Factors Affecting Finished hole size
Several factors can influence the finished hole size, including:
- Drill bit diameter
- Material properties
- Drilling technique
- Drill bit wear
- Thermal expansion
Drill Bit Diameter
The diameter of the drill bit is the primary factor that determines the finished hole size. However, it’s important to note that the actual hole size may vary slightly from the nominal size of the drill bit due to various reasons, such as drill bit wear, runout, and material properties.
Material Properties
The properties of the material being drilled can also affect the finished hole size. Softer materials, such as wood or plastic, may experience more deformation during drilling, leading to slightly larger hole sizes. On the other hand, harder materials, like metals, may result in more precise hole sizes but can also cause drill bit wear more quickly.
Drilling Technique
The drilling technique employed can also impact the finished hole size. Factors such as feed rate, spindle speed, and drilling pressure can all contribute to variations in hole size. Maintaining a consistent and appropriate drilling technique is essential for achieving accurate and repeatable results.
Drill Bit Wear
As drill bits are used, they naturally experience wear and tear. Over time, this wear can lead to changes in the cutting edge geometry, resulting in slightly larger or less precise hole sizes. Regular inspection and replacement of worn drill bits are necessary to maintain consistent finished hole sizes.
Thermal Expansion
In some cases, the heat generated during the drilling process can cause thermal expansion of the material being drilled. This expansion can result in slight variations in the finished hole size, particularly in materials with high coefficients of thermal expansion, such as plastics.
Measuring Finished Hole Size
To ensure that the finished hole size meets the desired specifications, it’s essential to measure the hole accurately. There are several methods for measuring finished hole size, including:
- Calipers
- Gauge pins
- Bore gauges
- Coordinate measuring machines (CMMs)
Calipers
Calipers are a versatile and commonly used tool for measuring finished hole sizes. They come in two main types: vernier calipers and digital calipers. To measure a hole with calipers, follow these steps:
- Clean the hole and the caliper jaws to ensure accurate measurements.
- Open the caliper jaws and insert them into the hole, ensuring that they are perpendicular to the hole’s axis.
- Gently close the jaws until they contact the hole’s surface.
- Read the measurement on the caliper scale or digital display.
Gauge Pins
Gauge pins, also known as plug gauges, are cylindrical pins with precise diameters used to check hole sizes. To use a gauge pin:
- Select a gauge pin with a diameter slightly smaller than the desired hole size.
- Insert the gauge pin into the hole.
- If the pin fits snugly without forcing it, the hole is within the acceptable size range.
- If the pin is loose or doesn’t fit, select the next size up or down and repeat the process until the correct size is determined.
Bore Gauges
Bore gauges are specialized measuring tools designed for accurately measuring the internal diameter of holes. They consist of a graduated beam with a movable head and interchangeable anvils. To use a bore gauge:
- Select the appropriate anvil size for the hole being measured.
- Insert the bore gauge into the hole, ensuring that it is perpendicular to the hole’s axis.
- Adjust the movable head until the anvil contacts the hole’s surface.
- Read the measurement on the graduated beam.
Coordinate Measuring Machines (CMMs)
For high-precision applications, coordinate measuring machines (CMMs) can be used to measure finished hole sizes. CMMs use a probe to collect data points along the surface of the hole, creating a 3D model of the hole’s geometry. This data can then be analyzed to determine the hole’s diameter, roundness, and other geometric characteristics.
Controlling Finished Hole Size
To achieve consistent and accurate finished hole sizes, several strategies can be employed:
- Pilot holes and step drilling
- Reaming
- Honing
- Using the right drill bit
Pilot Holes and Step Drilling
When drilling larger holes, it’s often beneficial to start with a smaller pilot hole and then progressively enlarge the hole using a series of increasingly larger drill bits. This process, known as step drilling, helps to minimize drill bit deflection and ensures a more accurate finished hole size.
Reaming
Reaming is a secondary process that is performed after drilling to improve the hole’s size, geometry, and surface finish. Reamers are cutting tools with multiple cutting edges that remove small amounts of material from the hole’s surface, resulting in a more precise and consistent finished hole size.
Honing
Honing is another secondary process that is used to improve the surface finish and geometry of a hole. Honing tools, such as abrasive stones or brushes, are used to remove small amounts of material from the hole’s surface, resulting in a smoother and more precise finish.
Using the Right Drill Bit
Selecting the appropriate drill bit for the material being drilled and the desired hole size is crucial for achieving accurate results. Factors to consider when choosing a drill bit include:
- Material-specific coatings or geometries
- Flute design and chip evacuation capabilities
- Point angle and tip geometry
- Overall length and rigidity
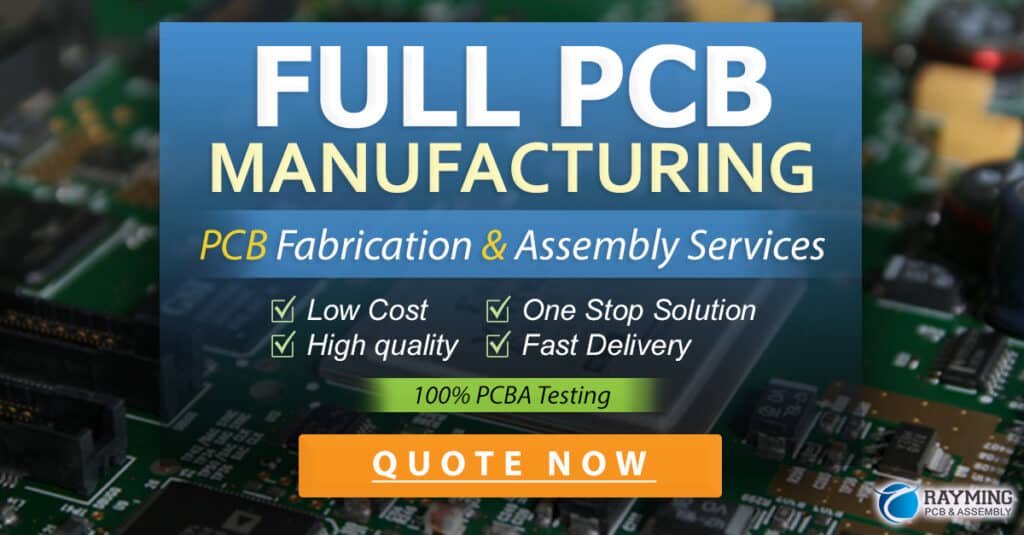
Common Finished Hole Size Applications
Finished hole size is a critical consideration in various industries and applications, including:
- Aerospace
- Automotive
- Construction
- Woodworking
- Plumbing
Aerospace
In the aerospace industry, precise hole sizes are essential for ensuring proper assembly and function of components. For example, holes drilled for fasteners must be within tight tolerances to ensure a secure and reliable connection between parts.
Automotive
Similar to the aerospace industry, the automotive sector requires accurate finished hole sizes for various components, such as engine blocks, transmission cases, and suspension systems. Proper hole sizes are crucial for ensuring correct fitment and operation of these components.
Construction
In construction applications, finished hole sizes are important for anchoring systems, plumbing installations, and electrical conduits. Accurately sized holes ensure that fasteners, pipes, and wires fit securely and safely.
Woodworking
Finished hole size is also critical in woodworking applications, such as dowel joinery, hinge installation, and hardware mounting. Precise hole sizes ensure proper alignment and a secure fit between components.
Plumbing
In plumbing applications, accurately sized holes are essential for installing pipes, fittings, and fixtures. Proper hole sizes help to prevent leaks and ensure a reliable and long-lasting plumbing system.
Frequently Asked Questions (FAQ)
- What is the difference between nominal and finished hole size?
-
Nominal hole size refers to the theoretical or designed size of the hole, while finished hole size is the actual measured size of the hole after drilling.
-
How can I ensure consistent finished hole sizes?
-
To ensure consistent finished hole sizes, use high-quality drill bits, maintain a consistent drilling technique, and regularly inspect and replace worn drill bits. Additionally, consider using secondary processes like reaming or honing to improve hole size consistency.
-
What is the best way to measure finished hole size?
-
The best way to measure finished hole size depends on the required accuracy and the application. For most general purposes, calipers or gauge pins are sufficient. For high-precision applications, bore gauges or coordinate measuring machines (CMMs) may be necessary.
-
How do I choose the right drill bit for a specific finished hole size?
-
When selecting a drill bit, consider factors such as the material being drilled, the desired hole size, and the required surface finish. Consult drill bit manufacturers’ recommendations or refer to machining handbooks for guidance on selecting the appropriate drill bit for your application.
-
What should I do if my finished hole size is out of tolerance?
- If your finished hole size is out of tolerance, first identify the root cause of the issue, such as drill bit wear, inconsistent drilling technique, or material variations. Then, take corrective actions, such as replacing the drill bit, adjusting the drilling parameters, or using secondary processes like reaming or honing to bring the hole size within the desired tolerance.
Conclusion
Understanding and controlling finished hole size is essential for ensuring proper fit, function, and reliability of components in various industries and applications. By considering factors such as drill bit selection, drilling technique, and material properties, and by employing appropriate measuring and secondary processing methods, manufacturers and craftsmen can achieve consistent and accurate finished hole sizes. As the demand for precision and quality continues to grow across industries, the importance of understanding and controlling finished hole size will only continue to increase.
Leave a Reply