Understanding Component Tombstoning
Components tombstoning is a phenomenon that occurs in electronic circuits where components stand up or tilt at an angle after being subjected to harsh conditions such as high temperatures during Reflow Soldering. This issue can lead to various problems, including poor electrical connections, reduced mechanical strength, and even complete circuit failure.
In this article, we will explore the causes of component tombstoning, its impact on electronic assemblies, and effective strategies to minimize its occurrence. By understanding and addressing this issue, manufacturers can improve the reliability and quality of their electronic products.
What Causes Components to Tombstone?
Several factors can contribute to the tombstoning of components during the reflow soldering process. Some of the primary causes include:
-
Uneven heating: When one side of a component heats up faster than the other, it can cause the component to lift or stand up on one end. This is often due to uneven heat distribution across the PCB or variations in the thermal mass of the component’s terminals.
-
Improper pad design: If the pads on the PCB are not designed correctly, with inadequate size or improper spacing, it can lead to uneven surface tension forces acting on the component during reflow. This imbalance can cause the component to tombstone.
-
Incorrect component placement: Misaligned or off-center component placement can also contribute to tombstoning. If one end of the component is not properly aligned with its corresponding pad, it may lift during reflow.
-
Insufficient solder paste: When there is not enough solder paste applied to the pads, the surface tension forces may be insufficient to keep the component in place during reflow. This can result in tombstoning.
-
Inappropriate reflow profile: An incorrect reflow temperature profile, with excessive peak temperatures or prolonged exposure to high temperatures, can exacerbate the risk of component tombstoning.
Impact of Component Tombstoning
Component tombstoning can have several negative consequences for electronic assemblies:
-
Poor electrical connections: When a component tombstones, it may not make proper contact with the pads on the PCB. This can lead to intermittent or complete loss of electrical connection, compromising the functionality of the circuit.
-
Reduced mechanical strength: Tombstoned components are not securely attached to the PCB, making them more susceptible to mechanical stresses and vibrations. This can result in premature failure of the component or the entire assembly.
-
Increased manufacturing costs: Tombstoning often requires manual rework or repair, which can be time-consuming and costly. In some cases, the affected PCBs may need to be scrapped entirely, leading to material waste and production delays.
-
Reliability issues: Even if a tombstoned component is repaired, it may still have a higher risk of failure in the field due to the compromised connection quality. This can impact the overall reliability and lifespan of the electronic product.
Strategies to Minimize Component Tombstoning
To reduce the occurrence of component tombstoning, manufacturers can implement various strategies:
1. Optimize Pad Design
Proper pad design is crucial for minimizing tombstoning. Consider the following guidelines:
- Ensure that the pads are appropriately sized for the component’s terminations. Pads that are too small may not provide sufficient surface area for the solder to grip the component.
- Maintain symmetry in pad design. Asymmetrical pads can lead to uneven surface tension forces, increasing the risk of tombstoning.
- Adjust pad spacing based on the component’s size and pitch. Adequate spacing allows for proper solder joint formation and helps prevent bridging.
Component Package | Recommended Pad Width | Recommended Pad Length |
---|---|---|
0201 | 0.25 mm | 0.35 mm |
0402 | 0.5 mm | 0.6 mm |
0603 | 0.7 mm | 0.9 mm |
0805 | 1.0 mm | 1.2 mm |
1206 | 1.5 mm | 1.8 mm |
2. Improve Component Placement Accuracy
Accurate component placement is essential for preventing tombstoning. Implement the following measures:
- Use high-precision pick-and-place machines with vision systems to ensure accurate component alignment.
- Regularly calibrate and maintain placement equipment to minimize positioning errors.
- Employ machine vision inspection systems to verify component placement before reflow.
- Optimize nozzle design and suction force to minimize component shifting during placement.
3. Control Solder Paste Deposition
Adequate and consistent solder paste deposition is critical for preventing tombstoning. Consider the following practices:
- Use appropriate stencil thickness and aperture sizes to ensure sufficient solder paste volume on the pads.
- Maintain proper stencil alignment and cleanliness to avoid inconsistent paste deposition.
- Implement solder paste inspection (SPI) systems to monitor paste volume and distribution.
- Optimize print parameters, such as squeegee pressure and speed, to achieve uniform paste deposition.
4. Optimize Reflow Profile
A well-designed reflow profile can help minimize tombstoning by ensuring even heating and proper solder joint formation. Consider the following guidelines:
- Follow the recommended reflow profile provided by the solder paste manufacturer.
- Ensure gradual and controlled ramp-up rates to avoid thermal shock to the components.
- Maintain appropriate peak temperatures and soaking times to allow for complete solder melting and wetting.
- Implement cooling zones with controlled ramp-down rates to minimize thermal stress on the components.
5. Select Appropriate Components
Choosing components with features that minimize tombstoning can also be beneficial. Consider the following:
- Opt for components with symmetrical terminations to promote even heating and solder joint formation.
- Use components with larger terminations or increased pitch to provide more surface area for solder attachment.
- Consider using components with terminations designed to reduce tombstoning, such as anchored or flat leads.
Frequently Asked Questions (FAQ)
1. What is component tombstoning?
Component tombstoning is a defect that occurs during reflow soldering, where a component stands up or tilts at an angle instead of lying flat on the PCB pads. It can lead to poor electrical connections and reduced reliability of the electronic assembly.
2. What are the main causes of component tombstoning?
The main causes of component tombstoning include uneven heating, improper pad design, incorrect component placement, insufficient solder paste, and inappropriate reflow profiles. These factors can lead to uneven surface tension forces acting on the component, causing it to lift or stand up during reflow.
3. How does component tombstoning affect electronic assemblies?
Tombstoned components can result in poor electrical connections, reduced mechanical strength, increased manufacturing costs due to rework or scrap, and reliability issues in the field. These problems can compromise the functionality and lifespan of the electronic product.
4. What can be done to minimize component tombstoning?
To minimize component tombstoning, manufacturers can optimize pad design, improve component placement accuracy, control solder paste deposition, optimize reflow profiles, and select appropriate components with features that reduce the risk of tombstoning. Implementing these strategies can help ensure proper solder joint formation and component stability during reflow.
5. How can solder paste deposition affect component tombstoning?
Insufficient or inconsistent solder paste deposition can contribute to component tombstoning. If there is not enough solder paste on the pads, the surface tension forces may be inadequate to keep the component in place during reflow. Ensuring appropriate stencil thickness, aperture sizes, and print parameters can help achieve uniform and sufficient solder paste deposition, reducing the risk of tombstoning.
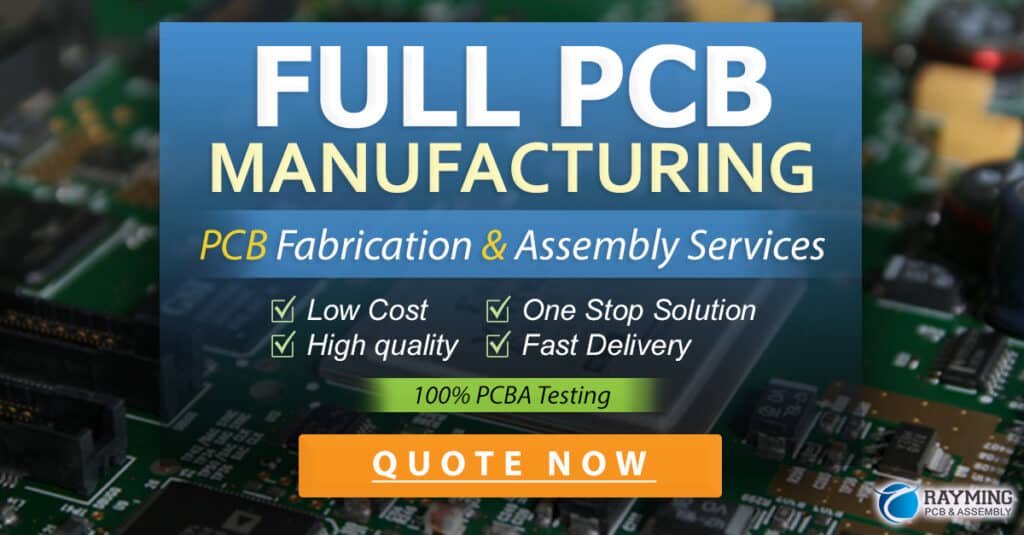
Conclusion
Component tombstoning is a significant challenge in electronic manufacturing that can impact the quality, reliability, and cost of electronic assemblies. By understanding the causes and consequences of tombstoning, manufacturers can implement effective strategies to minimize its occurrence.
Optimizing pad design, improving component placement accuracy, controlling solder paste deposition, optimizing reflow profiles, and selecting appropriate components are key steps in reducing tombstoning. By adopting these best practices, manufacturers can enhance the reliability and performance of their electronic products while minimizing production costs and delays associated with rework and scrap.
As electronic devices continue to become more complex and miniaturized, addressing component tombstoning will remain a critical aspect of ensuring high-quality and robust electronic assemblies.
Leave a Reply