Introduction to Purple PCBs
Purple PCBs, also known as purple printed circuit boards, are a unique and visually striking variation of the standard green pcbs commonly used in electronic devices. These boards feature a distinctive purple solder mask, which sets them apart from other PCB colors. In recent years, purple PCBs have gained popularity among electronics enthusiasts, designers, and manufacturers due to their aesthetic appeal and potential benefits.
What is a PCB?
Before diving into the specifics of purple PCBs, let’s briefly discuss what a PCB is. A printed circuit board (PCB) is a flat board made of insulating material, such as fiberglass or composite epoxy, that supports and connects electronic components using conductive tracks, pads, and other features etched from copper sheets laminated onto the board. PCBs are essential in almost all electronic devices, from smartphones and computers to industrial equipment and medical devices.
The Role of Solder Mask in PCBs
Solder mask, also known as solder resist or solder stop, is a thin layer of polymer applied to the surface of a PCB. Its primary purpose is to protect the copper traces and pads from oxidation, prevent solder bridges from forming between closely spaced pads, and provide electrical insulation. Additionally, solder mask improves the durability and reliability of the PCB by protecting it from dust, moisture, and other environmental factors.
Solder mask is typically applied using screen printing or liquid photo imaging techniques. The most common solder mask color is green, but other colors, such as red, blue, yellow, black, white, and purple, are also available.
The Significance of Purple PCBs
Aesthetic Appeal
One of the main reasons for the growing popularity of purple PCBs is their unique and eye-catching appearance. The purple color adds a touch of sophistication and creativity to electronic devices, making them stand out from the sea of green PCBs. This aesthetic appeal is particularly valuable for consumer electronics, where product differentiation and visual identity are crucial factors in attracting customers.
Improved Visibility
Another benefit of purple PCBs is enhanced visibility during the assembly process. The high contrast between the purple solder mask and the white silkscreen makes it easier for technicians to read component designators, orientation marks, and other important information printed on the board. This improved visibility can lead to fewer assembly errors, increased production efficiency, and better overall quality control.
Potential for Better Performance
Some manufacturers claim that purple PCBs offer better performance compared to traditional green PCBs. The argument is that the purple solder mask may have superior electrical insulation properties, leading to reduced signal interference and improved signal integrity. However, it is important to note that these claims are not universally accepted, and the actual performance differences between purple and green PCBs may be minimal or dependent on the specific solder mask material used.
Manufacturing Process of Purple PCBs
The manufacturing process for purple PCBs is similar to that of other PCB colors. The main difference lies in the selection of the solder mask material and the application of the purple pigment.
PCB Fabrication Steps
- Design: The PCB layout is designed using specialized software, such as Altium Designer, Eagle, or KiCad.
- Printing: The design is printed onto a transparent film, which will be used to create the photoresist mask.
- Etching: The copper-clad board is coated with a light-sensitive photoresist, exposed to UV light through the transparent film, and then etched to remove the unwanted copper, leaving only the desired traces and pads.
- Drilling: Holes are drilled into the board for component leads and vias.
- Solder Mask Application: The purple solder mask is applied to the board using screen printing or liquid photo imaging techniques.
- Silkscreen Printing: The white silkscreen, containing component designators and other information, is printed onto the solder mask.
- Surface Finish: A surface finish, such as HASL (Hot Air Solder Leveling), ENIG (Electroless Nickel Immersion Gold), or OSP (Organic Solderability Preservative), is applied to the exposed copper to prevent oxidation and improve solderability.
Choosing the Right Solder Mask Material
To achieve the desired purple color, PCB manufacturers must select a suitable solder mask material that can be pigmented with purple dye. The most common solder mask materials used for purple PCBs are:
-
Liquid Photoimageable Solder Mask (LPI): LPI is a high-performance, photopolymer-based solder mask that offers excellent resolution, adhesion, and resistance to chemicals and heat. LPI is the preferred choice for high-density PCBs and fine-pitch components.
-
Dry Film Solder Mask: Dry film solder mask is a solid photoresist film that is laminated onto the PCB surface. While it offers good resolution and adhesion, it may not be as durable as LPI and is more suitable for lower-density PCBs.
When selecting a solder mask material, manufacturers must ensure that the purple pigment is compatible with the chosen material and does not compromise its performance or reliability.
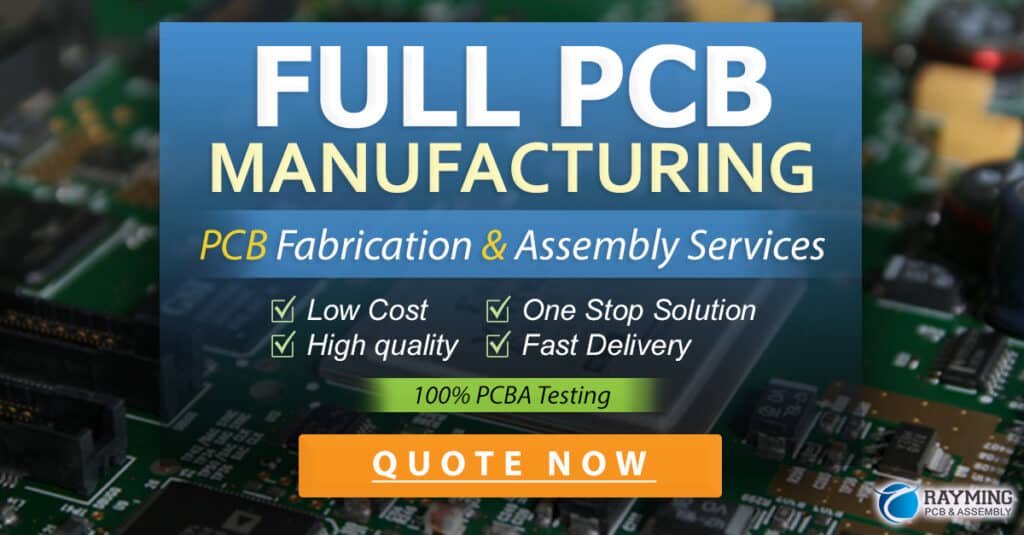
Applications of Purple PCBs
Purple PCBs can be used in a wide range of electronic devices and applications, just like their green counterparts. Some common applications include:
- Consumer Electronics: Smartphones, tablets, laptops, gaming consoles, and wearables.
- Industrial Electronics: Control systems, sensors, automation equipment, and power supplies.
- Medical Devices: Diagnostic equipment, monitoring systems, and implantable devices.
- Automotive Electronics: Infotainment systems, engine control units, and advanced driver assistance systems (ADAS).
- Aerospace and Defense: Avionics, communication systems, and military equipment.
Comparison with Other PCB Colors
While purple PCBs have gained popularity in recent years, they are not the only alternative to the traditional green PCB. Other common PCB colors include:
Red PCBs
Red PCBs are often used in high-speed, high-frequency applications, such as radio frequency (RF) and microwave circuits. The red solder mask is believed to have better dielectric properties, which can help minimize signal losses and improve overall performance.
Blue PCBs
Blue PCBs are another popular choice for their aesthetic appeal and potential performance benefits. Like purple PCBs, blue boards offer high contrast against the white silkscreen, improving visibility during assembly. Some manufacturers also claim that blue solder mask has better thermal dissipation properties, which can help prevent overheating in high-power applications.
Black PCBs
Black PCBs are often used in high-end consumer electronics and luxury products for their sleek and sophisticated appearance. They can also provide better contrast for white silkscreen printing, making them easier to read and assemble. However, black solder mask may have lower UV resistance compared to other colors, which can lead to degradation over time if exposed to direct sunlight.
white pcbs
White PCBs are less common but offer a unique and clean look. They are sometimes used in LED lighting applications, as the white solder mask can help reflect light and improve overall efficiency. However, white PCBs may be more susceptible to visible contamination and require more careful handling during assembly.
Frequently Asked Questions
Q1: Are purple PCBs more expensive than green PCBs?
A1: Yes, purple PCBs may be slightly more expensive than green PCBs due to the specialized solder mask material and pigment required. However, the price difference is usually minimal and may be worth it for the aesthetic appeal and potential benefits.
Q2: Can purple PCBs be used for all types of electronic devices?
A2: Yes, purple PCBs can be used in virtually any electronic device, just like green PCBs. The choice of PCB color is primarily driven by aesthetic preferences and potential performance benefits, rather than specific applications.
Q3: Do purple PCBs require special handling or assembly techniques?
A3: No, purple PCBs can be handled and assembled using the same techniques and equipment as green PCBs. The improved visibility of the white silkscreen on the purple background may even make the assembly process easier and more efficient.
Q4: Are there any disadvantages to using purple PCBs?
A4: The main disadvantage of purple PCBs is the slightly higher cost compared to green PCBs. Additionally, some manufacturers may not offer purple as a standard color option, which could lead to longer lead times or minimum order quantities.
Q5: How can I order custom purple PCBs for my project?
A5: To order custom purple PCBs, you can contact a PCB manufacturer that offers purple as a solder mask color option. Provide them with your PCB design files, specify the desired quantity, and request a quote. Many manufacturers also offer online ordering platforms, where you can upload your design files, select the purple color option, and receive an instant quote.
Conclusion
Purple PCBs are a unique and visually appealing alternative to the traditional green PCBs. They offer aesthetic benefits, improved visibility during assembly, and potential performance advantages. While they may be slightly more expensive than green PCBs, the cost difference is often minimal and may be justified by the benefits they provide.
As the demand for product differentiation and innovative design grows, purple PCBs are likely to become increasingly popular among electronics enthusiasts, designers, and manufacturers. Whether you are developing a consumer electronic device, industrial equipment, or a medical instrument, purple PCBs can help your product stand out from the competition and deliver the performance and reliability your customers expect.
PCB Color | Advantages | Disadvantages |
---|---|---|
Green | – Standard color, widely available | – Limited visual appeal |
– Cost-effective | ||
Purple | – Unique aesthetic appeal | – Slightly more expensive than green PCBs |
– Improved visibility during assembly | – May not be offered by all manufacturers | |
– Potential performance benefits | ||
Red | – Potential performance benefits for high-speed applications | – Limited availability compared to green PCBs |
– May require specialized solder mask material | ||
Blue | – Aesthetic appeal | – Potential higher cost than green PCBs |
– Improved visibility during assembly | – May not be offered by all manufacturers | |
– Potential thermal dissipation benefits | ||
Black | – Sleek and sophisticated appearance | – Lower UV resistance compared to other colors |
– High contrast for white silkscreen printing | – May require specialized handling during assembly | |
White | – Unique and clean appearance | – More susceptible to visible contamination |
– Potential benefits for LED lighting applications | – May require more careful handling during assembly |
In conclusion, purple PCBs offer a compelling combination of aesthetic appeal, improved visibility, and potential performance benefits. As the electronics industry continues to evolve and innovate, purple PCBs are poised to play an increasingly important role in the development of cutting-edge products and technologies.
Leave a Reply