What is PCB tolerance?
PCB tolerance is the allowable deviation from the specified dimensions or properties of a printed circuit board. It is a measure of how much a particular feature, such as the width of a trace or the diameter of a hole, can vary from its intended size while still maintaining the desired performance and functionality of the PCB.
Tolerances are essential in PCB design and manufacturing because they account for the inherent limitations and variations in the production process. No manufacturing method is perfect, and there will always be some level of deviation from the ideal dimensions. By specifying appropriate tolerances, designers can ensure that the PCB will function as intended, even if the actual dimensions vary slightly from the nominal values.
Factors Affecting PCB Tolerance
Several factors can influence the tolerance requirements for a PCB, including:
-
Manufacturing process: Different PCB fabrication techniques, such as etching, drilling, and plating, have their own inherent limitations and tolerances.
-
Material properties: The choice of substrate material, copper weight, and other materials used in the PCB can affect the achievable tolerances.
-
Feature size: Smaller features, such as narrow traces or small vias, typically require tighter tolerances than larger features.
-
Board complexity: More complex PCB designs with high component density, multiple layers, or fine-pitch components may require more stringent tolerances.
-
Environmental factors: The operating environment of the PCB, such as temperature, humidity, and vibration, can impact the required tolerances.
Typical PCB Tolerances
The typical tolerances for PCBs can vary depending on the specific manufacturing process, material, and feature size. However, there are some general guidelines that are commonly used in the industry.
Trace Width and Spacing
Trace width and spacing are critical parameters in PCB design, as they determine the current-carrying capacity and the risk of signal interference between adjacent traces. The typical tolerances for trace width and spacing are:
Feature | Nominal Dimension | Tolerance |
---|---|---|
Trace width | 0.1 mm (4 mil) | ±0.02 mm (±0.8 mil) |
Trace spacing | 0.1 mm (4 mil) | ±0.02 mm (±0.8 mil) |
For high-density designs or advanced manufacturing processes, tighter tolerances may be achievable, such as ±0.01 mm (±0.4 mil) for trace width and spacing.
Hole Size and Positioning
Holes in a PCB, such as through-holes for component leads or vias for inter-layer connections, must be precisely sized and positioned to ensure proper fit and connectivity. The typical tolerances for hole size and positioning are:
Feature | Nominal Dimension | Tolerance |
---|---|---|
Hole diameter | 0.5 mm (20 mil) | ±0.05 mm (±2 mil) |
Hole position | – | ±0.1 mm (±4 mil) |
Tighter tolerances, such as ±0.025 mm (±1 mil) for hole diameter and ±0.05 mm (±2 mil) for hole position, may be achievable with advanced manufacturing processes.
Board Dimensions
The overall dimensions of the PCB, including length, width, and thickness, must also be within the specified tolerances to ensure proper fit and compatibility with enclosures or other mating components. The typical tolerances for board dimensions are:
Feature | Nominal Dimension | Tolerance |
---|---|---|
Board length/width | 100 mm (3.94 in) | ±0.2 mm (±0.008 in) |
Board thickness | 1.6 mm (0.063 in) | ±0.1 mm (±0.004 in) |
For smaller or larger boards, the tolerances may need to be adjusted accordingly.
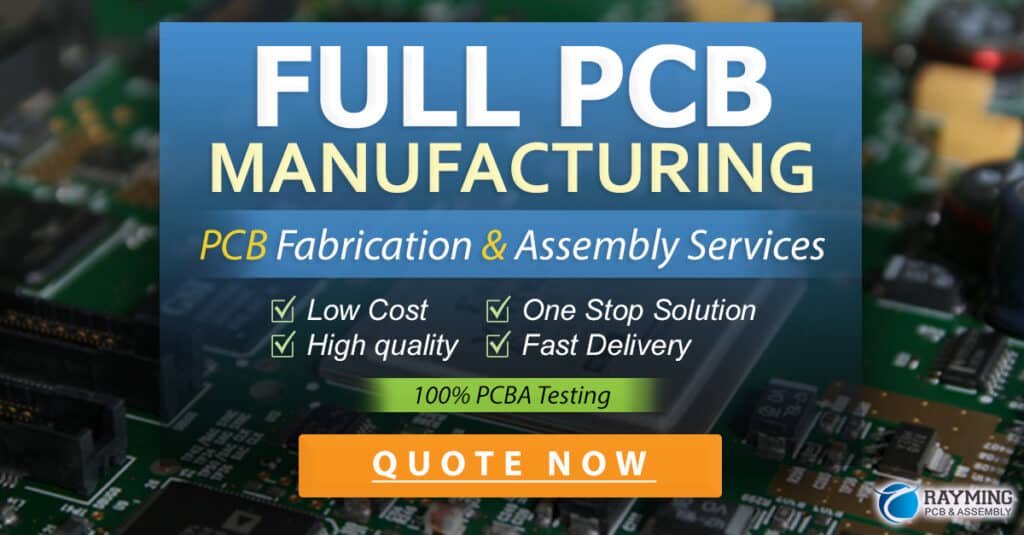
Achieving Tighter Tolerances
In some cases, tighter tolerances than the typical values may be required to meet specific design or performance requirements. Achieving tighter tolerances often involves:
-
Advanced manufacturing processes: Using more precise fabrication techniques, such as laser drilling or high-resolution photolithography, can help achieve tighter tolerances.
-
Higher-quality materials: Using higher-grade substrate materials or copper foils with more consistent properties can reduce variations in the finished PCB.
-
Improved process control: Implementing stricter process controls, such as more frequent inspections or tighter environmental control, can help maintain tighter tolerances throughout the manufacturing process.
-
Design optimization: Designing the PCB with manufacturability in mind, such as avoiding unnecessarily small features or using design rules that are compatible with the chosen manufacturing process, can help achieve tighter tolerances.
However, it is important to note that achieving tighter tolerances often comes with increased manufacturing costs and lead times. Therefore, it is essential to balance the tolerance requirements with the overall project goals and constraints.
FAQ
-
Q: What is the importance of PCB tolerance in the design and manufacturing process?
A: PCB tolerance is crucial in ensuring that the manufactured board meets the desired specifications and functions as intended. It accounts for the inherent variations in the manufacturing process and ensures that the PCB will be compatible with the components and assemblies it interfaces with. -
Q: How do I determine the appropriate tolerances for my PCB design?
A: The appropriate tolerances for a PCB design depend on various factors, such as the manufacturing process, material properties, feature sizes, and board complexity. Consulting with the PCB manufacturer and referring to industry standards and guidelines can help determine the suitable tolerances for a specific design. -
Q: Can I achieve tighter tolerances than the typical values?
A: Yes, achieving tighter tolerances is possible with advanced manufacturing processes, higher-quality materials, improved process control, and design optimization. However, tighter tolerances often come with increased manufacturing costs and lead times, so it is important to balance the tolerance requirements with the overall project goals and constraints. -
Q: What are the consequences of not adhering to the specified PCB tolerances?
A: Not adhering to the specified PCB tolerances can lead to various issues, such as poor component fit, signal integrity problems, reduced reliability, and even complete failure of the PCB. It can also result in increased manufacturing costs and delays due to the need for rework or redesign. -
Q: How can I ensure that my PCB design is within the acceptable tolerances?
A: To ensure that your PCB design is within the acceptable tolerances, follow these steps: - Consult with the PCB manufacturer to understand their capabilities and limitations.
- Use industry-standard design rules and guidelines that are compatible with the chosen manufacturing process.
- Perform design rule checks (DRC) using PCB design software to verify that the design meets the specified tolerances.
- Communicate the tolerance requirements clearly with the manufacturing team and include them in the fabrication files and documentation.
- Consider using more advanced manufacturing processes or higher-quality materials if tighter tolerances are required.
By understanding and adhering to the typical tolerances for PCBs, designers can create more robust and manufacturable designs that meet the desired performance and reliability requirements. Effective communication and collaboration between the design and manufacturing teams are essential to ensure that the PCB tolerances are properly specified, achieved, and verified throughout the product development process.
Leave a Reply