Importance of Solder paste testing
Solder paste is a mixture of tiny solder particles suspended in a flux medium. It is applied to the PCB pads using a stencil printing process before placing the surface mount components. The quality of the solder paste printing directly affects the following:
- Component placement accuracy
- Solder joint reliability
- Overall PCB Assembly yield
Proper solder paste testing helps identify and correct issues related to paste volume, consistency, and print quality, ultimately leading to improved manufacturing processes and end-product reliability.
Solder Paste Testing Methods
There are several methods for testing solder paste printing, each focusing on different aspects of the process. The most common testing methods include:
- Visual inspection
- Solder paste volume measurement
- Solder paste height and area measurement
- Solder paste spread test
- Solder paste slump test
- Solder paste tack time test
- Solder paste viscosity test
- Solder paste cold slump test
- Solder paste hot slump test
- Solder paste abandon time test
Let’s discuss each of these methods in detail.
1. Visual Inspection
Visual inspection is the most basic and quickest method for testing solder paste printing. It involves examining the printed PCB under magnification to check for any visible defects or inconsistencies. Some of the aspects to look for during visual inspection include:
- Print alignment and registration
- Paste coverage on pads
- Paste bridging between pads
- Paste smearing or slumping
- Foreign material or contamination
While visual inspection can help identify obvious defects, it is subjective and may not detect subtle issues that can affect the solder joint quality.
2. Solder Paste Volume Measurement
Solder paste volume measurement is a critical test that determines the amount of paste deposited on each PCB pad. Insufficient or excessive paste volume can lead to various defects, such as open circuits, shorts, or poor solder joint formation. There are two primary methods for measuring solder paste volume:
2.1 Solder Paste Inspection (SPI) Systems
SPI systems use 3D optical technology to scan the printed PCB and measure the volume of solder paste on each pad. These systems provide accurate and repeatable measurements, allowing for quick identification of any paste volume inconsistencies. SPI systems can also generate detailed reports and statistical data for process control and traceability.
Advantages of SPI Systems | Disadvantages of SPI Systems |
---|---|
High accuracy and repeatability | High initial cost |
Fast inspection speed | Requires skilled operators |
Detailed reporting and data analysis | May require regular calibration |
Suitable for high-volume production | Limited flexibility for different PCB designs |
2.2 Manual Solder Paste Volume Measurement
In the absence of an SPI system, manual methods can be used to measure solder paste volume. One common approach is to use a solder paste volume measurement stencil, which has cutouts that match the PCB pad sizes. The stencil is placed over the printed PCB, and the paste is scraped off into a measuring cup or onto a scale to determine its volume.
Manual measurement is less accurate and more time-consuming than using an SPI system but can still provide valuable insights into the solder paste printing process.
3. Solder Paste Height and Area Measurement
In addition to volume, the height and area of the printed solder paste are also important factors that affect the solder joint quality. Solder paste height and area measurements can be performed using the following methods:
3.1 3D Optical Profilers
3D optical profilers use non-contact, optical techniques to measure the height and area of the printed solder paste. These systems provide high-resolution, three-dimensional images of the paste deposits, allowing for detailed analysis of the paste profile and consistency.
Advantages of 3D Optical Profilers | Disadvantages of 3D Optical Profilers |
---|---|
Non-contact measurement | High equipment cost |
High resolution and accuracy | Requires skilled operators |
3D visualization of paste deposits | May require regular calibration |
Suitable for research and development | Limited throughput for high-volume production |
3.2 2D Optical Measurement Systems
2D optical measurement systems use image processing techniques to measure the area of the printed solder paste. These systems capture high-resolution images of the PCB and use software algorithms to calculate the paste area on each pad. While 2D systems do not provide height information, they can still detect issues such as insufficient paste coverage or bridging between pads.
Advantages of 2D Optical Measurement Systems | Disadvantages of 2D Optical Measurement Systems |
---|---|
Lower cost compared to 3D systems | No height information |
Faster inspection speed | Limited accuracy compared to 3D systems |
Suitable for high-volume production | May require regular calibration |
Easier to operate and maintain | Limited ability to detect subtle paste defects |
4. Solder Paste Spread Test
The solder paste spread test evaluates the ability of the paste to spread evenly on the PCB pads during the reflow process. A good solder paste should have a consistent spread pattern, ensuring proper wetting of the component leads and formation of reliable solder joints.
To perform the spread test, a small amount of solder paste is applied to a clean, flat surface (such as a glass slide) and heated to the reflow temperature. The spread pattern of the paste is then observed and measured. A uniform, circular spread pattern indicates good paste quality, while an irregular or inconsistent pattern may suggest issues with the paste formulation or printing process.
5. Solder Paste Slump Test
The solder paste slump test assesses the ability of the printed paste to maintain its shape and position on the PCB pads over time. Slumping occurs when the paste spreads or flows beyond the pad boundaries, potentially causing bridging or short circuits.
To conduct the slump test, a PCB is printed with solder paste and left at room temperature for a specified period (typically 1-2 hours). The printed PCB is then inspected for any signs of paste slumping or spreading. A good solder paste should maintain its original print pattern without significant slumping.
6. Solder Paste Tack Time Test
The solder paste tack time test measures the ability of the printed paste to hold components in place during the placement process. Tack time refers to the duration for which the paste remains sticky and able to secure the components before the reflow process begins.
To perform the tack time test, a small component (such as a chip resistor) is placed on a printed solder paste deposit. The PCB is then tilted to a specific angle (usually 45°), and the time taken for the component to slide off the paste is recorded. A longer tack time indicates better paste performance and reduces the risk of component misalignment during placement.
Tack Time (minutes) | Paste Performance |
---|---|
< 30 | Poor |
30 – 60 | Fair |
60 – 120 | Good |
> 120 | Excellent |
7. Solder Paste Viscosity Test
The solder paste viscosity test measures the flow properties of the paste, which can affect its printing and reflow behavior. Solder paste with the appropriate viscosity ensures good printability, component holding power, and solder joint formation.
Viscosity is typically measured using a rheometer, which applies a controlled shear force to the paste and measures its resistance to flow. The ideal viscosity range for solder paste depends on the specific application and printing process parameters.
Viscosity Range (Pa·s) | Paste Characteristics |
---|---|
< 100 | Low viscosity, may cause slumping and bridging |
100 – 200 | Suitable for fine-pitch printing |
200 – 300 | Suitable for standard SMT printing |
> 300 | High viscosity, may cause insufficient paste release from stencil |
8. Solder Paste Cold Slump Test
The cold slump test evaluates the ability of the printed solder paste to maintain its shape and position when exposed to low temperatures. This test is particularly relevant for PCBs that may be subjected to cold storage or transportation before the reflow process.
To perform the cold slump test, a printed PCB is placed in a refrigerated environment (typically 5-10°C) for a specified duration (usually 1-2 hours). The PCB is then inspected for any signs of paste slumping or spreading. A good solder paste should maintain its original print pattern without significant cold slumping.
9. Solder Paste Hot Slump Test
The hot slump test assesses the ability of the printed solder paste to maintain its shape and position when exposed to elevated temperatures before the reflow process. This test simulates the conditions encountered during the pre-heat stage of the reflow oven.
To conduct the hot slump test, a printed PCB is placed in a heated environment (typically 150-180°C) for a short duration (usually 30-60 seconds). The PCB is then inspected for any signs of paste slumping or spreading. A good solder paste should maintain its original print pattern without significant hot slumping.
10. Solder Paste Abandon Time Test
The solder paste abandon time test determines the maximum time the printed PCB can be left at room temperature before the paste loses its optimal properties. This test is important for establishing the acceptable time window for component placement and reflow after printing.
To perform the abandon time test, several PCBs are printed with solder paste and left at room temperature for different durations (e.g., 1, 2, 4, 8, and 24 hours). The PCBs are then subjected to reflow, and the resulting solder joints are inspected for quality and reliability. The maximum abandon time is determined based on the longest duration that still produces acceptable solder joint quality.
Abandon Time (hours) | Paste Performance |
---|---|
< 2 | Poor |
2 – 4 | Fair |
4 – 8 | Good |
> 8 | Excellent |
Implementing a Solder Paste Testing Program
To ensure consistent and reliable solder paste printing, it is essential to implement a comprehensive solder paste testing program. The following steps can help establish an effective testing protocol:
- Define the testing requirements based on the specific PCB assembly process and quality standards.
- Select the appropriate testing methods and equipment based on the available resources and production volume.
- Establish a regular testing schedule, including incoming paste inspection, process control checks, and periodic evaluations.
- Train the operators on the proper testing procedures and interpretation of results.
- Set up a data collection and analysis system to track the test results and identify trends or issues.
- Regularly review and update the testing program based on the process performance and continuous improvement initiatives.
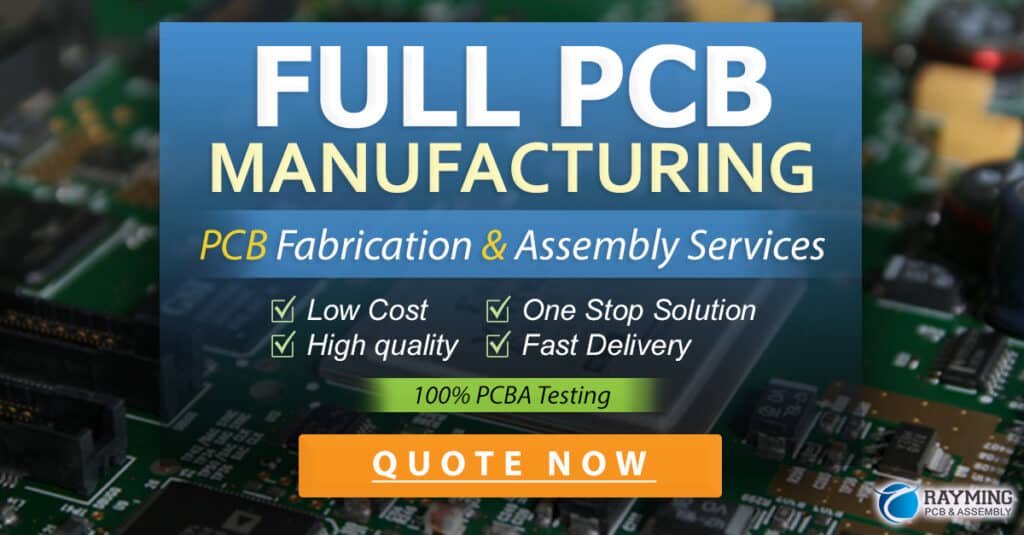
Frequently Asked Questions (FAQ)
1. What is the most critical solder paste testing method?
While all testing methods provide valuable insights, solder paste volume measurement is considered the most critical. Insufficient or excessive paste volume can directly impact the solder joint quality and reliability.
2. How often should solder paste testing be performed?
The frequency of solder paste testing depends on the production volume, paste stability, and process control requirements. Typically, incoming paste inspection should be performed on each new batch, while process control checks can be done hourly or per shift. Periodic evaluations, such as slump and tack time tests, can be conducted weekly or monthly.
3. Can solder paste testing be automated?
Yes, some solder paste testing methods, such as solder paste inspection (SPI) and 2D/3D optical measurement systems, can be automated for high-volume production. Automated testing provides faster, more consistent, and repeatable results compared to manual methods.
4. How do I interpret solder paste testing results?
Interpreting solder paste testing results requires an understanding of the acceptable ranges and limits for each testing parameter. The results should be compared against the established process specifications and quality standards. Any deviations or trends should be investigated and corrected to maintain optimal solder paste printing performance.
5. What are the consequences of insufficient solder paste testing?
Insufficient solder paste testing can lead to undetected printing issues, such as poor paste volume, inconsistent spread, or slumping. These issues can result in solder joint defects, component misalignment, or even complete assembly failures. Proper solder paste testing helps prevent these problems and ensures high-quality, reliable PCB assemblies.
Conclusion
Solder paste testing is a vital aspect of the SMT assembly process, ensuring consistent and reliable solder paste printing. By implementing a comprehensive testing program that includes various methods such as visual inspection, solder paste volume measurement, spread testing, and slump testing, manufacturers can identify and correct printing issues, ultimately improving the quality and yield of their PCB assemblies.
Regular solder paste testing, combined with proper process control and continuous improvement initiatives, can help optimize the solder paste printing process, reduce defects, and enhance the overall efficiency of the SMT assembly line. As the electronics industry continues to evolve, with smaller components and more complex PCB designs, effective solder paste testing will remain a critical factor in achieving manufacturing excellence.
Leave a Reply