What is V-scoring?
V-scoring, also known as v-grooving, is a method of creating a V-shaped groove along the surface of a PCB panel. This groove is typically cut using a special V-shaped blade on a CNC machine or a laser cutter. The depth and angle of the groove are carefully controlled to ensure that the PCB can be easily broken along the scored line without damaging the components or the board itself.
How V-scoring Works
The V-scoring process involves the following steps:
-
Design: The PCB design is created with designated v-score lines, which are usually placed along the edges of individual boards within a larger panel.
-
Panelization: Multiple PCB designs are combined into a single panel to maximize production efficiency.
-
Scoring: The panel is placed on a CNC machine or laser cutter, and the v-score lines are cut into the surface of the board according to the designated design.
-
Depaneling: After the manufacturing process is complete, the individual PCBs are separated from the panel by breaking them along the v-score lines.
Advantages of V-scoring in PCB Manufacturing
V-scoring offers several benefits in PCB manufacturing, including:
-
Improved Efficiency: V-scoring allows for multiple PCBs to be produced on a single panel, reducing handling time and increasing production speed.
-
Cost-effectiveness: By maximizing the number of PCBs per panel, v-scoring helps to minimize material waste and lower production costs.
-
Precise Breaking Points: V-score lines provide clean, accurate breaking points, ensuring that the individual PCBs are separated without damage to the components or the board itself.
-
Flexibility: V-scoring can be used with a variety of PCB materials and thicknesses, making it a versatile option for different applications.
Applications of V-scored PCBs
V-scored PCBs are used in a wide range of industries and applications, such as:
-
Consumer Electronics: Smartphones, tablets, laptops, and wearables often require compact, high-density PCBs that can be efficiently produced using v-scoring.
-
Automotive Industry: V-scored PCBs are used in various automotive electronics, including infotainment systems, sensors, and control modules.
-
Medical Devices: Compact, reliable PCBs are essential for medical devices such as pacemakers, glucose monitors, and portable diagnostic tools.
-
Industrial Equipment: V-scored PCBs are used in industrial control systems, sensors, and automation devices.
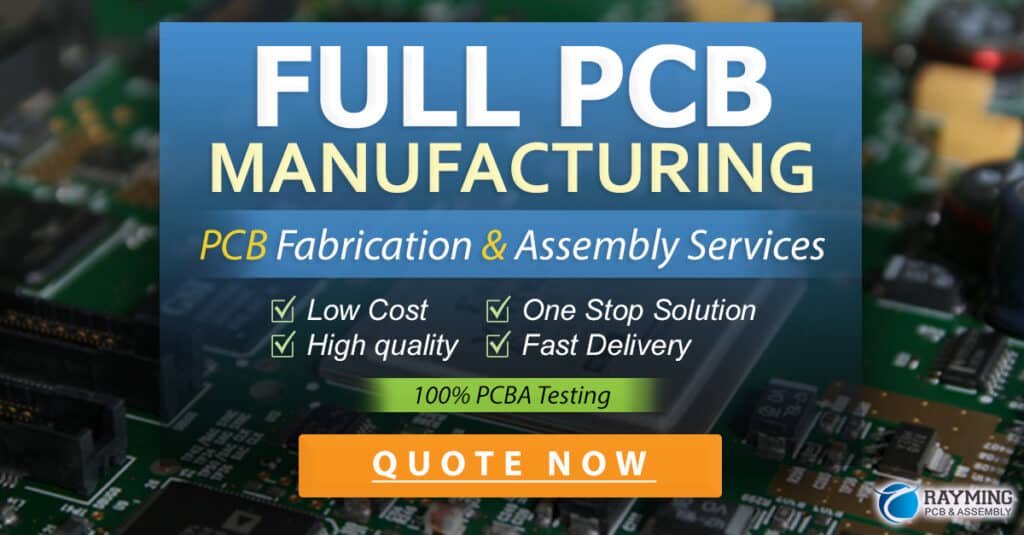
Best Practices for V-scoring in PCB Design
To ensure optimal results when using v-scoring in PCB manufacturing, consider the following best practices:
-
Placement: Position v-score lines away from components and sensitive areas of the PCB to avoid damage during the breaking process.
-
Depth Control: Carefully control the depth of the v-score to ensure that the PCB can be easily broken without compromising its structural integrity.
-
Angle Selection: Choose an appropriate v-score angle based on the thickness and material of the PCB to minimize stresses and prevent unintended breakage.
-
Panelization Strategy: Optimize the panel layout to maximize the number of PCBs per panel while ensuring sufficient space for v-score lines and other manufacturing considerations.
Comparing V-scoring to Other Depaneling Methods
While v-scoring is a popular choice for PCB depaneling, there are other methods available, each with its own advantages and disadvantages. Let’s compare v-scoring to some of these alternatives:
Method | Advantages | Disadvantages |
---|---|---|
V-scoring | – Precise and clean breaking points – Cost-effective – Flexible |
– Limited to straight lines – Requires specialized equipment |
Tab Routing | – Suitable for complex shapes – Minimal stress on the PCB |
– More expensive than v-scoring – Slower production process |
Pizza Cutting | – Fast and efficient – Suitable for large panels |
– Less precise than v-scoring – Can cause stress on the PCB |
Perforating | – Economical – Suitable for high-volume production |
– Less precise than v-scoring – Can leave rough edges |
Ultimately, the choice of depaneling method depends on factors such as the specific PCB design, production volume, and budget constraints.
Frequently Asked Questions (FAQ)
-
Q: Can v-scoring be used with any PCB material?
A: V-scoring is compatible with most common PCB materials, including FR-4, aluminum-backed boards, and flexible substrates. However, the specific v-scoring parameters may need to be adjusted based on the material properties. -
Q: How does the depth of the v-score affect the PCB?
A: The depth of the v-score is crucial in ensuring that the PCB can be easily broken along the scored line without damaging the board or components. If the v-score is too shallow, the PCB may not break cleanly, while an excessively deep score can weaken the board’s structural integrity. -
Q: Are there any limitations to the shape of v-score lines?
A: V-scoring is typically limited to straight lines, as the v-shaped blade or laser cutter follows a linear path. For more complex shapes or contours, alternative depaneling methods like tab routing may be more suitable. -
Q: Can v-scoring be used for both single-sided and double-sided PCBs?
A: Yes, v-scoring can be applied to both single-sided and double-sided PCBs. However, the v-scoring process may need to be adjusted to account for the presence of components on both sides of the board. -
Q: How does v-scoring compare to other depaneling methods in terms of cost?
A: V-scoring is generally considered a cost-effective depaneling method, as it allows for efficient production of multiple PCBs on a single panel. However, the specific cost comparison may vary depending on factors such as the PCB design, production volume, and the chosen alternative method.
Conclusion
V-scoring is a valuable technique in PCB manufacturing, offering a precise, efficient, and cost-effective way to separate individual boards from a larger panel. By creating clean, pre-determined breaking points, v-scoring simplifies the assembly process and reduces the risk of damage to components or the PCB itself. When designing PCBs for v-scoring, it is essential to consider factors such as v-score placement, depth, and angle to ensure optimal results.
As the electronics industry continues to demand smaller, more complex, and more reliable PCBs, v-scoring will likely remain an essential tool in PCB manufacturing. By understanding the principles, advantages, and best practices of v-scoring, PCB designers and manufacturers can leverage this technique to create high-quality, efficiently produced PCBs for a wide range of applications.
Leave a Reply