The PCB Fabrication Process
The PCB fabrication process can be broken down into several key steps:
1. PCB Design
The first step in PCB fabrication is the design phase. This involves creating a schematic diagram and a PCB layout using specialized software such as Altium Designer, Eagle, or KiCad. The schematic diagram shows the electrical connections between components, while the PCB layout shows the physical placement of components on the board.
2. PCB Printing
Once the design is complete, the next step is to print the PCB. This is done using a process called photolithography. The PCB design is printed onto a transparent film, which is then used to expose a photoresist layer on the copper-clad board. The exposed areas of the photoresist are then removed, leaving behind the desired circuit pattern.
3. Etching
After the photoresist has been developed, the next step is to etch away the unwanted copper from the board. This is typically done using a chemical etching process, where the board is immersed in an etchant solution that removes the exposed copper, leaving behind the desired circuit traces.
4. Drilling
Once the etching process is complete, the next step is to drill holes in the board for through-hole components and vias. This is done using a computer-controlled drill machine that precisely drills holes at the designated locations on the board.
5. Plating
After drilling, the board undergoes a plating process to improve the conductivity and durability of the copper traces. This is typically done using electroplating, where a thin layer of copper is deposited onto the board, followed by a layer of tin or gold to protect the copper from oxidation.
6. Solder Mask Application
The next step is to apply a solder mask to the board. The solder mask is a protective layer that covers the copper traces, leaving only the areas where components will be soldered exposed. This helps to prevent short circuits and improves the appearance of the board.
7. Silkscreen Printing
The final step in PCB fabrication is silkscreen printing. This involves printing text, logos, and other markings onto the board using a silkscreen printing process. This helps to identify components and provides a professional appearance to the finished board.
The PCB Assembly Process
Once the PCB fabrication process is complete, the next step is to assemble the components onto the board. The PCB assembly process can be broken down into several key steps:
1. Solder Paste Application
The first step in PCB assembly is to apply solder paste to the pads where components will be placed. This is typically done using a stencil printing process, where a thin metal stencil is placed over the board and solder paste is applied through the openings in the stencil.
2. Component Placement
After the solder paste has been applied, the next step is to place the components onto the board. This is typically done using a pick-and-place machine, which uses a vacuum nozzle to pick up components from a feeder and place them onto the board at the designated locations.
3. Reflow Soldering
Once the components have been placed, the next step is to perform reflow soldering. This involves passing the board through a reflow oven, which heats the solder paste to a temperature high enough to melt the solder and form a permanent connection between the components and the board.
4. Inspection
After reflow soldering, the board undergoes an inspection process to ensure that all components are properly soldered and that there are no defects or short circuits. This is typically done using automated optical inspection (AOI) equipment, which uses cameras and image processing software to detect any issues.
5. Through-Hole Component Soldering
If the board contains through-hole components, the next step is to solder these components onto the board. This is typically done using a wave soldering process, where the board is passed over a wave of molten solder, which flows through the holes and forms a connection between the component leads and the board.
6. Final Inspection and Testing
The final step in PCB assembly is to perform a final inspection and testing of the board. This involves visually inspecting the board for any defects or issues, as well as performing functional testing to ensure that the board operates as intended.
PCB Fabrication and Assembly: A Visual Guide
To help visualize the PCB fabrication and assembly process, let’s take a look at some images and diagrams:
Step | Image |
---|---|
PCB Design | |
PCB Printing | |
Etching | |
Drilling | |
Plating | |
Solder Mask Application | |
Silkscreen Printing | |
Solder Paste Application | |
Component Placement | |
Reflow Soldering | |
Inspection | |
Through-Hole Component Soldering | |
Final Inspection and Testing |
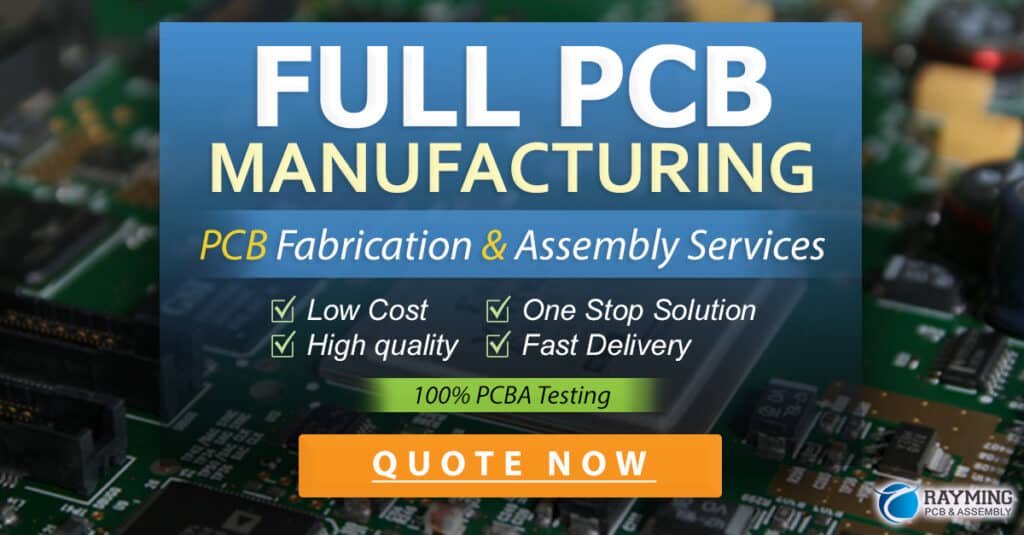
Frequently Asked Questions (FAQ)
1. What is the difference between PCB fabrication and PCB assembly?
PCB fabrication refers to the process of creating the bare PCB, including designing the circuit, printing the circuit pattern, etching, drilling, plating, and applying the solder mask and silkscreen. PCB assembly, on the other hand, refers to the process of attaching components to the fabricated PCB, including applying solder paste, placing components, reflow soldering, and inspection.
2. What are the different types of PCBs?
There are several types of PCBs, including:
- Single-layer PCBs: These have conductive copper traces on one side of the board only.
- Double-layer PCBs: These have conductive copper traces on both sides of the board.
- Multi-layer PCBs: These have conductive copper traces on multiple layers, with insulating layers in between.
- Flexible PCBs: These are made from flexible materials and can be bent or folded.
- Rigid-Flex PCBs: These combine rigid and flexible sections to create a more complex design.
3. What are the advantages of using a pick-and-place machine for component placement?
Using a pick-and-place machine for component placement offers several advantages, including:
- Increased accuracy and precision compared to manual placement
- Faster placement speed, which can reduce assembly time and costs
- Ability to handle smaller components that would be difficult to place manually
- Reduced risk of human error and component damage during placement
4. What is the purpose of the solder mask on a PCB?
The solder mask is a protective layer that covers the copper traces on a PCB, leaving only the areas where components will be soldered exposed. The main purposes of the solder mask are:
- To prevent short circuits between adjacent traces
- To protect the copper traces from oxidation and damage
- To provide electrical insulation between components and traces
- To improve the appearance of the board by providing a uniform color and surface finish
5. What are some common defects that can occur during PCB fabrication and assembly?
Some common defects that can occur during PCB fabrication and assembly include:
- Short circuits or open circuits due to incorrect etching or drilling
- Solder bridges or insufficient solder joints due to incorrect solder paste application or reflow soldering
- Component misalignment or damage due to incorrect placement or handling
- Contamination or oxidation of the copper traces due to improper cleaning or storage
- Delamination or warping of the board due to incorrect material selection or processing conditions
By understanding the common defects that can occur and implementing proper quality control measures, manufacturers can minimize the risk of defects and ensure the reliability and performance of the finished PCB.
Conclusion
PCB fabrication and assembly is a complex process that involves several steps, from design to the final product. By understanding each step in the process and implementing proper quality control measures, manufacturers can ensure the reliability and performance of the finished PCB.
Whether you are a designer, engineer, or manufacturer, it is important to have a thorough understanding of the PCB fabrication and assembly process in order to create high-quality, reliable PCBs that meet the needs of your application.
Leave a Reply