Types of PCB Materials
FR-4 (Flame Retardant 4)
FR-4 is the most commonly used material for PCB fabrication. It is a composite material made of woven fiberglass cloth with an epoxy resin binder. The “FR” stands for “Flame Retardant,” indicating that the material is designed to be fire-resistant.
Advantages of FR-4:
- Good mechanical strength and durability
- Excellent electrical insulation properties
- High resistance to moisture and chemicals
- Cost-effective
- Suitable for a wide range of applications
Disadvantages of FR-4:
- Limited thermal conductivity
- Higher dielectric constant compared to some other materials
- Not suitable for high-frequency applications above 2 GHz
Polyimide
Polyimide is a high-performance polymer material used in PCBs that require exceptional thermal and chemical resistance. It is often used in aerospace, military, and medical applications where reliability under extreme conditions is critical.
Advantages of Polyimide:
- Excellent thermal stability (up to 260°C)
- High mechanical strength and flexibility
- Low dielectric constant and dissipation factor
- Resistant to radiation and UV light
- Suitable for high-frequency applications
Disadvantages of Polyimide:
- Higher cost compared to FR-4
- More difficult to process and fabricate
- Limited availability and longer lead times
PTFE (Polytetrafluoroethylene)
PTFE, also known as Teflon, is a fluoropolymer material used in high-frequency and microwave pcbs. It offers excellent electrical properties and low dielectric loss, making it ideal for applications such as radar, satellite communication, and wireless networks.
Advantages of PTFE:
- Extremely low dielectric constant and dissipation factor
- High thermal stability and chemical resistance
- Excellent high-frequency performance (up to 100 GHz)
- Low moisture absorption
- Non-stick surface properties
Disadvantages of PTFE:
- High cost compared to other PCB materials
- Difficult to process and fabricate
- Poor mechanical strength and dimensional stability
- Limited availability and longer lead times
Rogers Materials
Rogers Corporation offers a range of specialized PCB materials designed for high-frequency and high-speed applications. These materials, such as RO3000, RO4000, and RT/duroid series, offer excellent electrical properties and low dielectric loss.
Advantages of Rogers Materials:
- Low dielectric constant and dissipation factor
- Excellent high-frequency performance
- Controlled dielectric constant and low thermal expansion
- Good thermal conductivity
- Suitable for applications such as 5G, IoT, and automotive radar
Disadvantages of Rogers Materials:
- Higher cost compared to FR-4 and other standard materials
- Limited availability and longer lead times
- Requires specialized processing and fabrication techniques
Comparison of PCB Materials
Material | Dielectric Constant | Dissipation Factor | Thermal Stability (°C) | Moisture Absorption | Typical Applications |
---|---|---|---|---|---|
FR-4 | 4.2 – 4.6 | 0.02 – 0.03 | 130 – 140 | 0.1 – 0.2% | General purpose |
Polyimide | 3.2 – 3.5 | 0.002 – 0.003 | 260 – 300 | 0.4 – 0.8% | High-temperature |
PTFE | 2.0 – 2.3 | 0.0002 – 0.0009 | 260 – 280 | < 0.01% | High-frequency |
Rogers RO4003 | 3.38 | 0.0027 | 280 | 0.06% | High-speed, RF |
Factors to Consider When Choosing PCB Materials
When selecting the appropriate PCB material for your application, consider the following factors:
-
Dielectric Constant: The dielectric constant (Dk) of a material determines the speed at which signals propagate through the PCB. A lower Dk value is desirable for high-frequency applications to minimize signal loss and distortion.
-
Dissipation Factor: The dissipation factor (Df) represents the amount of energy lost as heat when an alternating current is applied to the material. A lower Df value indicates better high-frequency performance and lower signal loss.
-
Thermal Stability: The thermal stability of a PCB material determines its ability to withstand high temperatures without degradation. This is especially important for applications exposed to extreme temperatures or high-power components.
-
Moisture Absorption: Moisture absorption can affect the electrical properties and dimensional stability of a PCB. Materials with low moisture absorption are preferred in environments with high humidity or exposure to liquids.
-
Cost and Availability: The cost and availability of PCB materials should be considered when selecting a material for your application. Standard materials like FR-4 are widely available and cost-effective, while specialized materials like PTFE and Rogers may have higher costs and longer lead times.
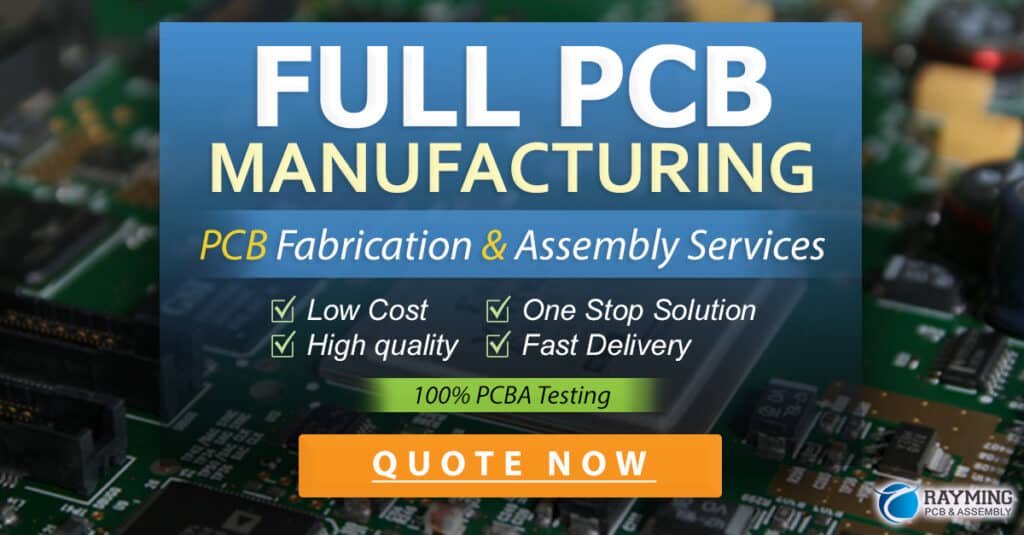
PCB Material Selection Process
-
Define application requirements: Determine the specific requirements of your application, such as operating frequency, temperature range, and environmental conditions.
-
Evaluate electrical properties: Consider the dielectric constant, dissipation factor, and other electrical properties of the materials based on your application requirements.
-
Assess thermal and mechanical properties: Evaluate the thermal stability, moisture absorption, and mechanical strength of the materials to ensure they meet your application’s needs.
-
Consider manufacturing constraints: Take into account the manufacturability of the materials, including processing techniques, minimum feature sizes, and available finishes.
-
Balance cost and performance: Find the right balance between material cost and performance to optimize your design within budget constraints.
-
Consult with PCB manufacturers: Collaborate with experienced PCB manufacturers to discuss your requirements and get recommendations on the most suitable materials for your application.
Frequently Asked Questions (FAQ)
-
What is the most commonly used PCB material?
FR-4 (Flame Retardant 4) is the most widely used PCB material due to its good balance of mechanical, electrical, and thermal properties, as well as its cost-effectiveness. -
What are the advantages of using Polyimide for PCBs?
Polyimide offers excellent thermal stability, high mechanical strength, and low dielectric constant, making it suitable for applications that require reliability under extreme conditions, such as aerospace and military electronics. -
Which PCB material is best for high-frequency applications?
PTFE (Polytetrafluoroethylene) and Rogers materials are preferred for high-frequency applications due to their extremely low dielectric constant and dissipation factor, which minimize signal loss and distortion at high frequencies. -
Can FR-4 be used for high-temperature applications?
While FR-4 is suitable for general-purpose applications, it has limited thermal stability compared to materials like Polyimide. For high-temperature applications, materials with higher thermal stability, such as Polyimide or certain Rogers materials, are recommended. -
How does moisture absorption affect PCB performance?
Moisture absorption can lead to changes in the dielectric constant and dimensional stability of a PCB, which can affect its electrical performance and mechanical integrity. Materials with low moisture absorption, such as PTFE, are preferred in environments with high humidity or exposure to liquids.
Conclusion
Selecting the appropriate PCB material is crucial for ensuring the performance, reliability, and cost-effectiveness of your electronic devices. By understanding the properties and characteristics of different PCB materials, such as FR-4, Polyimide, PTFE, and Rogers materials, you can make informed decisions when designing and manufacturing PCBs for various applications.
When choosing a PCB material, consider factors such as dielectric constant, dissipation factor, thermal stability, moisture absorption, and cost. Engage with experienced PCB manufacturers to discuss your specific requirements and obtain recommendations on the most suitable materials for your application.
By carefully selecting the right PCB material and optimizing your design, you can achieve superior performance, durability, and reliability in your electronic products while meeting budget and manufacturing constraints.
Leave a Reply