Understanding PCB component clearance
PCB component clearance refers to the minimum distance required between components, traces, and other features on a PCB to ensure proper assembly, soldering, and operation. Adequate clearances help prevent short circuits, unwanted interactions, and manufacturing defects.
Why is Component Clearance Important?
Maintaining proper component clearances is crucial for several reasons:
- Manufacturing feasibility: Sufficient clearances allow for reliable soldering and prevent bridging between adjacent pads or traces.
- Electrical isolation: Proper clearances help prevent short circuits and unintended electrical connections.
- Heat dissipation: Adequate spacing between components allows for better heat dissipation, preventing thermal issues.
- Signal integrity: Appropriate clearances minimize electromagnetic interference (EMI) and crosstalk between components and traces.
IPC Standards for PCB Component Clearance
The IPC has established several standards that address PCB design and manufacturing, including component clearances. The most relevant standard for this topic is IPC-2221, “Generic Standard on Printed Board Design.”
IPC-2221 Overview
IPC-2221 provides guidelines for PCB design, including recommendations for component and feature sizes, spacing, and clearances. The standard covers various aspects of PCB design, such as:
- Board layout and routing
- Hole sizes and spacing
- Conductor widths and spacing
- Solder mask and silkscreen requirements
- Electrical clearances
IPC Component Clearance Classes
IPC-2221 defines three classes of PCBs based on the level of reliability and performance required:
- Class 1: General electronic products
- Class 2: Dedicated service electronic products
- Class 3: High-reliability electronic products
The minimum component clearances vary depending on the PCB class and the specific component or feature type.
Minimum Component Clearances per IPC-2221
The following tables provide an overview of the minimum component clearances specified in IPC-2221 for different component types and PCB classes.
Surface Mount Technology (SMT) Components
Component Type | Class 1 (mm) | Class 2 (mm) | Class 3 (mm) |
---|---|---|---|
Chip Components | 0.50 | 0.50 | 0.75 |
Gull Wing Leads | 0.25 | 0.25 | 0.40 |
J-Leads | 0.25 | 0.25 | 0.40 |
Ball Grid Array (BGA) | 0.25 | 0.25 | 0.40 |
Through-Hole Technology (THT) Components
Component Type | Class 1 (mm) | Class 2 (mm) | Class 3 (mm) |
---|---|---|---|
Axial Lead | 0.50 | 0.50 | 0.75 |
Radial Lead | 0.50 | 0.50 | 0.75 |
DIP/SIP | 0.50 | 0.50 | 0.75 |
Connectors | 0.50 | 0.50 | 0.75 |
Clearances Between Components and Board Edge
PCB Class | Minimum Clearance (mm) |
---|---|
Class 1 | 1.00 |
Class 2 | 1.00 |
Class 3 | 1.50 |
Clearances Between Components and Mounting Holes
PCB Class | Minimum Clearance (mm) |
---|---|
Class 1 | 1.00 |
Class 2 | 1.00 |
Class 3 | 1.50 |
Clearances Between Components and Traces
PCB Class | Minimum Clearance (mm) |
---|---|
Class 1 | 0.25 |
Class 2 | 0.25 |
Class 3 | 0.40 |
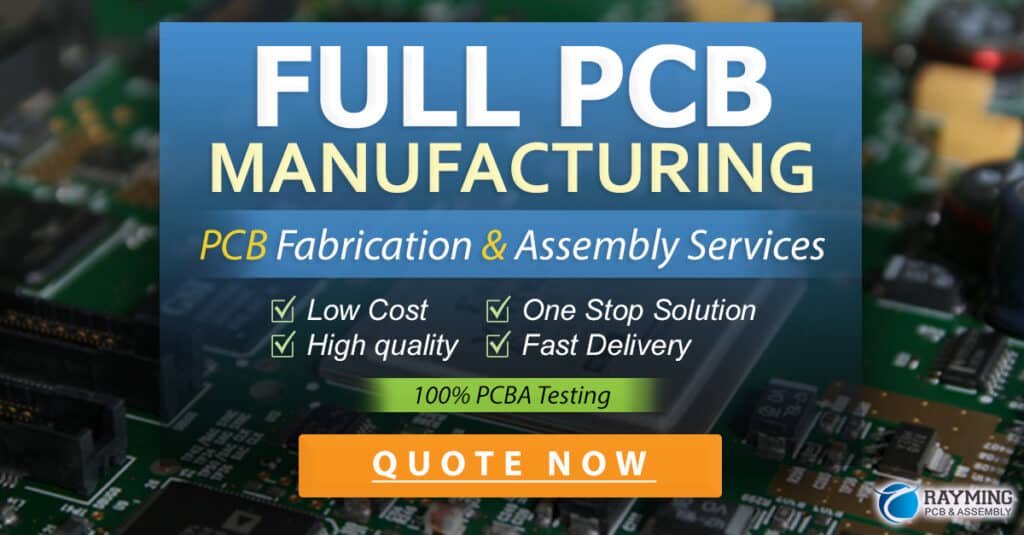
Factors Affecting Component Clearances
Several factors can influence the required component clearances on a PCB:
- PCB manufacturing process: Different manufacturing processes may have varying clearance requirements due to their capabilities and limitations.
- Component package type: The component package (e.g., SMT or THT) and its dimensions will affect the necessary clearances.
- PCB layer count: Multi-layer PCBs may require additional clearances to accommodate vias and layer transitions.
- Operating environment: Harsh environments (e.g., high temperature, vibration) may necessitate larger clearances for improved reliability.
- Signal characteristics: High-speed or high-frequency signals may demand increased clearances to minimize interference and maintain signal integrity.
Best Practices for Maintaining Component Clearances
To ensure your PCB design adheres to IPC standards and maintains proper component clearances, consider the following best practices:
- Use IPC-compliant PCB design software that includes built-in design rule checks (DRC) for component clearances.
- Regularly review and update your PCB design rules to align with the latest IPC standards and manufacturing capabilities.
- Collaborate closely with your PCB manufacturer to understand their specific clearance requirements and capabilities.
- Consider the PCB’s intended use and operating environment when determining appropriate component clearances.
- Conduct thorough design reviews and DRC checks before finalizing your PCB layout to catch any clearance violations.
Frequently Asked Questions (FAQ)
-
What happens if I don’t maintain proper component clearances on my PCB?
Insufficient component clearances can lead to manufacturing issues, such as solder bridging, short circuits, and poor soldering. It can also cause electrical problems, like signal interference and crosstalk, and may impact the PCB’s reliability and longevity. -
Can I use smaller component clearances than those specified in IPC-2221?
While it may be tempting to use smaller clearances to save space on your PCB, it’s generally not recommended to deviate from IPC standards. Doing so can increase the risk of manufacturing defects and reliability issues. If you need to use smaller clearances, consult with your PCB manufacturer to ensure they can accommodate your design. -
Do I need to follow IPC standards if my PCB is for a personal project?
Following IPC standards is always a good practice, even for personal projects. Adhering to these standards helps ensure your PCB will be manufacturable, reliable, and functional. However, if your project has unique requirements or constraints, you may need to adapt the clearances accordingly. -
How can I ensure my PCB design software is using the correct IPC clearances?
Most modern PCB design software packages include built-in design rule checks (DRC) that can be configured to match IPC standards. Check your software’s documentation or settings to ensure the correct IPC clearances are being applied. Some software may also include IPC-compliant component libraries and templates. -
What should I do if I’m unsure about the appropriate component clearances for my PCB?
If you’re unsure about the appropriate component clearances for your PCB, consult the IPC-2221 standard for guidance. You can also reach out to your PCB manufacturer for advice on their specific requirements and capabilities. In some cases, it may be necessary to engage a professional PCB designer to ensure your design meets all relevant standards and requirements.
Conclusion
Maintaining proper component clearances is essential for designing and manufacturing reliable, high-quality PCBs. The IPC-2221 standard provides comprehensive guidelines for minimum component clearances based on PCB class and component type. By understanding and adhering to these standards, you can help ensure your PCB design is manufacturable, reliable, and functional.
When designing your PCB, consider factors such as the manufacturing process, component package types, layer count, operating environment, and signal characteristics that may impact the required clearances. Use IPC-compliant PCB design software, collaborate with your manufacturer, and conduct thorough design reviews to maintain proper component clearances.
By following the guidelines and best practices outlined in this article, you can create PCB designs that meet industry standards, minimize the risk of manufacturing defects, and ensure optimal performance and reliability.
Leave a Reply