Understanding PCB Proto Service Defaults
When ordering PCB Prototypes from a manufacturer, there are many default settings and values to be aware of. These PCBProtoDefaults cover aspects like the default PCB material, number of layers, minimum trace width and spacing, via sizes, soldermask color, silkscreen color, surface finish, and more.
Understanding these default values is important to ensure your PCB prototype meets your design requirements and can be manufactured cost-effectively and reliably. Let’s dive into the details of common PCBProtoDefaults.
Default PCB Materials
The most common default PCB material is FR-4. This is a glass-reinforced epoxy laminate material that provides good electrical insulation, mechanical strength, and thermal stability. FR-4 is the standard choice for most PCB Prototypes and volume production.
Some PCB manufacturers may offer other materials by default or upon request, such as:
- High Tg FR-4: FR-4 with a higher glass transition temperature for improved thermal performance
- Polyimide: A high-temperature material used in aerospace, military, and medical applications
- Rogers laminates: Low-loss materials for high-frequency RF/microwave applications
- Aluminum: Metal-core PCBs for high power LED lighting and other thermal management needs
Default Number of Layers
The default number of layers offered by PCB prototype services is typically 2 layers. This means a double-sided board with copper on the top and bottom layers. 2-layer boards are sufficient for many simpler designs.
However, 4-layer boards are also a common default option. The additional inner layers allow more routing flexibility and signal integrity for more complex designs. Most PCB fab houses support 4-layer prototypes with standard layer stackups.
For designs requiring more than 4 layers, 6-layer and 8-layer options are usually available by default as well. The price per board typically increases with more layers. Boards with 10+ layers may be supported but often require custom quoting.
Default Trace Width and Spacing
The minimum trace width and spacing supported by a PCB manufacturer determines how fine of pitch components and dense routing you can achieve. Most PCB prototype services offer the following default trace width and spacing options:
Trace Width | Trace Spacing |
---|---|
6 mil (0.15mm) | 6 mil (0.15mm) |
5 mil (0.13mm) | 5 mil (0.13mm) |
4 mil (0.10mm) | 4 mil (0.10mm) |
3 mil (0.08mm) | 3 mil (0.08mm) |
A trace width/spacing of 6/6 mil is the most common default as it provides a good tradeoff of density and manufacturability. 5/5 mil and 4/4 mil options allow denser routing for finer pitch BGAs and more compact designs. 3/3 mil enables maximum component density but is less commonly offered by default.
Tighter trace widths and spacings than these may be possible but usually require discussion with the manufacturer and entail a higher cost. It’s best to stick to the standard options offered unless absolutely necessary.
Default Via Sizes
Vias are used to route traces between layers of the PCB. The via sizes supported impact routing density as well. Most prototype PCB fabs offer these default via sizes:
Finished Hole Size | Pad Diameter |
---|---|
0.3mm | 0.6mm |
0.2mm | 0.5mm |
0.1mm | 0.4mm |
The 0.3mm/0.6mm via size is the most common default option. It provides a good balance of routability and reliability. 0.2mm/0.5mm vias allow denser routing but may be more prone to manufacturing issues. 0.1mm/0.4mm microvias enable HDI designs but usually come at a higher cost.
Default Soldermask Color
The soldermask is the polymer coating applied over the copper traces to protect them and prevent solder bridging. The default soldermask color offered by most PCB prototype services is green. This is the most cost-effective and widely used option.
Other soldermask color options that may be available by default include:
- Red
- Yellow
- Blue
- Black
- White
Some manufacturers also offer matte/glossy finish options for the soldermask. Choosing an alternate soldermask color besides green will usually entail a slight cost adder.
Default Silkscreen Color
The silkscreen is used to print text and graphics onto the PCB for component labels, logos, marks, etc. The default silkscreen color is usually white as it provides good contrast on most soldermask colors.
However, black silkscreen is another commonly offered default option. Some prototype services may support other silkscreen colors upon request as well.
Default Surface Finish
The surface finish is applied to the exposed copper pads/lands on the PCB to protect them from oxidation and enhance solderability. The most common default surface finish options are:
-
HASL (Hot Air Solder Leveling): Solder is applied to the pads and then leveled with hot air. Provides good solderability but limited flatness.
-
Lead-free HASL: A variant of HASL using lead-free solder alloys to comply with RoHS.
-
ENIG (Electroless Nickel Immersion Gold): A thin layer of gold over nickel is plated onto the copper. Enables fine pitch soldering, aluminum wire bonding, and a long shelf life. Higher cost than HASL.
-
OSP (Organic Solderability Preservatives): An organic film is applied to the copper to protect it. Low-cost but shorter shelf life compared to HASL and ENIG.
HASL (leaded or lead-free) is the most typical default surface finish as it provides good performance for most applications at a low cost. ENIG is the next most common default option for designs requiring a flatter surface, finer pitches, or gold fingers.
Frequently Asked Questions (FAQ)
1. What if my design requires specs tighter than the default options?
If your PCB design requires tighter specs than the standard defaults (e.g. trace width/spacing, via sizes, etc.), reach out to the manufacturer to discuss your needs. They can usually accommodate tighter specs but it may come at a higher cost and/or longer lead time.
2. Are the default PCB proto options suitable for production?
In most cases, yes. The default options offered by PCB prototype services are chosen based on their suitability for volume production as well. If you anticipate very high-volume production though, it’s worth discussing your specific needs with the manufacturer to optimize the design for manufacturability and cost.
3. What’s the typical lead time for PCB prototypes using the default options?
This varies by manufacturer, but in general you can expect a lead time of 2-5 days for standard 2-layer and 4-layer PCB prototypes using the default material, finish, soldermask/silkscreen colors, and specifications. More complex designs and higher layer counts may have slightly longer lead times.
4. Can I specify different surface finishes on different areas of the board?
Some PCB prototype fabs do support selective surface finishes, e.g. ENIG on certain pads and HASL on others. However, this is not a standard default option and will likely entail higher cost and longer lead times. Check with your manufacturer to see if they offer this service.
5. What file formats should I provide for PCB prototyping?
The most common file format for PCB fabrication is Gerber RS-274X. This is widely supported by PCB design tools and manufacturers. Many PCB prototype services also accept ODB++ files. Be sure to provide all the necessary Gerber files (e.g. GTL/GBL, GTO/GBO, GTP/GBP, GTS/GBS, Outline, Drill, etc.) and to follow the manufacturer’s DFM guidelines when exporting your design files.
Conclusion
Familiarizing yourself with the typical PCBProtoDefaults offered by manufacturers is an important step in bringing your designs to life quickly and cost-effectively. By understanding the standard options for PCB material, layers, trace/space, vias, soldermask, silkscreen, and finish, you can design your boards to be readily manufacturable as prototypes and for volume production.
Of course, every design is unique and the specific PCB prototype defaults offered vary by manufacturer. Always check with your chosen fab house to confirm their capabilities and default options. And don’t hesitate to discuss any special requirements with them – most manufacturers are happy to accommodate your needs.
With the right PCB prototype partner and a solid understanding of their default offerings, you’ll be well on your way to successfully prototyping and commercializing your electronic product. Design within standards where possible, but don’t be afraid to push the boundaries when your application demands it. The key is effective communication with your manufacturer and a collaborative approach to DFM.
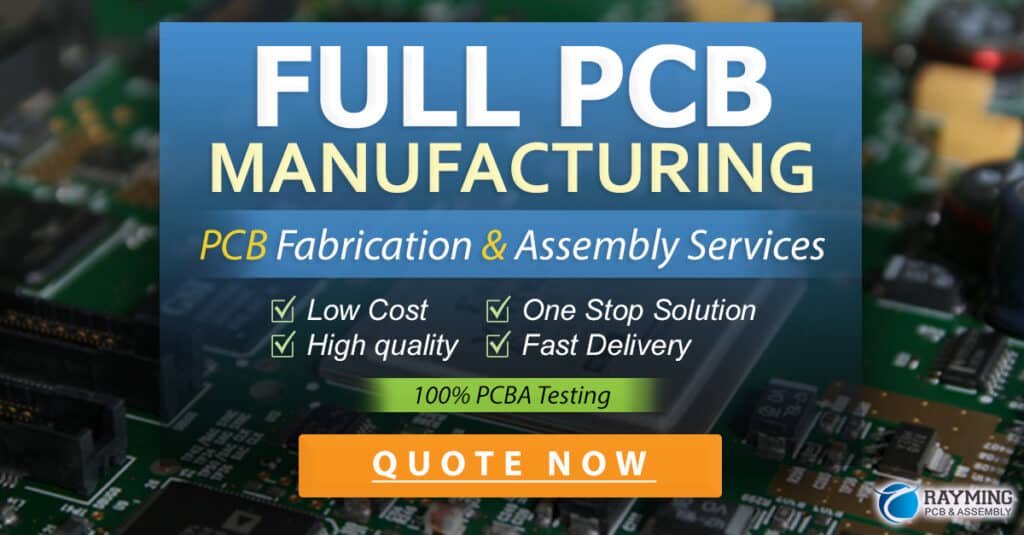
Leave a Reply