What is DFM and Why is it Important in PCB Manufacturing?
DFM stands for Design for Manufacturability. It is the process of optimizing a PCB design to ensure it can be manufactured efficiently and reliably at the lowest possible cost. DFM takes into account the capabilities and limitations of the PCB manufacturing process to identify and correct any potential issues before the design is sent for production.
DFM is crucial in PCB manufacturing for several reasons:
-
Cost Savings: By identifying and resolving potential manufacturing issues early in the design process, DFM helps avoid costly redesigns, production delays, and scrap.
-
Improved Quality: DFM ensures that the PCB design is compatible with the manufacturing process, resulting in higher quality boards with fewer defects.
-
Faster Time-to-Market: By streamlining the design and manufacturing process, DFM helps reduce lead times and bring products to market faster.
-
Enhanced Reliability: DFM takes into account factors such as material selection, component placement, and routing to improve the reliability and durability of the final product.
The Role of Gerber Files in PCB Manufacturing
Gerber files are the standard format used to describe the layout of a PCB for manufacturing. They contain all the necessary information for fabricating the board, including:
- Copper layers
- Solder mask
- Silkscreen
- Drill data
Gerber files are generated from the PCB design software and serve as the blueprint for the manufacturing process. They are essential for communicating the design intent to the PCB manufacturer and ensuring that the final product meets the specified requirements.
Converting Gerber Files to PCB production Data
To manufacture a PCB, the Gerber files must be converted into machine-readable instructions that guide the various production processes. This conversion process involves several steps:
1. Gerber File Import
The first step is to import the Gerber files into a CAM (Computer-Aided Manufacturing) system. The CAM software reads the Gerber data and creates a virtual representation of the PCB.
2. Design Rule Checking (DRC)
Once the Gerber data is imported, the CAM software performs a Design Rule Check to verify that the design meets the manufacturer’s capabilities and requirements. This includes checking for minimum trace widths, clearances, hole sizes, and other parameters.
3. Panelization
To optimize production efficiency, multiple PCBs are often grouped together into a single panel. The CAM software arranges the individual PCBs into an array and adds tooling features such as fiducials, coupons, and breakaway tabs.
4. Drill File Generation
The drill data from the Gerber files is used to generate machine-readable instructions for the drilling process. This includes specifying the size, location, and depth of each hole on the PCB.
5. Solder Mask and Silkscreen Preparation
The CAM software generates the necessary files for applying the solder mask and silkscreen layers to the PCB. This includes creating apertures and defining the areas to be covered by each layer.
6. Output File Generation
Finally, the CAM software generates the output files required for each step of the manufacturing process. These files are used to control the various machines and tools involved in PCB fabrication, such as:
- Photoplotter for imaging the copper layers
- Drill machine for drilling holes
- Solder mask and silkscreen application equipment
Process Step | Input | Output |
---|---|---|
Gerber File Import | Gerber Files | Virtual PCB Representation |
Design Rule Checking (DRC) | Virtual PCB Representation | DRC Report |
Panelization | Virtual PCB Representation | Panelized PCB Layout |
Drill File Generation | Drill Data from Gerber Files | Machine-Readable Drill Instructions |
Solder Mask and Silkscreen | Virtual PCB Representation | Solder Mask and Silkscreen Files |
Output File Generation | Virtual PCB Representation | Machine-Specific Output Files |
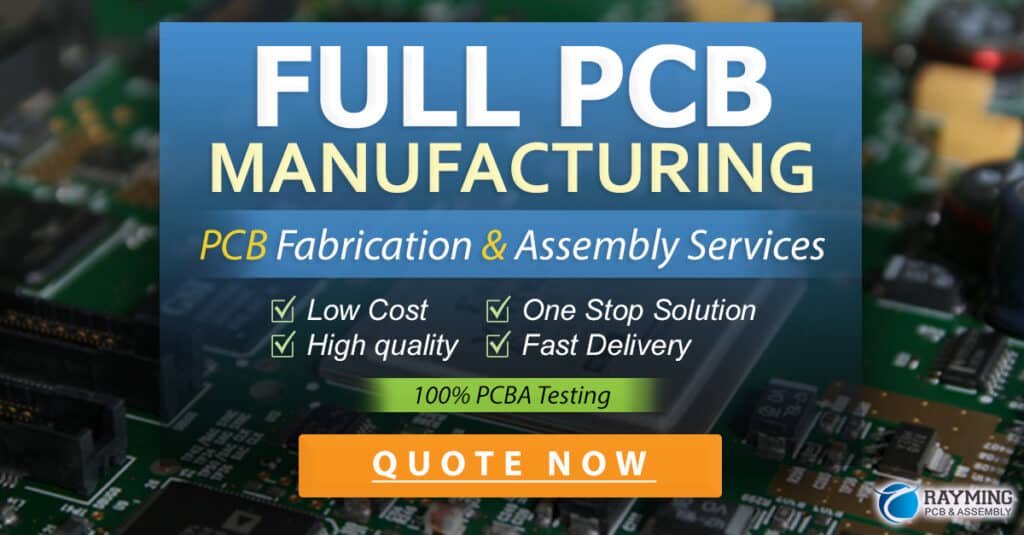
Best Practices for Ensuring DFM Compliance
To ensure that your PCB design is DFM compliant and can be efficiently manufactured, follow these best practices:
-
Adhere to Design Rules: Familiarize yourself with the manufacturer’s design rules and guidelines, and ensure that your design adheres to them. This includes minimum feature sizes, clearances, and drill sizes.
-
Use Standard Materials and Components: Whenever possible, use standard materials and components that are readily available and compatible with the manufacturing process. Custom materials and components can increase costs and lead times.
-
Optimize Component Placement: Place components in a way that minimizes the number of drill sizes and facilitates efficient assembly. Avoid placing components too close to the board edges or in hard-to-reach areas.
-
Minimize Layer Count: Use the minimum number of layers required to achieve the desired functionality. More layers increase complexity and cost.
-
Provide Comprehensive Documentation: Include clear and complete documentation with your Gerber files, such as a bill of materials (BOM), assembly drawings, and any special instructions. This helps avoid ambiguity and ensures that the manufacturer understands your requirements.
Frequently Asked Questions (FAQ)
1. What are the most common DFM issues encountered in PCB design?
Some of the most common DFM issues include:
– Insufficient clearances between traces, pads, and components
– Incorrect hole sizes and placement
– Incompatible materials and finishes
– Inadequate solder mask coverage
– Incorrect silkscreen legends
2. How can I ensure that my Gerber files are complete and accurate?
To ensure that your Gerber files are complete and accurate:
– Use a reputable PCB design software that generates industry-standard Gerber files
– Double-check that all necessary layers are included (copper, solder mask, silkscreen, drill data)
– Verify that the Gerber files match the original design intent
– Use a Gerber viewer to visually inspect the files for any errors or discrepancies
3. What is the difference between Gerber files and ODB++ files?
Gerber files are the traditional standard for PCB design data exchange, while ODB++ (Open Database++) is a more modern, intelligent format. ODB++ files contain additional information beyond the basic layout data, such as netlist, component data, and design rules. However, Gerber files remain the most widely supported format in the PCB industry.
4. Can I use the same Gerber files for different PCB manufacturers?
In most cases, yes. Gerber files are a universal standard and should be compatible with any PCB manufacturer that adheres to industry standards. However, it’s always a good idea to check with the specific manufacturer for their requirements and design rules.
5. How long does it typically take to convert Gerber files to PCB production data?
The time required to convert Gerber files to production data can vary depending on the complexity of the design and the manufacturer’s workload. In general, the process can take anywhere from a few hours to a few days. To minimize delays, ensure that your Gerber files are complete, accurate, and compliant with the manufacturer’s requirements.
Conclusion
DFM is a critical aspect of PCB manufacturing that ensures designs can be efficiently and reliably produced. By understanding the role of Gerber files and the process of converting them to production data, designers can create DFM-compliant PCBs that minimize costs, improve quality, and accelerate time-to-market. Adhering to best practices and working closely with your PCB manufacturer can help streamline the design-to-manufacturing process and ensure the success of your project.
Leave a Reply