Introduction to PCB Thickness
Printed Circuit Board (PCB) thickness is a crucial factor in the design and manufacturing of electronic devices. It plays a significant role in determining the overall performance, reliability, and durability of the PCB. The thickness of a PCB can vary depending on the specific application, the number of layers required, and the manufacturing process used.
In this article, we will delve into the complex story of PCB thickness, exploring its importance, the factors that influence it, and the various standards and guidelines that govern PCB thickness in the electronics industry.
Why PCB Thickness Matters
Mechanical Strength and Durability
One of the primary reasons why PCB thickness matters is its impact on the mechanical strength and durability of the board. A thicker PCB is generally more robust and can withstand greater mechanical stress and vibration compared to a thinner board. This is particularly important in applications where the PCB is subject to harsh environmental conditions or physical forces.
Thicker PCBs are often used in industries such as aerospace, automotive, and military, where reliability and durability are critical. These boards need to withstand extreme temperatures, vibrations, and shocks without compromising their functionality.
Electrical Performance
PCB thickness also plays a role in the electrical performance of the board. The thickness of the dielectric material between the copper layers affects the impedance and signal integrity of the PCB. Thinner dielectrics allow for faster signal propagation and reduced signal loss, which is essential for high-speed applications.
However, thinner PCBs also have limitations in terms of power handling capability and current carrying capacity. Thicker copper layers are required to handle higher currents and power levels, which in turn increases the overall thickness of the PCB.
Manufacturing Considerations
The thickness of a PCB also has implications for the manufacturing process. Thinner PCBs are generally easier to manufacture and require less material, resulting in lower production costs. However, they also pose challenges in terms of handling, assembly, and reliability.
Thicker PCBs, on the other hand, require more material and are more challenging to manufacture. They may require specialized equipment and processes, which can increase production costs. However, they offer better mechanical stability and are easier to handle during assembly.
Factors Influencing PCB Thickness
Number of Layers
One of the primary factors that determine the thickness of a PCB is the number of layers it contains. PCBs can have anywhere from one to multiple layers, depending on the complexity of the circuit design and the space constraints of the application.
As the number of layers increases, so does the thickness of the PCB. Each additional layer requires a dielectric material and Copper Foil, adding to the overall thickness of the board. The table below shows the typical thickness ranges for different numbers of layers:
Number of Layers | Thickness Range |
---|---|
1 – 2 | 0.4mm – 1.6mm |
4 – 6 | 0.8mm – 2.4mm |
8 – 10 | 1.6mm – 3.2mm |
12 – 16 | 2.4mm – 4.0mm |
18 – 24 | 3.2mm – 5.0mm |
Copper Weight
Another factor that contributes to PCB thickness is the weight of the copper used in the layers. Copper weight is typically measured in ounces per square foot (oz/ft²) and refers to the thickness of the copper foil used in the PCB.
Common copper weights used in PCBs include:
- 1/2 oz/ft² (17.5 μm)
- 1 oz/ft² (35 μm)
- 2 oz/ft² (70 μm)
- 3 oz/ft² (105 μm)
- 4 oz/ft² (140 μm)
Higher copper weights result in thicker PCBs, as the copper foil itself adds to the overall thickness of the board. The choice of copper weight depends on the current carrying requirements and the desired electrical performance of the PCB.
Dielectric Material
The dielectric material used in the PCB also plays a role in determining its thickness. The dielectric is the insulating material that separates the conductive copper layers and provides electrical isolation.
Common dielectric materials used in PCBs include:
- FR-4: A glass-reinforced epoxy laminate, widely used in the electronics industry.
- Rogers: High-performance dielectric materials used in high-frequency and microwave applications.
- Polyimide: A high-temperature, flexible dielectric material used in flexible PCBs.
The thickness of the dielectric material varies depending on the specific material and the requirements of the application. Thinner dielectrics allow for thinner PCBs, but they also have limitations in terms of voltage ratings and insulation properties.
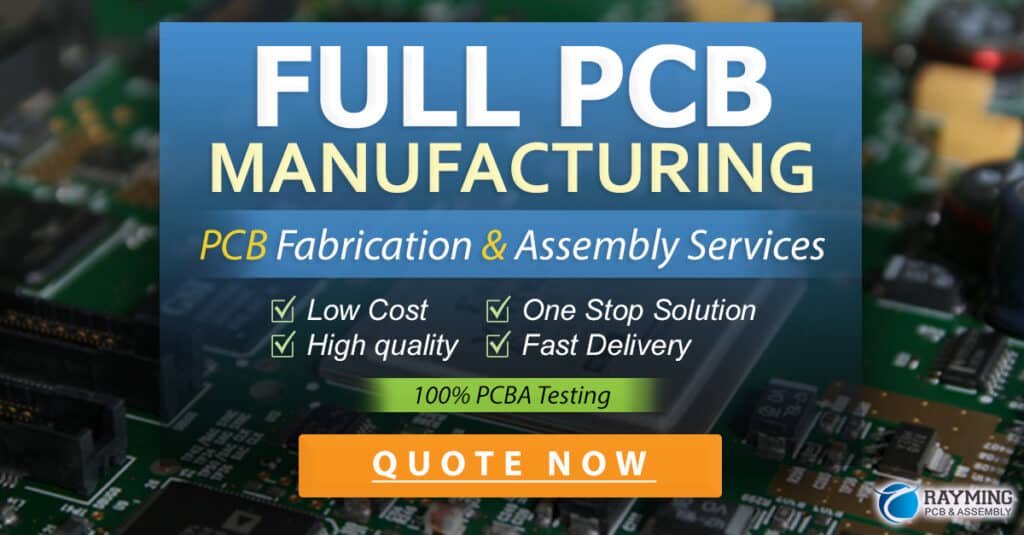
PCB Thickness Standards
To ensure consistency and reliability in PCB manufacturing, various standards and guidelines have been established by industry organizations. These standards provide specifications for PCB thickness, material properties, and manufacturing tolerances.
Some of the key standards related to PCB thickness include:
IPC-2221: Generic Standard on Printed Board Design
IPC-2221 is a comprehensive standard that provides guidelines for the design of printed circuit boards. It covers various aspects of PCB design, including thickness specifications for different types of boards.
According to IPC-2221, the minimum finished thickness for a single-sided PCB is 0.36mm, while the minimum finished thickness for a double-sided PCB is 0.56mm. The standard also provides guidelines for the thickness of multilayer PCBs based on the number of layers and the application requirements.
IPC-6012: Qualification and Performance Specification for Rigid Printed Boards
IPC-6012 is a performance specification that defines the requirements for the manufacture of rigid printed circuit boards. It includes specifications for PCB thickness, hole size, and other dimensional tolerances.
The standard specifies the acceptable thickness ranges for different classes of PCBs, based on their intended use and reliability requirements. For example, Class 1 PCBs, which are used for general electronic products, have a thickness tolerance of ±10% of the nominal thickness. Class 2 and Class 3 PCBs, which are used for dedicated service electronic products and high-reliability applications, have tighter thickness tolerances.
IPC-4101: Specification for Base Materials for Rigid and Multilayer Printed Boards
IPC-4101 is a specification that defines the requirements for the base materials used in the manufacture of rigid and multilayer printed circuit boards. It includes specifications for the thickness and tolerances of the dielectric materials used in PCBs.
The standard provides a list of approved base materials and their corresponding thickness ranges. It also specifies the acceptable thickness tolerances for each material, based on the nominal thickness and the manufacturing process used.
FAQ
1. What is the most common PCB thickness?
The most common PCB thickness used in the electronics industry is 1.6mm. This thickness provides a good balance between mechanical strength, durability, and manufacturing ease. It is widely used in consumer electronics, telecommunications, and industrial applications.
2. Can I specify a custom PCB thickness for my application?
Yes, it is possible to specify a custom PCB thickness for your application. PCB manufacturers can accommodate a wide range of thickness requirements, subject to the capabilities of their manufacturing processes and the availability of materials. However, custom thicknesses may incur additional costs and longer lead times compared to standard thicknesses.
3. How does PCB thickness affect the cost of manufacturing?
PCB thickness has a direct impact on the cost of manufacturing. Thicker PCBs require more material, both in terms of the dielectric and copper layers, which increases the raw material costs. They also require more processing time and may need specialized equipment, adding to the manufacturing costs. Thinner PCBs, on the other hand, use less material and are generally faster and easier to manufacture, resulting in lower production costs.
4. What is the minimum PCB thickness that can be manufactured?
The minimum PCB thickness that can be manufactured depends on the capabilities of the PCB manufacturer and the specific requirements of the application. Some manufacturers can produce PCBs as thin as 0.2mm, using specialized materials and processes. However, such thin PCBs are typically used in niche applications, such as ultra-compact devices or flexible electronics. The practical minimum thickness for most standard PCB applications is around 0.4mm to 0.8mm.
5. How do I choose the right PCB thickness for my application?
Choosing the right PCB thickness for your application involves considering several factors, such as:
- Mechanical requirements: Consider the mechanical stress, vibration, and environmental conditions the PCB will be subjected to.
- Electrical requirements: Evaluate the power handling, current carrying capacity, and signal integrity needs of your circuit.
- Space constraints: Determine the available space for the PCB in your device and consider the impact of thickness on the overall form factor.
- Manufacturing considerations: Assess the capabilities of your PCB manufacturer and the cost implications of different thickness options.
It is recommended to consult with a PCB design expert or manufacturer to determine the optimal thickness for your specific application. They can provide guidance based on industry standards, best practices, and their experience in manufacturing similar PCBs.
Conclusion
PCB thickness is a complex and critical aspect of PCB design and manufacturing. It affects the mechanical strength, electrical performance, and manufacturing feasibility of the board. Understanding the factors that influence PCB thickness, such as the number of layers, copper weight, and dielectric material, is essential for designing reliable and cost-effective PCBs.
Industry standards, such as IPC-2221, IPC-6012, and IPC-4101, provide guidelines and specifications for PCB thickness, ensuring consistency and reliability in PCB manufacturing. By adhering to these standards and working closely with experienced PCB manufacturers, designers can optimize the thickness of their PCBs to meet the specific requirements of their applications.
As technology advances and the demand for compact, high-performance electronics grows, the story of PCB thickness continues to evolve. Innovations in materials, manufacturing processes, and design techniques are pushing the boundaries of what is possible in terms of PCB thickness and functionality. By staying informed about the latest developments and best practices in PCB thickness, designers and manufacturers can create PCBs that are thinner, more reliable, and better suited to the needs of modern electronic devices.
Leave a Reply