Introduction to Immersion Tin PCB
Immersion tin (IT) is a surface finish technique widely used in the printed circuit board (PCB) industry. It involves the deposition of a thin layer of tin onto the exposed copper surfaces of a PCB through an electroless plating process. Immersion tin PCB offers several advantages, including excellent solderability, improved shelf life, and compatibility with lead-free soldering processes. In this article, we will delve into the process of immersion tin on PCB, its benefits, and its applications.
The Immersion Tin Process
The immersion tin process is a simple and cost-effective method for applying a thin layer of tin onto the copper surfaces of a PCB. The process involves the following steps:
-
Cleaning: The PCB is thoroughly cleaned to remove any contaminants, such as dirt, grease, or oxidation, from the copper surfaces. This step is crucial to ensure proper adhesion of the tin layer.
-
Microetching: The copper surfaces are then treated with a microetch solution to remove any remaining oxidation and to roughen the surface slightly. This step improves the adhesion of the tin layer to the copper.
-
Rinsing: The PCB is rinsed with deionized water to remove any residual microetch solution.
-
Immersion Tin Plating: The PCB is immersed in an immersion tin plating solution, which typically contains tin ions, thiourea, and other proprietary additives. The tin ions in the solution displace the copper atoms on the surface of the PCB, forming a thin layer of tin. This process is self-limiting, meaning that once the tin layer reaches a certain thickness (typically 0.5-2.0 μm), the reaction slows down significantly.
-
Rinsing: The PCB is rinsed again with deionized water to remove any excess plating solution.
-
Drying: The PCB is dried using hot air or an oven to remove any remaining moisture.
The entire immersion tin process is relatively quick, taking only a few minutes to complete. The resulting tin layer is uniform, thin, and provides excellent protection against oxidation and corrosion.
Benefits of Immersion Tin PCB
Immersion tin PCB offers several benefits over other surface finish options, such as hot air solder leveling (HASL) or electroless nickel immersion gold (ENIG). Some of the key benefits include:
-
Excellent Solderability: The thin layer of tin provides excellent solderability, ensuring reliable and strong solder joints. The tin layer also helps to prevent the formation of intermetallic compounds (IMCs) during soldering, which can lead to brittle and weak solder joints.
-
Improved Shelf Life: The tin layer acts as a barrier, protecting the underlying copper from oxidation and corrosion. This protection extends the shelf life of the PCB, allowing for longer storage times before assembly.
-
Compatibility with Lead-Free Soldering: Immersion tin is compatible with lead-free soldering processes, which are becoming increasingly common due to environmental and health concerns. The tin layer helps to facilitate the formation of reliable lead-free solder joints.
-
Cost-Effective: Compared to other surface finish options, such as ENIG, immersion tin is a cost-effective solution. The process is simple, quick, and requires fewer materials, making it an attractive option for budget-conscious projects.
-
Flat Surface: Unlike HASL, which can result in an uneven surface due to the hot air leveling process, immersion tin produces a flat and uniform surface. This flatness is essential for fine-pitch components and high-density PCB designs.
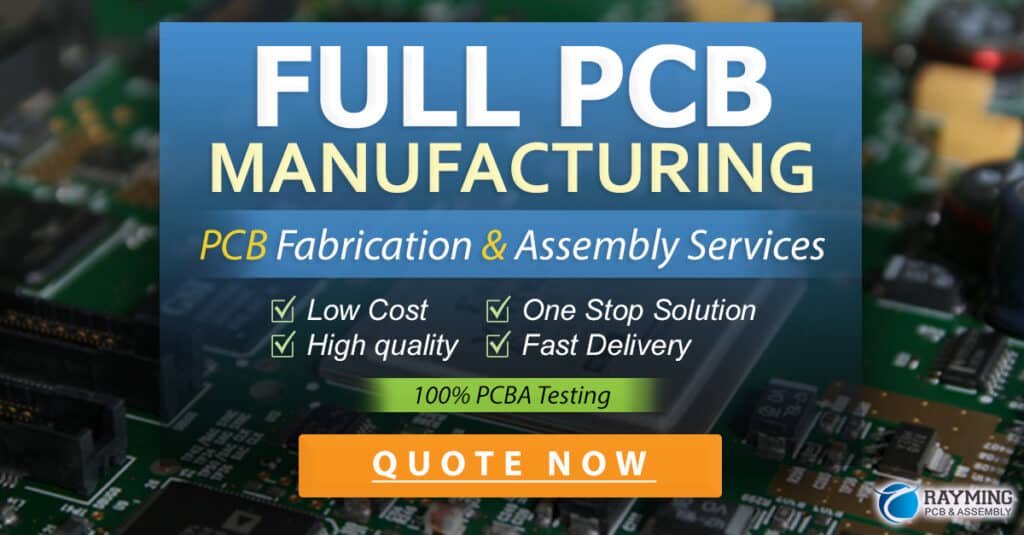
Applications of Immersion Tin PCB
Immersion tin PCB is widely used in various industries and applications, including:
-
Consumer Electronics: Immersion tin is commonly used in consumer electronics, such as smartphones, tablets, and laptops. The excellent solderability and compatibility with lead-free soldering make it an ideal choice for these applications.
-
Automotive Electronics: The automotive industry relies on immersion tin PCBs for various electronic components, such as engine control units, infotainment systems, and safety features. The improved shelf life and reliability of immersion tin are crucial for these applications.
-
Industrial Electronics: Immersion tin PCBs are used in industrial electronics, such as process control systems, automation equipment, and power supplies. The cost-effectiveness and reliability of immersion tin make it a popular choice for these applications.
-
Medical Devices: Medical devices, such as patient monitoring systems and diagnostic equipment, often utilize immersion tin PCBs. The flat surface and excellent solderability ensure reliable connections and performance in these critical applications.
Challenges and Considerations
While immersion tin PCB offers many benefits, there are some challenges and considerations to keep in mind:
-
Tin Whiskers: One potential issue with immersion tin is the formation of tin whiskers, which are thin, conductive filaments that can grow from the tin surface. Tin whiskers can cause short circuits and other reliability issues. However, proper process control and the use of tin alloys containing small amounts of copper or silver can mitigate this risk.
-
Limited Thickness: The self-limiting nature of the immersion tin process results in a relatively thin tin layer (typically 0.5-2.0 μm). This thin layer may not provide sufficient protection for applications exposed to harsh environments or requiring extended shelf life. In such cases, other surface finishes, such as ENIG, may be more appropriate.
-
Copper Dissolution: During the immersion tin process, some copper is dissolved into the plating solution. This copper dissolution can lead to a slightly thinner copper layer on the PCB, which may impact the electrical performance of the circuit. However, this effect is usually minimal and can be accounted for during the PCB design phase.
FAQs
-
Q: What is the typical thickness of the tin layer in immersion tin PCB?
A: The typical thickness of the tin layer in immersion tin PCB ranges from 0.5 to 2.0 μm. -
Q: Is immersion tin suitable for lead-free soldering?
A: Yes, immersion tin is compatible with lead-free soldering processes and helps to facilitate the formation of reliable lead-free solder joints. -
Q: How does immersion tin compare to ENIG in terms of cost?
A: Immersion tin is generally more cost-effective than ENIG, as the process is simpler, quicker, and requires fewer materials. -
Q: Can immersion tin be used for high-density PCB designs?
A: Yes, immersion tin is suitable for high-density PCB designs due to its flat and uniform surface, which is essential for fine-pitch components. -
Q: What is the main challenge associated with immersion tin PCB?
A: The main challenge associated with immersion tin PCB is the potential formation of tin whiskers, which can cause short circuits and reliability issues. However, this risk can be mitigated through proper process control and the use of tin alloys containing small amounts of copper or silver.
Conclusion
Immersion tin is a popular and reliable surface finish option for PCBs, offering excellent solderability, improved shelf life, and compatibility with lead-free soldering processes. The simple and cost-effective nature of the immersion tin process, combined with its numerous benefits, makes it an attractive choice for a wide range of industries and applications. While there are some challenges and considerations to keep in mind, such as the potential for tin whiskers and limited thickness, these can be addressed through proper process control and design considerations. As the electronics industry continues to evolve, immersion tin PCB is likely to remain a key player in the world of pcb surface finishes.
Leave a Reply