How Preheaters Work
Preheaters work by transferring heat from a heating medium to the substance that needs to be heated. The heating medium can be steam, hot water, electricity, or even waste heat from another process. The substance to be heated flows through tubes or channels within the preheater, while the heating medium flows around these tubes or channels, transferring its heat to the substance.
The heat transfer process in a preheater can occur through three main mechanisms:
- Conduction
- Convection
- Radiation
Conduction
Conduction is the transfer of heat through direct contact between two materials. In a preheater, conduction occurs when the substance to be heated comes into direct contact with the walls of the tubes or channels, which are heated by the heating medium.
Convection
Convection is the transfer of heat through the movement of fluids or gases. In a preheater, convection occurs when the heating medium flows around the tubes or channels containing the substance to be heated. As the heating medium moves, it transfers its heat to the walls of the tubes or channels, which then transfer the heat to the substance through conduction.
Radiation
Radiation is the transfer of heat through electromagnetic waves. In a preheater, radiation can occur when the heating medium and the substance to be heated are separated by a gap. The heating medium emits electromagnetic waves that travel across the gap and are absorbed by the substance, causing it to heat up.
Types of Preheaters
There are several types of preheaters used in various industrial applications. The choice of preheater depends on factors such as the nature of the substance to be heated, the required temperature range, and the available heating medium. Some common types of preheaters include:
- Shell and tube preheaters
- Plate heat exchangers
- Electric preheaters
- Waste heat recovery preheaters
Shell and Tube Preheaters
Shell and tube preheaters consist of a bundle of tubes enclosed within a cylindrical shell. The substance to be heated flows through the tubes, while the heating medium flows through the shell, around the tubes. This design provides a large surface area for heat transfer and is suitable for a wide range of applications.
Advantage | Disadvantage |
---|---|
High heat transfer efficiency | Larger size compared to other types |
Can handle high temperatures and pressures | Higher capital cost |
Suitable for a wide range of fluids | Requires more space for installation |
Plate Heat Exchangers
Plate heat exchangers consist of a series of thin, corrugated metal plates stacked together. The substance to be heated and the heating medium flow through alternate channels between the plates, allowing for efficient heat transfer. Plate heat exchangers are compact and easy to maintain, making them suitable for applications with limited space.
Advantage | Disadvantage |
---|---|
Compact design | Limited temperature and pressure range |
Easy to maintain and clean | Not suitable for fluids with high viscosity or particles |
High heat transfer efficiency | Higher pressure drop compared to shell and tube preheaters |
Electric Preheaters
Electric preheaters use electrical energy to heat the substance directly. They consist of heating elements immersed in the substance or in contact with the walls of the container holding the substance. Electric preheaters are suitable for applications where precise temperature control is required or where other heating media are not available.
Advantage | Disadvantage |
---|---|
Precise temperature control | Higher operating costs compared to other types |
Compact design | Limited to lower temperature ranges |
Easy to install and maintain | Not suitable for flammable or explosive substances |
Waste Heat Recovery Preheaters
Waste heat recovery preheaters use heat from other processes that would otherwise be lost to the environment. This type of preheater is becoming increasingly popular as industries strive to improve energy efficiency and reduce their environmental impact. Waste heat recovery preheaters can use various sources of waste heat, such as flue gases, steam, or hot water.
Advantage | Disadvantage |
---|---|
Improves overall energy efficiency | Requires a reliable source of waste heat |
Reduces energy costs | Higher capital cost compared to other types |
Reduces environmental impact | May require additional equipment for waste heat capture and transfer |
Applications of Preheaters
Preheaters are used in a wide range of industrial applications, including:
- Power generation
- Chemical processing
- Food and beverage processing
- Oil and gas processing
- Pulp and paper industry
Power Generation
In power generation, preheaters are used to heat the feedwater before it enters the boiler. Preheating the feedwater improves the efficiency of the boiler and reduces fuel consumption. Preheaters in power plants typically use steam extracted from the turbine as the heating medium.
Chemical Processing
In chemical processing, preheaters are used to heat reactants before they enter the reactor. Preheating the reactants can improve reaction rates, increase yield, and reduce energy consumption. Preheaters in chemical processing can use steam, hot oil, or electricity as the heating medium.
Food and Beverage Processing
In food and beverage processing, preheaters are used to heat ingredients or products before further processing. For example, milk is often preheated before pasteurization to improve the efficiency of the pasteurization process. Preheaters in food and beverage processing typically use steam or hot water as the heating medium.
Oil and Gas Processing
In oil and gas processing, preheaters are used to heat crude oil before it enters the distillation column. Preheating the crude oil reduces its viscosity and improves the efficiency of the distillation process. Preheaters in oil and gas processing can use steam, hot oil, or flue gases as the heating medium.
Pulp and Paper Industry
In the pulp and paper industry, preheaters are used to heat water and pulp before further processing. Preheating the water and pulp reduces energy consumption and improves the efficiency of the papermaking process. Preheaters in the pulp and paper industry typically use steam or hot water as the heating medium.
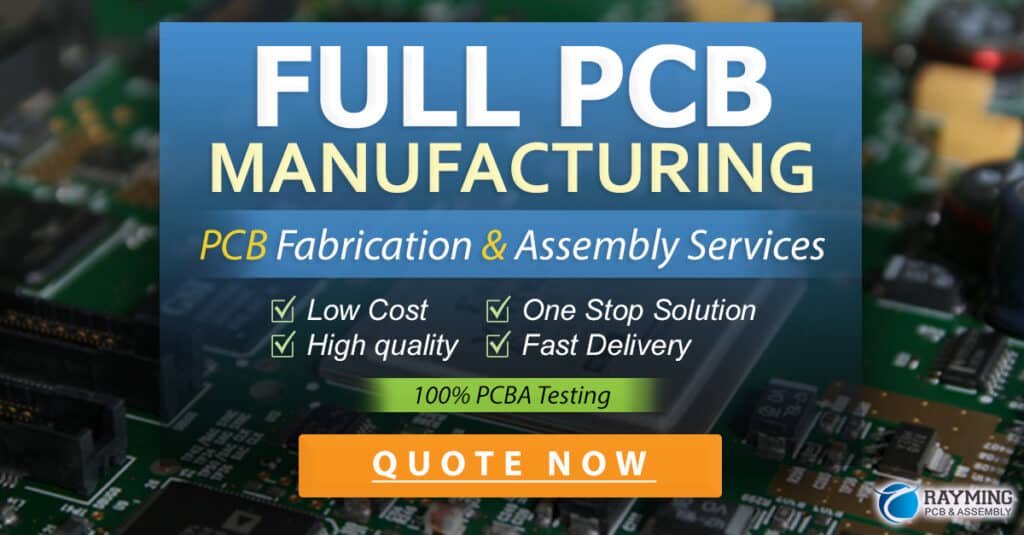
Advantages of Using Preheaters
Using preheaters in industrial processes offers several advantages, including:
- Improved energy efficiency
- Reduced fuel consumption
- Increased production capacity
- Improved product quality
- Reduced environmental impact
Improved Energy Efficiency
Preheaters improve energy efficiency by recovering heat that would otherwise be lost to the environment. By preheating the substance before it enters the main processing unit, less energy is required to bring the substance to the desired temperature. This reduction in energy consumption leads to lower operating costs and improved overall efficiency.
Reduced Fuel Consumption
Preheaters reduce fuel consumption by decreasing the amount of energy required to heat the substance in the main processing unit. By preheating the substance, the main processing unit requires less fuel to achieve the desired temperature, resulting in significant fuel savings.
Increased Production Capacity
Preheaters can increase production capacity by reducing the time required to heat the substance in the main processing unit. By preheating the substance, the main processing unit can operate at a higher throughput, resulting in increased production capacity.
Improved Product Quality
Preheaters can improve product quality by ensuring that the substance enters the main processing unit at the desired temperature. This consistency in temperature can lead to more uniform product quality and reduced waste.
Reduced Environmental Impact
Preheaters can reduce the environmental impact of industrial processes by reducing energy consumption and fuel usage. By improving energy efficiency and reducing fuel consumption, preheaters help to lower greenhouse gas emissions and other pollutants associated with energy production.
Maintenance and Troubleshooting of Preheaters
To ensure optimal performance and longevity of preheaters, regular maintenance and troubleshooting are essential. Some key aspects of preheater maintenance and troubleshooting include:
- Regular cleaning
- Inspections for wear and damage
- Calibration of temperature sensors
- Addressing common issues
Regular Cleaning
Regular cleaning of preheaters is crucial to maintaining their efficiency and preventing fouling. Fouling occurs when deposits build up on the heat transfer surfaces, reducing heat transfer efficiency and increasing pressure drop. Regular cleaning helps to remove these deposits and restore the preheater’s performance.
Inspections for Wear and Damage
Periodic inspections of preheaters are necessary to identify any wear or damage to the components. This includes checking for leaks, corrosion, and erosion of the tubes, shell, and other components. Identifying and addressing these issues early can prevent more serious problems from developing and extend the life of the preheater.
Calibration of Temperature Sensors
Temperature sensors in preheaters must be regularly calibrated to ensure accurate temperature control. Inaccurate temperature readings can lead to inefficient operation or even damage to the preheater or downstream equipment.
Addressing Common Issues
Some common issues that may arise with preheaters include:
- Fouling of heat transfer surfaces
- Leaks in tubes or shell
- Corrosion or erosion of components
- Malfunctioning temperature sensors
- Inadequate flow rates
Addressing these issues promptly is essential to maintaining the performance and reliability of the preheater.
Frequently Asked Questions (FAQ)
-
What is the purpose of a preheater?
The purpose of a preheater is to raise the temperature of a substance before it enters the main processing unit, improving efficiency and reducing energy consumption. -
What are the main types of preheaters?
The main types of preheaters are shell and tube preheaters, plate heat exchangers, electric preheaters, and waste heat recovery preheaters. -
What industries commonly use preheaters?
Preheaters are commonly used in power generation, chemical processing, food and beverage processing, oil and gas processing, and the pulp and paper industry. -
How do preheaters improve energy efficiency?
Preheaters improve energy efficiency by recovering heat that would otherwise be lost and reducing the amount of energy required to heat the substance in the main processing unit. -
What maintenance tasks are important for preheaters?
Important maintenance tasks for preheaters include regular cleaning, inspections for wear and damage, calibration of temperature sensors, and addressing common issues such as fouling, leaks, and corrosion.
In conclusion, preheaters are essential components in many industrial processes, serving to improve energy efficiency, reduce fuel consumption, increase production capacity, and improve product quality. By understanding the function, types, applications, and maintenance requirements of preheaters, industries can optimize their processes and minimize their environmental impact.
Leave a Reply