Why is Pad to Pad Spacing Important?
Proper Pad to Pad (PP) spacing is essential for several reasons:
1. Manufacturability
Adequate spacing between pads allows for reliable soldering of components to the PCB. If pads are too close together, there is a risk of solder bridges forming, causing short circuits and compromising the integrity of the electrical connections.
2. Signal Integrity
Sufficient PP spacing helps minimize electromagnetic interference (EMI) and crosstalk between adjacent traces or pads. This is particularly important for high-speed digital circuits where maintaining signal integrity is critical.
3. Component Placement
PP spacing also influences component placement on the PCB. Components must have their leads or contacts properly aligned with the corresponding pads. Insufficient spacing can make it challenging or impossible to place components accurately.
4. Compliance with Industry Standards
Various industry standards and guidelines, such as those set by the Institute for Printed Circuits (IPC), specify minimum PP spacing requirements for different PCB Designs and applications. Adhering to these standards ensures compatibility and reliability.
Factors Affecting Pad to Pad Spacing
Several factors influence the determination of appropriate PP spacing:
1. PCB Manufacturing Capabilities
The minimum achievable PP spacing depends on the capabilities of the PCB manufacturer. Advanced manufacturing processes, such as high-density interconnect (HDI) PCBs, allow for smaller pad sizes and tighter spacing compared to standard PCB Fabrication techniques.
2. Component Package Type
The package type of the components being used on the PCB affects the required PP spacing. Different package types, such as surface-mount devices (SMDs) or through-hole components, have varying lead pitches and sizes that dictate the minimum spacing between pads.
3. PCB Layer Stack-up
The number of layers in the PCB stack-up and the thickness of the dielectric material between layers impact PP spacing. Multilayer PCBs with thinner dielectrics enable tighter spacing compared to thicker, single-layer boards.
4. Electrical Requirements
The electrical requirements of the circuit, such as voltage levels and current carrying capacity, influence PP spacing. Higher voltage or current applications may require larger pad sizes and greater spacing to ensure electrical isolation and prevent arcing.
Pad to Pad Spacing Design Guidelines
When designing PCBs, engineers should follow certain guidelines to ensure proper PP spacing:
1. Refer to Industry Standards
Consult industry standards, such as IPC-2221 or IPC-7351, for recommended PP spacing values based on the specific PCB design and manufacturing requirements. These standards provide detailed guidelines for different Component Types and packaging technologies.
2. Consider Manufacturing Capabilities
Engage with the PCB manufacturer early in the design process to understand their specific capabilities and limitations regarding PP spacing. This helps ensure that the designed spacing is achievable and compatible with the manufacturing process.
3. Use CAD Tools with Design Rule Checks
Utilize computer-aided design (CAD) tools that incorporate design rule checks (DRC) to automatically verify PP spacing compliance. These tools can flag any violations of spacing rules and help optimize the PCB layout.
4. Perform Signal Integrity Simulations
Conduct signal integrity simulations to analyze the impact of PP spacing on signal quality and electromagnetic compatibility (EMC). These simulations help identify potential issues and optimize spacing for critical signals.
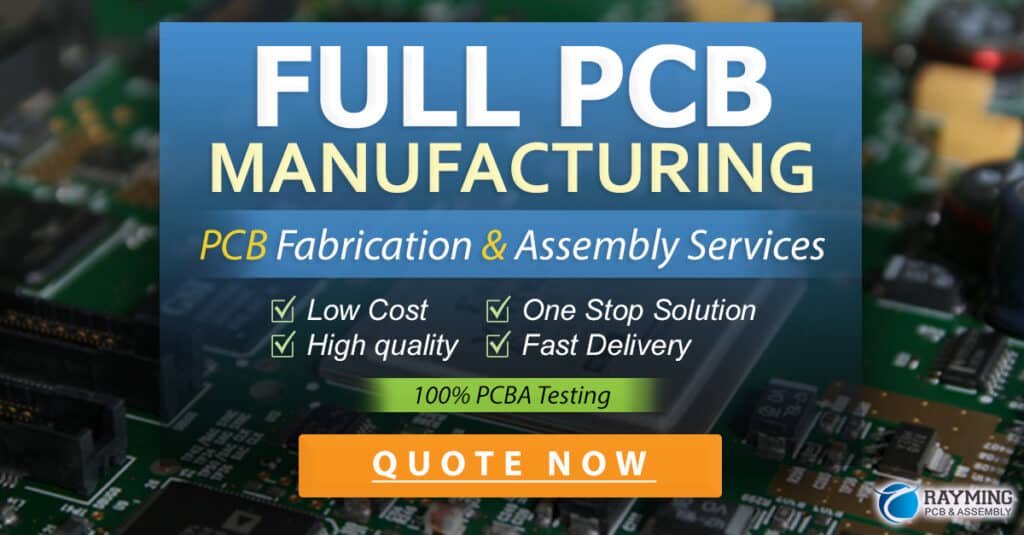
Common Pad to Pad Spacing Values
The following table provides a general overview of typical PP spacing values for different component package types:
Package Type | Typical Pad to Pad Spacing |
---|---|
Discrete SMD (0402, 0603) | 0.5 mm – 0.8 mm |
Discrete SMD (0805, 1206) | 0.8 mm – 1.2 mm |
SOT-23 | 0.65 mm – 0.95 mm |
SOIC | 1.27 mm |
QFP | 0.5 mm – 0.8 mm |
BGA | 0.5 mm – 1.0 mm |
Note: These values are for reference only. Always consult the specific component datasheet and PCB manufacturing capabilities for accurate spacing requirements.
Pad to Pad Spacing Measurement Techniques
Measuring PP spacing accurately is crucial for quality control and ensuring compliance with design specifications. Several techniques are commonly used:
1. Optical Measurement
Optical measurement systems, such as automated optical inspection (AOI) machines or microscopes with calibrated reticles, can measure PP spacing non-destructively. These systems capture high-resolution images of the PCB and use image processing algorithms to measure the distance between pad centers.
2. Coordinate Measuring Machines (CMM)
CMMs are precision measurement devices that use a probe to physically contact the PCB surface and measure the coordinates of specific points. They can accurately measure PP spacing by probing the center points of adjacent pads and calculating the distance between them.
3. X-Ray Inspection
For PCBs with hidden or obstructed pads, such as those in ball grid array (BGA) packages, X-ray inspection techniques are used. X-ray systems generate images of the internal structure of the PCB, allowing measurement of PP spacing even when pads are not directly accessible.
FAQ
1. What is the minimum Pad to Pad spacing for a standard SMD component?
The minimum PP spacing for a standard SMD component depends on the specific package size and PCB manufacturing capabilities. Typically, for commonly used package sizes like 0402 or 0603, the minimum spacing ranges from 0.5 mm to 0.8 mm. However, it is always recommended to consult the component datasheet and discuss with the PCB manufacturer to determine the appropriate spacing for a given design.
2. How does Pad to Pad spacing affect signal integrity?
PP spacing plays a crucial role in maintaining signal integrity on a PCB. Inadequate spacing between pads can lead to increased electromagnetic interference (EMI) and crosstalk between adjacent signals. When pads are too close together, the electromagnetic fields of the signals can couple, causing distortion and compromising signal quality. Sufficient PP spacing helps minimize these effects by providing adequate separation between signal paths.
3. Can Pad to Pad spacing be different on different layers of a multilayer PCB?
Yes, PP spacing can vary on different layers of a multilayer PCB. The spacing requirements may differ based on factors such as signal type, layer function, and dielectric thickness. For example, power and ground planes may have different spacing requirements compared to signal layers. Additionally, inner layers may allow for tighter spacing due to the controlled dielectric environment, while Outer Layers may require more generous spacing to accommodate soldering and component placement.
4. What are the consequences of violating Pad to Pad spacing rules?
Violating PP spacing rules can lead to various issues in PCB manufacturing and assembly. Some of the consequences include:
- Solder bridges: Insufficient spacing can cause solder to bridge between adjacent pads during the soldering process, creating unintended electrical connections and short circuits.
- Component placement difficulties: If PP spacing is too tight, it becomes challenging to accurately place components on the PCB, leading to misalignment and assembly errors.
- Reduced manufacturing yield: Violations of spacing rules can result in a higher rate of manufacturing defects, lowering the overall yield and increasing production costs.
- Reliability issues: Improper spacing can compromise the long-term reliability of the PCB, as it may be more susceptible to electrical failures or physical damage.
5. How can I ensure proper Pad to Pad spacing in my PCB design?
To ensure proper PP spacing in your PCB design, follow these best practices:
- Refer to industry standards and guidelines, such as IPC-2221 or IPC-7351, for recommended spacing values based on your specific design requirements and component types.
- Consult with your PCB manufacturer early in the design process to understand their capabilities and limitations regarding PP spacing.
- Use CAD tools that incorporate design rule checks (DRC) to automatically verify spacing compliance and flag any violations.
- Perform signal integrity simulations to analyze the impact of PP spacing on signal quality and make necessary adjustments.
- Review and validate the PCB layout thoroughly, paying close attention to critical areas where spacing is tight or components are densely populated.
By following these guidelines and collaborating with PCB manufacturing experts, you can ensure that your design adheres to proper PP spacing rules, minimizing potential issues and ensuring a successful PCB fabrication and assembly process.
Leave a Reply