Introduction to PCB Assembly Services
PCB (Printed Circuit Board) assembly services are crucial for the manufacturing of electronic devices. These services involve the process of assembling various electronic components onto a printed circuit board to create a functional electronic product. PCB assembly services are essential for industries such as consumer electronics, automotive, aerospace, medical devices, and telecommunications.
What is PCB Assembly?
PCB assembly is the process of soldering or mounting electronic components onto a printed circuit board. The process involves several steps, including:
- Solder Paste Application: Applying solder paste onto the PCB pads where components will be placed.
- Component Placement: Placing the electronic components onto the PCB using pick-and-place machines or manual placement.
- Reflow Soldering: Heating the PCB and components to melt the solder paste and create a permanent connection.
- Inspection and Testing: Conducting visual and automated inspections to ensure proper assembly and functionality.
Types of PCB Assembly Services
There are three main types of PCB assembly services:
- Through-Hole Assembly (THA): Involves inserting component leads through holes drilled in the PCB and soldering them on the opposite side.
- Surface Mount Assembly (SMT): Involves placing components directly onto the surface of the PCB and soldering them using reflow or wave soldering techniques.
- Mixed Assembly: Combines both through-hole and surface mount assembly techniques for more complex PCB designs.
Defined Impedance in PCB Design
Defined impedance is a critical aspect of PCB design, particularly for high-speed and high-frequency applications. It refers to the characteristic impedance of a transmission line on a PCB, which is determined by factors such as the geometry of the trace, the dielectric constant of the substrate, and the frequency of the signal.
Why is Defined Impedance Important?
Defined impedance is essential for several reasons:
- Signal Integrity: Proper impedance matching ensures that signals travel through the PCB without reflections or distortions, maintaining signal integrity.
- Reduced EMI: Controlled impedance helps minimize electromagnetic interference (EMI) by reducing the amount of radiated energy from the PCB traces.
- Improved Timing: Matched impedance ensures that signals arrive at their destination at the correct time, critical for high-speed digital systems.
- Reliability: Proper impedance control helps prevent issues such as overshoot, undershoot, and ringing, which can damage components and reduce system reliability.
Factors Affecting Defined Impedance
Several factors influence the defined impedance of a PCB trace:
- Trace Geometry: The width, thickness, and spacing of the traces affect the characteristic impedance.
- Dielectric Constant: The dielectric constant of the PCB substrate material influences the impedance of the traces.
- Frequency: The frequency of the signal affects the impedance, with higher frequencies requiring tighter impedance control.
- Layer Stack-up: The arrangement of signal, ground, and power layers in the PCB stack-up impacts the impedance of the traces.
Calculating Defined Impedance
Calculating the defined impedance of a PCB trace involves using specialized software tools and formulas. The most common formula for calculating the characteristic impedance of a microstrip trace is:
Z₀ = 87 / √(ℇᵣ + 1.41) × ln(5.98 × h / (0.8 × w + t))
Where:
– Z₀ is the characteristic impedance in ohms
– ℇᵣ is the dielectric constant of the substrate material
– h is the height of the substrate in mils
– w is the width of the trace in mils
– t is the thickness of the trace in mils
For stripline traces, the formula is slightly different:
Z₀ = 60 / √ℇᵣ × ln(4 × h / (0.67 × π × (0.8 × w + t)))
It’s essential to work with experienced PCB design engineers and use appropriate software tools to ensure accurate impedance calculations and control.
PCB Material Selection for Defined Impedance
The choice of PCB material is crucial for achieving defined impedance in high-speed and high-frequency designs. The dielectric constant (Dk) and dissipation factor (Df) of the substrate material directly impact the impedance and signal integrity of the PCB.
Common PCB Materials for Defined Impedance
Some of the most common PCB materials used for defined impedance applications include:
- FR-4: A popular and cost-effective choice for many applications, with a Dk of around 4.2-4.5.
- Rogers RO4000 Series: High-performance materials with a low Dk (3.3-3.7) and low Df, suitable for high-frequency applications.
- Isola I-Tera MT: A low-loss material with a stable Dk (3.45-3.65) and low Df, designed for high-speed digital and RF applications.
- PTFE (Teflon): Offers excellent high-frequency performance with a low Dk (2.1-2.5) and very low Df, but is more expensive than other materials.
Material Properties and Defined Impedance
The dielectric constant (Dk) and dissipation factor (Df) of the PCB material directly affect the defined impedance of the traces:
- Dielectric Constant (Dk): A measure of the material’s ability to store electrical energy. A lower Dk results in a higher characteristic impedance for a given trace geometry.
- Dissipation Factor (Df): A measure of the material’s loss tangent or the amount of energy dissipated as heat. A lower Df is desirable for maintaining signal integrity and reducing losses.
When selecting a PCB material for defined impedance applications, it’s essential to consider the specific requirements of the design, such as the operating frequency, signal integrity, and cost constraints.
PCB Material Comparison Table
Material | Dielectric Constant (Dk) | Dissipation Factor (Df) | Typical Applications |
---|---|---|---|
FR-4 | 4.2-4.5 | 0.02-0.03 | General-purpose, low-cost |
Rogers RO4000 | 3.3-3.7 | 0.0027-0.0037 | High-frequency, low-loss |
Isola I-Tera MT | 3.45-3.65 | 0.0035-0.0045 | High-speed digital, RF |
PTFE (Teflon) | 2.1-2.5 | 0.0002-0.0008 | Ultra-high-frequency, low-loss, high-cost |
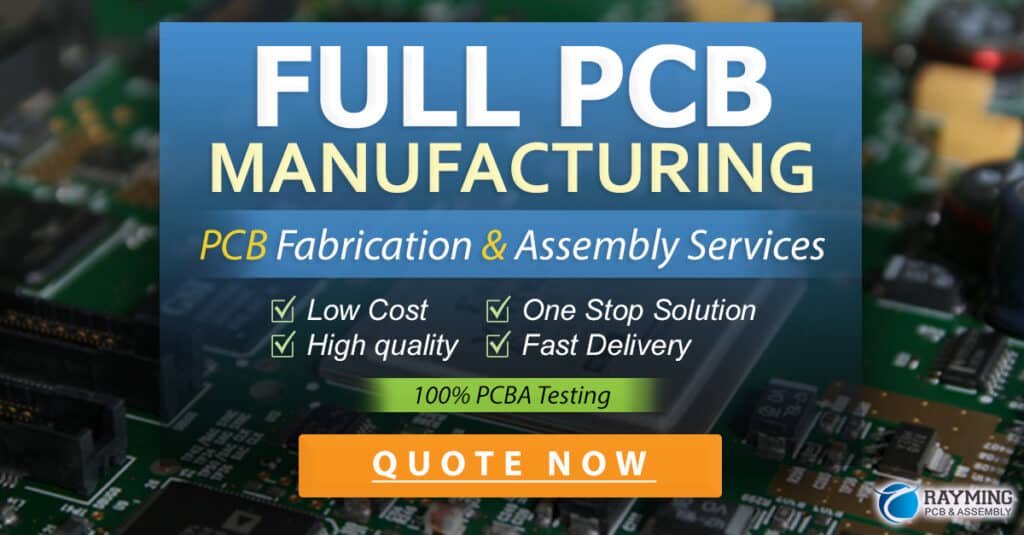
Defined Impedance Routing Techniques
Proper routing techniques are essential for maintaining defined impedance and ensuring signal integrity in PCB designs. Some of the key considerations and techniques for defined impedance routing include:
Trace Geometry
The width, thickness, and spacing of the traces directly affect the characteristic impedance. To maintain a consistent impedance along a trace, it’s crucial to keep the trace geometry uniform and avoid abrupt changes in width or direction.
- Trace Width: Determines the impedance of the trace. Wider traces have lower impedance, while narrower traces have higher impedance.
- Trace Thickness: Affects the current-carrying capacity and the skin effect at high frequencies. Thicker traces have lower impedance and better current-carrying capacity.
- Trace Spacing: Influences the coupling between adjacent traces. Adequate spacing helps minimize crosstalk and maintain signal integrity.
Reference Planes
Using uninterrupted reference planes (ground or power) beneath the signal traces is essential for maintaining defined impedance and controlling electromagnetic fields. Proper referencing helps to:
- Provide a low-impedance return path for the signal current
- Minimize electromagnetic interference (EMI) and reduce crosstalk
- Improve signal integrity by reducing inductance and providing shielding
Length Matching
For high-speed digital signals, it’s crucial to match the lengths of related traces (e.g., differential pairs or bus lines) to ensure that signals arrive at their destination at the same time. Length matching techniques include:
- Serpentine Routing: Adding gentle curves or serpentine patterns to shorter traces to match the length of longer traces.
- Delay Lines: Using controlled-impedance delay lines to add a specific amount of delay to shorter traces.
- Equidistant Routing: Placing related traces equidistant from each other and the reference plane to maintain consistent impedance and minimize skew.
Via Placement and Design
Vias are necessary for connecting traces between layers in a multi-layer PCB. However, vias can introduce discontinuities and affect the impedance of the traces. To minimize the impact of vias on defined impedance:
- Place vias close to the reference plane to minimize inductance
- Use smaller via diameters and higher aspect ratios to reduce capacitance
- Avoid placing vias in the middle of a trace, as this can cause impedance discontinuities
- Consider using blind or buried vias for high-speed signals to reduce the impact on impedance
By following these routing techniques and working with experienced PCB design engineers, you can ensure that your defined impedance design maintains signal integrity and meets the performance requirements of your application.
Defined Impedance PCB Manufacturing Process
Manufacturing PCBs with defined impedance requires specialized processes and strict quality control to ensure that the finished product meets the specified impedance requirements. The key steps in the defined impedance PCB manufacturing process include:
Impedance Modeling and Simulation
Before manufacturing, the PCB design undergoes impedance modeling and simulation to verify that the specified impedance can be achieved with the chosen material and stackup. This involves:
- Calculating the trace geometry (width, thickness, and spacing) for the target impedance
- Simulating the impedance of the traces using electromagnetic field solvers
- Optimizing the design to minimize impedance variations and ensure manufacturability
Material Selection and Stackup Design
The choice of PCB material and the arrangement of layers (stackup) are critical for achieving defined impedance. The manufacturing process must ensure that:
- The correct PCB material is used, with the specified dielectric constant (Dk) and dissipation factor (Df)
- The layer stackup is designed to provide the necessary reference planes and impedance control
- The copper weight and thickness are consistent with the impedance calculations
Controlled Etching and Plating
To maintain the specified trace geometry and impedance, the PCB manufacturing process must include controlled etching and plating steps:
- Use precise photolithography and etching techniques to create traces with the correct width and spacing
- Control the copper plating process to achieve the specified trace thickness and uniformity
- Monitor and adjust the etching and plating parameters to compensate for any variations in the material or process
Impedance Testing and Verification
After manufacturing, each PCB must undergo impedance testing to verify that it meets the specified requirements. This involves:
- Using a time-domain reflectometer (TDR) or network analyzer to measure the impedance of the traces
- Comparing the measured impedance to the specified tolerance (typically ±10%)
- Rejecting any PCBs that fail to meet the impedance requirements
Quality Control and Documentation
Throughout the manufacturing process, strict quality control measures must be in place to ensure consistency and reliability:
- Implement statistical process control (SPC) to monitor and adjust the manufacturing process
- Document all material and process parameters, including lot numbers, test results, and any deviations
- Provide a certificate of conformance (CoC) and impedance test report with each batch of PCBs
By following these manufacturing processes and working with experienced PCB fabrication partners, you can ensure that your defined impedance PCBs meet the specified requirements and provide the necessary signal integrity for your application.
Frequently Asked Questions (FAQ)
1. What is defined impedance in PCB design?
Defined impedance refers to the characteristic impedance of a transmission line on a PCB, which is determined by factors such as the geometry of the trace, the dielectric constant of the substrate, and the frequency of the signal. Maintaining a consistent and controlled impedance is essential for ensuring signal integrity and minimizing reflections and distortions in high-speed and high-frequency applications.
2. Why is impedance matching important in PCB design?
Impedance matching is crucial in PCB design for several reasons:
- Signal Integrity: Proper impedance matching ensures that signals travel through the PCB without reflections or distortions, maintaining signal integrity and reducing noise and crosstalk.
- Reduced EMI: Controlled impedance helps minimize electromagnetic interference (EMI) by reducing the amount of radiated energy from the PCB traces.
- Improved Timing: Matched impedance ensures that signals arrive at their destination at the correct time, critical for high-speed digital systems and avoiding timing errors.
- Reliability: Proper impedance control helps prevent issues such as overshoot, undershoot, and ringing, which can damage components and reduce system reliability.
3. How do you calculate the impedance of a PCB trace?
Calculating the impedance of a PCB trace involves using specialized software tools and formulas that take into account factors such as the trace geometry, dielectric constant of the substrate, and frequency of the signal. The most common formulas for calculating the characteristic impedance are:
- Microstrip: Z₀ = 87 / √(ℇᵣ + 1.41) × ln(5.98 × h / (0.8 × w + t))
- Stripline: Z₀ = 60 / √ℇᵣ × ln(4 × h / (0.67 × π × (0.8 × w + t)))
Where Z₀ is the characteristic impedance, ℇᵣ is the dielectric constant, h is the substrate height, w is the trace width, and t is the trace thickness (all dimensions in mils). It’s essential to work with experienced PCB design engineers and use appropriate software tools to ensure accurate impedance calculations and control.
4. What are some common PCB materials used for defined impedance applications?
Some of the most common PCB materials used for defined impedance applications include:
- FR-4: A popular and cost-effective choice for many applications, with a dielectric constant (Dk) of around 4.2-4.5.
- Rogers RO4000 Series: High-performance materials with a low Dk (3.3-3.7) and low dissipation factor (Df), suitable for high-frequency applications.
- Isola I-Tera MT: A low-loss material with a stable Dk (3.45-3.65) and low Df, designed for high-speed digital and RF applications.
- PTFE (Teflon): Offers excellent high-frequency performance with a low Dk (2.1-2.5) and very low Df, but is more expensive than other materials.
The choice of material depends on the specific requirements of the application, such as the operating frequency, signal integrity, and cost constraints.
5. How can you ensure that a manufactured PCB meets the specified impedance requirements?
To ensure that a manufactured PCB meets the specified impedance requirements, several steps are necessary:
-
Impedance Modeling and Simulation: Before manufacturing, the PCB design should undergo impedance modeling and simulation to verify that the specified impedance can be achieved with the chosen material and stackup.
-
Controlled Manufacturing Processes: The PCB manufacturing process must include controlled etching and plating steps to maintain the specified trace geometry and impedance, as well as strict quality control measures to ensure consistency and reliability.
-
Impedance Testing and Verification: After manufacturing, each PCB must undergo impedance testing using a time-domain reflectometer (TDR) or network analyzer to verify that it meets the specified requirements within the allowed tolerance (typically ±10%).
-
Documentation and Certification: The manufacturer should provide a certificate of conformance (CoC) and impedance test report with each batch of PCBs, documenting all material and process parameters, test results, and any deviations.
By working with experienced PCB fabrication partners and following these steps, you can ensure that your defined impedance PCBs meet the specified requirements and provide the necessary signal integrity for your application.
Conclusion
PCB assembly services play a vital role in the manufacturing of electronic devices across various industries. Defined impedance is a critical aspect of PCB design, particularly for high-speed and high-frequency applications, as it ensures signal integrity, reduces EMI, and improves system reliability.
Achieving defined impedance in PCB design involves careful material selection, trace geometry calculations, and proper routing techniques. The dielectric constant (Dk) and dissipation factor (Df) of the substrate material directly impact the impedance and signal integrity of the PCB, with common materials including FR-4, Rogers RO4000 series, Isola I-Tera MT, and PTFE (Teflon).
Proper routing techniques, such as maintaining consistent trace geometry, using uninterrupted reference planes, length matching, and optimizing via placement, are essential for maintaining defined impedance and ensuring signal integrity.
Manufacturing PCBs with defined impedance requires specialized processes and strict quality control, including impedance modeling and simulation, controlled etching and plating, impedance testing and verification, and comprehensive documentation.
By understanding the importance of defined impedance, selecting the appropriate PCB materials, employing proper routing techniques, and working with experienced PCB fabrication partners
Leave a Reply