Introduction to PCB Drilled Holes
Printed Circuit Boards (PCBs) are essential components in modern electronics, providing a platform for interconnecting electronic components. One crucial aspect of PCB manufacturing is the creation of drilled holes, which serve various purposes such as component mounting, electrical connectivity, and heat dissipation. In this article, we will explore the different types of PCB drilled holes, their characteristics, and their applications.
Types of PCB Drilled Holes
Through Holes
Through holes are the most common type of drilled holes found in PCBs. As the name suggests, these holes pass completely through the PCB, creating a connection between the top and bottom layers of the board. Through holes are primarily used for mounting through-hole components, such as resistors, capacitors, and connectors.
Characteristics of Through Holes
- Drilled completely through the PCB
- Typically plated with a conductive material (e.g., copper) to establish electrical connectivity
- Suitable for through-hole component mounting
- Provides mechanical stability for components
- Can be used for via connections between layers
Applications of Through Holes
- Mounting through-hole components
- Providing electrical connectivity between layers
- Mechanical reinforcement of the PCB
- Heat dissipation for power components
Blind Vias
Blind vias are drilled holes that start from one surface of the PCB and terminate at an inner layer without passing through the entire board. These holes are not visible from the opposite side of the PCB. Blind vias are commonly used in high-density PCB designs to save space and improve signal integrity.
Characteristics of Blind Vias
- Drilled from one surface of the PCB to an inner layer
- Not visible from the opposite side of the board
- Requires precise depth control during drilling
- Enables higher component density and more compact designs
- Improves signal integrity by reducing the length of interconnections
Applications of Blind Vias
- High-density PCB designs
- Connecting surface components to inner layers
- Reducing signal path length and improving signal integrity
- Saving space on the PCB surface
Buried Vias
Buried vias are drilled holes that connect inner layers of a multi-layer PCB without reaching either the top or bottom surface of the board. These vias are completely hidden within the PCB stack-up. Buried vias are used to create complex interconnections between inner layers and to optimize signal routing.
Characteristics of Buried Vias
- Drilled between inner layers of a multi-layer PCB
- Not visible from either the top or bottom surface of the board
- Requires precise alignment and registration of inner layers
- Enables intricate interconnections between inner layers
- Improves signal integrity and reduces electromagnetic interference (EMI)
Applications of Buried Vias
- Multi-layer PCB designs with complex interconnections
- Optimizing signal routing between inner layers
- Reducing crosstalk and EMI
- Creating shielded or controlled impedance signal paths
Micro Vias
Micro vias are small-diameter drilled holes, typically less than 150 microns (0.15 mm) in diameter. These vias are used in high-density interconnect (HDI) PCB designs to achieve fine-pitch component mounting and high-density interconnections. Micro vias can be blind, buried, or stacked, depending on the design requirements.
Characteristics of Micro Vias
- Small diameter, typically less than 150 microns
- Enables high-density interconnections and fine-pitch component mounting
- Can be blind, buried, or stacked
- Requires advanced drilling and plating techniques
- Improves signal integrity and reduces signal path length
Applications of Micro Vias
- HDI PCB designs
- Mounting fine-pitch components, such as ball grid arrays (BGAs) and chip-scale packages (CSPs)
- Creating high-density interconnections between layers
- Reducing signal path length and improving signal integrity
Backdrilled Holes
Backdrilled holes, also known as controlled depth drilling, are used to remove unwanted portions of through holes in high-speed PCB designs. The process involves drilling a larger diameter hole from the backside of the PCB to a specific depth, effectively removing the unused portion of the plated through hole. Backdrilling helps to reduce signal reflections and improve signal integrity.
Characteristics of Backdrilled Holes
- Larger diameter hole drilled from the backside of the PCB
- Removes unwanted portions of plated through holes
- Requires precise depth control and alignment
- Reduces signal reflections and improves signal integrity
- Commonly used in high-speed PCB designs
Applications of Backdrilled Holes
- High-speed digital PCB designs
- Removing unused portions of plated through holes
- Reducing signal reflections and improving signal quality
- Optimizing signal paths for critical high-speed signals
PCB Drilled Hole Sizes and Tolerances
The size and tolerance of PCB drilled holes are critical factors in ensuring proper component fit and reliable electrical connections. The hole size is determined by the component lead diameter and the required clearance for soldering or press-fitting. Tolerances are specified to account for variations in drilling and plating processes.
Hole Type | Typical Diameter Range | Tolerance |
---|---|---|
Through Holes | 0.3 mm – 6.0 mm | ±0.05 mm |
Blind Vias | 0.2 mm – 1.0 mm | ±0.025 mm |
Buried Vias | 0.2 mm – 1.0 mm | ±0.025 mm |
Micro Vias | 0.05 mm – 0.15 mm | ±0.01 mm |
It is essential to work closely with the PCB manufacturer to ensure that the drilled hole sizes and tolerances meet the design requirements and are compatible with the manufacturing capabilities.
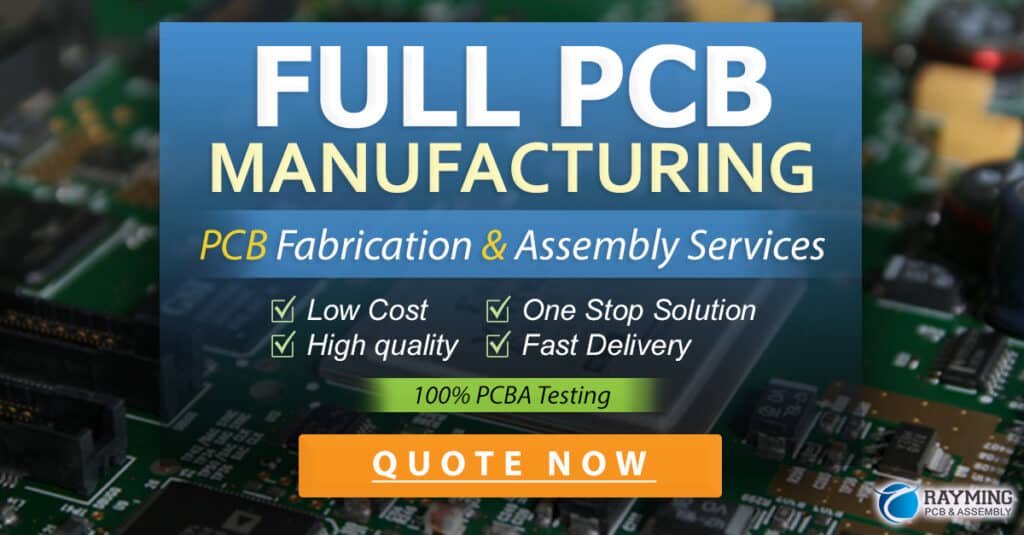
Frequently Asked Questions (FAQ)
-
What is the difference between through holes and vias?
Through holes are drilled holes that pass completely through the PCB, while vias are drilled holes that connect different layers of the PCB. Through holes are primarily used for mounting components, while vias are used for establishing electrical connections between layers. -
Can blind vias and buried vias be used in the same PCB?
Yes, blind vias and buried vias can be used together in the same PCB design. This combination allows for complex interconnections between layers and optimizes signal routing while saving space on the board surface. -
What are the advantages of using micro vias in PCB design?
Micro vias offer several advantages in PCB design, including higher component density, improved signal integrity, and reduced signal path length. They enable the mounting of fine-pitch components and create high-density interconnections between layers, making them essential for HDI PCB designs. -
How does backdrilling improve signal integrity in high-speed PCBs?
Backdrilling removes unwanted portions of plated through holes in high-speed PCB designs. By removing these unused portions, backdrilling reduces signal reflections and improves signal integrity. This technique helps to optimize signal paths and maintain signal quality for critical high-speed signals. -
What factors should be considered when specifying PCB drilled hole sizes and tolerances?
When specifying PCB drilled hole sizes and tolerances, several factors should be considered, including the component lead diameter, required clearance for soldering or press-fitting, and the manufacturing capabilities of the PCB fabricator. It is essential to work closely with the manufacturer to ensure that the specified hole sizes and tolerances are achievable and meet the design requirements.
Conclusion
PCB drilled holes play a vital role in the functionality and performance of electronic devices. Understanding the different types of drilled holes, their characteristics, and applications is crucial for designing reliable and efficient PCBs. Through holes, blind vias, buried vias, micro vias, and backdrilled holes each serve specific purposes and offer unique advantages in PCB design.
By selecting the appropriate type of drilled holes and specifying the correct sizes and tolerances, designers can create PCBs that meet the requirements of their applications, whether it’s high-density component mounting, complex interconnections between layers, or optimized signal routing for high-speed designs.
As technology advances and electronic devices become more compact and sophisticated, the importance of PCB drilled holes will continue to grow. Designers and manufacturers must stay up-to-date with the latest techniques and best practices to ensure the quality and reliability of their PCB designs.
Leave a Reply