Overview of PCB Manufacturing
PCB manufacturing is the process of creating the bare printed circuit board, which serves as the foundation for electronic components. The manufacturing process involves several steps, including:
- Design and layout
- Material selection
- Fabrication
- Inspection and testing
Design and Layout
The first step in PCB manufacturing is the design and layout of the circuit board. This process involves creating a schematic diagram of the electronic circuit and converting it into a physical layout using specialized software. The layout determines the placement of components, traces, and vias on the PCB.
Material Selection
PCBs can be made from various materials, depending on the application and performance requirements. The most common base material is FR-4, a glass-reinforced epoxy laminate. Other materials include polyimide, ceramic, and metal-core substrates for high-temperature or high-power applications.
Fabrication
The fabrication process involves several steps, including:
- Printing the circuit pattern onto the copper-clad laminate using photolithography
- Etching away the unwanted copper to create the traces
- Drilling holes for through-hole components and vias
- Applying solder mask and silkscreen for protection and labeling
Inspection and Testing
After fabrication, the bare PCBs undergo thorough inspection and testing to ensure they meet the required specifications. This includes visual inspection, electrical testing, and automated optical inspection (AOI) to detect any defects or inconsistencies.
Overview of PCB Assembly
PCB assembly is the process of populating the bare PCB with electronic components and creating a functional circuit board. The assembly process involves several steps, including:
- Component placement
- Soldering
- Inspection and testing
- Conformal coating (optional)
Component Placement
The first step in PCB assembly is placing the electronic components onto the bare PCB. This can be done manually for low-volume production or using automated pick-and-place machines for high-volume production. The components are placed according to the PCB layout, ensuring proper orientation and alignment.
Soldering
After component placement, the PCB undergoes soldering to create electrical connections between the components and the traces. There are two main soldering methods:
- Through-hole soldering: Components with long leads are inserted through holes in the PCB and soldered on the opposite side.
- Surface-mount soldering: Components with flat leads or terminations are soldered directly onto the surface of the PCB.
Soldering can be done manually using a soldering iron or automatically using wave soldering or reflow soldering machines.
Inspection and Testing
After soldering, the assembled PCBs undergo inspection and testing to ensure proper functionality and quality. This includes visual inspection, automated optical inspection (AOI), and in-circuit testing (ICT) to verify the presence and correct placement of components, as well as the integrity of solder joints.
Conformal Coating (Optional)
In some cases, assembled PCBs may require conformal coating for added protection against environmental factors such as moisture, dust, and chemicals. Conformal coating is a thin layer of polymer applied to the surface of the PCB, covering the components and traces.
Key Differences between PCB Manufacturing and Assembly
Aspect | PCB Manufacturing | PCB Assembly |
---|---|---|
Focus | Creating the bare PCB | Populating the PCB with components |
Steps | Design, material selection, fabrication, inspection | Component placement, soldering, inspection, conformal coating |
Equipment | Photolithography, etching, drilling machines | Pick-and-place machines, soldering equipment, inspection systems |
Outcome | Bare PCB without components | Functional PCB with components |
Skill Set | Knowledge of PCB materials, fabrication processes, and quality control | Knowledge of component handling, soldering techniques, and testing methods |
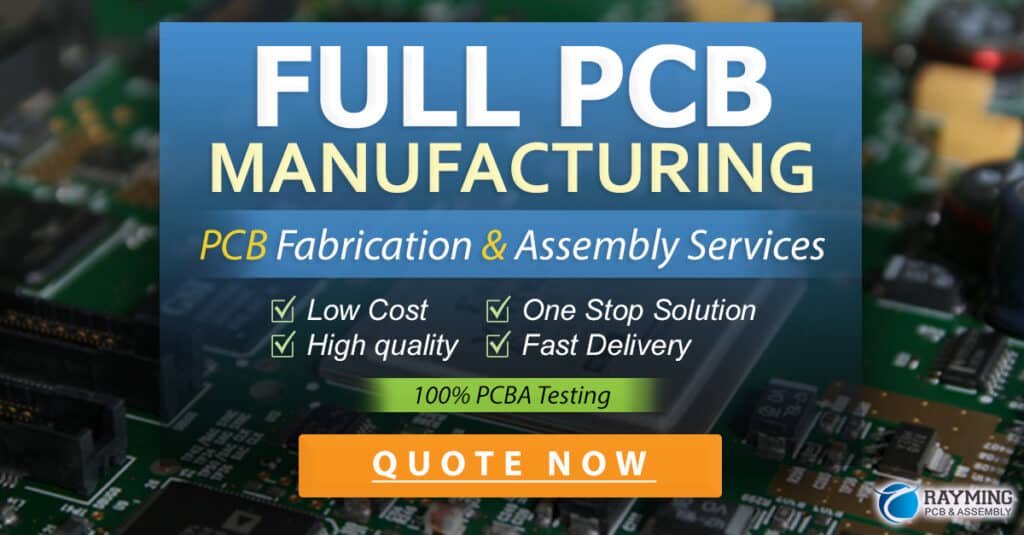
Importance of Understanding the Difference
Understanding the difference between PCB manufacturing and assembly is crucial for several reasons:
- Project planning: Knowing the distinct stages and lead times involved in manufacturing and assembly helps in effective project planning and scheduling.
- Cost estimation: Accurate cost estimation requires a clear understanding of the costs associated with each process, including materials, labor, and equipment.
- Quality control: Identifying potential issues and implementing quality control measures are more effective when the specific challenges of each process are understood.
- Communication: Clear communication between design, manufacturing, and assembly teams is essential for successful PCB production, and a shared understanding of the processes facilitates this communication.
Frequently Asked Questions (FAQ)
1. Can PCB manufacturing and assembly be done by the same company?
Yes, many companies offer both PCB manufacturing and assembly services, providing a one-stop solution for customers. This can streamline the production process and reduce lead times.
2. What is the typical turnaround time for PCB manufacturing and assembly?
Turnaround times vary depending on the complexity of the PCB, the volume of the order, and the capacity of the manufacturer. Typical turnaround times range from a few days to several weeks. Rush services may be available at a higher cost.
3. How do I choose between through-hole and surface-mount assembly?
The choice between through-hole and surface-mount assembly depends on factors such as component availability, PCB size constraints, performance requirements, and production volume. Surface-mount assembly is generally more cost-effective and space-efficient for high-volume production, while through-hole assembly may be preferred for larger components or lower-volume projects.
4. What are the common challenges in PCB manufacturing and assembly?
Common challenges in PCB manufacturing include maintaining tight tolerances, managing signal integrity, and ensuring reliable plating and etching processes. In PCB assembly, challenges include proper component placement, achieving consistent solder joint quality, and preventing damage to sensitive components during handling and soldering.
5. How can I ensure the quality of my PCB manufacturing and assembly?
To ensure the quality of PCB manufacturing and assembly, consider the following:
- Choose a reputable manufacturer with a proven track record and relevant certifications (e.g., ISO, IPC).
- Provide clear and accurate design files and specifications.
- Communicate regularly with your manufacturer and assembly team to address any issues or concerns.
- Implement thorough inspection and testing procedures at various stages of the process.
- Establish a quality assurance plan and monitor key performance indicators (KPIs) to continuously improve the process.
Conclusion
PCB manufacturing and assembly are two distinct but interconnected processes in the production of electronic devices. PCB manufacturing focuses on creating the bare circuit board, while assembly involves populating the board with components and creating a functional unit. Understanding the difference between these processes is essential for effective project planning, cost estimation, quality control, and communication within the electronics industry.
By recognizing the unique challenges and requirements of each process, manufacturers, designers, and engineers can collaborate more effectively to produce high-quality, reliable PCBs. As technology advances and electronic devices become increasingly complex, a deep understanding of PCB manufacturing and assembly will remain crucial for success in the industry.
Leave a Reply