality and reliability of your electronic products.
The Role of Automated Optical Inspection (AOI) in PCB Assembly
Automated Optical Inspection (AOI) is a critical quality control process in PCB assembly that uses advanced imaging technology to detect and identify defects or anomalies on the assembled PCBs. AOI systems capture high-resolution images of the PCB and compare them against a reference image or design data to identify any discrepancies.
The main advantages of using AOI in PCB assembly include:
-
Early Defect Detection: AOI allows for the early detection of defects such as missing or misaligned components, solder bridging, insufficient solder, or incorrect component polarity. By identifying these issues early in the assembly process, manufacturers can prevent the defective boards from progressing to the next stage, reducing the risk of costly rework or scrap.
-
Improved Quality and Reliability: By detecting and correcting defects early, AOI helps to improve the overall quality and reliability of the assembled PCBs. This, in turn, reduces the likelihood of field failures or product returns, enhancing customer satisfaction and brand reputation.
-
Increased Throughput: AOI systems can inspect PCBs at a much faster rate compared to manual inspection, allowing for higher production throughput and shorter lead times. This is particularly beneficial for high-volume production runs or time-sensitive projects.
-
Consistent and Objective Inspection: Unlike manual inspection, which can be subject to human error or inconsistency, AOI provides a consistent and objective assessment of the PCB assembly quality. This helps to maintain uniform quality standards across different production batches and assembly lines.
-
Traceability and Data Analysis: AOI systems generate detailed inspection reports and data that can be used for traceability, process improvement, and quality management purposes. By analyzing the AOI data, manufacturers can identify trends, root causes of defects, and implement corrective actions to prevent recurrence.
While AOI is a powerful tool for detecting assembly defects, it is important to note that it is not a substitute for comprehensive quality management and testing processes. AOI should be used in conjunction with other quality control methods, such as in-circuit testing (ICT), functional testing, and manual inspection, to ensure the highest level of PCB assembly quality.
Choosing the Right Components for PCB Assembly
Selecting the appropriate components is a critical aspect of PCB assembly that can significantly impact the performance, reliability, and cost of the final product. When choosing components for your PCB assembly, consider the following factors:
-
Functionality: Ensure that the selected components meet the functional requirements of your electronic device. Consider factors such as voltage ratings, current handling capacity, frequency response, and power dissipation to ensure optimal performance.
-
Quality and Reliability: Choose components from reputable manufacturers with a proven track record of producing high-quality and reliable parts. Look for components with appropriate certifications, such as RoHS compliance, and consider the expected lifespan and failure rates of the components in your specific application.
-
Availability and Lead Time: Select components that are readily available and have stable supply chains to avoid production delays or unexpected cost increases. Consider the lead times for each component and plan your procurement accordingly to meet your production schedule.
-
Cost: Evaluate the cost of the components in relation to your overall budget and production volume. While it may be tempting to choose the lowest-cost options, consider the long-term cost implications, including the potential for increased failure rates or reduced performance, which could lead to higher costs in the long run.
-
Packaging and Compatibility: Choose components with packaging that is compatible with your intended assembly processes, such as surface mount or through-hole technology. Consider the size and pitch of the component packages to ensure they can be efficiently placed and soldered onto the PCB.
-
Thermal Management: For components that generate significant heat, such as power transistors or voltage regulators, consider their thermal characteristics and ensure that the PCB design incorporates appropriate thermal management techniques, such as heat sinks or thermal vias, to prevent overheating and ensure reliable operation.
-
Future-Proofing: When possible, select components that offer a degree of future-proofing, such as those with backward compatibility or those that adhere to industry standards. This can help to extend the lifespan of your electronic device and facilitate easier upgrades or modifications in the future.
By carefully considering these factors and working closely with your PCB assembly service provider, you can select the optimal components for your PCB assembly, ensuring the best possible performance, reliability, and cost-effectiveness for your electronic product.
Component Selection Table
Factor | Consideration |
---|---|
Functionality | Voltage ratings, current handling, frequency response, power dissipation |
Quality and Reliability | Reputable manufacturers, certifications (e.g., RoHS), lifespan, failure rates |
Availability and Lead Time | Stable supply chains, lead times, procurement planning |
Cost | Overall budget, production volume, long-term cost implications |
Packaging and Compatibility | Compatibility with assembly processes (SMT, through-hole), package size and pitch |
Thermal Management | Thermal characteristics, heat sinks, thermal vias |
Future-Proofing | Backward compatibility, adherence to industry standards |
Frequently Asked Questions (FAQ)
- What is the difference between PCB assembly and PCB fabrication?
-
PCB fabrication involves the manufacturing of the bare printed circuit board, including the creation of the copper traces, drilling of holes, and the application of solder mask and silkscreen. PCB assembly, on the other hand, involves the soldering and mounting of electronic components onto the fabricated PCB to create a functional electronic assembly.
-
What are the most common PCB assembly methods?
-
The two most common PCB assembly methods are through-hole assembly (THA) and surface mount assembly (SMA). Through-hole assembly involves inserting component leads through holes drilled in the PCB and soldering them to pads on the opposite side. Surface mount assembly involves placing components directly onto pads on the surface of the PCB and soldering them in place.
-
What is the role of solder paste in PCB assembly?
-
Solder paste, a mixture of tiny solder particles and flux, is applied to the PCB’s pads before component placement. It serves two main purposes: first, it helps to temporarily hold the components in place during the assembly process; second, when heated in a reflow oven, it melts and forms a permanent electrical and mechanical connection between the components and the PCB pads.
-
What is the purpose of conformal coating in PCB assembly?
-
Conformal coating is a protective layer applied to the assembled PCB to shield the components from moisture, dust, chemicals, and other environmental factors. It helps to improve the reliability and longevity of the electronic assembly, particularly in harsh or demanding operating conditions.
-
How can I ensure the quality of my PCB assembly?
- To ensure the quality of your PCB assembly, partner with a reputable PCB assembly service provider that adheres to strict quality control processes and industry standards. Implement a comprehensive quality management system that includes incoming inspection of components, automated optical inspection (AOI) of the assembled PCBs, and functional testing to verify the performance of the final product. Additionally, incorporate Design for Manufacturing (DFM) principles during the PCB design phase to optimize the assembly process and minimize the risk of defects.
Conclusion
PCB assembly is a critical process in the production of electronic devices, involving the soldering and mounting of components onto a printed circuit board. By understanding the various aspects of PCB assembly, including the assembly methods, the importance of Design for Manufacturing (DFM), the role of Automated Optical Inspection (AOI), and the selection of appropriate components, companies can optimize their PCB assembly processes and ensure the production of high-quality, reliable electronic products.
Outsourcing PCB assembly to professional service providers offers numerous benefits, such as cost savings, quality assurance, faster turnaround times, access to expertise, and scalability. When choosing a PCB assembly service provider, it is essential to consider factors such as technical capabilities, quality management, industry experience, turnaround time, customer support, and overall value.
By partnering with a trusted PCB assembly service provider and implementing best practices throughout the design and manufacturing process, companies can achieve success in bringing their electronic products to market efficiently and effectively.
Leave a Reply