Introduction to PCB Oven Placement
Proper placement of printed circuit boards (PCBs) in a reflow oven is critical for achieving high-quality solder joints and reliable electronic assemblies. The location of the PCB within the oven chamber directly impacts the uniformity of heat distribution, which in turn affects the reflow soldering process. This article explores the factors to consider when determining the optimal PCB oven placement and provides guidelines for achieving the best results.
Factors Affecting PCB Oven Placement
Several key factors influence the decision of where to place a PCB in a reflow oven:
1. Oven Type and Configuration
The type and configuration of the reflow oven play a significant role in determining the ideal PCB placement. Ovens can be categorized based on their heating method, such as convection, infrared (IR), or vapor phase. Each type has its unique characteristics that affect heat distribution and PCB positioning.
Convection Ovens
In convection ovens, hot air circulates within the chamber to heat the PCBs. The placement of the PCBs should consider the airflow patterns to ensure even heat distribution. Generally, PCBs should be placed perpendicular to the airflow direction to maximize exposure to the circulating hot air.
Infrared (IR) Ovens
IR ovens use infrared emitters to heat the PCBs directly. The placement of the PCBs should consider the location and intensity of the IR emitters. PCBs should be positioned at a sufficient distance from the emitters to avoid overheating and ensure uniform heat distribution across the board.
Vapor Phase Ovens
Vapor phase ovens use a heated vapor to transfer heat to the PCBs. The placement of the PCBs is less critical in vapor phase ovens as the vapor provides a more uniform heating environment. However, proper spacing between PCBs is still important to allow adequate vapor circulation.
2. PCB Size and Complexity
The size and complexity of the PCB also influence its placement within the oven. Larger PCBs may require more space and attention to ensure even heat distribution across the entire board. Complex PCBs with varying component densities and heights may need specific placement considerations to achieve optimal reflow results.
Small PCBs
Small PCBs, typically those smaller than 100mm x 100mm, can be placed relatively close together in the oven. However, it is important to maintain sufficient spacing between boards to allow for proper heat circulation and to avoid shadowing effects.
Large PCBs
Large PCBs, exceeding 200mm x 200mm, require more careful placement to ensure uniform heating. These boards should be placed with ample space around them to promote even heat distribution. If multiple large PCBs are being processed simultaneously, they should be arranged in a staggered pattern to minimize shadowing and optimize airflow.
Complex PCBs
PCBs with complex layouts, varying component densities, and different component heights demand special attention during oven placement. The placement should consider the location of tall components, such as connectors or heatsinks, to prevent shadowing and ensure adequate heat exposure for smaller components.
3. Component Characteristics
The types and characteristics of the components on the PCB also influence the optimal oven placement. Some components are more sensitive to heat than others and may require specific placement considerations.
Temperature-Sensitive Components
Certain components, such as electrolytic capacitors, batteries, and some connectors, are sensitive to high temperatures. These components should be placed in cooler areas of the oven, typically near the edges or corners, to minimize their exposure to peak temperatures.
Moisture-Sensitive Components
Components that are prone to moisture absorption, such as certain IC packages and connectors, require careful placement to prevent moisture-induced damage during reflow. These components should be placed in areas with good airflow and away from regions prone to condensation.
Thermally Conductive Components
Components with high thermal conductivity, such as metal shields and heatsinks, can affect the temperature distribution on the PCB. These components should be placed strategically to avoid creating hot spots or cold spots on the board.
4. Oven Temperature Profile
The temperature profile used in the reflow oven also plays a role in determining the optimal PCB placement. Different temperature profiles may have varying ramp rates, peak temperatures, and dwell times, which can impact the heat distribution across the PCB.
Ramp Rate
The ramp rate, or the speed at which the oven temperature increases, can affect the placement of the PCB. Slower ramp rates allow for more even heat distribution, while faster ramp rates may require placing the PCB in areas with more direct exposure to the heat source.
Peak Temperature
The peak temperature of the reflow profile should be considered when placing the PCB. If the peak temperature is too high, temperature-sensitive components may need to be placed further away from the heat source. Conversely, if the peak temperature is too low, the PCB may need to be placed closer to the heat source to ensure proper reflow.
Dwell Time
The dwell time, or the duration at which the PCB is exposed to the peak temperature, also influences placement. Longer dwell times may require placing the PCB in areas with more consistent heat exposure, while shorter dwell times may allow for more flexibility in placement.
Guidelines for Optimal PCB Oven Placement
Based on the factors discussed above, here are some general guidelines for achieving optimal PCB oven placement:
-
Place PCBs perpendicular to the airflow direction in convection ovens to maximize exposure to the circulating hot air and promote even heat distribution.
-
Position PCBs at a sufficient distance from IR emitters in infrared ovens to avoid overheating and ensure uniform heat distribution across the board.
-
Maintain proper spacing between PCBs to allow for adequate heat circulation and to avoid shadowing effects, especially in convection and vapor phase ovens.
-
Arrange large PCBs in a staggered pattern to minimize shadowing and optimize airflow when processing multiple boards simultaneously.
-
Consider the location of tall components to prevent shadowing and ensure adequate heat exposure for smaller components.
-
Place temperature-sensitive components in cooler areas of the oven, typically near the edges or corners, to minimize their exposure to peak temperatures.
-
Position moisture-sensitive components in areas with good airflow and away from regions prone to condensation to prevent moisture-induced damage.
-
Place thermally conductive components strategically to avoid creating hot spots or cold spots on the board.
-
Adjust PCB placement based on the oven temperature profile, considering factors such as ramp rate, peak temperature, and dwell time.
-
Conduct test runs and monitor the reflow process to fine-tune the PCB placement and ensure optimal results.
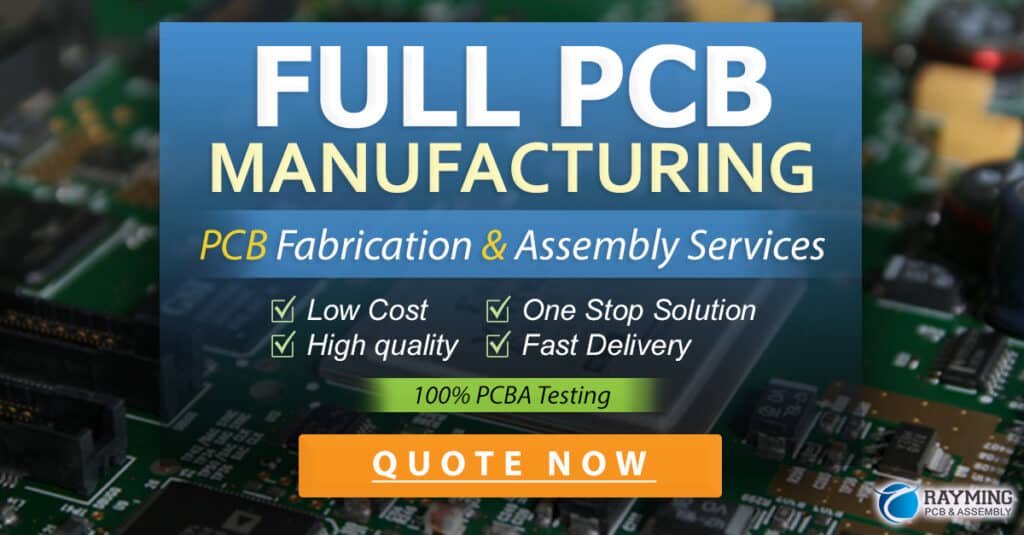
PCB Oven Placement Examples
To illustrate the application of these guidelines, let’s consider a few examples of PCB oven placement based on different scenarios.
Example 1: Small PCB in a Convection Oven
Scenario:
– PCB size: 50mm x 50mm
– Oven type: Convection
– Temperature profile: Standard (ramp to peak, hold, cool down)
Placement:
– Place the PCB perpendicular to the airflow direction
– Maintain a spacing of at least 20mm between adjacent PCBs
– Position the PCB near the center of the oven chamber for even heat exposure
Parameter | Value |
---|---|
PCB Size | 50mm x 50mm |
Oven Type | Convection |
Spacing | 20mm |
Position | Center of the oven chamber |
Example 2: Large PCB with Tall Components in an IR Oven
Scenario:
– PCB size: 250mm x 200mm
– Oven type: Infrared (IR)
– Temperature profile: Modified (slower ramp, longer dwell)
– Tall components: Connectors and heatsinks
Placement:
– Position the PCB at a distance of 150mm from the IR emitters
– Arrange tall components towards the edges of the PCB to minimize shadowing
– If processing multiple large PCBs, use a staggered pattern with a spacing of at least 50mm between boards
Parameter | Value |
---|---|
PCB Size | 250mm x 200mm |
Oven Type | Infrared (IR) |
Distance from IR Emitters | 150mm |
Tall Component Placement | Towards the edges of the PCB |
Staggered Spacing | 50mm |
Example 3: Complex PCB with Temperature-Sensitive Components in a Vapor Phase Oven
Scenario:
– PCB size: 180mm x 150mm
– Oven type: Vapor Phase
– Temperature profile: Standard (ramp to peak, hold, cool down)
– Temperature-sensitive components: Electrolytic capacitors and batteries
Placement:
– Place temperature-sensitive components near the corners of the PCB
– Maintain a spacing of at least 30mm between adjacent PCBs to allow for vapor circulation
– Position the PCB in the center of the oven chamber for uniform vapor exposure
Parameter | Value |
---|---|
PCB Size | 180mm x 150mm |
Oven Type | Vapor Phase |
Temperature-Sensitive Component Placement | Near the corners of the PCB |
Spacing | 30mm |
Position | Center of the oven chamber |
Frequently Asked Questions (FAQ)
1. Can I place PCBs vertically in the reflow oven?
While it is possible to place PCBs vertically in a reflow oven, it is generally not recommended. Vertical placement can lead to uneven heat distribution and may cause components to shift or fall off the board due to gravity. It is best to place PCBs horizontally to ensure stable component placement and uniform heating.
2. How do I determine the optimal spacing between PCBs in the oven?
The optimal spacing between PCBs in the oven depends on several factors, including the oven type, PCB size, and component heights. As a general rule, maintain a minimum spacing of 20mm between small PCBs and 50mm between large PCBs to allow for proper heat circulation and avoid shadowing effects. However, it is always recommended to refer to the oven manufacturer’s guidelines and conduct test runs to determine the best spacing for your specific setup.
3. Can I mix PCBs of different sizes in the same oven batch?
Mixing PCBs of different sizes in the same oven batch is possible but requires careful consideration. Smaller PCBs may be exposed to higher temperatures compared to larger PCBs due to their proximity to the heat source. To mitigate this, place smaller PCBs in cooler areas of the oven or adjust the temperature profile accordingly. It is also essential to ensure that the placement of the PCBs does not cause shadowing effects or hinder proper heat distribution.
4. How can I monitor the reflow process to ensure optimal PCB placement?
Monitoring the reflow process is crucial for ensuring optimal PCB placement and soldering results. Use temperature profiling systems, such as thermocouples or thermal cameras, to measure the temperature distribution across the PCB during the reflow process. Analyze the data to identify any hot spots, cold spots, or uneven heating patterns. Based on the findings, adjust the PCB placement, oven settings, or temperature profile to achieve more uniform heat distribution.
5. What should I do if I encounter soldering defects related to PCB placement?
If you encounter soldering defects, such as bridging, tombstoning, or insufficient wetting, related to PCB placement, take the following steps:
- Review the placement guidelines and factors discussed in this article to identify potential placement issues.
- Analyze the temperature profile data to determine if there are any hot spots, cold spots, or uneven heating patterns contributing to the defects.
- Adjust the PCB placement, spacing, or orientation based on the identified issues and guidelines.
- Modify the oven settings or temperature profile if necessary to achieve more uniform heat distribution.
- Conduct test runs with the updated placement and settings to verify the improvements in soldering quality.
If the defects persist, consult with experienced professionals or the oven manufacturer for further guidance and support.
Conclusion
Proper PCB oven placement is essential for achieving high-quality solder joints and reliable electronic assemblies. By considering factors such as oven type, PCB size and complexity, component characteristics, and temperature profile, you can determine the optimal placement for your PCBs.
Remember to follow the guidelines outlined in this article, including placing PCBs perpendicular to the airflow in convection ovens, maintaining sufficient spacing between boards, arranging large PCBs in a staggered pattern, and strategically placing temperature-sensitive and thermally conductive components.
Conduct test runs, monitor the reflow process, and make necessary adjustments to fine-tune the PCB placement and ensure optimal results. By implementing these practices and continuously improving your reflow soldering process, you can enhance the quality and reliability of your electronic assemblies.
Leave a Reply