Introduction to PCB Layers
A Printed Circuit Board (PCB) is a fundamental component in modern electronics. It provides a platform for mounting and interconnecting electronic components to create a functional circuit. One of the critical aspects of PCB design is the concept of layers. PCB layers are the different levels within a PCB that contain conductive traces, planes, and other features. Understanding PCB layers is essential for designing efficient and reliable electronic devices.
What are PCB Layers?
PCB layers are the individual levels within a PCB that are used to route signals and power between components. Each layer consists of a thin sheet of insulating material, typically fiberglass, with copper traces and other features etched onto its surface. The number of layers in a PCB can vary from one to over thirty, depending on the complexity of the circuit and the design requirements.
Why are PCB Layers Important?
PCB layers play a crucial role in the performance and functionality of electronic devices. They allow designers to create complex circuits with high component density, while minimizing the overall size of the PCB. By using multiple layers, designers can:
- Reduce signal interference and crosstalk
- Improve power distribution and heat dissipation
- Increase routing flexibility and efficiency
- Enhance mechanical stability and durability
Types of PCB Layers
There are several types of PCB layers, each serving a specific purpose in the overall design. The most common types of PCB layers include:
Signal Layers
Signal layers are used to route electrical signals between components on the PCB. They typically consist of thin copper traces that are etched onto the surface of the insulating material. The width and spacing of these traces are determined by factors such as the signal frequency, current requirements, and electromagnetic compatibility (EMC) considerations.
Power Planes
Power planes are used to distribute power to the components on the PCB. They are typically made of solid copper sheets that cover a large area of the PCB. Power planes help to minimize voltage drops and provide a low-impedance path for current flow. They also act as a reference plane for signal layers, helping to reduce electromagnetic interference (EMI) and improve signal integrity.
Ground Planes
Ground planes serve a similar purpose to power planes but are used to provide a common ground reference for the components on the PCB. They help to minimize ground loops and reduce EMI by providing a low-impedance return path for electrical currents. Ground planes are often placed adjacent to signal layers to provide shielding and reduce crosstalk between signals.
Dielectric Layers
Dielectric layers are the insulating layers that separate the conductive layers in a PCB. They are typically made of fiberglass or other insulating materials and provide electrical isolation between the layers. The thickness and material properties of the dielectric layers can affect the impedance and propagation delay of signals on the PCB.
PCB Layer Stackup
The arrangement of the various layers in a PCB is known as the layer stackup. The layer stackup is a critical aspect of PCB design, as it determines the electrical and mechanical properties of the board. A typical PCB layer stackup consists of alternating layers of conductors (signal, power, and ground) and insulators (dielectric).
Here is an example of a simple 4-layer PCB stackup:
Layer | Type | Material | Thickness (mm) |
---|---|---|---|
Top | Signal | Copper | 0.035 |
2 | Ground | Copper | 0.035 |
3 | Power | Copper | 0.035 |
Bottom | Signal | Copper | 0.035 |
Dielectric | FR-4 | 0.2 (between layers) |
In this example, the top and bottom layers are used for signal routing, while the inner layers are dedicated to power and ground planes. The dielectric material, FR-4, provides electrical isolation between the layers and determines the overall thickness of the PCB.
Designing a PCB Layer Stackup
When designing a PCB layer stackup, there are several factors to consider:
-
Signal integrity: The layer stackup should be designed to minimize signal distortion, crosstalk, and EMI. This can be achieved by proper placement of signal, power, and ground layers, as well as the use of appropriate dielectric materials and thicknesses.
-
Power distribution: The layer stackup should provide a low-impedance path for power distribution to all components on the PCB. This can be achieved by using dedicated power planes and minimizing the distance between power sources and loads.
-
Manufacturability: The layer stackup should be designed with manufacturing constraints in mind, such as minimum trace widths, spacing, and drill sizes. It is essential to consult with the PCB manufacturer to ensure that the design is feasible and cost-effective.
-
Thermal management: The layer stackup should be designed to facilitate heat dissipation from power-hungry components. This can be achieved by using thicker copper layers for power planes and providing adequate spacing between components and copper areas.
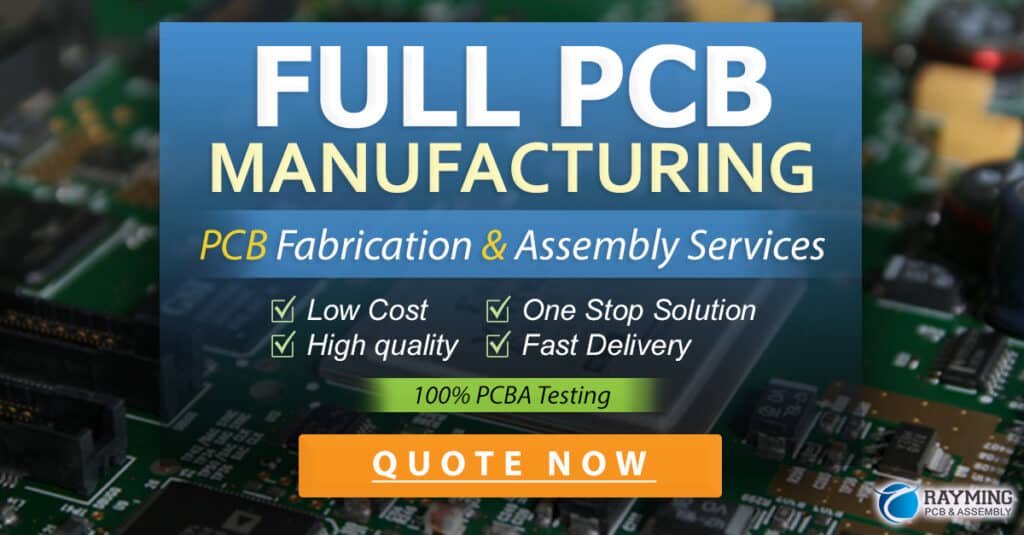
Advanced PCB Layer Techniques
As PCB designs become more complex, designers are using advanced techniques to optimize the performance and functionality of their boards. Some of these techniques include:
High-Density Interconnect (HDI)
HDI is a PCB manufacturing technology that allows for the creation of smaller vias and traces, enabling higher component density and improved signal integrity. HDI PCBs typically have more than eight layers and use microvias and buried vias to interconnect the layers.
Blind and Buried Vias
Blind vias are drilled from one surface of the PCB to an inner layer, while buried vias are drilled between two inner layers without reaching either surface. These types of vias allow for more efficient use of PCB real estate and can improve signal integrity by reducing the length of signal paths.
Controlled Impedance
Controlled impedance is a technique used to maintain a consistent impedance along a signal path. This is achieved by carefully designing the width and spacing of traces, as well as the properties of the dielectric material. Controlled impedance is essential for high-speed digital and RF circuits to minimize signal reflections and distortions.
PCB Layer Manufacturing Process
The manufacturing process for PCB layers involves several steps, each of which must be carefully controlled to ensure the quality and reliability of the final product. The main steps in the PCB layer manufacturing process are:
-
Material selection: The appropriate copper-clad laminate and prepreg materials are selected based on the electrical, mechanical, and thermal requirements of the design.
-
Layer stacking: The layers are stacked and aligned according to the designed stackup, with prepreg material placed between the layers for bonding.
-
Lamination: The stacked layers are subjected to high pressure and temperature in a lamination press, bonding them together to form a solid board.
-
Drilling: Holes are drilled through the board for vias and component mounting using computer-controlled drill machines.
-
Plating: The drilled holes are plated with copper to provide electrical connectivity between layers.
-
Etching: The copper layers are selectively etched to create the desired circuit patterns using photolithography and chemical etching processes.
-
Solder mask and silkscreen: A protective solder mask layer is applied to the Outer Layers, and silkscreen markings are added for component placement and identification.
-
Surface finish: A surface finish, such as HASL, ENIG, or OSP, is applied to the exposed copper areas to protect them from oxidation and facilitate soldering.
Frequently Asked Questions (FAQ)
-
Q: What is the minimum number of layers required for a functional PCB?
A: A functional PCB can be made with just one layer, known as a single-sided PCB. However, most modern electronic devices require at least two layers (double-sided PCB) to accommodate more complex circuits and improve performance. -
Q: What are the advantages of using more PCB layers?
A: Using more PCB layers allows for higher component density, improved signal integrity, better power distribution, and enhanced thermal management. It also provides more flexibility in routing and can help reduce the overall size of the PCB. -
Q: How does the choice of dielectric material affect PCB performance?
A: The dielectric material determines the electrical isolation between layers, as well as the impedance and propagation delay of signals. The choice of dielectric material depends on factors such as the operating frequency, temperature range, and cost requirements of the application. -
Q: What is the difference between blind and buried vias?
A: Blind vias are drilled from one surface of the PCB to an inner layer, while buried vias are drilled between two inner layers without reaching either surface. Both types of vias help to save PCB real estate and improve signal integrity, but buried vias are more challenging to manufacture and test. -
Q: How can PCB layers be optimized for thermal management?
A: PCB layers can be optimized for thermal management by using thicker copper layers for power planes, providing adequate spacing between components and copper areas, and using Thermal Vias to transfer heat from hot components to the outer layers of the PCB. Additionally, the use of metal-Core PCBs or insulated metal substrates can enhance heat dissipation in high-power applications.
Conclusion
PCB layers are a fundamental aspect of modern electronic design, enabling the creation of complex, high-performance circuits in compact form factors. Understanding the types, stackup, and manufacturing process of PCB layers is essential for designing reliable and efficient electronic devices. As PCB technology continues to advance, designers are using innovative techniques such as HDI, blind and buried vias, and controlled impedance to push the boundaries of what is possible with PCB design. By mastering the concepts and best practices of PCB layers, electronics engineers and hobbyists can unlock new possibilities in the world of electronic design.
Leave a Reply