What are PCB Castellations?
PCB castellations are a type of edge connector feature found on printed circuit boards (PCBs). They are small, semi-circular cuts or plated half-holes arranged along the edge of a PCB, resembling the battlements of a castle wall, hence the name “castellations.” These castellations serve as connection points for joining multiple PCBs together or for connecting a PCB to another device or system.
The Purpose of PCB Castellations
Castellations on a PCB provide several advantages over traditional connectors:
- Space-saving: Castellations eliminate the need for bulky connectors, allowing for more compact PCB designs.
- Cost-effective: By using castellations instead of connectors, manufacturing costs can be reduced.
- Reliable connections: Castellations offer secure and reliable electrical connections between boards or devices.
- Simplified assembly: Castellated PCBs can be easily soldered together or connected to other devices using Reflow Soldering techniques.
How are PCB Castellations Made?
The process of creating castellations on a PCB involves several steps:
-
PCB design: The PCB layout is designed with castellations incorporated along the desired edges of the board. The castellation holes are typically plated through-holes (PTHs) with a specific diameter and pitch (spacing between holes).
-
PCB Fabrication: During the PCB manufacturing process, the castellations are created by drilling or routing the semi-circular cuts along the edge of the board. The holes are then plated with a conductive material, such as copper, to ensure electrical connectivity.
-
PCB finishing: After the castellations are formed, the PCB undergoes the standard finishing processes, such as solder mask application and surface finish (e.g., HASL, ENIG, or immersion silver).
PCB Castellation Design Considerations
When designing PCBs with castellations, several factors must be considered to ensure optimal performance and manufacturability:
-
Castellation dimensions: The size and spacing of the castellations should be carefully chosen based on the PCB Thickness, connection requirements, and manufacturing capabilities. Common castellation diameters range from 0.5mm to 2mm, with a pitch of 1mm to 2.54mm.
-
Plating thickness: The plating thickness of the castellation holes should be sufficient to ensure reliable electrical connections and mechanical strength. A typical plating thickness for castellations is 25-50 micrometers of copper.
-
Solder mask: The solder mask should be properly applied around the castellations to prevent solder bridging and short circuits during the assembly process.
-
Mechanical stress: Castellations can be subject to mechanical stress during handling and assembly. Proper design and reinforcement techniques, such as using additional non-plated holes or support structures, can help minimize the risk of damage.
Applications of PCB Castellations
PCB castellations find applications in various industries and products, including:
-
Modular electronics: Castellations enable the creation of modular electronic systems, where multiple PCBs can be easily interconnected to form larger, more complex assemblies.
-
IoT devices: Many Internet of Things (IoT) devices utilize castellated PCBs for their compact size and reliable connections.
-
Wearable technology: Castellations are often used in wearable electronic devices, such as smartwatches and fitness trackers, due to their space-saving properties and robust connections.
-
Automotive electronics: In the automotive industry, castellated PCBs are employed in various electronic control units (ECUs) and sensor modules, where reliable connections and compact designs are essential.
-
Industrial control systems: Castellations are used in industrial control systems, such as programmable logic controllers (PLCs) and human-machine interfaces (HMIs), to create modular and scalable designs.
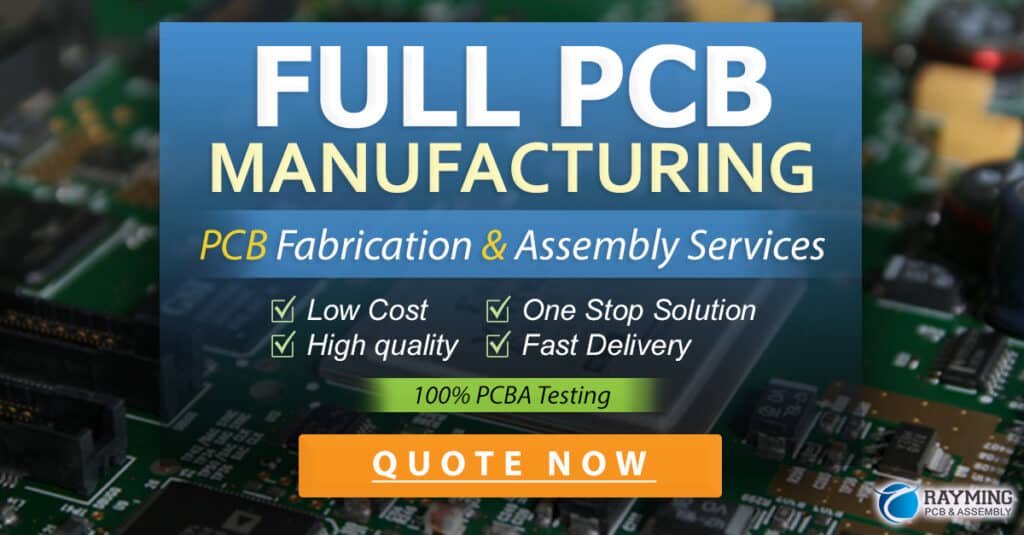
Advantages of Using PCB Castellations
PCB castellations offer several benefits compared to traditional connectors:
-
Reduced cost: By eliminating the need for separate connectors, castellations can significantly reduce the overall cost of PCB Assembly.
-
Improved reliability: Castellations provide robust and reliable electrical connections, minimizing the risk of connection failures due to vibration or mechanical stress.
-
Space savings: Castellated PCBs enable more compact designs, as they eliminate the need for bulky connectors and allow for closer board-to-board spacing.
-
Simplified assembly: Castellated PCBs can be easily assembled using reflow soldering techniques, streamlining the manufacturing process and reducing assembly time.
-
Enhanced design flexibility: Castellations allow for greater design flexibility, as they can be placed along any edge of the PCB and can accommodate various Board Thicknesses and connection requirements.
Challenges and Considerations
While PCB castellations offer numerous advantages, there are also some challenges and considerations to keep in mind:
-
Manufacturing complexity: Creating castellations requires precise drilling or routing and plating processes, which can increase the complexity and cost of PCB manufacturing compared to standard PCBs.
-
Limited connection density: Castellations have a lower connection density compared to some high-density connectors, which may be a limitation in certain applications.
-
Mechanical stress: Castellated PCBs can be more susceptible to mechanical stress during handling and assembly, requiring careful design and handling procedures to minimize the risk of damage.
-
Signal integrity: In high-speed or high-frequency applications, the signal integrity of castellated connections may be affected by factors such as impedance mismatches, crosstalk, and reflections. Careful design and simulation techniques are necessary to ensure optimal signal integrity.
-
Soldering challenges: Soldering castellated PCBs requires precise control of solder volume and temperature to avoid bridging or insufficient solder joints. Specialized soldering techniques, such as pin-in-paste or selective soldering, may be necessary for optimal results.
Best Practices for Designing and Manufacturing PCBs with Castellations
To ensure successful design and manufacturing of PCBs with castellations, consider the following best practices:
-
Collaborate with your PCB manufacturer: Work closely with your PCB manufacturer to ensure that your castellation design is compatible with their manufacturing capabilities and guidelines.
-
Use appropriate design tools: Employ PCB design software that supports the creation and validation of castellated designs, such as Altium Designer, Cadence Allegro, or KiCad.
-
Follow recommended design guidelines: Adhere to the recommended castellation dimensions, spacing, and plating requirements provided by your PCB manufacturer or industry standards (e.g., IPC-2221).
-
Perform thorough design reviews: Conduct comprehensive design reviews to ensure that your castellated PCB design meets all functional, mechanical, and manufacturing requirements.
-
Consider mechanical reinforcement: Incorporate mechanical reinforcement techniques, such as additional non-plated holes or support structures, to minimize the risk of damage to the castellations during handling and assembly.
-
Utilize appropriate soldering techniques: Select soldering techniques that are suitable for castellated PCBs, such as pin-in-paste or selective soldering, to ensure reliable and consistent solder joints.
-
Implement quality control measures: Establish thorough quality control procedures, including visual inspection, electrical testing, and cross-sectioning, to verify the integrity of the castellated connections.
FAQ
- What are the typical dimensions for PCB castellations?
-
Common castellation diameters range from 0.5mm to 2mm, with a pitch (spacing between holes) of 1mm to 2.54mm. The specific dimensions depend on the PCB thickness, connection requirements, and manufacturing capabilities.
-
Can castellated PCBs be used in high-speed applications?
-
Yes, castellated PCBs can be used in high-speed applications, but careful design and simulation techniques are necessary to ensure optimal signal integrity. Factors such as impedance matching, crosstalk, and reflections must be considered and addressed during the design process.
-
How are castellated PCBs assembled?
-
Castellated PCBs are typically assembled using reflow soldering techniques, where the PCBs are aligned and soldered together in a reflow oven. Other techniques, such as pin-in-paste or selective soldering, may also be used depending on the specific requirements of the application.
-
Are there any industry standards for PCB castellations?
-
Yes, industry standards such as IPC-2221 provide guidelines for the design and manufacturing of PCBs with castellations. These standards cover aspects such as castellation dimensions, spacing, plating requirements, and quality control procedures.
-
Can castellated PCBs be repaired or reworked?
- Repairing or reworking castellated PCBs can be challenging due to the small size and close spacing of the castellations. Specialized tools and techniques, such as micro-soldering or hot-air rework, may be necessary to perform repairs or modifications. However, it is generally recommended to replace the entire PCB assembly if possible, rather than attempting to repair individual castellations.
Castellation Dimensions Table
PCB Thickness (mm) | Castellation Diameter (mm) | Pitch (mm) |
---|---|---|
0.8 | 0.5 – 1.0 | 1.0 – 1.27 |
1.0 | 0.8 – 1.2 | 1.27 – 1.6 |
1.6 | 1.0 – 1.5 | 1.6 – 2.0 |
2.0 | 1.2 – 2.0 | 2.0 – 2.54 |
Conclusion
PCB castellations offer a space-saving, cost-effective, and reliable method for interconnecting multiple PCBs or connecting a PCB to another device or system. By eliminating the need for bulky connectors, castellations enable more compact and modular electronic designs across various industries, including IoT, wearable technology, automotive electronics, and industrial control systems.
Designing and manufacturing PCBs with castellations requires careful consideration of factors such as castellation dimensions, plating thickness, solder mask application, and mechanical stress. Following best practices and industry standards, collaborating with experienced PCB manufacturers, and implementing thorough quality control measures are essential for ensuring the success of castellated PCB designs.
As electronic devices continue to become smaller, more complex, and more interconnected, the use of PCB castellations is likely to grow in popularity. By understanding the advantages, challenges, and best practices associated with castellated PCBs, designers and engineers can leverage this technology to create innovative, reliable, and cost-effective electronic solutions.
Leave a Reply