Introduction to Production Holes
In the oil and gas industry, a production hole refers to the wellbore drilled into a reservoir formation to extract hydrocarbons such as crude oil and natural gas. The diameter of this hole is a critical parameter that impacts the well’s productivity, completion design, and overall economics.
Significance of Production Hole Diameter
The production hole diameter plays a vital role in determining:
– Flow rates of oil and gas
– Tubing and casing sizes
– Completion equipment dimensions
– Stimulation treatments
– Artificial lift methods
Selecting the optimum production hole size involves considering various factors such as reservoir properties, expected flow rates, completion requirements, and economic constraints. A well-designed production hole diameter can maximize hydrocarbon recovery while minimizing costs.
Factors Influencing Production Hole Diameter Selection
Reservoir Properties
The characteristics of the reservoir rock and fluids significantly influence the choice of production hole diameter:
Property | Impact on Hole Size |
---|---|
Permeability | Higher permeability may allow smaller hole sizes |
Porosity | Higher porosity may require larger hole sizes for stability |
Fluid viscosity | Higher viscosity may necessitate larger hole sizes for flow |
Gas-oil ratio | Higher GOR may demand larger hole sizes to accommodate gas flow |
Understanding these properties through logs, core analysis, and well testing helps engineers optimize the production hole diameter for the specific reservoir conditions.
Expected Flow Rates
The anticipated production rates of oil, gas, and water are key drivers for selecting an appropriate hole size. Higher expected flow rates generally require larger diameters to:
– Minimize friction pressure losses
– Avoid velocity-induced erosion of tubulars
– Accommodate future production growth
Nodal analysis is often used to model the well’s inflow and outflow performance and determine the optimal production hole size that balances productivity and economics.
Completion Design Considerations
The planned completion type and equipment also dictate the suitable production hole diameter:
Completion Type | Hole Size Requirements |
---|---|
Open hole | Sized to accommodate max. reservoir contact |
Cased hole | Sized to fit casing, tubing, and downhole equipment |
Gravel pack | Sized to allow space for gravel and screen |
Fracturing | Sized to fit frac string and handle proppant flowback |
The production hole must provide sufficient clearance for running and cementing casing, installing downhole equipment, and performing necessary completion operations without compromising the well’s integrity.
Economic Considerations
Drilling larger diameter production holes typically incurs higher costs due to increased:
– Rig time
– Fluid volumes
– Casing and tubing sizes
– Cementing and completion expenses
However, the long-term benefits of improved well productivity and recovery may justify the initial investment. Economic analysis, such as net present value (NPV) calculations, helps operators make informed decisions on production hole sizing based on their financial objectives and risk tolerance.
Common Production Hole Sizes
The following table lists some commonly used production hole diameters in the oil and gas industry:
Hole Size (inches) | Typical Application |
---|---|
6 1/8 | Slim hole or monobore designs |
8 1/2 | Conventional onshore vertical wells |
12 1/4 | Large bore or extended reach wells |
17 1/2 | Deepwater or high-rate gas wells |
These sizes are not exhaustive and may vary based on regional practices, specific field requirements, and evolving technologies. Operators often standardize their hole sizes to optimize procurement, inventory management, and operational efficiency.
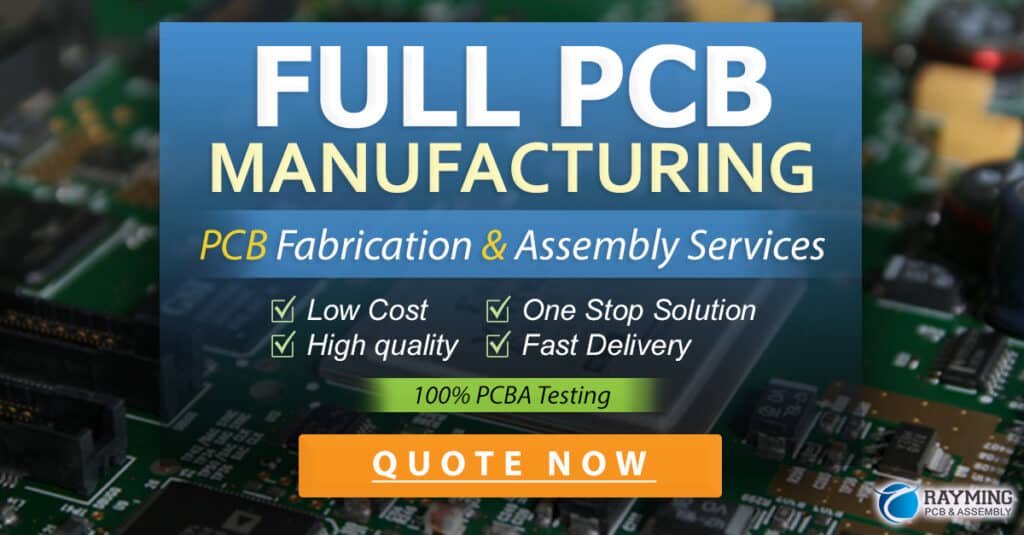
Hole Enlargement Techniques
In some cases, the initially drilled production hole may not be adequately sized for the desired completion or production objectives. Hole enlargement techniques can be employed to increase the diameter of the wellbore:
Underreaming
Underreaming involves using an expandable cutting tool to enlarge the hole diameter below a restriction, such as a casing shoe or a problematic formation. The underreamer is run in the hole in a collapsed state and then expanded to the desired diameter once it passes the restriction.
Hole Opening
Hole opening refers to the process of re-drilling a previously drilled section of the wellbore to a larger diameter. This is typically done using a hole opener, which is a specialized drill bit with expandable cutter arms that can enlarge the hole while drilling ahead.
These techniques allow operators to optimize the production hole diameter in specific sections of the well without incurring the cost and time of drilling a larger hole from surface.
Production Hole Challenges and Mitigation Strategies
Drilling and maintaining a stable production hole can be challenging due to various geological and operational factors:
Wellbore Instability
Unstable formations, such as shales or fractured zones, can cause the production hole to collapse or cave in, leading to stuck pipe, lost circulation, and reduced well productivity. Mitigation strategies include:
– Using appropriate mud weight and chemistry to balance formation pressures
– Running casing or liner to isolate problematic zones
– Employing wellbore strengthening techniques, such as fracture gradient enhancement
Differential Sticking
Differential sticking occurs when the drill string or casing becomes stuck against a permeable formation due to the pressure differential between the wellbore and the formation. This can be mitigated by:
– Maintaining a low-overbalance drilling mud weight
– Using lubricants and additives to reduce friction
– Minimizing static time and ensuring continuous pipe movement
Lost Circulation
Lost circulation happens when the drilling fluid escapes into the formation instead of returning to the surface, leading to wellbore instability and potential well control issues. Lost circulation can be managed by:
– Identifying and characterizing loss zones through logging and drilling data analysis
– Using lost circulation materials (LCMs) to plug and seal the loss zones
– Implementing managed pressure drilling (MPD) techniques to precisely control the wellbore pressure profile
Hole Cleaning
Ineffective hole cleaning can lead to the accumulation of drill cuttings and debris in the production hole, causing stuck pipe, reduced rate of penetration, and poor cement jobs. Hole cleaning can be optimized by:
– Maintaining adequate flow rates and annular velocities
– Using high-performance drilling fluids with good suspension and transport properties
– Employing wiper trips and backreaming to remove cuttings beds
Regularly monitoring and mitigating these challenges is essential to ensure a clean, stable, and productive production hole that meets the well’s objectives.
Future Trends in Production Hole Optimization
As the oil and gas industry continues to evolve, new technologies and approaches are emerging to optimize production hole design and performance:
Digitalization and Data Analytics
The increasing availability of real-time data from drilling and completion operations, along with advancements in data analytics and machine learning, enables operators to make data-driven decisions on production hole sizing. Predictive models can be developed to optimize hole diameter based on historical well performance, reservoir characteristics, and economic parameters.
Expandable Tubular Technology
Expandable tubulars, such as expandable casing and liners, allow operators to maintain a larger production hole diameter while still being able to run completions through smaller restrictions. This technology can reduce the need for hole enlargement operations and enable slimmer well designs that save on material and operational costs.
Multilateral and Smart Completions
Multilateral wells, which have multiple branches drilled from a single main wellbore, can maximize reservoir contact and drainage efficiency without requiring large diameter production holes. Smart completions, which incorporate downhole sensors and flow control devices, can optimize production from different zones and manage well performance without the need for intervention or hole size changes.
Sustainable Drilling Practices
With increasing focus on environmental sustainability, operators are exploring ways to minimize the environmental footprint of drilling operations. This includes using more efficient and low-emission rigs, optimizing mud systems to reduce waste, and employing casing while drilling (CWD) techniques to eliminate the need for multiple hole sizes and casing strings.
As these trends continue to shape the future of production hole design, operators who stay at the forefront of technology and adopt innovative approaches will be better positioned to optimize their well performance and maximize their returns on investment.
Frequently Asked Questions (FAQs)
- What is the difference between a production hole and a pilot hole?
A pilot hole is a small-diameter hole drilled ahead of the main production hole to gather geological and drilling data, such as formation pressures, pore pressure gradients, and rock properties. The information from the pilot hole is used to optimize the design of the subsequent production hole. In contrast, the production hole is the final wellbore drilled to the target depth and sized to accommodate the planned completion and production operations.
- How does the production hole diameter affect the well’s productivity?
The production hole diameter impacts the well’s productivity in several ways:
– A larger diameter allows for higher flow rates by reducing friction pressure losses and increasing the cross-sectional area for fluid flow.
– A larger diameter provides more space for running completion equipment, such as tubing, packers, and downhole sensors, which can optimize well performance.
– A larger diameter may enable better reservoir contact and drainage, especially in horizontal or multilateral wells.
However, the benefits of a larger production hole must be balanced against the increased drilling and completion costs and the potential for wellbore stability issues.
- What is the relationship between production hole diameter and casing size?
The production hole diameter dictates the maximum size of the casing that can be run in the well. The casing outer diameter (OD) must be smaller than the production hole diameter to allow for sufficient clearance for running the casing, centralizing it, and achieving a good cement job. Typically, the production casing is sized to provide a 1-2 inch annular space between the casing OD and the hole diameter, depending on the well depth, formation characteristics, and cementing requirements.
- Can the production hole diameter be changed after the well is drilled?
Yes, the production hole diameter can be changed after the initial drilling using hole enlargement techniques such as underreaming or hole opening. These techniques involve using specialized tools to enlarge the wellbore to the desired diameter in specific sections of the well. Hole enlargement may be required to accommodate changes in the completion design, to address wellbore stability issues, or to optimize production performance.
- What are the challenges associated with drilling a large diameter production hole?
Drilling a large diameter production hole can present several challenges:
– Increased drilling costs due to higher rig time, fluid volumes, and equipment requirements
– Potential for wellbore instability, especially in weak or fractured formations
– Difficulty in achieving adequate hole cleaning and cuttings removal
– Increased risk of lost circulation and differential sticking
– Limitations on the maximum depth and lateral reach that can be achieved economically
To mitigate these challenges, operators use advanced drilling technologies, such as high-performance drilling fluids, pressure management techniques, and real-time monitoring systems, to optimize the drilling process and ensure a stable and productive production hole.
Conclusion
The production hole diameter is a critical parameter in well design and performance optimization. It impacts the well’s productivity, completion options, and economic viability. Selecting the appropriate production hole size requires a thorough understanding of the reservoir properties, expected flow rates, completion requirements, and economic constraints.
While larger production holes offer benefits such as improved flow rates and greater flexibility in completion design, they also come with challenges related to wellbore stability, drilling efficiency, and cost control. Operators must balance these trade-offs and employ advanced technologies and best practices to drill and maintain a stable, productive production hole.
As the oil and gas industry embraces digitalization, automation, and sustainable practices, new opportunities are emerging to optimize production hole design and performance. By leveraging data analytics, expandable tubulars, smart completions, and eco-friendly drilling techniques, operators can push the boundaries of what is possible with production hole optimization and unlock greater value from their assets.
Ultimately, the key to success in production hole design lies in continuous learning, innovation, and collaboration among operators, service companies, and technology providers. By staying at the forefront of these developments and adopting a holistic approach to well optimization, the industry can continue to safely and efficiently deliver the energy resources that power our world.
Leave a Reply