Introduction to PCB Routing
Printed Circuit Board (PCB) routing is the process of creating the conductive traces that electrically connect the various components on a PCB. Proper PCB routing is critical for ensuring the reliability, performance, and manufacturability of the final board.
There are many factors that go into successful PCB routing, including choosing the right trace widths and clearances, avoiding electromagnetic interference, minimizing crosstalk, and adhering to various design rules and constraints. In this article, we’ll take an in-depth look at the key routing rules and best practices for PCB design.
The Importance of PCB Routing Rules
Following proper PCB routing rules is essential for several reasons:
-
Reliability: Well-routed traces with appropriate widths and spacings are less likely to fail due to manufacturing defects, thermal stress, or mechanical stress.
-
Signal Integrity: Proper routing helps maintain signal integrity by minimizing crosstalk, reflections, and electromagnetic interference (EMI).
-
Manufacturability: Following routing rules ensures that the PCB can be manufactured reliably and cost-effectively by pcb fabricators.
-
Compliance: Many industries have specific standards and regulations for PCB design, such as the IPC standards. Adhering to routing rules helps ensure compliance with these requirements.
Basic PCB Routing Rules
Here are some of the fundamental rules to follow when routing a PCB:
Trace Width
The width of a trace determines its current-carrying capacity and resistance. Wider traces can carry more current and have lower resistance, but they also take up more space on the board. The appropriate trace width depends on several factors, including:
- The amount of current the trace needs to carry
- The desired voltage drop across the trace
- The available space on the board
- The copper thickness (weight) of the PCB
As a general rule, you can use the following table as a starting point for determining trace widths based on current requirements:
Current (A) | Trace Width (mm) |
---|---|
0.5 | 0.2 |
1 | 0.3 |
2 | 0.4 |
3 | 0.6 |
4 | 0.8 |
5 | 1.0 |
However, it’s important to use a trace width calculator or consult with your PCB fabricator to determine the optimal trace widths for your specific design.
Clearance
Clearance refers to the minimum distance between two conductive features on a PCB, such as traces, pads, or vias. Adequate clearance is necessary to prevent short circuits and ensure reliable manufacturing.
The minimum clearance depends on several factors, including:
- The voltage difference between the two features
- The PCB material and thickness
- The PCB fabrication process and capabilities
As a general rule, a clearance of 0.2 mm (8 mil) is a good starting point for most designs. However, higher voltage differences or finer pitch components may require greater clearances.
Via Size and Spacing
Vias are conductive holes that allow traces to pass from one layer of the PCB to another. The size and spacing of vias are important considerations in PCB routing.
The diameter of a via should be large enough to allow reliable plating of the hole wall, but small enough to minimize the space occupied on the board. A typical via diameter is 0.4 mm (16 mil), but smaller or larger diameters may be used depending on the design requirements.
The spacing between vias should be sufficient to prevent shorts and ensure reliable manufacturing. A minimum via-to-via spacing of 0.6 mm (24 mil) is a common starting point.
Trace Routing Angles
When routing traces, it’s generally best to use 45-degree angles rather than 90-degree angles. 90-degree angles can create reflections and impedance discontinuities that degrade signal integrity, especially at high frequencies.
However, 45-degree routing may not always be possible due to space constraints or other design requirements. In such cases, using curved traces or adding teardrops at the corners can help minimize the impact of 90-degree angles.
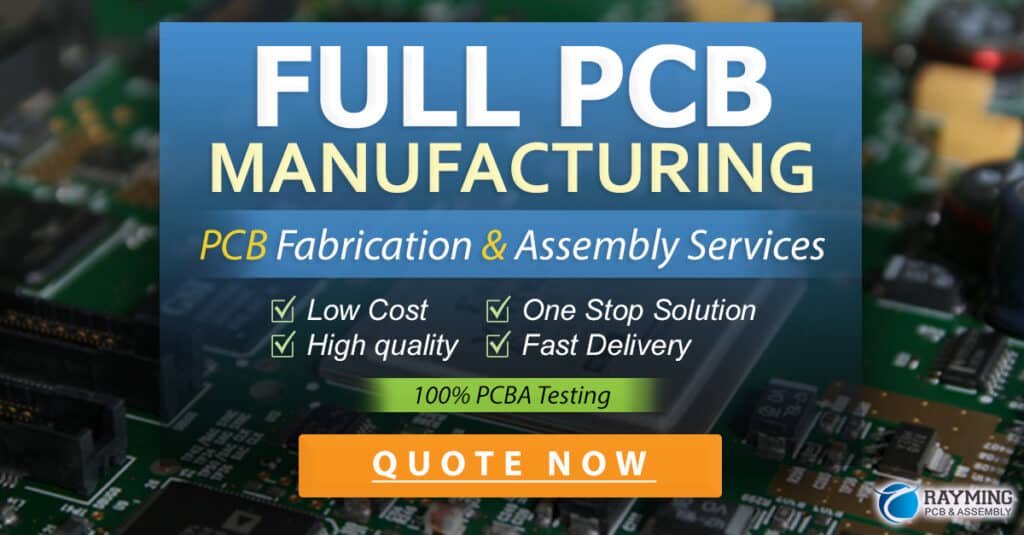
Advanced PCB Routing Considerations
In addition to the basic rules, there are several advanced factors to consider when routing a PCB:
Differential Pairs
Differential signaling uses two traces carrying complementary signals to reduce noise and improve signal integrity. When routing differential pairs, it’s important to maintain a constant spacing between the traces to ensure a consistent impedance along the length of the pair.
The optimal spacing between differential traces depends on the desired impedance and the PCB material properties. Common differential pair spacings range from 0.1 mm to 0.3 mm (4 to 12 mil).
Length Matching
In some cases, it’s necessary to match the lengths of certain traces to ensure synchronous arrival of signals at their destinations. This is particularly important for high-speed interfaces like DDR memory or PCI Express.
Length matching can be achieved by adding serpentine or trombone structures to the shorter traces to equalize their lengths with the longer traces. The maximum allowable length difference (skew) depends on the specific interface requirements, but a common target is 100 ps or less.
Crosstalk
Crosstalk occurs when signals on adjacent traces interfere with each other due to electromagnetic coupling. To minimize crosstalk, you can:
- Increase the spacing between sensitive traces
- Use guard traces or ground planes to shield sensitive signals
- Route sensitive traces perpendicular to each other on adjacent layers
- Use differential signaling for high-speed interfaces
EMI and EMC
Electromagnetic interference (EMI) and electromagnetic compatibility (EMC) are important considerations in PCB routing, particularly for designs that must comply with regulatory standards like FCC Part 15.
To minimize EMI and ensure EMC compliance, you can:
- Use proper grounding and shielding techniques
- Avoid creating unintentional antennas with long, unterminated traces
- Use bypass and decoupling capacitors to reduce high-frequency noise
- Follow recommended layout practices for switch-mode power supplies and other noise-sensitive circuits
PCB Routing Tools and Techniques
Modern PCB design software includes a variety of tools and features to help with routing, such as:
- Auto-routers that can automatically route traces based on design rules and constraints
- Interactive routing tools that allow manual routing with real-time design rule checking (DRC)
- High-speed design tools that can analyze signal integrity, impedance, and crosstalk
- 3D visualization tools that can help identify clearance issues and mechanical conflicts
However, it’s important to remember that auto-routers and other automated tools are not a substitute for good design practices and engineering judgment. Manual routing and careful review of the design are still necessary to ensure optimal results.
Frequently Asked Questions (FAQ)
1. What is the difference between a trace and a via?
A trace is a conductive path that carries signals or power between components on the same layer of a PCB. A via is a conductive hole that allows traces to pass between different layers of the PCB.
2. How do I determine the right trace width for my design?
The appropriate trace width depends on factors like the current requirements, desired voltage drop, available board space, and PCB copper thickness. You can use a trace width calculator or consult with your PCB fabricator to determine the optimal widths for your specific design.
3. What is the minimum clearance between traces?
The minimum clearance between traces depends on factors like the voltage difference, PCB material, and fabrication process. A common starting point is 0.2 mm (8 mil), but higher voltage differences or finer pitch components may require greater clearances.
4. Why is it important to use 45-degree angles when routing traces?
45-degree angles help minimize reflections and impedance discontinuities that can degrade signal integrity, especially at high frequencies. 90-degree angles should be avoided when possible, or mitigated with curved traces or teardrops.
5. What is the purpose of length matching in PCB routing?
Length matching ensures that signals arriving at their destinations synchronously, which is particularly important for high-speed interfaces like DDR memory or PCI Express. Matching trace lengths within a specified tolerance (e.g. 100 ps) helps maintain signal integrity and prevent timing errors.
Conclusion
PCB routing is a critical aspect of PCB design that directly impacts the reliability, performance, and manufacturability of the final product. By following the basic routing rules and considering advanced factors like differential pairs, length matching, crosstalk, and EMI/EMC, designers can create high-quality PCBs that meet their functional and regulatory requirements.
While modern PCB design software provides powerful tools to automate and optimize routing, it’s important to remember that good design practices and engineering judgment are still essential for successful PCB routing. By understanding the underlying principles and trade-offs involved in routing, designers can make informed decisions and achieve the best possible results for their projects.
Leave a Reply