Understanding the Basics of PCB Design
Before we dive into the tips and tricks, let’s quickly review the basics of PCB design. A PCB consists of a non-conductive substrate, usually made of fiberglass, with conductive copper traces printed on one or both sides. The copper traces connect the various electronic components mounted on the board.
PCBs can be classified based on the number of layers:
PCB Type | Description |
---|---|
Single-layer | Copper traces on one side of the substrate |
Double-layer | Copper traces on both sides of the substrate |
Multi-layer | Multiple layers of copper traces separated by insulating layers |
When designing a PCB, you need to consider factors such as:
- Component placement
- Trace width and spacing
- Via size and placement
- Power and ground planes
- Signal integrity and electromagnetic compatibility (EMC)
PCB Design Software and Tools
To create a PCB design, you will need to use specialized software. There are several options available, ranging from free and open-source to commercial tools. Some popular PCB design software include:
- KiCad (free and open-source)
- Eagle (free for non-commercial use, paid for commercial use)
- Altium Designer (commercial)
- OrCAD (commercial)
In addition to the PCB design software, you may also need other tools such as:
- Schematic capture software for creating circuit diagrams
- 3D modeling software for creating component footprints and enclosures
- Gerber viewer for reviewing and verifying the final PCB design files
Tips for Efficient PCB Design
1. Start with a Good Schematic
A well-organized and accurate schematic is the foundation of a successful PCB design. Ensure that your schematic is clear, easy to read, and follows standard conventions. Use descriptive labels for components and signals, and group related components together.
2. Choose the Right Component Footprints
When selecting components for your PCB, pay attention to their footprints. Footprints define the physical dimensions and pin layout of the components. Using the correct footprints ensures that the components will fit properly on the PCB and can be easily soldered.
3. Consider the PCB Stackup
The PCB stackup refers to the arrangement of copper layers and insulating layers in a multi-layer PCB. A proper stackup helps minimize signal integrity issues and improves the overall performance of the PCB. Work with your PCB manufacturer to determine the optimal stackup for your design.
4. Follow Design for Manufacturing (DFM) Guidelines
DFM guidelines ensure that your PCB can be easily and reliably manufactured. Some key DFM considerations include:
- Minimum trace width and spacing
- Minimum via size and drill hole size
- Clearance between components and the board edge
- Solder mask and silkscreen requirements
Consult with your PCB manufacturer to obtain their specific DFM guidelines.
5. Use a Grid System for Component Placement
Placing components on a grid helps create a neat and organized PCB layout. It also makes it easier to route traces and maintain consistent spacing between components. Choose a grid size that is appropriate for your component sizes and PCB dimensions.
6. Route Power and Ground Traces First
When routing traces on your PCB, start with the power and ground traces. These traces carry high currents and need to be wider than signal traces to minimize voltage drop and heat generation. Use solid copper planes for power and ground whenever possible.
7. Minimize Trace Length and Vias
Long traces and excessive use of vias can introduce signal integrity issues and increase manufacturing costs. Try to place components close together to minimize trace length, and use vias sparingly. When vias are necessary, use the smallest size that meets your design requirements.
8. Consider Signal Integrity and EMC
Signal integrity and EMC are critical factors in PCB design, especially for high-speed and sensitive circuits. Some tips to improve signal integrity and EMC include:
- Use controlled impedance traces for high-speed signals
- Provide adequate ground planes and shielding
- Avoid routing sensitive signals near noisy components or traces
- Use decoupling capacitors near power pins of ICs
9. Perform Design Rule Checks (DRC)
DRC is an automated process that checks your PCB design for potential errors and violations of design rules. Run DRC regularly during the design process to catch and fix issues early. Most PCB design software include built-in DRC tools.
10. Review and Verify the Final Design
Before sending your PCB design for manufacturing, thoroughly review and verify the final design files. Check for any missing or incorrect components, traces, or vias. Use a Gerber viewer to ensure that the exported files match your intended design.
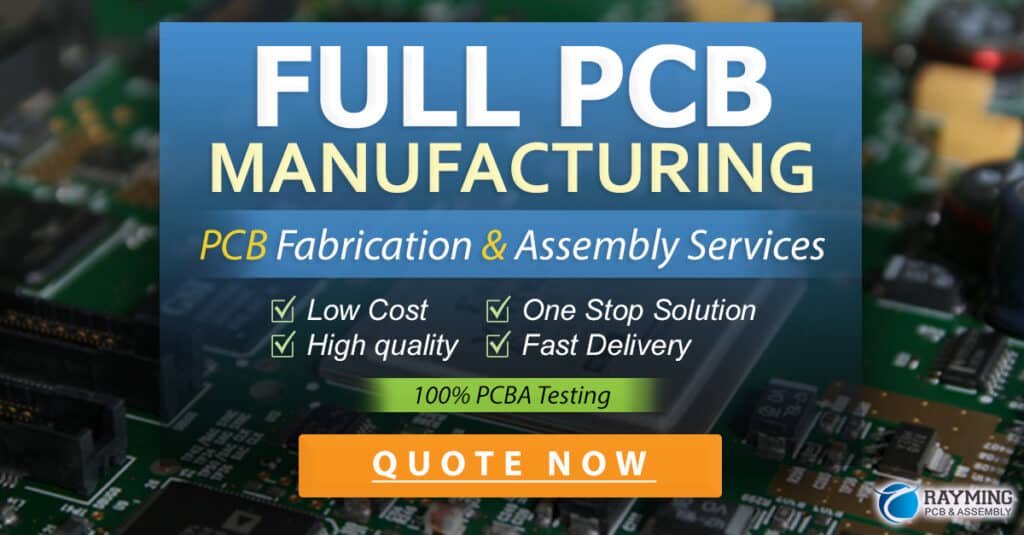
PCB Manufacturing and Assembly
Once your PCB design is complete, it’s time to move on to manufacturing and assembly. Here are some tips to ensure a smooth and successful process:
1. Choose a Reputable PCB Manufacturer
Select a PCB manufacturer with a proven track record of quality and reliability. Look for certifications such as ISO 9001 and UL. Request references and samples to evaluate their capabilities and quality.
2. Provide Comprehensive Documentation
Supply your PCB manufacturer with complete and accurate documentation, including:
- Gerber files
- Drill files
- Bill of Materials (BOM)
- Assembly drawings
- Special instructions or requirements
Clear and comprehensive documentation helps prevent misunderstandings and delays.
3. Consider PCB Surface Finish
The surface finish of your PCB affects its solderability, durability, and appearance. Common surface finishes include:
Surface Finish | Description |
---|---|
HASL (Hot Air Solder Leveling) | Dipped in molten solder and leveled with hot air |
ENIG (Electroless Nickel Immersion Gold) | Thin layer of gold over nickel |
OSP (Organic Solderability Preservative) | Organic coating to prevent oxidation |
Choose a surface finish that meets your design requirements and budget.
4. Specify PCB Testing Requirements
PCB testing helps ensure the quality and functionality of your boards. Common PCB testing methods include:
- Visual inspection
- Automated Optical Inspection (AOI)
- In-Circuit Testing (ICT)
- Functional testing
Discuss your testing requirements with your PCB manufacturer and agree on the appropriate testing methods for your project.
5. Plan for PCB Assembly
If your PCB requires component assembly, consider the following:
- Choose between through-hole or surface-mount components
- Provide a detailed BOM with part numbers and quantities
- Specify any special handling or assembly instructions
- Consider using an assembly service provided by your PCB manufacturer
Proper planning and communication can help ensure a smooth and efficient PCB assembly process.
Frequently Asked Questions (FAQ)
1. What is the difference between a schematic and a PCB layout?
A schematic is a graphical representation of the electrical connections and components in a circuit. It shows how the components are connected logically, but does not represent their physical placement. A PCB layout, on the other hand, is the physical design of the PCB, showing the actual placement and routing of components and traces.
2. How do I choose the right trace width for my PCB?
The appropriate trace width depends on several factors, such as:
- The current carrying capacity of the trace
- The desired voltage drop across the trace
- The available space on the PCB
You can use online trace width calculators or consult with your PCB manufacturer to determine the appropriate trace width for your design.
3. What is the purpose of a solder mask on a PCB?
A solder mask is a thin layer of polymer applied to the copper traces on a PCB. It serves several purposes:
- Protects the copper traces from oxidation and corrosion
- Prevents accidental short circuits during soldering
- Provides electrical insulation between adjacent traces
- Improves the appearance of the PCB
4. How can I reduce the cost of my PCB?
Some ways to reduce the cost of your PCB include:
- Minimizing the PCB size and layer count
- Using standard component sizes and footprints
- Choosing a cost-effective surface finish
- Ordering in larger quantities to take advantage of volume discounts
- Selecting a PCB manufacturer with competitive pricing
5. What is the typical turnaround time for PCB manufacturing?
The turnaround time for PCB manufacturing varies depending on factors such as:
- PCB complexity and layer count
- Quantity ordered
- Manufacturing process and capabilities of the PCB manufacturer
Typical turnaround times can range from a few days to several weeks. Rush services may be available for an additional cost.
Conclusion
Designing and manufacturing PCBs can be a complex and challenging process, but by following the tips and tricks outlined in this article, you can streamline your workflow and achieve better results. Remember to start with a good schematic, choose the right components and footprints, follow DFM guidelines, and carefully review and verify your final design.
When it comes to PCB manufacturing and assembly, choose a reputable manufacturer, provide comprehensive documentation, and plan for testing and assembly requirements. By taking a systematic and thorough approach to PCB design and manufacturing, you can create high-quality, reliable, and cost-effective PCBs for your projects.
Leave a Reply