What is PCB Silk-screen?
PCB silk-screen, also known as legend or nomenclature, is the layer of text, symbols, and artwork printed on the surface of a printed circuit board (PCB). It serves several important functions:
-
Component identification: Silk-screen labels components with their reference designators (e.g., R1, C2, U3) and values (e.g., 10K, 22μF, 74HC00), making it easier for engineers and technicians to locate and identify them during assembly, testing, and debugging.
-
Orientation indicators: Silk-screen often includes polarity markers, pin 1 indicators, and other symbols to show the correct orientation of components like diodes, electrolytic capacitors, and ICs.
-
Branding and aesthetics: Company logos, product names, version numbers, and decorative elements can be added to the silk-screen layer to enhance the appearance and branding of the PCB.
How is PCB Silk-screen Applied?
The silk-screen process involves applying ink through a fine mesh stencil onto the surface of the PCB. The stencil, also called a screen, has the desired artwork etched into it, allowing ink to pass through only in the areas where text or graphics should appear.
The process typically follows these steps:
-
Artwork preparation: The silk-screen artwork is designed using PCB layout software, ensuring that text and symbols are correctly sized, positioned, and oriented.
-
Screen fabrication: A fine mesh screen, usually made of polyester or stainless steel, is coated with a light-sensitive emulsion. The artwork is then exposed onto the screen, hardening the emulsion in the areas where ink should not pass through.
-
Ink application: The screen is placed over the PCB, and ink is applied using a squeegee. The ink is forced through the open areas of the screen onto the PCB surface.
-
Curing: The printed ink is then cured, typically using heat or ultraviolet (UV) light, to ensure good adhesion and durability.
Silk-screen Ink Types and Properties
Several types of ink can be used for PCB silk-screening, each with specific properties and curing requirements:
Ink Type | Composition | Curing Method | Durability | Cost |
---|---|---|---|---|
Epoxy | Two-part epoxy resin | Heat (120-150°C) | High | High |
UV-curable | Acrylic or polyester-based | UV light | High | Moderate |
Solvent-based | Acrylic or enamel | Air drying or heat (60-80°C) | Moderate | Low |
Epoxy inks offer the highest durability and resistance to abrasion, chemicals, and high temperatures, making them suitable for demanding applications. However, they are also the most expensive and require a higher curing temperature.
UV-curable inks provide good durability and faster curing times compared to epoxy inks. They are cured using UV light, which allows for a more controlled and energy-efficient process. UV-curable inks are a popular choice for high-volume PCB production.
Solvent-based inks are the most economical option and can be air-dried or heat-cured at lower temperatures. While they offer adequate durability for many applications, they are less resistant to abrasion and chemicals compared to epoxy and UV-curable inks.
Designing for Optimal Silk-screen Legibility
To ensure that the silk-screen text and symbols are easily readable and maintain their integrity during the PCB manufacturing process, consider the following guidelines:
Font Selection and Size
- Use sans-serif fonts like Arial, Helvetica, or Verdana for better legibility at small sizes.
- Maintain a minimum font size of 0.8mm (32 mils) for reference designators and 0.6mm (24 mils) for component values.
- Keep font stroke width between 0.15mm (6 mils) and 0.2mm (8 mils) for optimal clarity.
Spacing and Placement
- Provide sufficient spacing between text and components, typically at least 0.5mm (20 mils), to avoid overlapping or smudging during the silk-screen process.
- Orient text to read from left to right or bottom to top for easy readability when the PCB is mounted in its final orientation.
- Avoid placing text over pads, vias, or other conductive features to prevent short circuits or soldering issues.
Polarity and Orientation Markers
- Include polarity indicators for components like diodes, electrolytic capacitors, and LEDs, using industry-standard symbols (e.g., a triangle for the cathode of a diode).
- Use a small dot, triangle, or beveled edge to indicate pin 1 of ICs and connectors.
- Ensure that polarity and orientation markers are clearly visible and properly aligned with the corresponding components.
Silk-screen Curing Methods
After the silk-screen ink is applied to the PCB, it must be cured to ensure proper adhesion and durability. The curing process depends on the type of ink used:
Heat Curing
Epoxy and some solvent-based inks require heat curing. The PCBs are typically placed in a convection oven or passed through an infrared (IR) heater to evaporate solvents and activate the curing process.
- Epoxy inks: Cured at 120-150°C for 30-60 minutes
- Solvent-based inks: Cured at 60-80°C for 15-30 minutes
Heat curing provides a reliable and consistent method for achieving a durable silk-screen finish. However, it is energy-intensive and may cause warping or damage to heat-sensitive components if not controlled properly.
UV Curing
UV-curable inks are exposed to high-intensity UV light to trigger a rapid polymerization reaction, causing the ink to harden within seconds. UV curing offers several advantages:
- Fast curing times (typically 1-5 seconds)
- Low energy consumption compared to heat curing
- Minimal heat generation, reducing the risk of damaging components
- Consistent and controllable curing process
UV curing requires specialized equipment, such as UV lamps or LED arrays, and may have higher initial costs compared to heat curing. However, the faster curing times and lower energy consumption can lead to long-term cost savings and increased production efficiency.
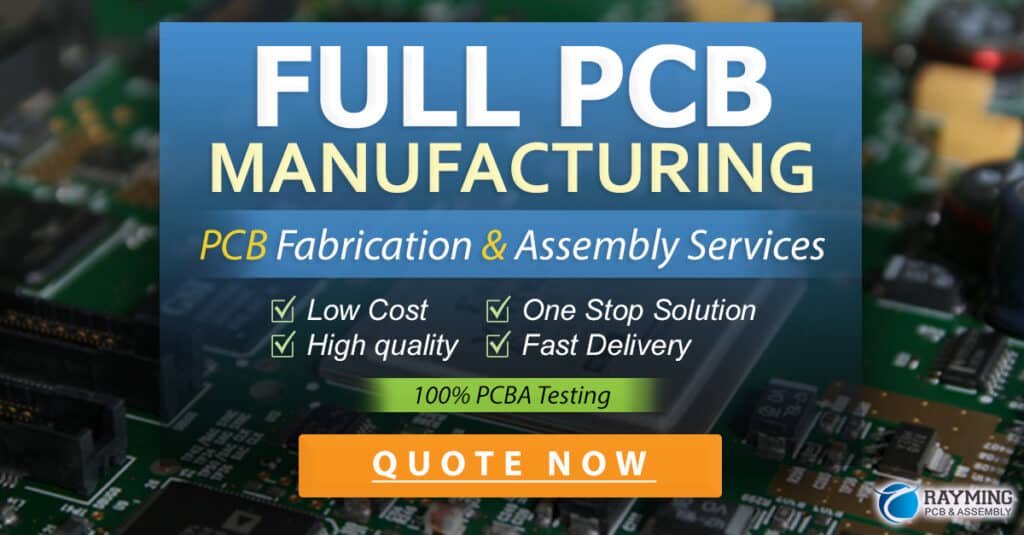
Quality Control and Inspection
To ensure the quality and consistency of the silk-screen layer, PCB manufacturers employ various inspection methods:
Visual Inspection
Skilled operators visually examine the silk-screened PCBs for defects such as:
- Incomplete or missing text or symbols
- Smudging, blurring, or inconsistent ink coverage
- Misaligned or overlapping text and components
- Contamination or foreign particles in the ink
Visual inspection is a simple and effective method for catching gross defects but may not detect subtle issues or consistently maintain quality across large production runs.
Automated Optical Inspection (AOI)
AOI systems use high-resolution cameras and image processing algorithms to compare the silk-screened PCBs against a digital reference image. AOI can detect defects such as:
- Incorrect or missing characters
- Font size or stroke width deviations
- Positional errors or misalignments
- Color or contrast inconsistencies
AOI provides a faster, more consistent, and more reliable inspection method compared to visual inspection. It can catch subtle defects and maintain quality across large production volumes, reducing the risk of defective PCBs reaching the end-user.
Frequently Asked Questions (FAQ)
1. Can silk-screen be applied to both sides of a PCB?
Yes, silk-screen can be applied to both the top and bottom sides of a PCB. However, it is more common to have silk-screen on the top side only, as this is the side where most components are placed and where the text and symbols are most useful for assembly and debugging.
2. Is it possible to have multiple colors of silk-screen on a single PCB?
While most PCBs use a single color (usually white) for the silk-screen layer, it is possible to have multiple colors. This requires additional screens and printing steps for each color, which increases production time and costs. Multi-color silk-screen is typically used for decorative purposes or to highlight important information on the PCB.
3. Can silk-screen be removed or modified after the PCB is manufactured?
Removing or modifying the silk-screen layer after the PCB is manufactured is difficult and not recommended. Attempting to scratch off or chemically remove the ink can damage the PCB surface and compromise its functionality. If changes to the silk-screen are necessary, it is best to revise the artwork and produce new PCBs.
4. How does the silk-screen layer affect the PCB’s electrical properties?
The silk-screen layer is a non-conductive, decorative layer that does not directly affect the PCB’s electrical properties. However, if the silk-screen ink is applied too thickly or if it overlaps with conductive features like pads or traces, it can cause issues such as poor solderability or short circuits. Proper design and quality control measures help prevent these issues.
5. Are there any environmental concerns associated with PCB silk-screening?
Some silk-screen inks, particularly solvent-based inks, may contain volatile organic compounds (VOCs) that can be harmful to the environment and human health if not handled properly. UV-curable and epoxy inks generally have lower VOC content and are considered more environmentally friendly. PCB manufacturers should follow proper safety and disposal guidelines when working with silk-screen inks to minimize environmental impact.
Leave a Reply