Introduction to Copper Fills
Copper fills, also known as copper inlays or copper plugs, are a crucial component in the manufacturing of printed circuit boards (PCBs) and other electronic devices. These fills are used to enhance the mechanical, thermal, and electrical properties of the PCB, ensuring optimal performance and reliability. In this comprehensive article, we will delve into the world of copper fills, exploring their applications, advantages, and the various processes involved in their implementation.
What are Copper Fills?
Copper fills are essentially areas on a PCB where copper is added to fill in gaps or voids. These fills are typically used in multi-layer PCBs to create a solid, continuous copper plane that can provide a low-impedance ground or power connection. Copper fills also help to improve the mechanical strength of the PCB, reducing the risk of warping or cracking during the manufacturing process or in use.
Applications of Copper Fills
Copper fills find extensive use in a wide range of electronic applications, including:
- High-speed digital circuits
- RF and microwave devices
- Power electronics
- Automotive electronics
- Aerospace and defense systems
In these applications, copper fills play a vital role in ensuring signal integrity, minimizing electromagnetic interference (EMI), and dissipating heat efficiently.
Advantages of Copper Fills
Improved Mechanical Strength
One of the primary benefits of using copper fills in PCBs is the significant improvement in mechanical strength. By filling in the gaps between copper traces and components, copper fills create a more solid and robust structure. This added strength helps to prevent warping, twisting, or cracking of the PCB, especially during the manufacturing process when the board undergoes thermal stress.
The improved mechanical strength provided by copper fills is particularly important in applications where the PCB is subjected to vibration, shock, or other mechanical stresses. In automotive and aerospace electronics, for example, copper fills help to ensure the long-term reliability and durability of the PCB, even in harsh operating conditions.
Enhanced Thermal Management
Copper fills also play a crucial role in the thermal management of PCBs. As electronic components generate heat during operation, it is essential to dissipate this heat efficiently to prevent overheating and ensure optimal performance. Copper fills help to spread the heat evenly across the PCB, acting as a heat sink and facilitating better thermal dissipation.
By providing a continuous copper plane, fills allow heat to be conducted away from hot spots and distributed more evenly across the board. This helps to reduce the risk of thermal stress and improves the overall reliability of the electronic device.
Improved Electrical Performance
In addition to their mechanical and thermal benefits, copper fills also contribute to the improved electrical performance of PCBs. By providing a low-impedance ground or power plane, fills help to reduce signal noise, crosstalk, and EMI. This is particularly important in high-speed digital circuits and RF applications, where signal integrity is critical.
Copper fills also help to minimize the loop area between the signal trace and the ground plane, reducing the inductance and improving the signal quality. In power electronics, fills can help to distribute the current more evenly, reducing the risk of voltage drops and ensuring a stable power supply to the components.
Cost-effective Solution
Compared to other methods of improving the mechanical, thermal, and electrical properties of PCBs, such as using thicker copper traces or adding additional layers, copper fills offer a cost-effective solution. Fills can be easily incorporated into the PCB design using standard manufacturing processes, without significantly increasing the overall cost of production.
Moreover, by improving the reliability and durability of the PCB, copper fills can help to reduce the need for repairs or replacements, further contributing to cost savings over the lifetime of the electronic device.
Copper Fill Implementation
Design Considerations
When incorporating copper fills into a PCB design, several key factors must be considered to ensure optimal performance and manufacturability. These include:
-
Fill pattern: The fill pattern should be chosen based on the specific requirements of the application, such as thermal dissipation, mechanical strength, and electrical performance. Common fill patterns include solid fills, hatched fills, and crosshatched fills.
-
Fill density: The density of the fill pattern determines the amount of copper added to the PCB. Higher fill densities provide better mechanical strength and thermal dissipation but may increase the overall weight and cost of the board.
-
Clearance and spacing: Adequate clearance and spacing must be maintained between the fill areas and other components, traces, and vias to ensure proper insulation and avoid short circuits.
-
Thermal relief: In areas where components are soldered to the PCB, thermal relief patterns should be incorporated into the fill design to prevent heat from being drawn away from the solder joint during the soldering process.
Manufacturing Process
The process of implementing copper fills in PCBs typically involves the following steps:
-
PCB design: The fill areas are defined in the PCB design files, specifying the fill pattern, density, and clearance requirements.
-
Copper deposition: During the PCB manufacturing process, copper is deposited onto the board using techniques such as electroplating or electroless plating. The fills are plated along with the other copper features on the board.
-
Etching: After the copper deposition, the unwanted copper is etched away, leaving behind the desired fill pattern and other copper features.
-
Inspection: The PCB undergoes visual and automated optical inspection (AOI) to ensure that the fills have been correctly implemented and meet the required specifications.
Design Software and Tools
To incorporate copper fills into PCB designs, engineers and designers rely on specialized PCB design software and tools. These tools provide a range of features and capabilities specifically tailored for managing and optimizing fill patterns, such as:
-
Automated fill generation: Many PCB design tools offer automated fill generation features that can create fill patterns based on user-defined parameters, such as fill density, clearance, and thermal relief settings.
-
Fill pattern libraries: Some software packages include libraries of pre-defined fill patterns that can be easily incorporated into PCB designs, saving time and effort.
-
Design rule checking (DRC): DRC tools help to ensure that the fill patterns comply with the design requirements and manufacturing constraints, flagging any potential issues or violations.
-
Simulation and analysis: Advanced PCB design tools may include simulation and analysis capabilities that allow designers to evaluate the mechanical, thermal, and electrical performance of the fills before finalizing the design.
Fill Pattern | Advantages | Disadvantages |
---|---|---|
Solid Fill | Excellent mechanical strength and thermal dissipation | Increased weight and cost |
Hatched Fill | Good balance of strength, thermal dissipation, and weight | May require more complex design and manufacturing |
Crosshatch Fill | Provides good strength and thermal dissipation in both axes | Increased complexity in design and manufacturing |
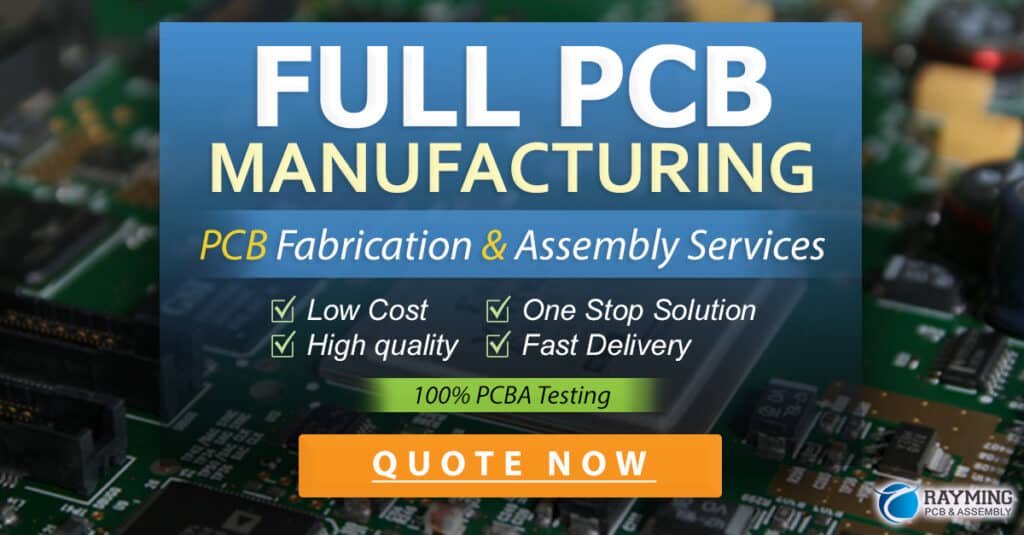
Frequently Asked Questions (FAQ)
1. What is the purpose of copper fills in PCBs?
Copper fills serve multiple purposes in PCBs, including improving mechanical strength, enhancing thermal dissipation, and providing a low-impedance ground or power plane for better electrical performance.
2. How do copper fills improve the mechanical strength of PCBs?
Copper fills create a more solid and robust structure by filling in the gaps between copper traces and components. This added strength helps to prevent warping, twisting, or cracking of the PCB during the manufacturing process and in use.
3. What are the common fill patterns used in PCB design?
Common fill patterns include solid fills, hatched fills, and crosshatched fills. The choice of fill pattern depends on the specific requirements of the application, such as mechanical strength, thermal dissipation, and electrical performance.
4. How do copper fills contribute to better thermal management in PCBs?
Copper fills help to spread heat evenly across the PCB, acting as a heat sink and facilitating better thermal dissipation. By providing a continuous copper plane, fills allow heat to be conducted away from hot spots and distributed more evenly across the board, reducing the risk of thermal stress.
5. Are copper fills a cost-effective solution for improving PCB performance?
Yes, compared to other methods such as using thicker copper traces or adding additional layers, copper fills offer a cost-effective solution for improving the mechanical, thermal, and electrical properties of PCBs. Fills can be easily incorporated into the PCB design using standard manufacturing processes, without significantly increasing the overall cost of production.
Conclusion
Copper fills are an essential component in the design and manufacturing of high-performance PCBs. By providing improved mechanical strength, enhanced thermal management, and better electrical performance, fills contribute to the overall reliability, durability, and efficiency of electronic devices.
As the demand for more advanced and compact electronic systems continues to grow, the importance of copper fills in PCB design will only increase. By understanding the advantages, design considerations, and manufacturing processes involved in copper fill implementation, engineers and designers can create PCBs that meet the ever-increasing performance requirements of modern electronic applications.
With the help of specialized PCB design software and tools, incorporating copper fills into PCB layouts has become more streamlined and efficient. As these tools continue to evolve and improve, we can expect to see even more innovative and optimized fill patterns and strategies in the future.
In conclusion, copper fills play a vital role in the world of PCB design and manufacturing, offering a cost-effective and reliable solution for improving the mechanical, thermal, and electrical properties of electronic devices. As the electronics industry continues to push the boundaries of performance and miniaturization, the importance of copper fills will only continue to grow, making them a crucial consideration for any PCB designer or manufacturer.
Leave a Reply