Introduction to PCBs and their colors
Printed Circuit Boards (PCBs) are the backbone of modern electronics. They are used in almost every electronic device, from smartphones and laptops to industrial machinery and medical equipment. PCBs come in various shapes, sizes, and colors, but one color that stands out is red. In this article, we will explore the reasons behind the use of red PCBs and their advantages.
What are PCBs?
PCBs are flat boards made of insulating materials, such as fiberglass or plastic, with conductive pathways etched onto them. These pathways, also known as traces, connect various electronic components, such as resistors, capacitors, and integrated circuits, to form a complete circuit. PCBs eliminate the need for messy wiring and provide a compact, reliable, and efficient way to assemble electronic devices.
Common PCB colors and their significance
PCBs come in a variety of colors, each serving a specific purpose or indicating a particular characteristic. Some of the most common PCB colors include:
- Green: The most widely used color for PCBs, green is the default choice for many manufacturers due to its good contrast with copper traces and its ability to hide dirt and scratches.
- Blue: Often used for high-quality or military-grade PCBs, blue boards are known for their durability and resistance to moisture and heat.
- Black: Black PCBs are popular in high-end consumer electronics, such as smartphones and gaming consoles, for their sleek and modern appearance.
- White: White PCBs are commonly used in LED lighting applications, as they reflect light better than other colors, enhancing the overall brightness and efficiency of the device.
- Red: Red PCBs are less common than other colors but have gained popularity in recent years for various reasons, which we will discuss in detail throughout this article.
The science behind red PCBs
The manufacturing process of red PCBs
Red PCBs are manufactured using the same basic process as other colored PCBs, with a few additional steps. The process involves the following stages:
- Substrate preparation: The base material, usually fiberglass or plastic, is cut to the desired size and shape.
- Copper lamination: A thin layer of copper is bonded to the substrate using heat and pressure.
- Photoresist application: A light-sensitive material called photoresist is applied to the copper layer.
- Exposure and development: The photoresist is exposed to UV light through a patterned mask, hardening the exposed areas. The unexposed areas are then removed using a developer solution, leaving the desired circuit pattern.
- Etching: The exposed copper is removed using an etchant solution, leaving only the circuit traces protected by the hardened photoresist.
- Photoresist removal: The remaining photoresist is stripped away, revealing the copper traces.
- Solder mask application: A protective layer, called solder mask, is applied to the board, covering the copper traces but leaving the connection points exposed. This is where the red color comes into play, as the solder mask can be pigmented with red dye.
- Silkscreen printing: White text and symbols are printed onto the board for component identification and orientation.
- Surface finish: A final protective layer, such as HASL (Hot Air Solder Leveling) or ENIG (Electroless Nickel Immersion Gold), is applied to the exposed copper to prevent oxidation and enhance solderability.
The role of solder mask in determining PCB color
The solder mask is the key factor in determining the color of a PCB. Solder mask is a thin, protective layer applied to the copper traces on a PCB to prevent short circuits, protect against oxidation, and provide electrical insulation. It also helps to improve the aesthetics of the board by hiding the complex network of copper traces beneath a smooth, uniform surface.
Solder mask is typically applied using a silkscreen printing process, where a fine mesh screen is used to transfer the solder mask material onto the board. The solder mask is then cured using UV light or heat, depending on the type of material used.
To create a red PCB, red pigments are added to the solder mask material before it is applied to the board. The pigments used are usually organic or inorganic compounds that are stable at high temperatures and resistant to UV light, ensuring that the color remains vibrant and durable over the lifespan of the PCB.
Advantages of red solder mask
Red solder mask offers several advantages over other colors, making it an attractive choice for certain applications:
- High visibility: Red is a highly visible color that stands out against most backgrounds, making it easier to spot on a crowded workbench or production line. This can help to reduce errors and improve efficiency during assembly and inspection processes.
- Enhanced contrast: Red provides excellent contrast against the white silkscreen markings and the silver or gold-plated components on a PCB, making it easier to read text and identify components.
- Improved aesthetics: Red PCBs can give a product a unique, eye-catching appearance, which can be particularly appealing in consumer electronics or custom designs.
- Reduced eye strain: Some studies suggest that red is a more comfortable color for the human eye to focus on for extended periods compared to other colors, potentially reducing eye strain and fatigue for technicians and assembly workers.
Applications of red PCBs
Consumer electronics
Red PCBs have found their way into various consumer electronics, particularly in the gaming and enthusiast PC market. Some examples include:
- Gaming motherboards: Many high-end gaming motherboards feature red PCBs, often paired with black or red components and LED lighting to create a visually striking and cohesive aesthetic.
- Graphics cards: Some graphics card manufacturers, such as AMD and NVIDIA, have released special edition cards with red PCBs to appeal to enthusiast gamers and PC builders.
- Custom mechanical keyboards: Red PCBs are popular among mechanical keyboard enthusiasts for their unique appearance and the ability to complement other red components, such as keycaps and switches.
Industrial and automotive applications
Red PCBs are also used in industrial and automotive applications, where their high visibility and contrast can be particularly beneficial:
- Automotive electronics: Red PCBs are sometimes used in automotive electronics, such as dashboard displays and vehicle control modules, for their enhanced visibility and readability.
- Industrial control systems: In industrial settings, red PCBs can make it easier for technicians to identify and troubleshoot components on a control board, reducing downtime and improving maintenance efficiency.
- Aerospace and defense: Red PCBs may be used in aerospace and defense applications, where high visibility and readability are crucial for safety and reliability.
Prototyping and testing
Red PCBs can be useful during the prototyping and testing phases of product development:
- Rapid prototyping: Red PCBs can help developers quickly identify and track different versions of a prototype, making it easier to organize and iterate on designs.
- Testing and debugging: The high visibility and contrast of red PCBs can make it easier for engineers to probe test points and identify components during debugging sessions, saving time and reducing the risk of errors.
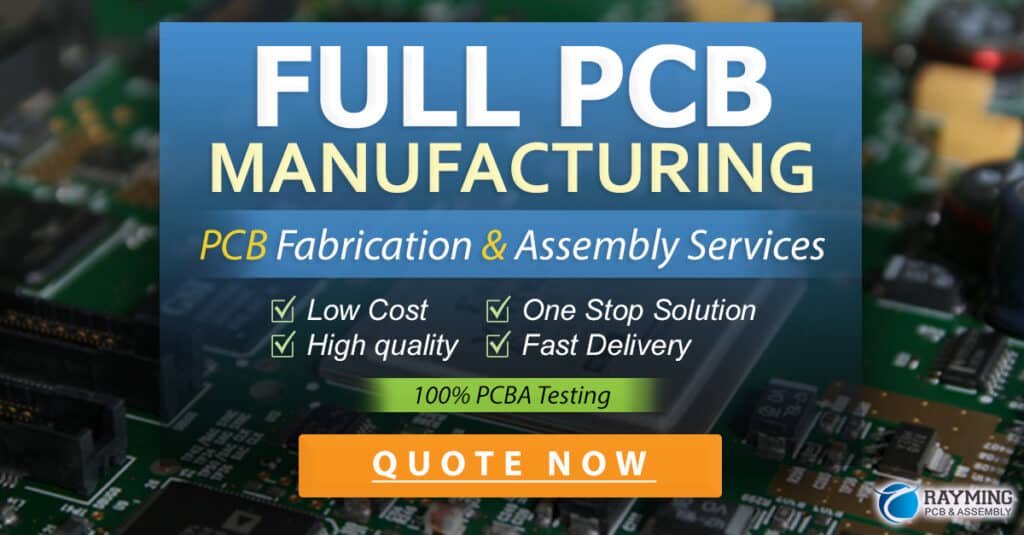
Myths and misconceptions about red PCBs
Despite their advantages, red PCBs have been the subject of some myths and misconceptions. Let’s address a few of the most common ones:
Myth 1: Red PCBs are more expensive than other colors
While red PCBs may have a slightly higher cost than standard green PCBs due to the additional pigments used in the solder mask, the difference in price is generally negligible, especially for larger production runs. The benefits of using red PCBs, such as improved visibility and aesthetics, often outweigh the minimal extra cost.
Myth 2: Red PCBs are less reliable than other colors
There is no evidence to suggest that red PCBs are inherently less reliable than other colors. The reliability of a PCB depends on factors such as the quality of the materials used, the manufacturing process, and the design of the circuit itself. The color of the solder mask has no bearing on the performance or longevity of a PCB.
Myth 3: Red PCBs are harder to manufacture than other colors
The manufacturing process for red PCBs is essentially the same as for other colored PCBs, with the only difference being the addition of red pigments to the solder mask. This does not make the manufacturing process significantly more difficult or time-consuming. In fact, many PCB manufacturers offer red as a standard color option alongside green, blue, and black.
Frequently Asked Questions (FAQ)
-
Q: Are red PCBs more expensive than other colors?
A: While red PCBs may have a slightly higher cost due to the additional pigments used in the solder mask, the difference in price is generally negligible, especially for larger production runs. -
Q: Do red PCBs offer any performance advantages over other colors?
A: The color of a PCB does not directly affect its performance. However, red PCBs offer benefits such as high visibility, enhanced contrast, and improved aesthetics, which can indirectly lead to better efficiency and reduced errors during assembly and inspection processes. -
Q: Can red PCBs be used in any application?
A: Yes, red PCBs can be used in virtually any application where a standard PCB would be used. They are particularly popular in consumer electronics, gaming products, and industrial control systems. -
Q: Are there any disadvantages to using red PCBs?
A: There are no significant disadvantages to using red PCBs. They offer the same performance and reliability as other colored PCBs, with the added benefits of high visibility and enhanced aesthetics. -
Q: Can I order custom red PCBs for my project?
A: Yes, most PCB manufacturers offer red as a standard color option for custom PCB orders. You can specify the desired color when placing your order, and the manufacturer will produce the PCBs according to your specifications.
Conclusion
Red PCBs have gained popularity in recent years due to their high visibility, enhanced contrast, and improved aesthetics. While they may have a slightly higher cost than standard green PCBs, the benefits they offer often outweigh the minimal extra expense. Red PCBs are used in a wide range of applications, from consumer electronics and gaming products to industrial control systems and automotive electronics.
Despite some myths and misconceptions surrounding red PCBs, there is no evidence to suggest that they are less reliable, more expensive, or harder to manufacture than other colored PCBs. In fact, red PCBs can offer several advantages, such as reduced eye strain for assembly workers and improved efficiency during inspection processes.
As the demand for unique and visually appealing electronic products continues to grow, it is likely that we will see more widespread adoption of red PCBs across various industries. Whether you are a hobbyist working on a custom project or a professional designer developing a new product, consider the benefits of using red PCBs to enhance the visibility, aesthetics, and overall appeal of your design.
Leave a Reply