Introduction to Core PCB
A printed circuit board (PCB) is a fundamental component in modern electronics. It serves as a platform for mounting and interconnecting electronic components, such as resistors, capacitors, and integrated circuits. The core of a PCB plays a crucial role in its overall performance and reliability. In this article, we will explore the concept of the core PCB, its importance, and its various types.
What is a Core PCB?
A core PCB refers to the central layer or layers of a multi-layer PCB. It acts as the foundation upon which the other layers are built. The core provides mechanical support and helps in the distribution of power and signals throughout the board. The core material is typically made of a dielectric substrate, such as FR-4, which is a glass-reinforced epoxy laminate.
Composition of a Core PCB
The core PCB consists of the following components:
-
Substrate: The substrate is the base material of the PCB. It is usually made of FR-4, which offers good electrical insulation, mechanical strength, and thermal stability.
-
Copper Layers: Copper layers are bonded to the substrate using an adhesive. These layers are etched to create the desired circuit patterns. The number of copper layers depends on the complexity of the circuit design.
-
Prepreg: Prepreg (pre-impregnated) is a layer of glass fabric that is pre-coated with a partially cured resin. It is used to bond the core layers together and provide insulation between them.
-
Solder Mask: A solder mask is a protective coating applied to the outer layers of the PCB. It prevents accidental short circuits and protects the copper traces from oxidation and damage.
-
Silkscreen: Silkscreen is a layer of text and symbols printed on the PCB for identification and assembly purposes.
Importance of Core PCB
The core PCB plays a vital role in the overall performance and reliability of the printed circuit board. Here are some reasons why the core is crucial:
-
Mechanical Support: The core provides the necessary mechanical support to the PCB. It ensures that the board remains flat and stable, preventing warping or bending during the manufacturing process and use.
-
Electrical Insulation: The core material, such as FR-4, offers excellent electrical insulation properties. It prevents short circuits and ensures proper signal integrity by isolating the copper layers from each other.
-
Thermal Management: The core helps in dissipating heat generated by the electronic components. It allows for efficient thermal management, preventing overheating and ensuring the long-term reliability of the PCB.
-
Signal Integrity: The core plays a crucial role in maintaining signal integrity. It provides a stable platform for the copper layers, minimizing signal distortion and ensuring accurate signal transmission.
-
Manufacturability: The core material and its properties affect the manufacturability of the PCB. A well-designed core enables easier fabrication, assembly, and testing of the board.
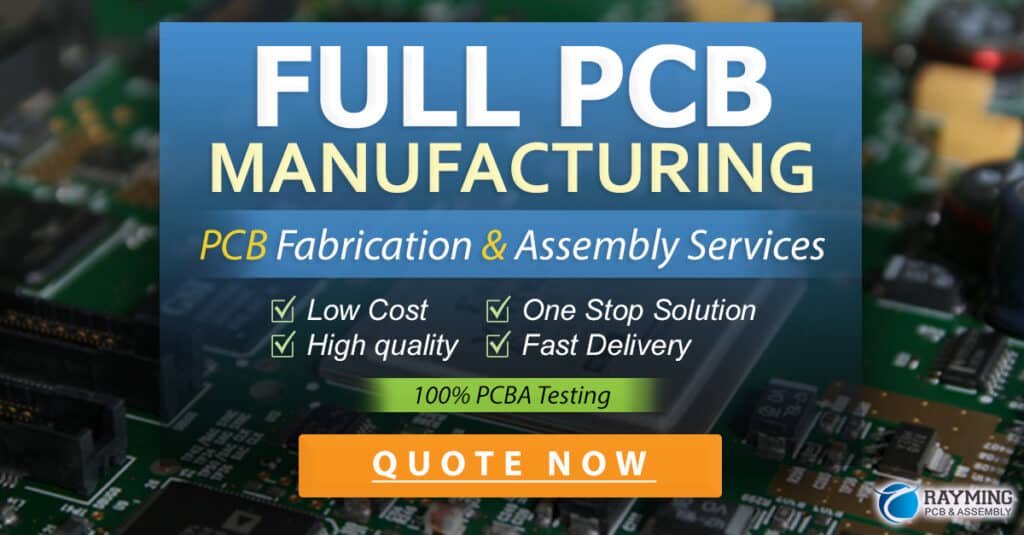
Types of Core PCB
There are several types of core PCBs, each with its own characteristics and applications. Let’s explore some common types:
1. Single-Layer Core PCB
A single-layer core PCB consists of a single substrate layer with Copper Foil bonded to one or both sides. It is the simplest and most cost-effective type of core PCB. Single-layer core PCBs are suitable for basic electronic circuits with low complexity.
2. Double-Layer Core PCB
A double-layer core PCB has two copper layers, one on each side of the substrate. The layers are interconnected using through-hole technology or via holes. Double-layer core PCBs offer more routing options and higher component density compared to single-layer boards.
3. Multi-Layer Core PCB
Multi-layer core PCBs consist of three or more layers of substrate and copper foil. The layers are bonded together using prepreg and laminated under high pressure and temperature. Multi-layer core PCBs are used for complex circuits that require high component density and advanced routing capabilities.
Type | Layers | Applications |
---|---|---|
Single-Layer | 1 | Simple circuits, low-cost applications |
Double-Layer | 2 | Moderate complexity, higher density |
Multi-Layer | 3+ | Complex circuits, advanced routing |
4. High Tg Core PCB
High Tg (glass transition temperature) core PCBs use substrates with higher glass transition temperatures compared to standard FR-4. These cores offer improved thermal stability and are suitable for high-temperature applications, such as automotive and aerospace electronics.
5. Flexible Core PCB
Flexible core PCBs use flexible substrates, such as polyimide or polyester, instead of rigid materials like FR-4. They are designed to bend and flex without damaging the circuit. Flexible core PCBs are commonly used in wearable electronics, medical devices, and applications where conformity to curved surfaces is required.
Manufacturing Process of Core PCB
The manufacturing process of a core PCB involves several steps. Here’s a brief overview of the process:
-
Material Selection: The appropriate substrate material, copper foil, and prepreg are selected based on the desired properties and application requirements.
-
Lamination: The substrate layers, copper foil, and prepreg are stacked and laminated together under high pressure and temperature. This process bonds the layers and creates a solid core.
-
Drilling: Holes are drilled through the core to accommodate through-hole components and create via connections between layers.
-
Plating: The drilled holes are plated with copper to establish electrical connections between layers.
-
Etching: The copper layers are selectively etched to create the desired circuit patterns. This is typically done using photolithography and chemical etching processes.
-
Solder Mask and Silkscreen: A solder mask is applied to the outer layers to protect the copper traces, and silkscreen is added for identification and assembly purposes.
-
Surface Finish: A surface finish, such as HASL (Hot Air Solder Leveling) or ENIG (Electroless Nickel Immersion Gold), is applied to the exposed copper areas to prevent oxidation and improve solderability.
Choosing the Right Core PCB
When selecting a core PCB for your project, consider the following factors:
-
Circuit Complexity: Choose a core type that can accommodate the complexity of your circuit design. Single-layer cores are suitable for simple circuits, while multi-layer cores are necessary for more complex designs.
-
Thermal Requirements: Consider the thermal management needs of your application. If your circuit generates significant heat, choose a core material with good thermal conductivity, such as high Tg FR-4 or metal-core PCBs.
-
Mechanical Demands: Evaluate the mechanical requirements of your project. If your PCB will be subjected to vibrations, impacts, or bending, consider using a flexible core or a reinforced substrate.
-
Cost: Consider the cost implications of different core types. Single-layer cores are generally the most cost-effective, while multi-layer cores and specialized materials like high Tg FR-4 may incur higher costs.
-
Manufacturing Capabilities: Ensure that your chosen core type is compatible with the manufacturing capabilities of your PCB fabricator. Some advanced core materials may require specialized processing techniques.
Frequently Asked Questions (FAQ)
-
What is the most common material used for PCB cores?
The most common material used for PCB cores is FR-4, which is a glass-reinforced epoxy laminate. FR-4 offers good electrical insulation, mechanical strength, and thermal stability. -
Can a PCB have multiple cores?
Yes, a PCB can have multiple cores. Multi-layer PCBs often consist of multiple core layers bonded together using prepreg. Each core layer can have its own set of copper layers and circuitry. -
What is the difference between a core and a prepreg in a PCB?
A core is a solid substrate layer with copper foil bonded to one or both sides. Prepreg, on the other hand, is a partially cured layer of glass fabric pre-coated with resin. Prepreg is used to bond the core layers together and provide insulation between them. -
How does the core thickness affect the performance of a PCB?
The core thickness can affect the electrical and mechanical properties of a PCB. Thicker cores provide better mechanical stability and can help in reducing signal interference. However, thicker cores may also increase the overall thickness of the PCB and limit the routing density. -
Can the core material be customized for specific applications?
Yes, the core material can be customized based on the specific requirements of an application. For example, high Tg FR-4 cores are used for high-temperature applications, while metal-core PCBs are used for enhanced thermal management. Specialized core materials can be selected to meet specific electrical, thermal, or mechanical demands.
Conclusion
The core of a PCB is a critical component that provides the foundation for the entire circuit board. It offers mechanical support, electrical insulation, thermal management, and signal integrity. Understanding the different types of core PCBs and their properties is essential for designing and manufacturing reliable and high-performance electronic devices.
When selecting a core PCB, consider factors such as circuit complexity, thermal requirements, mechanical demands, cost, and manufacturing capabilities. By choosing the right core material and configuration, you can ensure that your PCB meets the specific needs of your application.
As technology advances, new core materials and manufacturing techniques are being developed to address the ever-increasing demands of modern electronics. Staying informed about the latest advancements in core PCB technology can help you make informed decisions and stay ahead in the competitive world of Electronics Design and manufacturing.
Leave a Reply