Introduction to V-groove PCB Technology
V-groove PCB, also known as v-scoring or v-cut PCB, is an advanced printed circuit board fabrication technique that involves cutting V-shaped grooves partially through the board substrate. This process enables the creation of clean, precise break-away tabs, making it easier to separate individual boards from a larger panel. V-groove technology is widely used in the electronics industry for various applications, such as prototyping, small-batch production, and manufacturing of complex PCB designs.
What are the Benefits of V-groove PCB?
V-groove PCB offers several advantages over traditional PCB fabrication methods:
-
Cleaner and more precise breaks: V-grooves ensure clean, smooth edges when separating individual boards from a panel, reducing the risk of damage to the PCB or its components.
-
Faster assembly: With pre-scored break-away tabs, assembling and separating PCBs becomes quicker and more efficient.
-
Cost-effective: V-groove technology allows for the maximization of panel space, reducing material waste and lowering production costs.
-
Versatility: V-scoring can be applied to various PCB materials, including FR-4, aluminum-backed, and flexible substrates.
How V-groove PCB Technology Works
The V-groove PCB fabrication process involves several steps:
-
PCB design: The PCB layout is designed with designated v-score lines, indicating where the grooves will be cut.
-
Groove cutting: Using specialized equipment, V-shaped grooves are cut into the PCB substrate along the designated lines. The depth of the groove is carefully controlled to ensure that it does not completely penetrate the board.
-
PCB fabrication: The PCB undergoes the standard fabrication process, including the application of copper layers, solder mask, and silkscreen.
-
Component assembly: Electronic components are soldered onto the PCB as per the design requirements.
-
Board separation: Individual boards are easily separated from the panel by applying gentle pressure along the v-score lines, resulting in clean, precise breaks.
V-groove Depth and Angle
The depth and angle of the V-groove are critical factors in ensuring the proper functioning of break-away tabs. The groove depth is typically set at around 30-40% of the PCB thickness, depending on the substrate material and thickness. The most common V-groove angles are:
V-groove Angle | Application |
---|---|
30° | Suitable for thinner PCBs (0.8mm to 1.0mm) |
45° | Widely used for standard PCB thicknesses (1.2mm to 1.6mm) |
60° | Recommended for thicker PCBs (1.6mm or more) |
Choosing the appropriate V-groove depth and angle ensures that the break-away tabs are strong enough to hold the boards together during fabrication and assembly, yet easy to separate when needed.
Applications of V-groove PCB Technology
V-groove PCB technology finds applications in various industries and sectors, including:
-
Consumer electronics: V-scored PCBs are used in the production of smartphones, tablets, wearables, and other consumer devices.
-
Automotive: V-groove technology is employed in the manufacturing of automotive electronic components, such as infotainment systems, sensors, and control modules.
-
Medical devices: V-scored PCBs are utilized in the production of medical equipment, including patient monitors, diagnostic tools, and wearable health devices.
-
Industrial automation: V-groove PCBs are used in the fabrication of industrial control systems, sensors, and communication modules.
-
Aerospace and defense: V-scoring is applied in the manufacturing of high-reliability PCBs for aerospace and defense applications, such as avionics, satellite systems, and military communication equipment.
Case Study: V-groove PCB in Smartphone Manufacturing
One of the most prominent applications of V-groove PCB technology is in the production of smartphones. Modern smartphones feature complex PCB designs with multiple layers and high component density. V-scoring allows manufacturers to maximize panel utilization, reduce waste, and streamline the assembly process.
In a typical smartphone PCB panel, multiple individual boards are laid out with v-score lines between them. After the fabrication and assembly processes, the boards are easily separated along the v-score lines, resulting in clean, precise breaks. This technique enables smartphone manufacturers to produce high volumes of PCBs efficiently and cost-effectively.
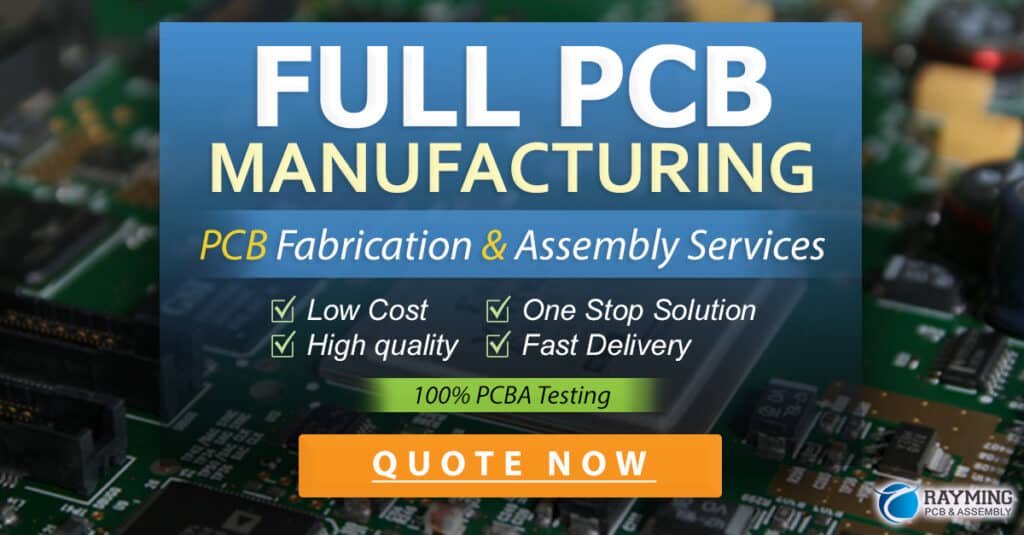
Advantages of V-groove PCB Over Other Separation Methods
V-groove PCB technology offers several advantages over alternative board separation methods, such as routing or punching:
-
Cleaner breaks: V-scoring produces cleaner, smoother edges compared to routing or punching, reducing the risk of damage to the PCB or its components.
-
Higher precision: V-grooves allow for more precise and consistent board separation, ensuring that the dimensions of the individual boards remain within the specified tolerances.
-
Faster processing: V-scoring is a faster process compared to routing, as it does not require the complete cutting of the board substrate. This translates to shorter lead times and increased production efficiency.
-
Cost-effectiveness: V-groove technology enables the maximization of panel space, reducing material waste and lowering overall production costs.
Comparison Table: V-groove PCB vs. Routing and Punching
Separation Method | Precision | Edge Quality | Processing Speed | Cost |
---|---|---|---|---|
V-groove PCB | High | Clean, smooth | Fast | Low |
Routing | Medium | Rough, prone to damage | Slow | High |
Punching | Low | Rough, prone to damage | Fast | Medium |
As evident from the comparison table, V-groove PCB technology offers the best combination of precision, edge quality, processing speed, and cost-effectiveness among the three board separation methods.
Designing for V-groove PCB
When designing a PCB layout for V-groove fabrication, there are several essential considerations to keep in mind:
-
V-score line placement: Ensure that the v-score lines are placed in non-critical areas of the PCB, away from components, traces, and other sensitive features.
-
Groove depth and angle: Choose the appropriate groove depth and angle based on the PCB material, thickness, and the desired break-away tab strength.
-
Panelization: Optimize the panel layout to maximize board density and minimize material waste. Consider factors such as board orientation, spacing, and tooling holes.
-
Design rules: Adhere to the manufacturer’s design rules and guidelines for V-groove PCB fabrication, including minimum spacing, trace width, and hole size.
By following these design considerations, you can ensure that your V-groove PCB is fabricated and assembled efficiently, with clean, precise break-away tabs.
FAQ
-
Q: Can V-groove technology be applied to any PCB material?
A: V-scoring can be used on most common PCB substrates, including FR-4, aluminum-backed, and flexible materials. However, some specialized materials may require different groove depths or angles. -
Q: What is the minimum spacing required between components and v-score lines?
A: The minimum spacing between components and v-score lines depends on the specific design rules provided by the PCB manufacturer. Typically, a minimum distance of 0.5mm to 1mm is recommended to ensure the structural integrity of the board. -
Q: How does the v-groove depth affect the break-away tab strength?
A: The groove depth directly influences the strength of the break-away tab. A shallower groove results in a stronger tab, while a deeper groove makes the tab easier to break. The optimal groove depth balances the need for structural stability during fabrication and assembly with the ease of separating individual boards. -
Q: Can V-groove PCBs be used for high-density designs?
A: Yes, V-groove technology is suitable for high-density PCB designs. By optimizing the panel layout and following the manufacturer’s design rules, you can achieve efficient board separation without compromising the integrity of the components or traces. -
Q: Are there any limitations to the size or shape of V-groove PCBs?
A: V-groove PCBs can be fabricated in various sizes and shapes, depending on the capabilities of the manufacturing equipment. However, very small or intricate board outlines may pose challenges for v-scoring. It is essential to consult with the PCB manufacturer to ensure that your design is compatible with their V-groove fabrication process.
Conclusion
V-groove PCB technology is a valuable tool for the electronics industry, enabling the efficient and cost-effective production of high-quality printed circuit boards. By incorporating v-score lines into the PCB design, manufacturers can create clean, precise break-away tabs, simplifying the board separation process and reducing material waste.
As the demand for smaller, more complex electronic devices continues to grow, V-groove PCB technology will play an increasingly crucial role in meeting the challenges of modern PCB fabrication. By understanding the principles, applications, and design considerations of v-scoring, PCB designers and manufacturers can leverage this technology to create innovative, reliable, and cost-effective electronic products.
Leave a Reply