Types of PCB Surface Finishes
There are several types of PCB surface finishes available, each with its own advantages and disadvantages. The most common surface finishes include:
1. Hot Air Solder Leveling (HASL)
HASL is one of the most widely used surface finishes in the PCB industry. The process involves dipping the PCB into a molten solder bath and then using hot air to level the solder on the surface. The resulting finish is a thin, uniform layer of solder that protects the copper and provides excellent solderability.
Advantages:
– Cost-effective
– Excellent solderability
– Good shelf life
– Suitable for through-hole and surface mount components
Disadvantages:
– Uneven surface due to solder dipping process
– Potential for thermal shock to the PCB
– Not suitable for fine-pitch components
– Contains lead (Pb), which is subject to environmental regulations
2. Organic Solderability Preservative (OSP)
OSP is a chemical coating that is applied to the copper surface of the PCB to protect it from oxidation. The coating is transparent and does not affect the electrical properties of the copper. OSP is an environmentally friendly alternative to HASL, as it does not contain lead.
Advantages:
– Cost-effective
– Environmentally friendly (lead-free)
– Flat and uniform surface
– Suitable for fine-pitch components
Disadvantages:
– Limited shelf life (6-12 months)
– Requires proper handling and storage to maintain solderability
– Not suitable for multiple reflow cycles
– Can be difficult to inspect visually
3. Electroless Nickel Immersion Gold (ENIG)
ENIG is a two-layer surface finish that consists of an electroless nickel layer followed by a thin immersion gold layer. The nickel layer provides a barrier between the copper and the gold, while the gold layer protects the nickel from oxidation and provides excellent solderability.
Advantages:
– Excellent solderability
– Long shelf life
– Flat and uniform surface
– Suitable for fine-pitch components
– Good thermal and electrical conductivity
Disadvantages:
– Higher cost compared to HASL and OSP
– Potential for “black pad” issue due to improper plating process
– Gold can dissolve into solder during reflow, affecting joint reliability
4. Immersion Silver (IAg)
Immersion silver is a single-layer surface finish that involves depositing a thin layer of silver onto the copper surface of the PCB. The silver layer protects the copper from oxidation and provides good solderability.
Advantages:
– Cost-effective
– Excellent solderability
– Flat and uniform surface
– Suitable for fine-pitch components
– Environmentally friendly (lead-free)
Disadvantages:
– Limited shelf life (6-12 months)
– Potential for silver migration, which can cause short circuits
– Not suitable for high-temperature applications
– Can tarnish over time
5. Immersion Tin (ISn)
Immersion tin is another single-layer surface finish that involves depositing a thin layer of tin onto the copper surface of the PCB. The tin layer protects the copper from oxidation and provides good solderability.
Advantages:
– Cost-effective
– Good solderability
– Flat and uniform surface
– Suitable for fine-pitch components
– Environmentally friendly (lead-free)
Disadvantages:
– Limited shelf life (6-12 months)
– Potential for tin whiskers, which can cause short circuits
– Not suitable for high-temperature applications
– Can be difficult to inspect visually
Comparison of PCB Surface Finishes
The following table compares the key characteristics of the five main PCB surface finishes:
Surface Finish | Cost | Shelf Life | Solderability | Fine-Pitch Compatibility | Environmental Impact |
---|---|---|---|---|---|
HASL | Low | Good | Excellent | Limited | Contains lead (Pb) |
OSP | Low | Limited | Good | Suitable | Lead-free |
ENIG | High | Excellent | Excellent | Suitable | Lead-free |
Immersion Silver | Moderate | Limited | Excellent | Suitable | Lead-free |
Immersion Tin | Moderate | Limited | Good | Suitable | Lead-free |
Factors to Consider When Choosing a PCB Surface Finish
When selecting a surface finish for your PCB, consider the following factors:
- Application requirements
- Operating environment (temperature, humidity, etc.)
- Expected lifespan of the device
-
Electrical and thermal conductivity needs
-
Component compatibility
- Fine-pitch components
- Through-hole or surface mount components
-
Multiple reflow cycles
-
Manufacturing process
- Soldering method (wave, reflow, hand soldering)
-
Compatibility with other processes (e.g., conformal coating)
-
Cost and budget constraints
- Initial cost of the surface finish
-
Long-term cost implications (rework, reliability issues)
-
Environmental regulations
- Lead-free requirements
- Recyclability and disposal considerations
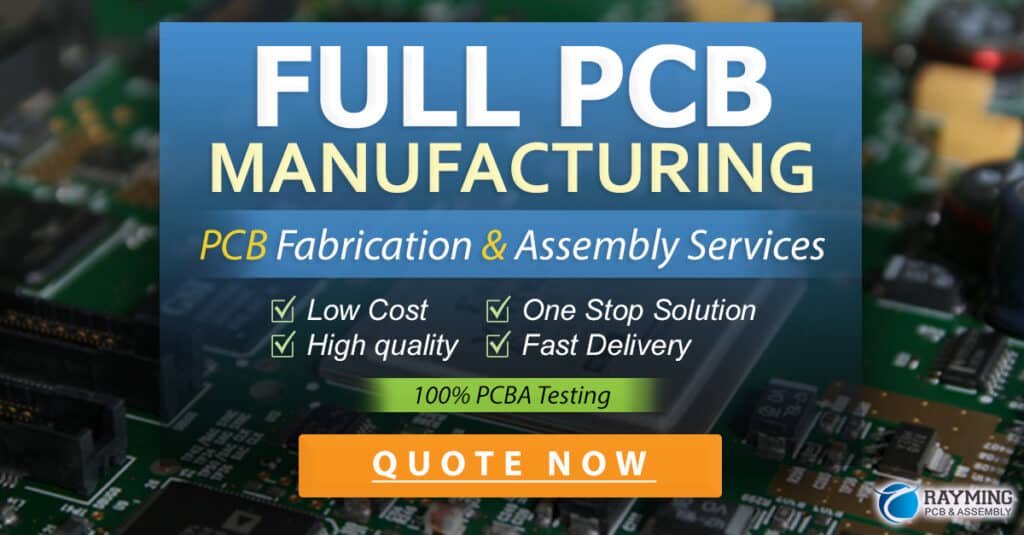
PCB Surface Finish Selection Guide
To help you choose the most suitable surface finish for your PCB, follow this step-by-step guide:
- Determine the application requirements
- Identify the operating environment and expected lifespan of the device
-
Consider the electrical and thermal conductivity needs
-
Evaluate component compatibility
- Check if the PCB will use fine-pitch components
- Determine if the components are through-hole or surface mount
-
Consider if the PCB will undergo multiple reflow cycles
-
Assess manufacturing process compatibility
- Identify the soldering method (wave, reflow, hand soldering)
-
Check compatibility with other processes (e.g., conformal coating)
-
Consider cost and budget constraints
- Compare the initial cost of different surface finishes
-
Evaluate potential long-term cost implications (rework, reliability issues)
-
Ensure compliance with environmental regulations
- Check if the application requires lead-free surface finishes
-
Consider recyclability and disposal requirements
-
Consult with your PCB manufacturer
- Discuss your specific requirements with your PCB manufacturer
- Ask for their recommendation based on their experience and expertise
By following this guide and carefully considering each factor, you can select the most appropriate surface finish for your PCB, ensuring optimal performance, reliability, and cost-effectiveness.
FAQ
-
Q: What is the most cost-effective PCB surface finish?
A: HASL and OSP are generally the most cost-effective PCB surface finishes. However, HASL contains lead, which may be subject to environmental regulations. -
Q: Which surface finish is best for fine-pitch components?
A: ENIG, immersion silver, and immersion tin are all suitable for fine-pitch components due to their flat and uniform surface. -
Q: How long do PCB surface finishes typically last?
A: The shelf life of PCB surface finishes varies. HASL and ENIG have a good shelf life, while OSP, immersion silver, and immersion tin have a limited shelf life of 6-12 months. -
Q: Are all PCB surface finishes environmentally friendly?
A: OSP, ENIG, immersion silver, and immersion tin are considered environmentally friendly, as they are lead-free. HASL contains lead, which is subject to environmental regulations. -
Q: Can the choice of surface finish affect the reliability of solder joints?
A: Yes, the choice of surface finish can affect solder joint reliability. For example, gold in ENIG can dissolve into the solder during reflow, potentially affecting joint reliability. Proper process control and selection of compatible materials are essential to ensure reliable solder joints.
Leave a Reply