How Through-Hole PCB Assembly Works
The through-hole PCB assembly process involves several key steps:
-
PCB Design and Fabrication: The PCB is designed using specialized software, and the design is sent to a PCB manufacturer for fabrication. The manufacturer creates the board with the required number of layers, drills the necessary holes, and applies any required surface finishes.
-
Component Placement: The electronic components are inserted into the drilled holes on the PCB. This process can be done manually for small-scale production or prototypes, or by using automated insertion machines for larger-scale manufacturing.
-
Soldering: Once the components are in place, the board undergoes soldering to create electrical connections between the component leads and the PCB traces. This is typically done using wave soldering machines, which pass the board over a molten solder wave, or through reflow soldering ovens, which use a precise temperature profile to melt the solder paste and form the connections.
-
Inspection and Testing: After soldering, the assembled PCBs are inspected for any defects or errors. This can be done visually, using automated optical inspection (AOI) systems, or through various electrical testing methods to ensure the board functions as intended.
Advantages of Through-Hole PCB Assembly
Through-hole PCB assembly offers several advantages over other methods, such as surface-mount technology (SMT):
-
Mechanical Strength: Through-hole components are generally more robust and resistant to mechanical stress and vibration due to the stronger physical connection between the component leads and the PCB.
-
Ease of Manual Assembly: Through-hole components are easier to handle and install manually, making them ideal for prototyping, small-scale production, or hobbyist projects.
-
Simplified Rework and Repair: Replacing or repairing through-hole components is often easier than their surface-mount counterparts, as the leads are more accessible and the components are larger.
-
High Power Handling: Through-hole components can often handle higher power levels than surface-mount components due to their larger size and better heat dissipation capabilities.
Disadvantages of Through-Hole PCB Assembly
Despite its many benefits, through-hole PCB assembly also has some drawbacks:
-
Larger PCB Size: Through-hole components require drilled holes and more space on the PCB, resulting in larger board sizes compared to surface-mount designs.
-
Increased Production Time: The need to drill holes and manually insert components can increase production time and costs, especially for high-volume manufacturing.
-
Limited Component Availability: As surface-mount technology has become more prevalent, some newer components may only be available in SMT packages, limiting design options for through-hole assemblies.
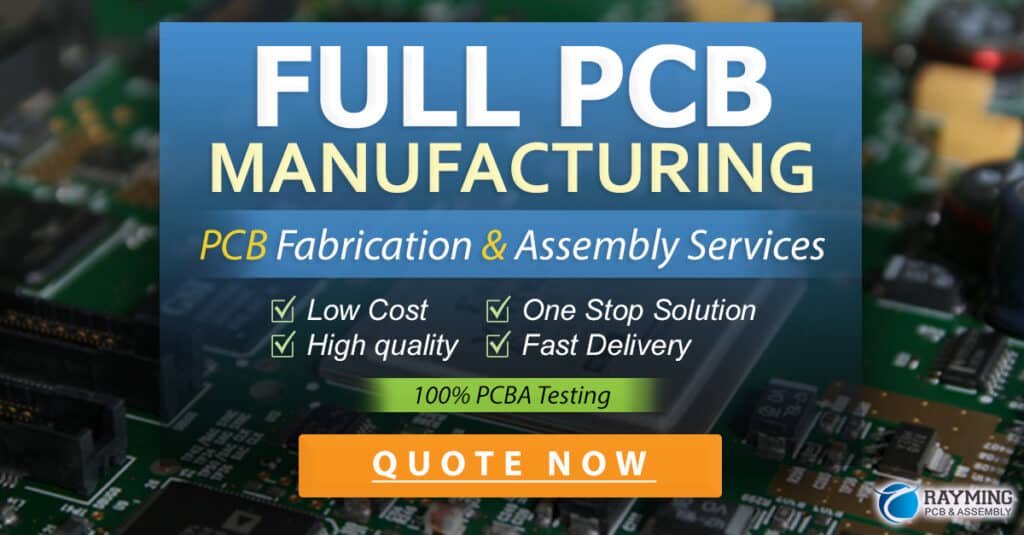
Applications of Through-Hole PCB Assembly
Through-hole PCB assembly is used in a wide range of applications, including:
-
Industrial Equipment: Through-hole components are often used in industrial equipment due to their reliability and resistance to harsh environments.
-
Aerospace and Military: The mechanical strength and high power handling capabilities of through-hole components make them well-suited for aerospace and military applications.
-
Automotive Electronics: Through-hole assembly is commonly used in automotive electronics, particularly for high-power components and applications that require increased durability.
-
Consumer Electronics: While surface-mount technology dominates the consumer electronics market, through-hole components are still used for certain high-power or mechanical components, such as connectors and transformers.
-
Prototyping and Hobbyist Projects: The ease of manual assembly and repair makes through-hole PCB assembly a popular choice for prototyping and hobbyist electronics projects.
Comparison of Through-Hole and Surface-Mount PCB Assembly
Characteristic | Through-Hole Assembly | Surface-Mount Assembly |
---|---|---|
Component Size | Larger | Smaller |
PCB Size | Larger | Smaller |
Component Density | Lower | Higher |
Mechanical Strength | Higher | Lower |
Power Handling | Higher | Lower |
Ease of Manual Assembly | Easier | More Difficult |
Rework and Repair | Easier | More Difficult |
Production Time | Longer | Shorter |
Production Cost | Higher | Lower |
Future of Through-Hole PCB Assembly
While surface-mount technology has largely overtaken through-hole assembly in many applications, through-hole PCB assembly remains an essential technique in the electronics industry. Its reliability, mechanical strength, and ease of manual assembly ensure that it will continue to be used in specific applications and scenarios.
As technology advances, some manufacturers are exploring hybrid designs that combine both through-hole and surface-mount components on the same PCB. This approach allows designers to take advantage of the benefits of both technologies while minimizing their drawbacks.
Additionally, advancements in automated through-hole assembly equipment, such as selective soldering machines and robotic component insertion systems, are helping to bridge the gap between through-hole and surface-mount assembly in terms of production efficiency and cost.
Frequently Asked Questions (FAQ)
-
Q: What is the difference between through-hole and surface-mount PCB assembly?
A: Through-hole assembly involves inserting component leads through drilled holes in the PCB and soldering them on the opposite side, while surface-mount assembly involves placing components directly onto the surface of the PCB and soldering them in place. -
Q: When should I choose through-hole PCB assembly over surface-mount?
A: Through-hole assembly is preferable when mechanical strength, high power handling, or ease of manual assembly and repair are primary concerns. It is also suitable for prototyping and small-scale production. -
Q: Can through-hole and surface-mount components be used on the same PCB?
A: Yes, hybrid PCB designs that incorporate both through-hole and surface-mount components are possible, allowing designers to take advantage of the benefits of both technologies. -
Q: Are through-hole components becoming obsolete?
A: While surface-mount technology has become more prevalent, through-hole components are still widely used in specific applications and scenarios where their strengths are required. They are not likely to become completely obsolete in the foreseeable future. -
Q: What are the main advantages of through-hole PCB assembly?
A: The main advantages of through-hole PCB assembly include increased mechanical strength, ease of manual assembly and repair, high power handling capabilities, and suitability for prototyping and small-scale production.
In conclusion, through-hole PCB assembly remains a vital technique in the electronics industry, offering a reliable and robust solution for creating electronic devices. Despite the growing popularity of surface-mount technology, through-hole assembly continues to be the preferred choice for applications that require mechanical strength, high power handling, and ease of manual assembly and repair. As technology advances, through-hole PCB assembly will likely evolve and adapt to meet the changing needs of the electronics industry.
Leave a Reply