How Galvanic electrolysis Works
In galvanic electrolysis, two dissimilar metals are immersed in an electrolyte solution and connected by an external circuit. The metal with the more negative reduction potential acts as the anode and undergoes oxidation, losing electrons. The metal with the more positive reduction potential acts as the cathode and undergoes reduction, gaining electrons.
The anode and cathode are connected to a power source, such as a battery or electrical outlet. When the power is turned on, electrons flow from the anode to the cathode through the external circuit. This flow of electrons drives the non-spontaneous redox reactions at the electrodes.
At the anode, the metal atoms lose electrons and go into solution as positively charged ions. The general half-reaction at the anode is:
M(s) → M^n+(aq) + ne^−
where M is the metal, n is the number of electrons transferred, and e^− represents the electrons.
At the cathode, positively charged ions in solution gain electrons and are reduced to their neutral metallic state. The general half-reaction at the cathode is:
M^n+(aq) + ne^− → M(s)
The overall redox reaction is the sum of the half-reactions at the anode and cathode:
Anode (oxidation): M1(s) → M1^n+(aq) + ne^−
Cathode (reduction): M2^n+(aq) + ne^− → M2(s)
Overall: M1(s) + M2^n+(aq) → M1^n+(aq) + M2(s)
The metal ions produced at the anode can either remain in solution or be deposited onto the cathode, depending on the relative reduction potentials of the metals and the applied potential.
Factors Affecting Galvanic Electrolysis
Several factors influence the rate and efficiency of galvanic electrolysis:
-
Electrode potential: The difference in reduction potentials between the anode and cathode determines the magnitude and direction of electron flow. A larger potential difference results in a greater driving force for the redox reactions.
-
Electrolyte composition: The type and concentration of ions in the electrolyte solution affect the conductivity and the mobility of the ions. Higher ion concentrations generally increase the rate of electrolysis.
-
Temperature: Increasing the temperature of the electrolyte solution increases the rate of ion diffusion and the kinetics of the electrode reactions, resulting in faster electrolysis.
-
Current density: The current density, which is the current per unit area of the electrode surface, determines the rate of the electrode reactions. Higher current densities lead to faster electrolysis but may also result in uneven deposits or side reactions.
-
Electrode surface area: Larger electrode surface areas provide more sites for the redox reactions to occur, increasing the rate of electrolysis.
-
Agitation: Stirring or agitating the electrolyte solution helps to maintain a uniform concentration of ions near the electrode surfaces and prevents the buildup of concentration gradients, which can slow down the electrolysis.
Applications of Galvanic Electrolysis
Galvanic electrolysis has numerous industrial and commercial applications, including:
Electroplating
Electroplating is a process in which a thin layer of one metal is deposited onto the surface of another metal using galvanic electrolysis. The metal to be plated serves as the cathode, while the plating metal is the anode. When an electric current is applied, ions of the plating metal are reduced at the cathode, forming a thin, adherent coating.
Electroplating is used to improve the appearance, durability, and corrosion resistance of metal objects. Common examples include:
- Chromium plating of steel parts for increased wear resistance and shine
- Nickel plating of copper or brass for improved corrosion resistance
- Gold plating of jewelry and electronics for enhanced appearance and conductivity
- Zinc plating (galvanization) of iron and steel for corrosion protection
The thickness and quality of the electroplated coating depend on factors such as the current density, plating time, electrolyte composition, and additives used.
Electrorefining
Electrorefining is a process used to purify metals by selectively dissolving impure metal at the anode and depositing pure metal at the cathode. The impure metal is cast into a slab and serves as the anode, while a thin sheet of pure metal acts as the cathode. Both electrodes are immersed in an electrolyte solution containing ions of the metal being refined.
When an electric current is applied, the impure metal at the anode dissolves, releasing metal ions into the solution along with any impurities. The pure metal ions migrate to the cathode and are reduced, forming a deposit of high-purity metal. The impurities either remain in solution or form a sludge at the bottom of the cell.
Electrorefining is widely used in the production of high-purity copper, nickel, lead, and precious metals such as gold and silver. The process enables the removal of impurities that cannot be eliminated by other refining methods, such as pyrometallurgy.
Electrowinning
Electrowinning is a process used to extract metals from their ores or solutions by galvanic electrolysis. In this process, the metal of interest is present in the electrolyte solution as dissolved ions, often obtained by leaching the ore with an acid or base.
An inert anode, such as lead or graphite, is used, while the cathode is a thin sheet of the metal being extracted or a suitable substrate material. When an electric current is applied, the metal ions in solution are reduced at the cathode, forming a pure metal deposit. The oxygen evolved at the anode is either released as a gas or reacts with the electrolyte.
Electrowinning is commonly used for the production of copper, zinc, nickel, cobalt, and rare earth elements. It is particularly useful for recovering metals from low-grade ores or from solutions obtained by hydrometallurgical processes, such as solvent extraction.
Cathodic Protection
Cathodic protection is a technique used to prevent or minimize corrosion of metal structures by making them the cathode in a galvanic cell. This is achieved by connecting the metal to be protected to a more easily corroded metal (sacrificial anode) or by applying an external current using an inert anode (impressed current cathodic protection).
In sacrificial anode cathodic protection, the sacrificial anode, typically made of zinc, magnesium, or aluminum, corrodes preferentially, protecting the metal structure. The sacrificial anode is gradually consumed and must be replaced periodically.
In impressed current cathodic protection, an external power source is used to supply electrons to the metal structure, making it the cathode. An inert anode, such as graphite or titanium, is used to complete the circuit. The impressed current overcomes the natural corrosion potential of the metal, preventing its dissolution.
Cathodic protection is widely used to protect pipelines, storage tanks, ship hulls, offshore structures, and reinforced concrete structures from corrosion. It is particularly effective in protecting metals in contact with electrolytes, such as seawater or soil.
Advantages and Disadvantages of Galvanic Electrolysis
Galvanic electrolysis offers several advantages:
-
Controlled deposition: Electrolysis allows for precise control over the thickness, composition, and morphology of the deposited metal layer by adjusting parameters such as current density, time, and electrolyte composition.
-
High purity: Electrorefining and electrowinning can produce metals with very high purity, often exceeding 99.99%, as the process selectively deposits the desired metal while leaving impurities in the electrolyte or anode sludge.
-
Versatility: Galvanic electrolysis can be applied to a wide range of metals and alloys, including those that are difficult to purify or deposit using other methods.
-
Cost-effective: For large-scale production, galvanic electrolysis can be a cost-effective method for metal purification and deposition, as it can be easily scaled up and automated.
However, galvanic electrolysis also has some disadvantages:
-
Energy consumption: Electrolysis processes require a significant amount of electrical energy, which can be costly and may have environmental impacts depending on the source of the electricity.
-
Limited throwing power: In electroplating, the thickness of the deposited layer may not be uniform on irregularly shaped objects or in recessed areas due to the limited throwing power of the electrolyte.
-
Hydrogen embrittlement: In some cases, hydrogen gas evolved at the cathode during electrolysis can be absorbed by the metal, leading to hydrogen embrittlement and reduced mechanical properties.
-
Waste generation: Electrolysis processes generate waste streams, such as spent electrolytes and anode sludges, which must be properly treated and disposed of to minimize environmental impacts.
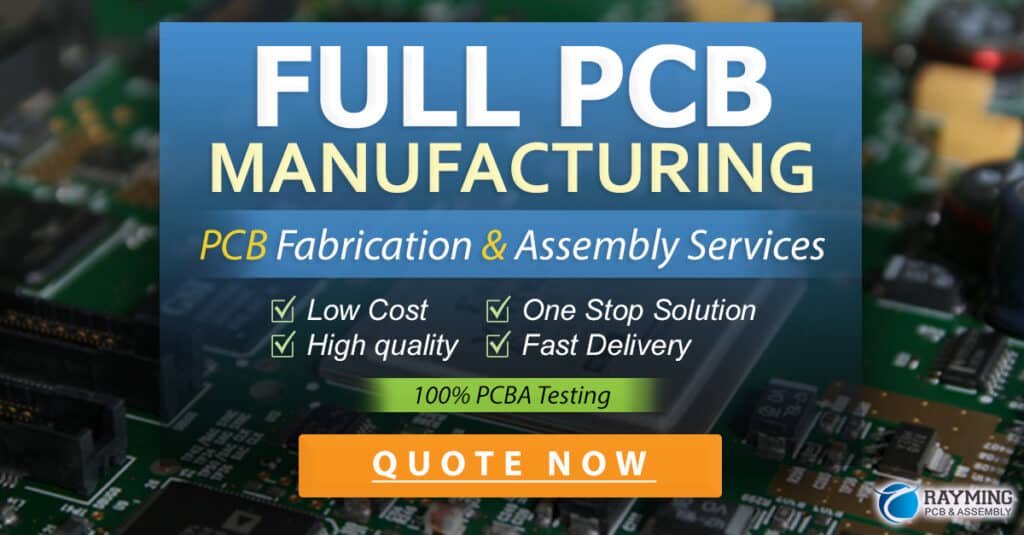
Frequently Asked Questions (FAQ)
-
What is the difference between galvanic electrolysis and electrolytic electrolysis?
Galvanic electrolysis and electrolytic electrolysis are both electrochemical processes that involve the transfer of electrons between electrodes in an electrolyte solution. However, they differ in their driving force and spontaneity: -
Galvanic electrolysis is driven by the difference in reduction potentials between the two electrodes, causing a spontaneous redox reaction when the electrodes are connected. The more reactive metal acts as the anode and undergoes oxidation, while the less reactive metal acts as the cathode and undergoes reduction.
-
Electrolytic electrolysis, on the other hand, is driven by an external power source that supplies electrical energy to force a non-spontaneous redox reaction. The direction of the electron flow and the reactions at the electrodes are determined by the polarity of the applied potential, rather than the relative reactivities of the electrodes.
-
Can galvanic electrolysis be used to produce hydrogen gas?
Yes, galvanic electrolysis can be used to produce hydrogen gas. In this case, the cathode reaction involves the reduction of water molecules or hydrogen ions to form hydrogen gas:
2H2O(l) + 2e^− → H2(g) + 2OH^−(aq)
or
2H^+(aq) + 2e^− → H2(g)
The anode reaction depends on the material used and may involve the oxidation of a sacrificial metal or the evolution of oxygen gas. Hydrogen gas produced by galvanic electrolysis has various applications, such as in fuel cells, chemical synthesis, and welding.
-
What is the role of the electrolyte in galvanic electrolysis?
The electrolyte in galvanic electrolysis serves several important roles: -
It provides a conductive medium for the transfer of ions between the electrodes, allowing the redox reactions to occur.
- It supplies the necessary ions for the electrode reactions, such as metal ions for deposition or hydrogen ions for gas evolution.
- It helps to maintain charge balance by transporting counter ions (anions for cations and vice versa) between the electrodes.
- In some cases, the electrolyte may also contain additives that influence the morphology, composition, or properties of the deposited metal layer.
The choice of electrolyte depends on the specific application and the metals involved. Common electrolytes include aqueous solutions of salts, acids, or bases, as well as molten salts and ionic liquids.
-
How does temperature affect galvanic electrolysis?
Temperature has a significant impact on the kinetics and efficiency of galvanic electrolysis. In general, increasing the temperature of the electrolyte has the following effects: -
Higher temperatures increase the mobility of ions in the electrolyte, reducing the resistance and allowing for higher current densities and faster reaction rates.
- Elevated temperatures can improve the diffusion of reactants and products to and from the electrode surfaces, reducing concentration polarization and improving the uniformity of the deposited layer.
- In some cases, higher temperatures may also increase the solubility of the metal ions or other reactants in the electrolyte, facilitating the electrode reactions.
However, excessively high temperatures can also lead to undesirable effects, such as increased evaporation of the electrolyte, degradation of additives, or changes in the morphology of the deposited layer. The optimal temperature for galvanic electrolysis depends on the specific system and application.
-
What are some common problems encountered in galvanic electrolysis, and how can they be addressed?
Some common problems encountered in galvanic electrolysis include: -
Non-uniform deposition: Uneven current distribution or mass transport limitations can lead to non-uniform thickness or composition of the deposited layer. This can be addressed by optimizing the electrode geometry, electrolyte composition, and agitation conditions.
-
Dendrite formation: In some cases, the deposited metal may form dendritic or powdery deposits, reducing the quality and adherence of the layer. This can be mitigated by using additives that promote smooth and compact deposits, such as leveling agents or brighteners.
-
Hydrogen embrittlement: Hydrogen gas evolved at the cathode can be absorbed by the metal, leading to embrittlement and reduced mechanical properties. This can be addressed by using lower current densities, pulsed current techniques, or post-deposition heat treatments to remove the absorbed hydrogen.
-
Contamination: Impurities in the electrolyte or the electrodes can lead to contamination of the deposited layer, affecting its properties and performance. This can be minimized by using high-purity reagents, maintaining proper electrolyte filtration and purification, and ensuring the cleanliness of the electrode surfaces.
-
Anode passivation: In some cases, the anode may become passivated by the formation of an insulating oxide layer, reducing its efficiency and increasing the cell voltage. This can be addressed by using sacrificial anodes, periodic anode replacement, or by adding depolarizers to the electrolyte that prevent passivation.
Addressing these problems requires a thorough understanding of the galvanic electrolysis process, as well as careful control and optimization of the operating parameters and electrolyte composition.
Leave a Reply