What is Defined Impedance?
Defined impedance refers to the characteristic impedance of a transmission line used to carry electrical signals. In high-frequency circuit design, transmission lines must have a specific impedance, typically 50 ohms, to ensure proper signal transmission and minimize reflections or power loss. Defined impedance is critical for applications involving radio frequency (RF), microwave, and high-speed digital signals.
Impedance, measured in ohms (Ω), is the total opposition a circuit presents to the flow of alternating current at a given frequency. It consists of both resistance and reactance. In a transmission line, impedance depends on the physical properties of the conductors and the insulating material (dielectric) between them.
Why is Defined Impedance Important?
Maintaining a consistent defined impedance throughout a signal path is essential for several reasons:
-
Signal Integrity: Mismatched impedances cause reflections at the interface, leading to signal distortions, ringing, and degraded signal quality. By ensuring all components have the same defined impedance, reflections are minimized, and signal integrity is maintained.
-
Power Transfer: Maximum power transfer occurs when the source impedance matches the load impedance. If there is an impedance mismatch, some of the signal power is reflected back to the source, reducing the power delivered to the load.
-
Frequency Response: Impedance mismatches create standing waves on the transmission line, which can cause variations in the frequency response. Maintaining a constant defined impedance helps achieve a flat frequency response over a wide bandwidth.
-
Reduced EMI: Impedance discontinuities can cause electromagnetic radiation, leading to electromagnetic interference (EMI). By keeping the impedance consistent, EMI is minimized, ensuring the device meets regulatory requirements.
Factors Affecting Defined Impedance
Several factors influence the defined impedance of a transmission line:
-
Conductor Geometry: The width, thickness, and spacing of the conductors determine the impedance. In PCB design, the trace width and copper thickness are adjusted to achieve the desired impedance.
-
Dielectric Material: The insulating material between the conductors affects the impedance. The dielectric constant (Dk) and dissipation factor (Df) of the material influence the impedance and signal propagation speed.
-
Frequency: Impedance can vary with frequency due to the skin effect and dielectric losses. Higher frequencies cause the current to flow closer to the surface of the conductors, effectively reducing the cross-sectional area and increasing the resistance.
-
Surrounding Environment: The presence of other conductors, such as ground planes or adjacent traces, can impact the impedance through electromagnetic coupling.
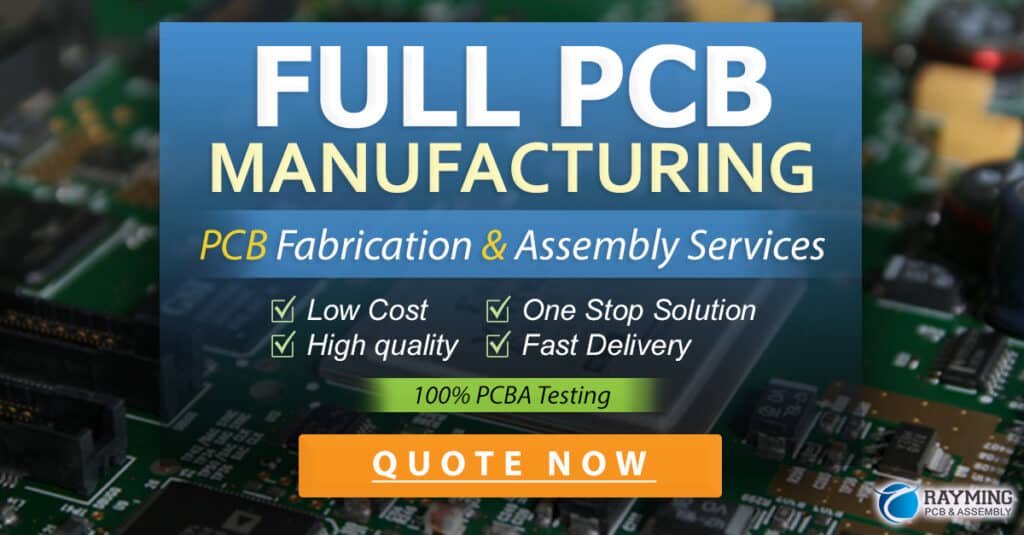
Common Defined Impedance Values
The most common defined impedance values used in RF, microwave, and high-speed digital applications are:
Impedance (Ω) | Application |
---|---|
50 | Coaxial cables, PCB traces, RF connectors |
75 | Video transmission, cable TV, some RF applications |
90-110 | Differential pairs in high-speed digital (USB, HDMI) |
100 | Twisted pair Ethernet (10Base-T, 100Base-TX) |
The choice of impedance depends on the specific application, standards, and design constraints. 50 ohms has become the de facto standard for most RF and microwave systems due to its good balance between power handling and low loss.
Achieving Defined Impedance in PCB Design
In printed circuit board (PCB) design, achieving defined impedance is critical for high-speed signals. The PCB stackup, trace geometry, and dielectric properties must be carefully designed to maintain the desired impedance. Here are some key considerations:
-
Stackup Design: The PCB stackup should be designed with controlled impedance in mind. This involves selecting the appropriate dielectric materials and thicknesses to achieve the target impedance.
-
Trace Geometry: The width and spacing of the traces must be calculated based on the desired impedance and the PCB stackup. Impedance Calculators or simulation tools are used to determine the optimal trace dimensions.
-
Dielectric Properties: The dielectric constant (Dk) and dissipation factor (Df) of the PCB materials must be accurately known and controlled. Variations in these properties can lead to impedance deviations.
-
Manufacturing Tolerance: PCB fabrication processes have tolerances that can affect the impedance. It’s essential to communicate the impedance requirements to the PCB manufacturer and specify the acceptable tolerance range.
-
Impedance Control: During PCB manufacturing, impedance control techniques, such as time-domain reflectometry (TDR) or impedance testing, are used to verify that the actual impedance matches the designed value.
Here’s an example of how trace geometry affects impedance for a microstrip transmission line:
Trace Width (mm) | Dielectric Thickness (mm) | Dielectric Constant (Dk) | Impedance (Ω) |
---|---|---|---|
0.2 | 0.2 | 4.0 | 86 |
0.3 | 0.2 | 4.0 | 68 |
0.4 | 0.2 | 4.0 | 57 |
0.5 | 0.2 | 4.0 | 50 |
As the trace width increases, the impedance decreases for a given dielectric thickness and constant. The PCB designer must carefully choose the trace geometry to achieve the desired impedance while considering manufacturing constraints and signal integrity requirements.
Measuring Defined Impedance
Verifying the defined impedance of a transmission line is crucial to ensure proper functionality. Several techniques are used to measure impedance:
-
Time-Domain Reflectometry (TDR): TDR measures impedance by sending a fast-rising pulse down the transmission line and analyzing the reflected waveform. The amplitude and timing of the reflections provide information about the impedance profile along the line.
-
Vector Network Analyzer (VNA): A VNA measures the scattering parameters (S-parameters) of a device under test (DUT) over a range of frequencies. The S-parameters can be used to calculate the impedance of the DUT.
-
Impedance Analyzer: An impedance analyzer directly measures the impedance of a component or transmission line by applying a test signal and measuring the voltage and current.
-
Simulation Tools: Electromagnetic simulation software can be used to model the transmission line and predict its impedance based on the physical properties and geometry.
Choosing the appropriate measurement technique depends on the application, frequency range, and required accuracy. TDR is commonly used for PCB impedance verification, while VNAs are preferred for RF and microwave components.
Matching Defined Impedance
When connecting components with different impedances, impedance matching techniques are used to minimize reflections and ensure maximum power transfer. Some common matching methods include:
-
Resistive Matching: Adding series or parallel resistors to match the impedance. This method is simple but introduces attenuation and power loss.
-
Reactive Matching: Using inductors and capacitors to create an impedance-matching network. This method is lossless but is frequency-dependent and can be narrow-band.
-
Transformer Matching: Using a transformer with the appropriate turns ratio to match impedances. This method provides wideband matching and DC isolation but can be bulky and expensive.
-
Stub Matching: Adding open or short-circuited transmission line stubs to match impedances. This method is compact and can be implemented on PCBs but is narrow-band.
The choice of matching technique depends on the frequency range, bandwidth, and allowable insertion loss. In some cases, a combination of methods may be used to achieve the desired impedance match.
Impedance Discontinuities and Their Effects
Impedance discontinuities occur when there is an abrupt change in the impedance along a transmission line. These discontinuities can arise from various sources, such as:
- Connectors and transitions
- Vias and layer changes in PCBs
- Bends and corners in transmission lines
- Variations in trace width or dielectric properties
Impedance discontinuities cause reflections, which can lead to several problems:
-
Signal Integrity Degradation: Reflections can cause ringing, overshoot, and undershoot on the signal, leading to increased jitter, reduced eye opening, and potential bit errors.
-
Power Loss: Reflected energy is not delivered to the load, resulting in reduced power transfer efficiency.
-
Resonances and Standing Waves: Impedance discontinuities can create standing waves on the transmission line, causing voltage and current peaks at specific locations. These resonances can lead to signal distortions and increased EMI.
-
Frequency-Dependent Effects: The impact of impedance discontinuities becomes more pronounced at higher frequencies, where the wavelength becomes comparable to the size of the discontinuity.
To minimize the effects of impedance discontinuities, designers must carefully consider the transmission line geometry, material properties, and transitions. Techniques such as impedance matching, gradual transitions, and avoiding sharp bends can help reduce reflections and maintain signal integrity.
FAQ
1. What is the difference between impedance and resistance?
Impedance is the total opposition to the flow of alternating current (AC) and includes both resistance and reactance. Resistance is the opposition to the flow of direct current (DC) and is frequency-independent. In other words, impedance is a complex quantity that varies with frequency, while resistance is a real quantity that is constant with frequency.
2. Why is 50 ohms the most common impedance value?
50 ohms has become the standard impedance value for RF and microwave systems because it offers a good compromise between power handling capability and low loss. Lower impedances allow for higher power handling but also result in higher losses, while higher impedances have lower losses but limited power handling. 50 ohms strike a balance between these two factors and has been widely adopted in the industry.
3. Can I use a different impedance value other than the common ones?
Yes, it is possible to use impedance values other than the common ones (50, 75, 90-110 ohms) depending on the specific application and design requirements. For example, some high-power RF applications may use lower impedances like 25 ohms, while some specialized high-speed digital interfaces may use higher impedances. However, using non-standard impedances may require custom components and increase design complexity.
4. How do I choose the right dielectric material for my PCB to achieve defined impedance?
The choice of dielectric material depends on several factors, including the desired impedance, frequency range, loss requirements, and cost. Materials with lower dielectric constants (Dk) generally result in wider traces for a given impedance, which can be advantageous for manufacturability. However, lower Dk materials may also have higher losses. It’s essential to consult with PCB material suppliers and manufacturers to select the appropriate material based on your specific application and requirements.
5. What is the impact of temperature on defined impedance?
Temperature can affect the defined impedance of a transmission line in several ways. First, the dielectric constant and dissipation factor of the insulating material can change with temperature, causing variations in the impedance. Second, the conductors’ dimensions may expand or contract due to thermal expansion, altering the impedance. In applications with significant temperature variations, it’s crucial to consider the temperature coefficient of the materials and design the transmission line to maintain the desired impedance over the expected temperature range.
Conclusion
Defined impedance is a critical concept in high-frequency circuit design, ensuring proper signal transmission, power transfer, and signal integrity. Maintaining a consistent impedance throughout a signal path is essential to minimize reflections, reduce power loss, and achieve a flat frequency response. Factors such as conductor geometry, dielectric properties, and frequency influence the defined impedance.
In PCB design, achieving defined impedance requires careful consideration of the stackup, trace geometry, and manufacturing tolerances. Simulation tools and impedance calculators are used to determine the optimal trace dimensions for a given impedance and dielectric material.
Measuring and verifying the defined impedance is crucial to ensure proper functionality. Techniques such as time-domain reflectometry (TDR), vector network analyzers (VNA), and impedance analyzers are used to characterize the impedance of transmission lines and components.
When connecting components with different impedances, impedance matching techniques are employed to minimize reflections and maximize power transfer. Resistive, reactive, transformer, and stub matching are common methods used in high-frequency circuits.
Impedance discontinuities, caused by abrupt changes in the transmission line geometry or material properties, can lead to signal integrity degradation, power loss, and resonances. Careful design and layout practices are necessary to minimize the impact of discontinuities.
Understanding and controlling defined impedance is vital for successful high-frequency circuit design. By considering the factors affecting impedance, employing appropriate design techniques, and verifying the impedance through measurements, designers can ensure optimal signal quality, power transfer, and system performance.
Leave a Reply