What is Selective Soldering?
Selective soldering is a process used in electronics manufacturing to solder specific components to a PCB-Assembly.com/printed-circuit-board/”>printed circuit board (PCB) using a precisely controlled solder fountain or mini wave. Unlike wave soldering, which solders all components on a PCB simultaneously, selective soldering targets only the desired through-hole components, leaving surface mount components and other areas of the board untouched.
This selective approach offers several advantages, including:
- Reduced thermal stress on sensitive components
- Increased flexibility in PCB Design
- Improved solder joint quality
- Reduced post-soldering cleaning requirements
How Does Selective Soldering Work?
The selective soldering process typically involves the following steps:
-
PCB Loading: The PCB is loaded into a fixture or carrier, which holds it securely during the soldering process.
-
Flux Application: A thin layer of flux is applied to the areas of the PCB that require soldering. Flux helps to remove oxides from the metal surfaces and promotes better solder wetting.
-
Preheating: The PCB is preheated to a specific temperature to minimize thermal shock and ensure better solder joint formation.
-
Soldering: The selective soldering machine uses a precisely controlled solder fountain or mini wave to apply molten solder to the desired areas of the PCB. The solder nozzle moves along a predefined path, soldering only the specified components.
-
Cooling: After soldering, the PCB is allowed to cool down gradually to prevent thermal stress and ensure the formation of strong solder joints.
-
Inspection: The soldered PCB undergoes visual inspection and, if necessary, automated optical inspection (AOI) to verify the quality of the solder joints.
Advantages of Selective Soldering
1. Reduced Thermal Stress
One of the primary advantages of selective soldering is the reduction of thermal stress on sensitive components. In wave soldering, the entire PCB is exposed to high temperatures, which can damage heat-sensitive components such as LEDs, connectors, and certain ICs. Selective soldering, on the other hand, targets only the specific areas that require soldering, minimizing the heat exposure to the rest of the board.
2. Increased Design Flexibility
Selective soldering allows for greater flexibility in PCB design. With wave soldering, all components must be able to withstand the high temperatures of the solder wave, limiting the types of components that can be used. Selective soldering enables the use of a wider range of components, including those with lower temperature tolerances, as they can be selectively soldered without exposing the entire board to high temperatures.
3. Improved Solder Joint Quality
Selective soldering can produce higher-quality solder joints compared to wave soldering. The precise control over the solder fountain or mini wave allows for optimal solder flow and wetting, resulting in consistent and reliable solder joints. Additionally, selective soldering minimizes the risk of solder bridges, icicles, and other defects commonly associated with wave soldering.
4. Reduced Post-Soldering Cleaning
Selective soldering can reduce the amount of post-soldering cleaning required. In wave soldering, the entire PCB is exposed to flux and solder, necessitating thorough cleaning to remove residues. With selective soldering, only the specific areas that were soldered need to be cleaned, reducing the overall cleaning time and the use of cleaning agents.
Challenges of Selective Soldering
Despite its numerous advantages, selective soldering also presents some challenges:
-
Initial Investment: Selective soldering machines can be more expensive than wave soldering machines, requiring a higher initial investment.
-
Programming and Setup: Each PCB design requires a specific soldering program and setup, which can be time-consuming and may require skilled operators.
-
Cycle Time: Selective soldering typically has a longer cycle time compared to wave soldering, as each component is soldered individually.
-
Fixturing: Designing and manufacturing fixtures for selective soldering can be complex and costly, especially for high-mix, low-volume production.
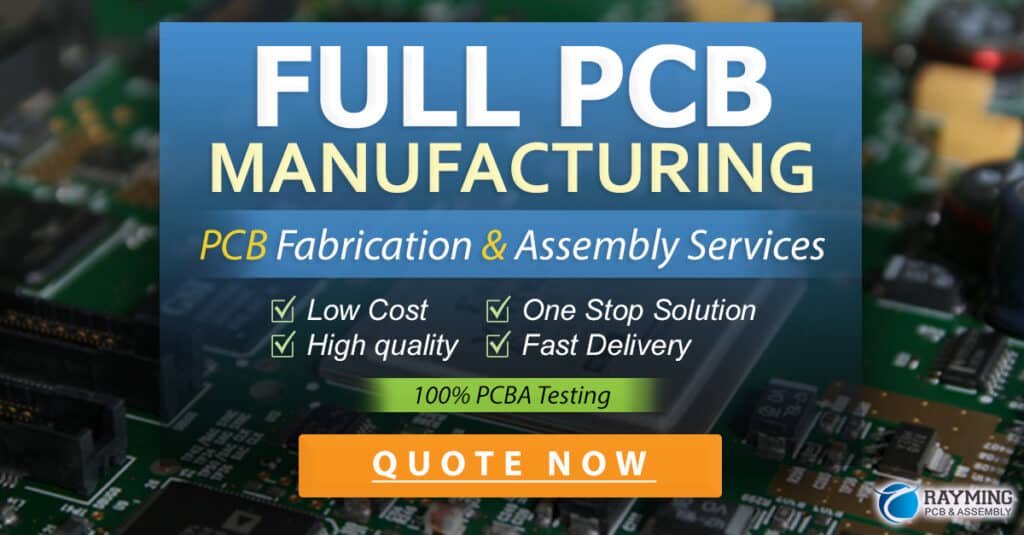
Selective Soldering Equipment
Selective soldering machines come in various configurations and sizes to accommodate different production requirements. Some common types of selective soldering equipment include:
-
Standalone Machines: These are dedicated selective soldering machines that can be integrated into an existing production line or used as standalone units.
-
In-Line Systems: In-line selective soldering systems are designed to be integrated into an automated production line, allowing for continuous flow of PCBs.
-
Multi-Station Machines: These machines feature multiple soldering stations, enabling simultaneous soldering of different components or PCBs for increased throughput.
-
Robotic Soldering Systems: Robotic selective soldering systems use articulated robots to position the solder nozzle, offering high flexibility and precision.
When choosing a selective soldering machine, consider factors such as:
- Production volume and mix
- PCB size and complexity
- Component Types and sizes
- Required cycle time
- Available floor space
- Budget
Process Optimization
To achieve the best results with selective soldering, it is essential to optimize the process parameters and settings. Some key factors to consider include:
-
Solder Nozzle Selection: Choose the appropriate solder nozzle size and shape based on the component leads and PCB layout.
-
Solder Temperature: Set the solder temperature according to the solder alloy being used and the thermal requirements of the components.
-
Preheat Temperature: Determine the optimal preheat temperature to minimize thermal shock and ensure proper solder flow.
-
Flux Type and Application: Select the appropriate flux type (e.g., no-clean, water-soluble) and ensure uniform application.
-
Soldering Path and Speed: Program the soldering path and adjust the speed to achieve optimal solder wetting and minimize cycle time.
Regular process monitoring and quality control are essential to maintain consistent solder joint quality. This can include visual inspection, automated optical inspection (AOI), and x-ray inspection for hidden solder joints.
Selective Soldering Applications
Selective soldering finds applications in various industries and product categories, including:
- Automotive electronics
- Aerospace and defense
- Medical devices
- Industrial controls
- Consumer electronics
- Telecommunications
Some specific examples of components and assemblies that often require selective soldering are:
- Connectors
- Through-hole components on mixed-technology PCBs
- Heat-sensitive components
- High-power components
- Odd-form components
- Pin-in-paste components
Selective Soldering vs. Other Soldering Methods
Selective soldering offers unique advantages compared to other soldering methods, such as wave soldering and hand soldering.
Selective Soldering vs. Wave Soldering
Factor | Selective Soldering | Wave Soldering |
---|---|---|
Thermal Stress | Lower | Higher |
Design Flexibility | Higher | Lower |
Solder Joint Quality | Higher | Lower |
Post-Soldering Cleaning | Reduced | More extensive |
Cycle Time | Longer | Shorter |
Initial Investment | Higher | Lower |
Selective Soldering vs. Hand Soldering
Factor | Selective Soldering | Hand Soldering |
---|---|---|
Consistency | Higher | Lower |
Speed | Faster | Slower |
Skill Requirements | Lower | Higher |
Scalability | Higher | Lower |
Initial Investment | Higher | Lower |
Future Trends in Selective Soldering
As the electronics industry continues to evolve, selective soldering technology is also advancing to meet new challenges and requirements. Some of the future trends in selective soldering include:
-
Increased Automation: Integration of selective soldering machines with robotic handling systems and automated inspection for end-to-end process automation.
-
Faster Cycle Times: Development of high-speed selective soldering machines to meet the demands of high-volume production.
-
Miniaturization: Adaptation of selective soldering technology to accommodate smaller components and denser PCB layouts.
-
Inline Process Control: Implementation of real-time process monitoring and control systems for improved quality and traceability.
-
Eco-Friendly Processes: Adoption of lead-free solders and environmentally friendly flux formulations to comply with environmental regulations.
Frequently Asked Questions (FAQ)
1. What types of components are best suited for selective soldering?
A: Selective soldering is ideal for through-hole components, particularly those that are heat-sensitive, high-power, or odd-form. It is also suitable for mixed-technology PCBs with both through-hole and surface-mount components.
2. Can selective soldering be used for high-volume production?
A: Yes, selective soldering can be used for high-volume production, especially with in-line systems and multi-station machines. However, the cycle time is generally longer compared to wave soldering.
3. Is selective soldering compatible with lead-free solders?
A: Yes, selective soldering can be used with lead-free solders. The process parameters, such as solder temperature and preheat settings, may need to be adjusted to accommodate the specific properties of lead-free solders.
4. How can I ensure consistent solder joint quality with selective soldering?
A: To ensure consistent solder joint quality, optimize process parameters, such as solder temperature, preheat settings, and flux application. Regularly monitor the process and perform quality inspections using visual, AOI, or x-ray methods.
5. What should I consider when selecting a selective soldering machine for my production line?
A: When choosing a selective soldering machine, consider factors such as production volume and mix, PCB size and complexity, component types and sizes, required cycle time, available floor space, and budget. Consult with equipment manufacturers and conduct thorough evaluations to find the best solution for your specific requirements.
Conclusion
Selective soldering is a versatile and precise method for soldering through-hole components on PCBs. It offers numerous advantages over traditional wave soldering, including reduced thermal stress, increased design flexibility, improved solder joint quality, and reduced post-soldering cleaning requirements.
By understanding the selective soldering process, its challenges, and the available equipment options, electronics manufacturers can make informed decisions when implementing selective soldering in their production lines. Optimizing process parameters, regular quality control, and staying updated with the latest trends and advancements in selective soldering technology are key to achieving consistent, high-quality results.
As the electronics industry continues to evolve, selective soldering will play an increasingly important role in meeting the demands for more complex and diverse PCB assemblies while ensuring reliability and cost-effectiveness.
Leave a Reply