Early Days of PCBs
The history of printed circuit boards (PCBs) dates back to the early 20th century. The concept of creating an electrical connection using a conductive material on an insulating base was first patented by Albert Hanson, a German inventor, in 1903. However, it took several decades before this idea was put into practical use.
In the 1920s, Charles Ducas, an American inventor, created a method of electroplating circuit patterns onto an insulated surface. This process involved printing the circuit pattern on the substrate using a stencil, then electroplating the exposed areas with copper.
During World War II, the development of PCBs accelerated due to the need for more compact and reliable electronic equipment in military applications. In the 1940s, Paul Eisler, an Austrian engineer, developed a method of etching copper foil on a non-conductive substrate to create circuit patterns. This technique, known as the “printed wiring” or “etched wiring” method, became the basis for modern PCB manufacturing.
Year | Milestone |
---|---|
1903 | Albert Hanson patents the concept of creating electrical connections on an insulating base |
1920s | Charles Ducas develops a method of electroplating circuit patterns onto an insulated surface |
1940s | Paul Eisler develops the etched wiring method, laying the foundation for modern PCB manufacturing |
PCB Evolution in the 1950s and 1960s
In the 1950s, the U.S. Army Signal Corps developed a process called “Auto-Sembly” which used a combination of screen printing and dip soldering to produce PCBs. This process allowed for the mass production of PCBs and led to their widespread adoption in the electronics industry.
The introduction of through-hole technology in the 1960s further revolutionized PCB design and manufacturing. Through-hole components had leads that could be inserted into drilled holes on the PCB and soldered onto copper pads on the other side. This allowed for the creation of double-sided PCBs and the ability to mount components on both sides of the board.
Decade | Advancements |
---|---|
1950s | Auto-Sembly process developed, enabling mass production of PCBs |
1960s | Through-hole technology introduced, allowing for double-sided PCBs and component mounting on both sides |
The Rise of Surface Mount Technology (SMT)
The 1980s saw the emergence of Surface Mount Technology (SMT), which revolutionized PCB design and manufacturing. SMT components were smaller and had metal tabs or end caps that could be soldered directly onto the surface of the PCB. This eliminated the need for drilled holes and allowed for much higher component densities on the board.
SMT also enabled the use of smaller components, such as chip resistors and capacitors, which further reduced the size of PCBs. The adoption of SMT led to the development of new soldering techniques, such as reflow soldering, which used a conveyor belt to pass PCBs through a high-temperature oven to melt the solder and create electrical connections.
Benefits of SMT over Through-Hole Technology
- Higher component density
- Smaller PCB sizes
- Improved electrical performance
- Faster assembly processes
- Lower production costs
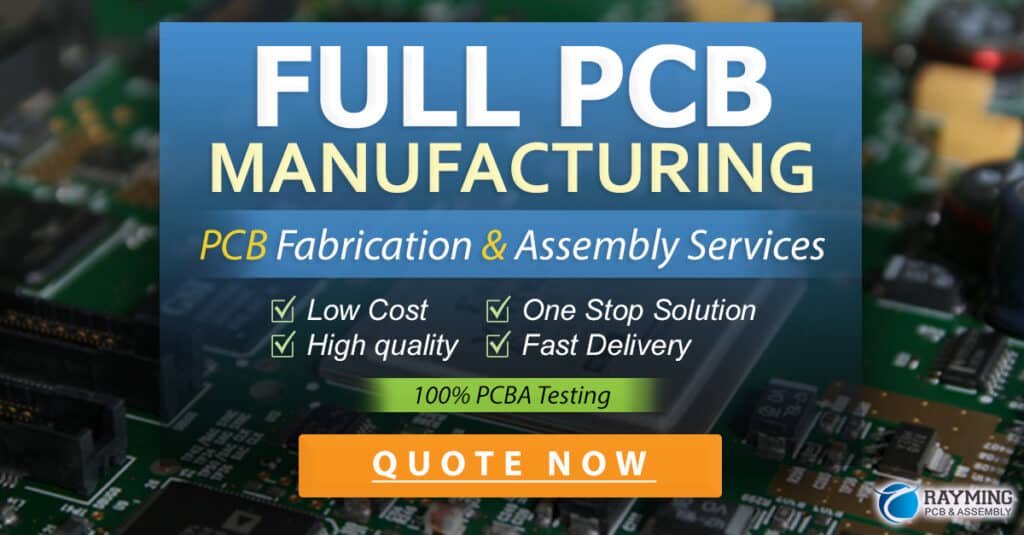
Advancements in PCB Materials
Throughout the history of PCBs, various materials have been used as substrates, including paper, phenolic resin, and fiberglass. In the 1970s, FR-4 (Flame Retardant 4) became the most widely used PCB substrate material due to its excellent electrical, mechanical, and thermal properties. FR-4 is a composite material composed of woven fiberglass cloth and epoxy resin.
In recent years, the demand for high-speed and high-frequency PCBs has led to the development of advanced substrate materials, such as polyimide, PTFE (polytetrafluoroethylene), and ceramic-based substrates. These materials offer superior dielectric properties, lower signal loss, and better thermal stability compared to traditional FR-4.
Material | Properties | Applications |
---|---|---|
FR-4 | Good electrical, mechanical, and thermal properties | General-purpose PCBs |
Polyimide | High heat resistance, excellent dielectric properties | High-temperature, high-frequency PCBs |
PTFE | Low dielectric constant, low loss tangent | High-frequency, microwave PCBs |
Ceramic | High thermal conductivity, low CTE | High-power, high-reliability PCBs |
The Advent of Multilayer PCBs
As electronic devices became more complex and compact, the need for higher interconnection density led to the development of multilayer PCBs. Multilayer PCBs consist of multiple layers of conductive material separated by insulating layers, allowing for more complex routing and higher component density.
The first multilayer PCBs were developed in the 1960s and typically consisted of two to four layers. As manufacturing processes improved, the number of layers in multilayer PCBs increased, with modern high-density interconnect (HDI) PCBs featuring up to 50 layers or more.
Advantages of Multilayer PCBs
- Higher interconnection density
- Improved signal integrity
- Reduced electromagnetic interference (EMI)
- Better heat dissipation
- Compact design
The Impact of Computer-Aided Design (CAD) on PCB Development
The introduction of computer-aided design (CAD) software in the 1980s revolutionized the PCB design process. CAD tools allowed engineers to create complex PCB layouts, simulate circuit behavior, and generate manufacturing data more efficiently than ever before.
As CAD software evolved, it integrated more advanced features, such as autorouting, design rule checking (DRC), and 3D modeling. These tools have greatly enhanced the accuracy, speed, and reliability of PCB design, enabling the development of more sophisticated and compact electronic devices.
CAD Feature | Benefit |
---|---|
Autorouting | Automatically routes traces between components, saving time and effort |
Design Rule Checking (DRC) | Verifies the PCB layout against a set of predefined design rules, ensuring manufacturability and reliability |
3D Modeling | Allows designers to visualize the PCB in 3D, helping to identify potential mechanical issues and optimize component placement |
Modern PCB Manufacturing Processes
Today, PCB manufacturing involves a combination of automated and manual processes to create high-quality, reliable boards. The main steps in modern PCB manufacturing include:
- PCB Design: Creating the PCB layout using CAD software
- PCB Fabrication: Manufacturing the bare PCB, including etching, drilling, and lamination
- PCB Assembly: Mounting and soldering components onto the PCB
- PCB Testing: Verifying the functionality and reliability of the assembled PCB
Automated optical inspection (AOI) and in-circuit testing (ICT) are widely used to ensure the quality and consistency of manufactured PCBs. AOI systems use high-resolution cameras to detect surface defects, while ICT employs a bed-of-nails fixture to test the electrical connectivity and functionality of the assembled PCB.
Future Trends in PCB Technology
As electronic devices continue to evolve, PCB technology must keep pace to meet the ever-increasing demands for performance, reliability, and miniaturization. Some of the future trends in PCB technology include:
- Embedded Components: Integrating passive components, such as resistors and capacitors, directly into the PCB substrate to save space and improve performance
- Flexible and Stretchable PCBs: Developing PCBs that can conform to non-planar surfaces and withstand bending and stretching for wearable and implantable electronics
- 3D Printed Electronics: Using additive manufacturing techniques to create PCBs with complex geometries and embedded components
- Advanced Materials: Exploring new substrate materials, such as graphene and carbon nanotubes, for high-performance, high-frequency applications
- Industry 4.0 Integration: Incorporating smart sensors, IoT connectivity, and data analytics into PCB manufacturing processes for enhanced automation, quality control, and predictive maintenance
As PCB technology continues to advance, it will enable the development of more innovative, efficient, and reliable electronic devices that shape our future.
Frequently Asked Questions (FAQ)
1. What is a printed circuit board (PCB)?
A printed circuit board (PCB) is a thin board made of insulating material with conductive pathways printed or etched onto its surface. It provides mechanical support and electrical interconnection for electronic components.
2. What are the main types of PCBs?
The main types of PCBs are:
- Single-sided PCBs: Components and conductive traces are on one side of the board
- Double-sided PCBs: Components and conductive traces are on both sides of the board
- Multilayer PCBs: Multiple layers of conductive material separated by insulating layers
3. What is the difference between through-hole and surface mount technology (SMT)?
Through-hole technology involves components with leads that are inserted into drilled holes on the PCB and soldered onto copper pads on the other side. SMT components have metal tabs or end caps that are soldered directly onto the surface of the PCB, eliminating the need for drilled holes.
4. What materials are commonly used in PCB fabrication?
Common materials used in PCB fabrication include:
- FR-4: A composite material made of woven fiberglass cloth and epoxy resin
- Polyimide: A high-temperature, high-performance material with excellent dielectric properties
- PTFE: A low-loss material with a low dielectric constant, suitable for high-frequency applications
- Ceramic: A material with high thermal conductivity and low coefficient of thermal expansion (CTE)
5. What role does computer-aided design (CAD) software play in PCB development?
CAD software is essential for creating complex PCB layouts, simulating circuit behavior, and generating manufacturing data. It includes features such as autorouting, design rule checking (DRC), and 3D modeling, which greatly enhance the accuracy, speed, and reliability of PCB design.
Leave a Reply