Understanding Thermal Conductivity
Thermal conductivity is a physical property that quantifies a material’s ability to conduct heat. It is defined as the rate at which heat is transferred through a material per unit thickness, per unit area, and per unit temperature difference. The SI unit for thermal conductivity is watts per meter-kelvin (W/mK).
Materials with high thermal conductivity allow heat to flow through them easily, while materials with low thermal conductivity act as thermal insulators. In the context of PCBs, having a substrate material with good thermal conductivity is crucial for efficient heat dissipation.
Factors Affecting Thermal Conductivity of PCBs
Several factors influence the thermal conductivity of PCBs:
1. PCB Substrate Material
The choice of substrate material significantly impacts the thermal conductivity of a PCB. Common PCB substrate materials include:
Material | Thermal Conductivity (W/mK) |
---|---|
FR-4 | 0.25 – 0.35 |
Polyimide | 0.12 – 0.35 |
Aluminum | 205 – 250 |
Copper | 385 – 400 |
Ceramic (Alumina) | 20 – 30 |
Metal Core PCB (MCPCB) | 1 – 8 |
FR-4, a glass-reinforced epoxy laminate, is the most commonly used PCB substrate material due to its good mechanical and electrical properties. However, its thermal conductivity is relatively low compared to metal-based substrates like aluminum or copper.
2. Copper Thickness and Distribution
Copper is an excellent thermal conductor, with a thermal conductivity of around 400 W/mK. The thickness and distribution of copper layers in a PCB can significantly affect its overall thermal performance. Thicker copper layers and more evenly distributed copper planes enhance heat spreading and dissipation.
3. PCB Layer Stack-up
The number and arrangement of layers in a PCB stack-up also influence its thermal behavior. Multi-layer PCBs with dedicated ground and power planes can provide better heat spreading compared to single or double-layer boards. The use of thermal vias, which are copper-filled holes connecting different layers, can further improve heat transfer through the PCB thickness.
4. PCB Surface Finish
The surface finish of a PCB can impact its thermal conductivity to some extent. Some common surface finishes and their thermal conductivities are:
Surface Finish | Thermal Conductivity (W/mK) |
---|---|
Hot Air Solder Leveling (HASL) | 50 – 60 |
Organic Solderability Preservative (OSP) | 0.2 – 0.3 |
Electroless Nickel Immersion Gold (ENIG) | 60 – 90 |
Immersion Silver | 406 – 418 |
While the surface finish contributes to the overall thermal conductivity, its impact is relatively minor compared to the substrate material and copper distribution.
Typical Thermal Conductivity Values for PCBs
The thermal conductivity of a typical FR-4 based PCB ranges from 0.25 to 0.35 W/mK. This relatively low value makes FR-4 PCBs less suitable for applications with high heat dissipation requirements. In such cases, alternative substrate materials or specialized thermal management techniques may be necessary.
Some examples of PCBs with higher thermal conductivity include:
- Metal Core PCBs (MCPCBs): 1 – 8 W/mK
- Aluminum PCBs: 205 – 250 W/mK
- Copper PCBs: 385 – 400 W/mK
These PCBs offer better thermal performance but come with trade-offs such as higher cost, weight, and manufacturing complexity.
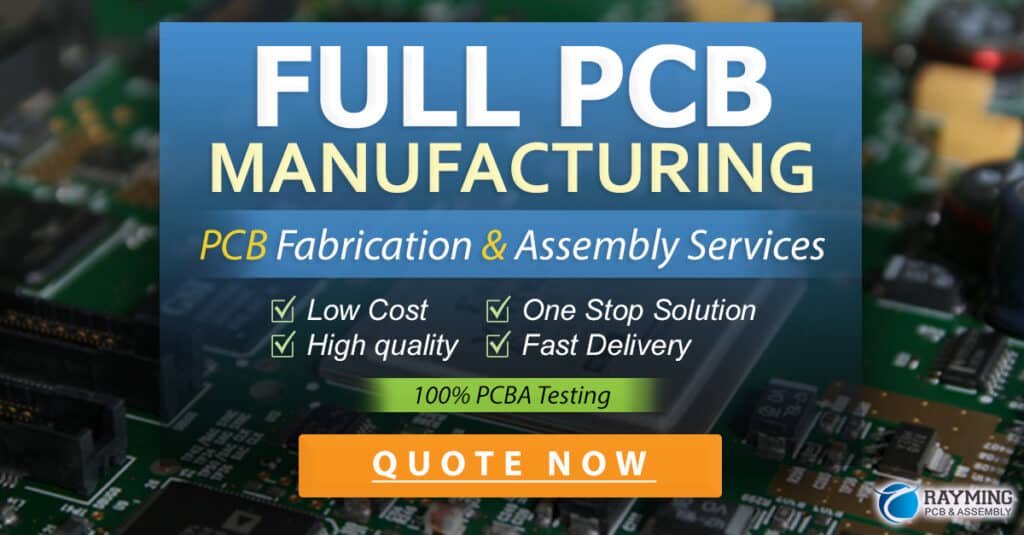
Strategies to Improve Thermal Conductivity of PCBs
There are several strategies to enhance the thermal conductivity and heat dissipation in PCB designs:
1. Use High Thermal Conductivity Substrate Materials
Selecting PCB substrate materials with higher thermal conductivity, such as MCPCBs or ceramic-based substrates, can significantly improve heat dissipation. However, this comes at the cost of increased material and manufacturing expenses.
2. Optimize Copper Distribution and Thickness
Increasing the thickness of copper layers and strategically placing copper planes and traces can enhance heat spreading. Using wider traces for high-current paths and providing sufficient copper coverage on power and ground planes helps in distributing heat more evenly across the PCB.
3. Incorporate Thermal Vias
Thermal vias are copper-filled holes that connect different layers of a PCB, providing a low-resistance path for heat transfer. Placing thermal vias under high-power components and in areas with high heat concentration can greatly improve heat dissipation through the PCB thickness.
4. Use Thermal Interface Materials (TIMs)
Thermal interface materials, such as thermal pads, pastes, or adhesives, can be used to enhance thermal coupling between components and the PCB. These materials fill the air gaps and improve heat transfer from the component package to the PCB substrate.
5. Implement Proper Component Placement and Spacing
Proper component placement and spacing are crucial for optimal thermal management. High-power components should be placed in areas with good airflow and sufficient space for heat dissipation. Placing components too close together can lead to localized hot spots and thermal interaction between components.
6. Consider External Cooling Methods
In some cases, the thermal conductivity of the PCB alone may not be sufficient to dissipate the generated heat. External cooling methods, such as heatsinks, fans, or liquid cooling systems, can be employed to enhance heat dissipation. These methods work in conjunction with the PCB’s thermal conductivity to provide effective thermal management.
Measuring Thermal Conductivity of PCBs
Measuring the thermal conductivity of PCBs is essential for validating thermal designs and ensuring proper heat dissipation. Several methods can be used to measure thermal conductivity:
- Guarded Hot Plate Method
- Heat Flow Meter Method
- Laser Flash Method
- Transient Plane Source (TPS) Method
These methods involve applying a known heat flux to the PCB sample and measuring the resulting temperature gradient. The thermal conductivity can then be calculated using the Fourier’s law of heat conduction.
Conclusion
The thermal conductivity of PCBs plays a crucial role in the thermal management of electronic devices. Typical FR-4 based PCBs have a relatively low thermal conductivity, ranging from 0.25 to 0.35 W/mK. However, by understanding the factors affecting thermal conductivity and employing appropriate design strategies, engineers can optimize heat dissipation in PCB designs.
Selecting high thermal conductivity substrate materials, optimizing copper distribution and thickness, incorporating thermal vias, using thermal interface materials, and implementing proper component placement and spacing are some of the key strategies to enhance the thermal performance of PCBs.
As electronic devices continue to shrink in size and increase in power density, the importance of effective thermal management in PCB designs will only grow. By carefully considering the thermal conductivity of PCBs and adopting appropriate thermal design practices, engineers can ensure reliable and efficient operation of electronic systems.
Frequently Asked Questions (FAQ)
1. What is the thermal conductivity of a typical FR-4 PCB?
The thermal conductivity of a typical FR-4 based PCB ranges from 0.25 to 0.35 W/mK.
2. How does the choice of substrate material affect the thermal conductivity of a PCB?
The choice of substrate material significantly impacts the thermal conductivity of a PCB. Materials like aluminum and copper have much higher thermal conductivity compared to FR-4, allowing for better heat dissipation.
3. What are thermal vias, and how do they improve heat dissipation in PCBs?
Thermal vias are copper-filled holes that connect different layers of a PCB, providing a low-resistance path for heat transfer. They help in transferring heat through the PCB thickness and improve overall heat dissipation.
4. How can component placement and spacing influence the thermal performance of a PCB?
Proper component placement and spacing are crucial for optimal thermal management. High-power components should be placed in areas with good airflow and sufficient space to avoid localized hot spots and thermal interaction between components.
5. When should external cooling methods be considered for PCB thermal management?
External cooling methods, such as heatsinks, fans, or liquid cooling systems, should be considered when the thermal conductivity of the PCB alone is not sufficient to dissipate the generated heat. These methods work in conjunction with the PCB’s thermal conductivity to provide effective thermal management.
Leave a Reply