Introduction to Prepreg in PCB Manufacturing
Prepreg, short for pre-impregnated, is a crucial material used in the manufacturing of printed circuit boards (PCBs). It is a composite material made of a reinforcement fabric, such as fiberglass, that is pre-impregnated with a partially cured epoxy resin. Prepreg plays a vital role in the construction of multi-layer PCBs, offering essential benefits such as insulation, mechanical strength, and dimensional stability.
In this article, we will explore the various aspects of prepreg in PCB manufacturing, including its composition, properties, and applications. We will also discuss the advantages of using prepreg in PCB fabrication and its impact on the overall performance and reliability of the finished product.
Composition and Properties of Prepreg
Reinforcement Fabric
The reinforcement fabric used in prepreg is typically made of fiberglass, which is known for its excellent electrical insulation properties and high mechanical strength. The most common types of fiberglass used in prepreg are:
- E-glass: A low-cost, general-purpose fiberglass with good electrical and mechanical properties.
- S-glass: A high-strength fiberglass that offers superior mechanical properties compared to E-glass.
- NE-glass: A fiberglass with enhanced dielectric properties, making it suitable for high-frequency applications.
The choice of reinforcement fabric depends on the specific requirements of the PCB, such as the desired electrical performance, mechanical strength, and cost considerations.
Epoxy Resin
The epoxy resin used in prepreg is a thermosetting polymer that undergoes a partial curing process during the prepreg manufacturing. The partial curing allows the prepreg to maintain its flexibility and tackiness, which is essential for the lamination process in PCB fabrication. The most common types of epoxy resins used in prepreg are:
- FR-4: A flame-retardant epoxy resin that is widely used in the PCB industry due to its excellent electrical and mechanical properties, as well as its cost-effectiveness.
- High Tg epoxy: An epoxy resin with a higher glass transition temperature (Tg), which offers improved thermal stability and resistance to deformation at elevated temperatures.
- Low Dk/Df epoxy: An epoxy resin with low dielectric constant (Dk) and dissipation factor (Df), making it suitable for high-frequency applications.
The selection of the epoxy resin depends on the specific performance requirements of the PCB, such as the operating temperature range, electrical properties, and environmental factors.
Prepreg Manufacturing Process
The manufacturing process of prepreg involves the following steps:
- The reinforcement fabric is unwound from a roll and passed through a resin bath containing the uncured epoxy resin.
- The resin-impregnated fabric is then passed through a series of rollers to ensure uniform distribution of the resin and to remove any excess resin.
- The impregnated fabric is then partially cured in an oven under controlled temperature and time conditions.
- The partially cured prepreg is cooled and cut to the desired size and shape.
- The prepreg sheets are then packaged and stored under controlled conditions to maintain their properties until they are ready for use in PCB fabrication.
Applications of Prepreg in PCB Manufacturing
Multi-layer PCB Construction
Prepreg is primarily used in the construction of multi-layer PCBs, where it serves as the insulating and bonding material between the conductive copper layers. The typical structure of a multi-layer PCB using prepreg is as follows:
Layer | Material |
---|---|
Outer Layer | Copper Foil |
Prepreg | Fiberglass + Epoxy Resin |
Inner Layer | Copper Foil |
Core Material | FR-4, Aluminum, or other substrate |
Inner Layer | Copper Foil |
Prepreg | Fiberglass + Epoxy Resin |
Outer Layer | Copper Foil |
During the lamination process, the prepreg sheets are placed between the copper layers and subjected to heat and pressure. The heat causes the epoxy resin in the prepreg to fully cure, bonding the layers together and creating a solid, cohesive structure.
Insulation and Dielectric Properties
One of the primary functions of prepreg in PCBs is to provide electrical insulation between the conductive copper layers. The fiberglass reinforcement fabric and the epoxy resin in the prepreg offer excellent dielectric properties, preventing short circuits and ensuring reliable signal transmission.
The dielectric properties of prepreg are characterized by two key parameters:
- Dielectric Constant (Dk): A measure of the material’s ability to store electrical energy. A lower Dk value indicates better signal integrity and higher signal speed.
- Dissipation Factor (Df): A measure of the material’s ability to dissipate electrical energy as heat. A lower Df value indicates lower signal loss and better signal quality.
The choice of prepreg material with the appropriate Dk and Df values is crucial for high-frequency applications, such as RF and microwave circuits, to ensure optimal signal performance.
Mechanical Strength and Dimensional Stability
Prepreg also provides mechanical strength and dimensional stability to the PCB structure. The fiberglass reinforcement fabric in the prepreg offers high tensile strength and resistance to deformation, preventing warping and twisting of the PCB during the manufacturing process and in operation.
The dimensional stability of prepreg is essential for maintaining the precise alignment of the copper layers and the drilled holes in the PCB. Any misalignment or shifting of the layers can lead to connection failures and compromised signal integrity.
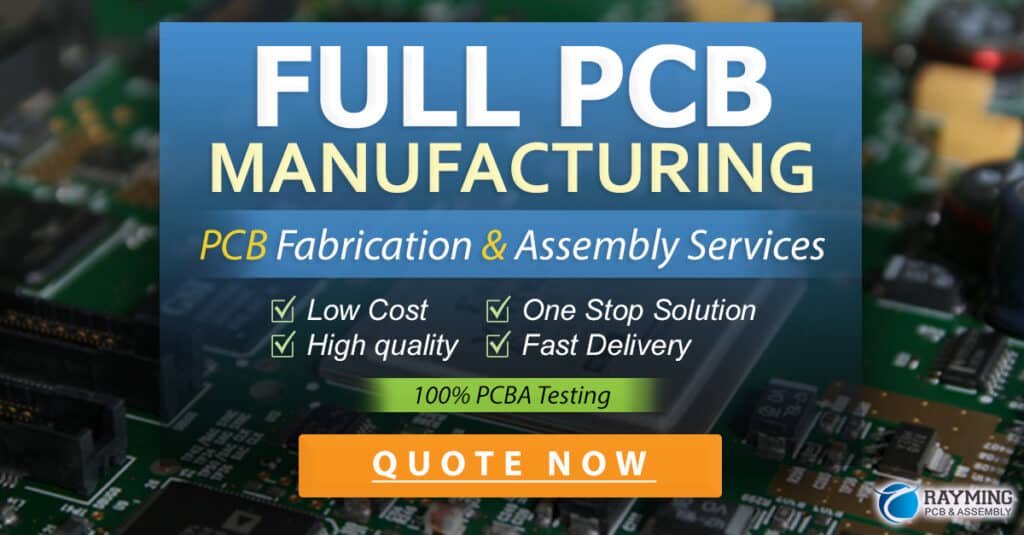
Advantages of Using Prepreg in PCB Manufacturing
Improved Reliability and Durability
The use of prepreg in PCB manufacturing offers several advantages that contribute to the overall reliability and durability of the finished product:
- Strong inter-layer bonding: The fully cured epoxy resin in the prepreg creates a strong, cohesive bond between the copper layers, preventing delamination and ensuring the structural integrity of the PCB.
- Resistance to environmental factors: The epoxy resin in the prepreg provides protection against moisture, chemicals, and other environmental factors that can degrade the performance and reliability of the PCB.
- Thermal stability: The use of high Tg prepreg materials ensures that the PCB can withstand elevated operating temperatures without deformation or loss of mechanical strength.
Enhanced Signal Integrity
Prepreg materials with low Dk and Df values contribute to enhanced signal integrity in high-frequency PCB applications:
- Reduced signal distortion: The low Dk value of the prepreg minimizes the signal distortion caused by the dielectric material, ensuring clean and accurate signal transmission.
- Lower signal loss: The low Df value of the prepreg reduces the amount of signal energy dissipated as heat, resulting in lower signal loss and improved signal quality.
Cost-effectiveness and Scalability
The use of prepreg in PCB manufacturing offers cost-effectiveness and scalability advantages:
- Streamlined manufacturing process: The use of prepreg simplifies the PCB manufacturing process by eliminating the need for separate lamination and curing steps, reducing production time and costs.
- Scalability: Prepreg materials are available in various thicknesses and sizes, allowing for the fabrication of PCBs with different layer counts and form factors, making it a scalable solution for a wide range of applications.
Conclusion
Prepreg is an essential material in the manufacturing of high-quality, reliable, and high-performance PCBs. Its unique composition, consisting of a reinforcement fabric pre-impregnated with a partially cured epoxy resin, offers a combination of electrical insulation, mechanical strength, and dimensional stability that is crucial for the construction of multi-layer PCBs.
The use of prepreg in PCB manufacturing provides numerous advantages, including improved reliability and durability, enhanced signal integrity, and cost-effectiveness and scalability. As the demand for more complex and high-performance electronic devices continues to grow, the role of prepreg in PCB fabrication will remain pivotal in ensuring the quality and reliability of these products.
Frequently Asked Questions (FAQ)
1. What is the difference between prepreg and core material in PCBs?
Prepreg is a composite material made of a reinforcement fabric pre-impregnated with a partially cured epoxy resin, used as an insulating and bonding layer between the copper layers in a multi-layer PCB. Core material, on the other hand, is a fully cured substrate, such as FR-4 or aluminum, that serves as the base material for the PCB stack-up.
2. Can prepreg be used in single-layer PCBs?
While prepreg is primarily used in the construction of multi-layer PCBs, it can also be used in single-layer PCBs as a base material or a protective coating. However, the use of prepreg in single-layer PCBs is less common, as it may not offer significant benefits over other substrate materials in terms of cost and performance.
3. How does the choice of prepreg material affect the performance of high-frequency PCBs?
The choice of prepreg material with the appropriate dielectric constant (Dk) and dissipation factor (Df) values is crucial for high-frequency PCB applications. Low Dk and Df values minimize signal distortion and loss, ensuring clean and accurate signal transmission. Therefore, selecting the right prepreg material based on the specific high-frequency application requirements is essential for optimal signal performance.
4. What are the storage requirements for prepreg materials?
Prepreg materials must be stored under controlled conditions to maintain their properties until they are ready for use in PCB fabrication. Typically, prepreg sheets are stored in a cool, dry environment with a temperature range of 40-50°F (4-10°C) and a relative humidity of 50-70%. Proper storage helps to prevent the premature curing of the epoxy resin and ensures the consistency of the prepreg properties.
5. Can prepreg be used in flexible PCBs?
Yes, prepreg can be used in the construction of flexible PCBs. In this case, the reinforcement fabric is typically made of a flexible material, such as polyimide, and the epoxy resin is formulated to provide the necessary flexibility and bend resistance. The use of prepreg in flexible PCBs helps to improve the mechanical strength and dimensional stability of the circuit while maintaining the desired flexibility.
Leave a Reply