What is a PCB?
A PCB, or Printed Circuit Board, is a flat board made of insulating material, such as fiberglass or plastic, with conductive pathways printed or etched onto its surface. These pathways, also known as traces, connect various electronic components together to form a complete circuit.
PCBs are the foundation of modern electronics and are used in a wide range of applications, from simple consumer devices to complex industrial equipment. They provide a stable and reliable platform for electronic components to be mounted and interconnected, allowing for the creation of compact and efficient electronic systems.
Types of PCBs
There are several types of PCBs, each with its own unique characteristics and applications:
-
Single-sided PCB: A single-sided PCB has conductive traces on only one side of the board. These are the simplest and most cost-effective PCBs, often used in basic electronic devices.
-
Double-sided PCB: A double-sided PCB has conductive traces on both sides of the board, allowing for more complex circuits and higher component density. The two sides are connected using through-hole technology or vias.
-
Multi-layer PCB: A multi-layer PCB consists of three or more layers of conductive traces, separated by insulating layers. These PCBs offer the highest level of complexity and density, making them suitable for advanced electronic systems.
-
Flexible PCB: A flexible PCB is made from a thin, flexible insulating material, allowing the board to bend and conform to various shapes. These PCBs are often used in applications where space is limited or where the device needs to be flexible.
-
Rigid-Flex PCB: A rigid-flex PCB combines the features of both rigid and flexible PCBs, with rigid sections for mounting components and flexible sections for connecting them. This type of PCB is used in applications that require both stability and flexibility.
PCB Manufacturing Process
The PCB manufacturing process involves several steps, each of which is critical to ensuring the quality and reliability of the final product. The main steps in the PCB manufacturing process are:
-
Design: The PCB design is created using specialized software, such as Altium Designer or Eagle. The design includes the layout of the conductive traces, the placement of components, and the creation of the Gerber files used for manufacturing.
-
Printing: The PCB design is printed onto a copper-clad laminate using a process called photolithography. This involves applying a photoresist layer to the copper, exposing it to UV light through a photomask, and then developing the resist to remove the unexposed areas.
-
Etching: The exposed copper is then etched away using a chemical solution, leaving only the desired conductive traces on the board.
-
Drilling: Holes are drilled into the PCB to allow for the mounting of components and the creation of vias, which connect the layers of a multi-layer PCB.
-
Plating: The holes are then plated with a conductive material, such as copper, to ensure proper electrical connectivity.
-
Silkscreening: The component labels, logos, and other markings are printed onto the PCB using a silkscreening process.
-
Surface Finishing: A surface finish, such as HASL (Hot Air Solder Leveling) or ENIG (Electroless Nickel Immersion Gold), is applied to the PCB to protect the copper traces and improve solderability.
-
Quality Control: The PCB undergoes a series of quality control tests to ensure that it meets the required specifications and is free from defects.
What is a PCBA?
A PCBA, or Printed Circuit Board Assembly, is a PCB that has been populated with electronic components and tested to ensure proper functionality. In other words, a PCBA is a completed electronic assembly that includes both the PCB and the components mounted on it.
The process of assembling a PCBA involves several steps, including component placement, soldering, and testing. The components are typically mounted onto the PCB using one of two methods: through-hole mounting or surface mount technology (SMT).
Through-Hole Mounting
Through-hole mounting involves inserting the leads of the components through pre-drilled holes in the PCB and soldering them to the conductive traces on the opposite side. This method is often used for larger components or those that require more mechanical stability.
Surface Mount Technology (SMT)
SMT involves placing the components directly onto the surface of the PCB and soldering them to the conductive traces using a reflow soldering process. This method allows for smaller components and higher component density, making it the preferred choice for most modern electronic devices.
PCBA Manufacturing Process
The PCBA manufacturing process involves several steps, each of which is critical to ensuring the quality and reliability of the final product. The main steps in the PCBA manufacturing process are:
-
Solder Paste Application: A thin layer of solder paste is applied to the PCB using a stencil or screen printing process. The solder paste consists of tiny solder balls suspended in a flux medium, which helps to clean and protect the metal surfaces during soldering.
-
Component Placement: The electronic components are placed onto the PCB using a pick-and-place machine. This machine uses a vacuum nozzle to pick up the components from a tape reel or tray and place them onto the pre-programmed locations on the PCB.
-
Reflow Soldering: The PCB is then passed through a reflow oven, which heats the board to a specific temperature profile, causing the solder paste to melt and form a permanent electrical and mechanical connection between the components and the PCB.
-
Inspection: The assembled pcbA undergoes a visual inspection to check for any visible defects, such as misaligned components or solder bridges.
-
Testing: The PCBA is then subjected to various electrical tests to ensure proper functionality. These tests may include in-circuit testing (ICT), flying probe testing, or functional testing.
-
Conformal Coating: In some cases, a conformal coating may be applied to the PCBA to protect it from environmental factors such as moisture, dust, or chemical contamination.
-
Final Assembly: The tested and approved PCBA is then integrated into the final product or packaging, depending on the application.
Differences Between PCB and PCBA
Now that we have a better understanding of what PCBs and PCBAs are and how they are manufactured, let’s summarize the key differences between them:
Factor | PCB | PCBA |
---|---|---|
Definition | A bare board with conductive traces and no components | A PCB populated with electronic components and tested for functionality |
Components | None | Includes electronic components such as resistors, capacitors, ICs, and connectors |
Manufacturing Process | Design, printing, etching, drilling, plating, silkscreening, and finishing | Includes PCB manufacturing steps plus component placement, soldering, and testing |
Functionality | Not functional on its own, requires components to be added | A complete, functional electronic assembly |
Testing | Limited to visual inspection and continuity testing | Undergoes comprehensive electrical and functional testing |
Applications | Used as a base for electronic assemblies | Used in a wide range of electronic devices and systems |
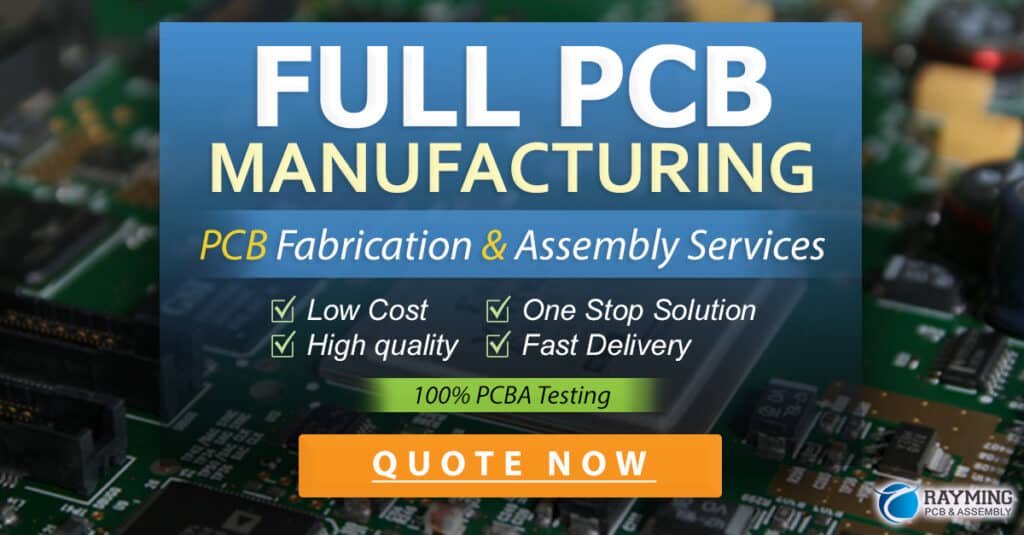
Applications of PCBs and PCBAs
PCBs and PCBAs are used in a wide range of applications across various industries. Some common applications include:
-
Consumer Electronics: PCBs and PCBAs are found in smartphones, tablets, laptops, televisions, and other household electronic devices.
-
Automotive Electronics: Modern vehicles rely heavily on electronic systems, such as engine control units, infotainment systems, and advanced driver assistance systems (ADAS), all of which utilize PCBs and PCBAs.
-
Medical Devices: PCBs and PCBAs are used in various medical devices, including patient monitors, imaging equipment, and implantable devices.
-
Industrial Equipment: Industrial automation, process control, and monitoring systems often rely on PCBs and PCBAs for reliable and efficient operation.
-
Aerospace and Defense: PCBs and PCBAs are used in a wide range of aerospace and defense applications, such as avionics, radar systems, and military communication equipment.
-
IoT Devices: The Internet of Things (IoT) has led to a proliferation of connected devices, each of which requires a PCB or PCBA to function.
Frequently Asked Questions (FAQ)
-
Q: Can a PCB function without components?
A: No, a PCB is merely a substrate with conductive traces and requires electronic components to be mounted on it to function as a complete electronic assembly. -
Q: Is it possible to repair a damaged PCBA?
A: In some cases, a damaged PCBA can be repaired by replacing faulty components or resoldering broken connections. However, the feasibility of repair depends on the extent of the damage and the complexity of the assembly. -
Q: What is the difference between through-hole and surface mount components?
A: Through-hole components have leads that are inserted into pre-drilled holes in the PCB and soldered to the opposite side, while surface mount components are placed directly onto the surface of the PCB and soldered using a reflow soldering process. -
Q: What is the purpose of a conformal coating on a PCBA?
A: A conformal coating is a thin, protective layer applied to a PCBA to protect it from environmental factors such as moisture, dust, or chemical contamination, thus improving its reliability and longevity. -
Q: How are PCBs and PCBAs tested for functionality?
A: PCBs are typically tested for continuity and visual defects, while PCBAs undergo more comprehensive testing, including in-circuit testing (ICT), flying probe testing, and functional testing to ensure proper operation and performance.
Conclusion
In summary, while PCBs and PCBAs are closely related, they represent different stages in the electronics manufacturing process. A PCB is a bare board with conductive traces that serves as the foundation for an electronic assembly, while a PCBA is a fully populated and tested board that includes both the PCB and the mounted components.
Understanding the differences between PCBs and PCBAs is essential for anyone involved in electronics design, manufacturing, or procurement. By recognizing the unique characteristics and manufacturing processes of each, you can make informed decisions when selecting the appropriate solution for your specific application.
As technology continues to advance, the demand for high-quality, reliable PCBs and PCBAs will only continue to grow. By staying informed about the latest developments and best practices in the industry, you can ensure that your electronic products meet the highest standards of performance and reliability.
Leave a Reply