What is RF Shielding?
RF shielding is a technique used to protect electronic devices from electromagnetic interference (EMI) and radio frequency interference (RFI). It involves enclosing the sensitive electronic components within a conductive barrier, which effectively blocks the electromagnetic waves from entering or escaping the shielded area.
Types of RF Shielding
There are two main types of RF shielding:
- Faraday Cage Shielding
- Absorptive Shielding
Faraday Cage Shielding
A Faraday cage is an enclosure made of conductive material, such as metal mesh or foil, that blocks electromagnetic fields. It works by redistributing the charges on its surface, creating an equal and opposite charge that cancels out the external field. Faraday cages are named after Michael Faraday, who discovered the principle in 1836.
Absorptive Shielding
Absorptive shielding involves using materials that absorb electromagnetic energy, converting it into heat. These materials are typically composed of ferrite compounds or carbon-based composites. Absorptive shielding is effective at reducing reflections and resonances within the shielded area, which can cause signal integrity issues.
Materials Used for PCB RF Shielding
Several materials are commonly used for creating an rf shield pcb. Each material has its own advantages and disadvantages, and the choice depends on the specific application and design requirements.
Metal Shielding Cans
Metal shielding cans are the most common type of RF shielding used in PCBs. They are typically made of aluminum, steel, or copper, and are designed to fit over the sensitive electronic components on the PCB. The cans are soldered or clipped onto the board, creating a Faraday cage around the shielded area.
Material | Advantages | Disadvantages |
---|---|---|
Aluminum | Lightweight, low cost, easy to form | Lower conductivity than copper |
Steel | Strong, durable, low cost | Heavy, prone to corrosion |
Copper | High conductivity, good shielding effectiveness | Expensive, difficult to form |
Conductive Coatings
Conductive coatings are another option for creating an rf shield pcb. These coatings are applied directly onto the PCB surface, forming a thin layer of conductive material around the sensitive components. Common conductive coatings include:
- Copper Coatings
- Silver Coatings
- Nickel Coatings
Conductive coatings offer several advantages over metal shielding cans:
- Thinner profile, allowing for smaller device designs
- Lower cost, as less material is required
- Easier to apply, using standard PCB manufacturing processes
However, conductive coatings also have some disadvantages:
- Lower shielding effectiveness compared to metal cans
- Susceptible to scratches and abrasion, which can compromise the shielding
- May require additional insulation to prevent short circuits
Conductive Gaskets
Conductive gaskets are often used in conjunction with metal shielding cans to improve the rf shield pcb performance. These gaskets are made of conductive elastomers, such as silicone or fluorosilicone, filled with conductive particles like silver, copper, or nickel.
Conductive gaskets are placed between the shielding can and the PCB, creating a continuous conductive path and ensuring a tight seal. This helps to prevent electromagnetic leakage and improves the overall shielding effectiveness.
Gasket Material | Filler Material | Advantages | Disadvantages |
---|---|---|---|
Silicone | Silver | High conductivity, good compression set | Expensive |
Fluorosilicone | Copper | Good chemical resistance, high temperature stability | Lower conductivity than silver |
EPDM | Nickel | Low cost, good weatherability | Limited temperature range |
Absorptive Materials
Absorptive materials, such as ferrite compounds and carbon-based composites, can be used to create an rf shield pcb with unique properties. These materials work by absorbing electromagnetic energy and converting it into heat, rather than reflecting it like metal shields.
Absorptive materials are particularly useful in applications where reflections and resonances within the shielded area can cause signal integrity issues. They are also effective at reducing high-frequency noise and harmonics.
Some common absorptive materials used in PCB RF shielding include:
- Ferrite Sheets
- Carbon-Loaded Plastics
- Conductive Foams
Material | Advantages | Disadvantages |
---|---|---|
Ferrite Sheets | High permeability, good absorption at high frequencies | Brittle, limited temperature range |
Carbon-Loaded Plastics | Lightweight, easy to mold, good absorption over wide frequency range | Lower absorption than ferrites |
Conductive Foams | Conformable, good absorption at high frequencies | Limited temperature range, may require compression |
Designing an Effective RF Shield PCB
Creating an effective rf shield pcb requires careful consideration of several factors, including the shielding material, the shield geometry, and the PCB layout.
Shielding Material Selection
The choice of shielding material depends on the specific application and design requirements. Factors to consider include:
- Frequency range of the EMI/RFI
- Required shielding effectiveness
- Environmental conditions (temperature, humidity, etc.)
- Space constraints and device form factor
- Manufacturing process and cost
Metal shielding cans offer the best shielding effectiveness but may not be suitable for all applications due to their size and weight. Conductive coatings and gaskets can provide a thinner profile and lower cost, but may have lower shielding effectiveness and durability.
Absorptive materials are useful for reducing reflections and resonances, but may not provide sufficient shielding against external EMI/RFI.
Shield Geometry Optimization
The geometry of the rf shield pcb plays a critical role in its effectiveness. The shield should be designed to minimize any gaps or seams, which can allow electromagnetic leakage.
Some key considerations for optimizing the shield geometry include:
- Minimizing the number of openings and penetrations
- Ensuring a tight fit between the shield and the PCB
- Using conductive gaskets or fingers to seal any necessary openings
- Avoiding sharp corners and edges, which can cause reflections and resonances
PCB Layout Considerations
The PCB layout also impacts the effectiveness of the rf shield pcb. Some best practices for PCB layout include:
- Placing sensitive components away from the edges of the board
- Using ground planes and power planes to provide additional shielding
- Minimizing the loop area of high-frequency traces
- Using guard traces and stitching vias to create local shielding regions
By carefully considering the shielding material, shield geometry, and PCB layout, designers can create an effective rf shield pcb that meets the specific requirements of their application.
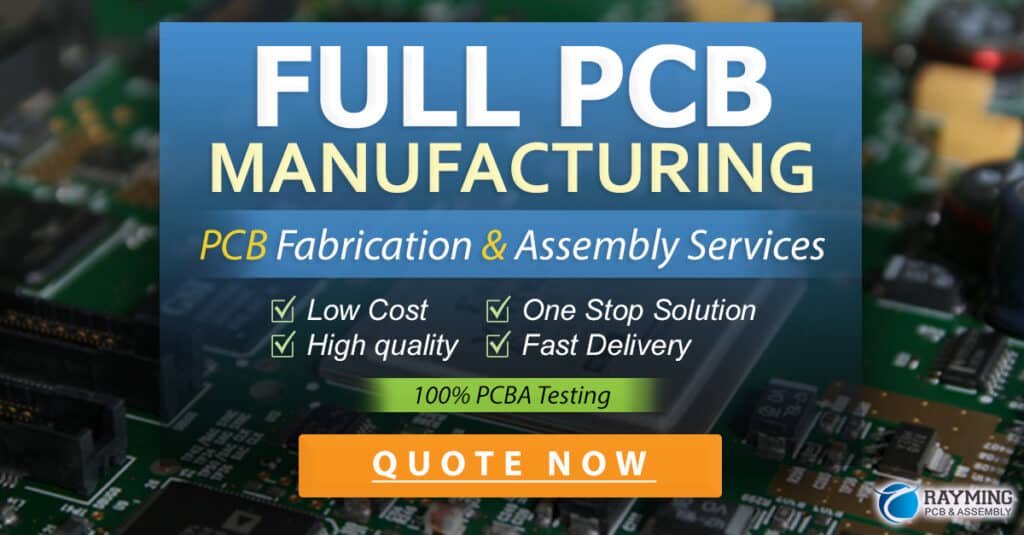
Frequently Asked Questions (FAQ)
1. What is the purpose of RF shielding in PCBs?
RF shielding in PCBs is used to protect sensitive electronic components from electromagnetic interference (EMI) and radio frequency interference (RFI). By enclosing these components within a conductive barrier, the shield prevents unwanted electromagnetic waves from entering or escaping the shielded area, thus ensuring the proper functioning of the device.
2. What are the most common materials used for PCB RF shielding?
The most common materials used for PCB RF shielding include:
- Metal shielding cans (aluminum, steel, copper)
- Conductive coatings (copper, silver, nickel)
- Conductive gaskets (silicone, fluorosilicone, EPDM)
- Absorptive materials (ferrite sheets, carbon-loaded plastics, conductive foams)
Each material has its own advantages and disadvantages, and the choice depends on the specific application and design requirements.
3. What are the advantages of using conductive coatings for RF shielding?
Conductive coatings offer several advantages over metal shielding cans for RF shielding in PCBs:
- Thinner profile, allowing for smaller device designs
- Lower cost, as less material is required
- Easier to apply, using standard PCB manufacturing processes
However, conductive coatings may have lower shielding effectiveness compared to metal cans and are susceptible to scratches and abrasion, which can compromise the shielding.
4. When should absorptive materials be used for RF shielding in PCBs?
Absorptive materials, such as ferrite compounds and carbon-based composites, are particularly useful in applications where reflections and resonances within the shielded area can cause signal integrity issues. They are also effective at reducing high-frequency noise and harmonics. Absorptive materials work by absorbing electromagnetic energy and converting it into heat, rather than reflecting it like metal shields.
5. What factors should be considered when designing an effective RF shield PCB?
When designing an effective rf shield pcb, several factors should be considered:
-
Shielding material selection: Choose a material that provides the required shielding effectiveness, fits the environmental conditions, and meets the space constraints and cost requirements.
-
Shield geometry optimization: Design the shield to minimize gaps and seams, ensure a tight fit with the PCB, and avoid sharp corners and edges that can cause reflections and resonances.
-
PCB layout considerations: Place sensitive components away from board edges, use ground and power planes for additional shielding, minimize high-frequency trace loop areas, and use guard traces and stitching vias for local shielding regions.
By carefully considering these factors, designers can create an rf shield pcb that effectively protects the device from EMI/RFI and ensures proper operation.
Leave a Reply