Introduction to PCB Plating
Printed Circuit Boards (PCBs) are essential components in modern electronic devices. They provide a platform for mounting and interconnecting electronic components, allowing for the creation of complex circuits. PCB plating is a crucial process in the manufacturing of PCBs, as it ensures proper conductivity, durability, and reliability of the board. In this article, we will explore the differences between prepreg and core in PCB, and how they relate to the pcb plating process.
What is a PCB Core?
A PCB core is the base material used in the construction of a printed circuit board. It is typically made of a non-conductive substrate, such as fiberglass or epoxy resin, which provides the foundation for the copper layers and other components. The core is usually rigid and offers excellent dimensional stability, ensuring that the PCB maintains its shape and size throughout the manufacturing process and during its operational life.
Types of PCB Cores
There are several types of PCB cores available, each with its own unique properties and advantages:
-
FR-4: This is the most common type of PCB core, made from a composite material consisting of woven fiberglass cloth and epoxy resin. FR-4 offers good mechanical strength, electrical insulation, and heat resistance.
-
CEM-1: Composite Epoxy Material-1 (CEM-1) is a lower-cost alternative to FR-4, made from a combination of paper and epoxy resin. While not as durable as FR-4, CEM-1 is suitable for less demanding applications.
-
Polyimide: Polyimide cores are used in high-temperature applications, as they can withstand temperatures up to 260°C. They offer excellent thermal stability and chemical resistance, making them ideal for harsh environments.
-
Aluminum: Aluminum cores are used in applications that require excellent heat dissipation, such as high-power LED lighting or power electronics. The aluminum substrate helps to efficiently transfer heat away from the components, improving overall system performance and reliability.
The Role of PCB Cores in Plating
The PCB core plays a crucial role in the plating process, as it provides the foundation for the copper layers that will be deposited onto its surface. The quality and type of core used can significantly impact the final result of the plating process, as well as the overall performance of the PCB.
For example, using a high-quality FR-4 core ensures that the copper layers will adhere properly to the substrate, minimizing the risk of delamination or other defects. Additionally, the choice of core material can affect the PCB’s ability to dissipate heat, which is essential for maintaining the stability and reliability of the electronic components.
What is Prepreg in PCB?
Prepreg, short for “pre-impregnated,” is a material used in the construction of multi-layer PCBs. It consists of a thin, flexible sheet of fiberglass or other reinforcement material that is pre-impregnated with a partially cured epoxy resin. When heat and pressure are applied during the lamination process, the prepreg flows and bonds the individual layers of the PCB together, creating a strong, unified structure.
The Role of Prepreg in PCB Plating
Prepreg plays a vital role in the PCB plating process, particularly in the construction of multi-layer boards. By bonding the individual layers together, prepreg ensures that the PCB maintains its structural integrity and prevents the formation of voids or other defects that could compromise the board’s performance.
In addition to its bonding properties, prepreg also acts as an insulator between the conductive layers of the PCB. This is essential for preventing short circuits and ensuring proper signal integrity throughout the board.
Prepreg vs. Core: Key Differences
While both prepreg and core are essential components in the construction of a PCB, they serve different purposes and have distinct characteristics. Here are the key differences between prepreg and core:
-
Composition: PCB cores are typically made of rigid, non-conductive materials such as fiberglass or epoxy resin, while prepreg is a thin, flexible sheet of reinforcement material pre-impregnated with partially cured epoxy resin.
-
Function: The core provides the foundation for the copper layers and other components of the PCB, while prepreg is used to bond the individual layers together in a multi-layer board.
-
Rigidity: PCB cores are generally rigid, providing structural support for the board, while prepreg is flexible until it is fully cured during the lamination process.
-
Insulation: While both materials offer some level of electrical insulation, prepreg is specifically designed to act as an insulator between the conductive layers of a multi-layer PCB.
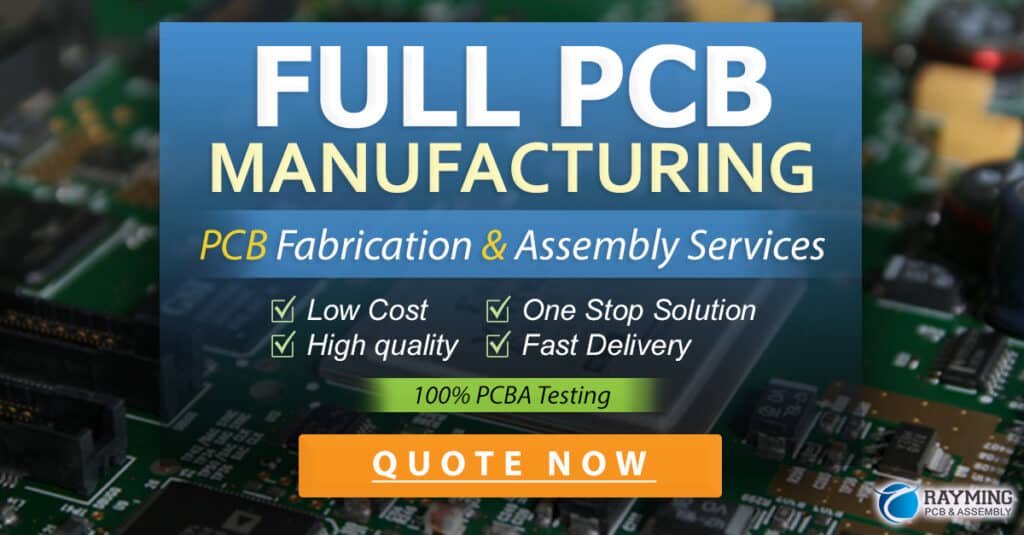
The PCB Plating Process
PCB plating is a multi-step process that involves depositing a thin layer of conductive material, typically copper, onto the surface of the PCB core. This process is essential for creating the electrical connections between components and ensuring proper signal transmission throughout the board.
Steps in the PCB Plating Process
-
Cleaning: The PCB core is thoroughly cleaned to remove any dirt, grease, or other contaminants that could interfere with the plating process.
-
Hole Drilling: Holes are drilled into the PCB core to accommodate component leads and vias, which are used to connect different layers of the board.
-
Desmear: A chemical or plasma process is used to remove any smear or debris from the drilled holes, ensuring a clean surface for plating.
-
Electroless Copper Deposition: A thin layer of copper is chemically deposited onto the surface of the PCB core and inside the drilled holes, providing a conductive base for the subsequent plating steps.
-
Electrolytic Copper Plating: The PCB is immersed in a copper sulfate solution, and an electric current is applied to deposit a thicker layer of copper onto the board’s surface and inside the holes.
-
Resist Application: A photoresist material is applied to the PCB and patterned using UV light exposure and development, creating a protective mask that defines the desired circuit pattern.
-
Etching: The exposed copper areas are removed using a chemical etching process, leaving only the desired circuit pattern on the board.
-
Resist Removal: The remaining photoresist is stripped away, revealing the final copper circuit pattern.
-
Finish Plating: Additional plating layers, such as nickel, gold, or tin, may be applied to the copper surfaces to improve solderability, corrosion resistance, or aesthetic appearance.
The Importance of PCB Plating
PCB plating is a critical process in the manufacturing of printed circuit boards, as it directly impacts the board’s functionality, reliability, and durability. Here are some of the key reasons why PCB plating is so important:
-
Conductivity: The plating process creates the conductive pathways that allow electrical signals to travel between components on the PCB. Without proper plating, the board would not function as intended.
-
Durability: The plated copper layers provide a robust and durable surface for component attachment and help to protect the board from environmental factors such as moisture, corrosion, and wear.
-
Signal Integrity: High-quality plating ensures that electrical signals can travel through the board with minimal loss or distortion, maintaining signal integrity and overall system performance.
-
Reliability: Properly plated PCBs are less likely to experience failures or malfunctions due to issues such as poor connections, corrosion, or delamination, resulting in a more reliable end product.
Factors Affecting PCB Plating Quality
Several factors can influence the quality of the PCB plating process, ultimately impacting the performance and reliability of the finished board. These factors include:
-
Surface Preparation: Proper cleaning and preparation of the PCB core surface prior to plating is essential for ensuring good adhesion and uniformity of the deposited copper layers.
-
Plating Bath Composition: The chemistry of the plating bath, including the concentration of copper ions, additives, and other components, must be carefully controlled to achieve consistent and high-quality plating results.
-
Current Density: The amount of electric current applied during the electrolytic plating process can affect the thickness, uniformity, and grain structure of the deposited copper layer.
-
Temperature: Maintaining the proper temperature of the plating bath is crucial for controlling the rate of copper deposition and ensuring consistent plating quality.
-
Agitation: Adequate agitation of the plating bath helps to maintain a uniform distribution of copper ions and prevents the formation of nodules or other defects on the plated surface.
-
Contamination: Any contaminants present in the plating bath or on the PCB surface can lead to defects or poor plating quality, so maintaining a clean and controlled environment is essential.
PCB Plating Defects and Troubleshooting
Despite careful process control, various defects can occur during the PCB plating process. Some common plating defects include:
-
Nodules: Small, ball-like protrusions on the plated surface, often caused by contaminants or uneven current distribution.
-
Voids: Gaps or missing areas in the plated copper layer, typically caused by poor surface preparation or inadequate hole cleaning.
-
Thin Plating: Insufficient copper thickness, resulting from low current density, short plating time, or poor bath composition.
-
Rough Plating: An uneven or granular plated surface, often caused by excessive current density or poor bath chemistry control.
-
Delamination: Separation of the plated copper layer from the PCB core, usually due to poor surface preparation or contamination.
To troubleshoot and prevent these defects, PCB manufacturers must maintain strict process controls, regularly monitor and adjust plating parameters, and conduct thorough quality inspections throughout the production process.
Advanced PCB Plating Techniques
As electronic devices become more complex and demanding, PCB manufacturers are continuously developing new and advanced plating techniques to improve board performance and reliability. Some of these advanced techniques include:
-
High Aspect Ratio Plating: This technique enables the plating of very small, deep holes in high-density PCBs, ensuring reliable connections between layers.
-
Selective Plating: By using specialized masking and plating processes, manufacturers can selectively plate specific areas of the PCB, reducing material usage and improving design flexibility.
-
Embedded Trace Plating: This technique involves plating copper traces directly into the PCB substrate, allowing for higher circuit densities and improved signal integrity.
-
Semi-Additive Processing (SAP): SAP is an advanced plating method that enables the creation of very fine, high-density circuit patterns, making it ideal for miniaturized electronic devices.
As these and other advanced plating techniques continue to evolve, PCBs will become even more capable of meeting the demands of cutting-edge electronic applications.
Conclusion
In summary, understanding the differences between prepreg and core in PCB, as well as the role they play in the PCB plating process, is essential for designing and manufacturing high-quality printed circuit boards. By carefully selecting the appropriate materials, controlling the plating process parameters, and employing advanced techniques when necessary, PCB manufacturers can ensure that their boards meet the ever-increasing demands of modern electronic devices.
As the electronics industry continues to evolve, it is likely that new materials, processes, and techniques will emerge to further enhance the performance and reliability of PCBs. By staying up-to-date with these developments and continuously improving their manufacturing processes, PCB manufacturers can remain competitive and deliver the high-quality products that their customers demand.
Frequently Asked Questions (FAQ)
- What is the primary difference between prepreg and core in PCB?
-
The primary difference between prepreg and core in PCB is their composition and function. PCB cores are rigid, non-conductive materials that provide the foundation for the copper layers and components, while prepreg is a thin, flexible sheet of reinforcement material pre-impregnated with partially cured epoxy resin used to bond the layers together in multi-layer PCBs.
-
Why is PCB plating important?
-
PCB plating is important because it creates the conductive pathways that allow electrical signals to travel between components on the board, provides durability and protection against environmental factors, ensures signal integrity, and improves the overall reliability of the finished product.
-
What are some common defects that can occur during the PCB plating process?
-
Common defects that can occur during the PCB plating process include nodules, voids, thin plating, rough plating, and delamination. These defects can be caused by various factors, such as poor surface preparation, contamination, or improper control of plating parameters.
-
How can PCB manufacturers troubleshoot and prevent plating defects?
-
To troubleshoot and prevent plating defects, PCB manufacturers must maintain strict process controls, regularly monitor and adjust plating parameters, and conduct thorough quality inspections throughout the production process. This includes ensuring proper surface preparation, maintaining the correct plating bath composition, and controlling factors such as current density, temperature, and agitation.
-
What are some advanced PCB plating techniques, and how do they benefit the electronics industry?
- Advanced PCB plating techniques include high aspect ratio plating, selective plating, embedded trace plating, and semi-additive processing (SAP). These techniques enable the creation of high-density, miniaturized PCBs with improved signal integrity and reliability, allowing for the development of more complex and advanced electronic devices.
PCB Component | Composition | Function |
---|---|---|
Core | Rigid, non-conductive materials (e.g., fiberglass, epoxy resin) | Provides the foundation for copper layers and components |
Prepreg | Thin, flexible sheet of reinforcement material pre-impregnated with partially cured epoxy resin | Bonds the layers together in multi-layer PCBs |
PCB Plating Defect | Description | Causes |
---|---|---|
Nodules | Small, ball-like protrusions on the plated surface | Contaminants or uneven current distribution |
Voids | Gaps or missing areas in the plated copper layer | Poor surface preparation or inadequate hole cleaning |
Thin Plating | Insufficient copper thickness | Low current density, short plating time, or poor bath composition |
Rough Plating | Uneven or granular plated surface | Excessive current density or poor bath chemistry control |
Delamination | Separation of the plated copper layer from the PCB core | Poor surface preparation or contamination |
Leave a Reply