What is PCB Warpage?
PCB warpage, also known as PCB bow and twist, is a common issue that occurs during the manufacturing process of printed circuit boards (PCBs). It refers to the unintentional deformation or distortion of the PCB substrate, causing it to deviate from its intended flat and planar shape. PCB warpage can lead to various problems, such as difficulties in component assembly, reduced reliability, and compromised performance of the final electronic device.
Types of PCB Warpage
There are two main types of PCB warpage:
-
Bow: Bow refers to the curvature of the PCB along its length or width. It occurs when the PCB substrate bends or curves in a concave or convex manner, forming an arc-like shape.
-
Twist: Twist, on the other hand, refers to the rotational deformation of the PCB. It happens when the corners of the PCB substrate are not in the same plane, causing the board to have a twisted or warped appearance.
Both bow and twist can occur simultaneously on a PCB, leading to complex warpage patterns.
Causes of PCB Warpage
Several factors can contribute to the development of PCB warpage during the manufacturing process:
-
Thermal Stress: PCBs undergo multiple heating and cooling cycles during the fabrication process, such as during lamination, soldering, and reflow. The uneven distribution of heat and the different thermal expansion coefficients of the materials used in the PCB stackup can lead to thermal stress, resulting in warpage.
-
Material Selection: The choice of materials used in the PCB stackup plays a crucial role in determining the susceptibility to warpage. The mismatch in the coefficient of thermal expansion (CTE) between the copper layers, dielectric materials, and solder mask can cause differential expansion and contraction, leading to warpage.
-
Copper Distribution: The distribution of copper on the PCB layers can also influence warpage. Uneven copper distribution, such as having more copper on one side of the board compared to the other, can create an imbalance in thermal expansion and lead to warpage.
-
Manufacturing Process: Various aspects of the manufacturing process, such as the lamination pressure, cooling rate, and handling techniques, can affect the likelihood of PCB warpage. Improper process control and handling can introduce stresses and contribute to warpage.
Impact of PCB Warpage
PCB warpage can have several detrimental effects on the manufacturing process and the final product:
-
Assembly Challenges: Warped PCBs can pose difficulties during the component assembly process. The uneven surface of the PCB can affect the placement accuracy of components, leading to misalignments, poor soldering, and potential short circuits. This can result in increased assembly time, higher rework rates, and reduced production yields.
-
Reliability Issues: Warped PCBs can compromise the reliability of the electronic device. The stress induced by warpage can cause solder joint failures, component cracking, and reduced mechanical strength of the board. These issues can lead to premature device failure and decreased product lifespan.
-
Performance Degradation: In some cases, PCB warpage can impact the electrical performance of the device. Warpage can affect the impedance of high-speed signal traces, leading to signal integrity issues. It can also cause changes in the capacitance and inductance of the PCB, affecting the overall circuit behavior.
-
Compatibility Problems: Warped PCBs may not fit properly into their designated enclosures or mating connectors. This can result in alignment issues, poor contact, and mechanical stress on the components and the board itself. Compatibility problems can hinder the final assembly and integration of the electronic device.
Measuring and Quantifying PCB Warpage
To control and mitigate PCB warpage, it is essential to have methods for measuring and quantifying the extent of warpage. Several techniques are commonly used in the industry:
-
3D Scanning: 3D scanning technologies, such as structured light scanning or laser scanning, can capture the surface topology of the PCB. These scans provide detailed measurements of the warpage profile, allowing for quantitative analysis and comparison against specified tolerances.
-
Shadow Moiré: Shadow moiré is an optical measurement technique that uses the interference pattern created by a grating and a light source to measure surface deformations. It provides a visual representation of the warpage profile and allows for quantitative measurements.
-
Coordinate Measuring Machine (CMM): CMMs are precision measurement devices that can accurately measure the dimensions and geometry of a PCB. By measuring multiple points on the PCB surface, a CMM can generate a 3D profile of the warpage.
-
Warpage Gauges: Warpage gauges are specialized tools designed to measure the maximum bow and twist of a PCB. These gauges typically have a flat reference surface and movable indicators that can quantify the deviation of the PCB from the reference plane.
Measurement Technique | Advantages | Disadvantages |
---|---|---|
3D Scanning | High accuracy, detailed warpage profile | Expensive equipment, data processing required |
Shadow Moiré | Visual representation, quantitative measurements | Limited resolution, sensitive to surface reflectivity |
CMM | High accuracy, 3D profile generation | Slow measurement process, requires skilled operators |
Warpage Gauges | Simple and quick measurements, low cost | Limited to maximum bow and twist, no detailed profile |
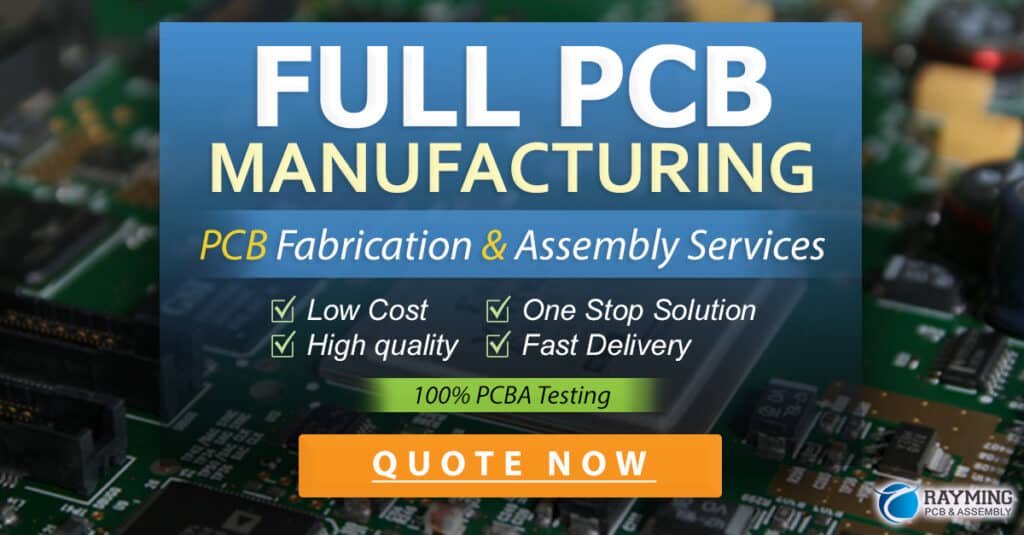
Controlling and Mitigating PCB Warpage
To minimize the occurrence and impact of PCB warpage, several strategies can be employed during the design and manufacturing stages:
-
Material Selection: Choosing materials with similar CTEs for the PCB stackup can help reduce the mismatch in thermal expansion and minimize warpage. Using high-quality, dimensionally stable materials can also contribute to improved warpage performance.
-
Balanced Copper Distribution: Designing the PCB with a balanced copper distribution across the layers can help mitigate warpage. Techniques such as copper thieving, where unused areas are filled with copper, can be used to achieve a more even copper distribution.
-
Optimized Stackup Design: The PCB stackup should be designed to minimize the CTE mismatch between layers. Symmetrical stackups, where the layer arrangement is mirrored about the center, can help balance the thermal stresses and reduce warpage.
-
Process Control: Strict control over the manufacturing process parameters, such as lamination pressure, temperature profiles, and cooling rates, can help minimize the introduction of stresses that lead to warpage. Following best practices and adhering to industry standards can contribute to reduced warpage.
-
Panelization Techniques: Proper panelization techniques, such as using symmetrical panel layouts and incorporating stress-relief features, can help distribute the stresses evenly across the panel and reduce localized warpage.
-
Post-Processing: In some cases, post-processing techniques can be employed to correct or mitigate PCB warpage. Techniques such as baking, where the PCB is subjected to a controlled heating process, can help relieve residual stresses and flatten the board.
Frequently Asked Questions (FAQ)
- What is the difference between bow and twist in PCB warpage?
-
Bow refers to the curvature of the PCB along its length or width, while twist refers to the rotational deformation of the PCB, causing the corners to be in different planes.
-
What are the main causes of PCB warpage?
-
The main causes of PCB warpage include thermal stress, material selection, copper distribution, and manufacturing process variations.
-
How does PCB warpage affect the assembly process?
-
PCB warpage can cause difficulties in component placement, leading to misalignments, poor soldering, and potential short circuits. It can increase assembly time, rework rates, and reduce production yields.
-
What techniques are used to measure and quantify PCB warpage?
-
Techniques used to measure PCB warpage include 3D scanning, shadow moiré, coordinate measuring machines (CMMs), and warpage gauges. Each technique has its advantages and disadvantages in terms of accuracy, speed, and cost.
-
How can PCB warpage be controlled and mitigated during the design and manufacturing stages?
- PCB warpage can be controlled and mitigated through careful material selection, balanced copper distribution, optimized stackup design, strict process control, proper panelization techniques, and post-processing methods such as baking.
Conclusion
PCB warpage, encompassing both bow and twist, is a critical issue in the manufacturing of printed circuit boards. It can lead to assembly challenges, reliability issues, performance degradation, and compatibility problems. Understanding the causes and impact of PCB warpage is crucial for designers and manufacturers to take proactive measures in mitigating its occurrence.
By employing techniques such as careful material selection, balanced copper distribution, optimized stackup design, and strict process control, the likelihood of PCB warpage can be reduced. Measuring and quantifying warpage using various methods allows for effective monitoring and quality control.
Addressing PCB warpage requires a collaborative effort between design teams and manufacturing partners. By implementing best practices and continuously refining processes, the electronics industry can minimize the impact of warpage and ensure the production of high-quality, reliable PCBs.
As technology advances and miniaturization trends continue, the challenges posed by PCB warpage will remain an important consideration. Ongoing research and development efforts in materials science, manufacturing technologies, and simulation tools will play a vital role in further understanding and mitigating this complex phenomenon.
Leave a Reply