Understanding CPL and BoM
When it comes to manufacturing and supply chain management, two important concepts are often discussed: the Cost of Poor Quality (CPL) and the Bill of Materials (BoM). While both play crucial roles in optimizing production processes and ensuring product quality, they serve distinct purposes. In this article, we will delve into the differences between CPL and BoM, exploring their definitions, applications, and the ways in which they contribute to the success of manufacturing operations.
What is CPL?
CPL, or Cost of Poor Quality, is a financial metric that quantifies the costs incurred by a company due to quality issues, defects, and non-conformances in their products or processes. It encompasses all expenses associated with preventing, detecting, and rectifying quality problems, as well as the costs of customer dissatisfaction and lost opportunities resulting from subpar quality.
The CPL can be broken down into four main categories:
-
Prevention Costs: Expenses related to activities designed to prevent quality issues from occurring, such as quality planning, training, and process improvement initiatives.
-
Appraisal Costs: Costs associated with measuring, evaluating, and auditing products or processes to ensure conformance to quality standards, including inspection, testing, and calibration.
-
Internal Failure Costs: Expenses incurred when defects or non-conformances are detected before the product reaches the customer, such as scrap, rework, and redesign costs.
-
External Failure Costs: Costs that arise when quality issues are discovered after the product has been delivered to the customer, including warranty claims, returns, and damage to brand reputation.
By tracking and analyzing CPL, companies can identify areas for improvement, prioritize quality initiatives, and ultimately reduce the overall cost of poor quality.
What is BoM?
BoM, or Bill of Materials, is a comprehensive list of all the raw materials, sub-assemblies, intermediate assemblies, sub-components, parts, and the quantities of each needed to manufacture a product. It serves as a blueprint for the production process, ensuring that all necessary components are available and accurately accounted for.
A typical BoM includes the following information:
-
Part Numbers: Unique identifiers for each component or sub-assembly.
-
Part Descriptions: Detailed descriptions of each item, including specifications and characteristics.
-
Quantities: The number of each component required to produce one unit of the finished product.
-
Unit of Measure: The standard unit in which each component is measured (e.g., pieces, liters, kilograms).
-
Procurement Type: Indicates whether a component is manufactured in-house, purchased from a supplier, or a combination of both.
The BoM is an essential tool for various departments within a manufacturing organization, including engineering, procurement, production, and quality control. It ensures effective communication and coordination among these teams, facilitating efficient resource planning, inventory management, and production scheduling.
Key Differences between CPL and BoM
While both CPL and BoM are important concepts in manufacturing, they serve different purposes and have distinct characteristics. The following table highlights the key differences between CPL and BoM:
Aspect | CPL (Cost of Poor Quality) | BoM (Bill of Materials) |
---|---|---|
Definition | Financial metric that quantifies the costs incurred due to quality issues and non-conformances | Comprehensive list of raw materials, sub-assemblies, and components needed to manufacture a product |
Purpose | Identifies and measures the financial impact of quality problems to drive continuous improvement | Serves as a blueprint for the production process, ensuring accurate component tracking and resource planning |
Focus | Quality management and cost reduction | Product structure and component management |
Scope | Encompasses prevention, appraisal, internal failure, and external failure costs | Covers all components and sub-assemblies required to produce a finished product |
Application | Used by quality, finance, and management teams to prioritize quality initiatives and measure their effectiveness | Used by engineering, procurement, production, and quality control teams to ensure efficient production and inventory management |
Timing | Calculated and analyzed periodically (e.g., monthly, quarterly) | Created during the product design phase and updated throughout the product lifecycle |
Impact | Helps identify and eliminate sources of quality-related costs, improving profitability and customer satisfaction | Ensures accurate production planning, inventory control, and cost estimation, contributing to overall operational efficiency |
Importance of CPL and BoM in Manufacturing
Both CPL and BoM play vital roles in optimizing manufacturing processes, improving product quality, and ultimately driving business success. Let’s explore the importance of each concept in more detail.
The Significance of CPL
-
Financial Impact: By identifying and quantifying the costs associated with quality issues, CPL helps companies understand the financial burden of poor quality. This information enables them to make informed decisions about investing in quality improvement initiatives and prioritizing resources effectively.
-
Continuous Improvement: CPL serves as a key performance indicator (KPI) for quality management. By tracking CPL over time, companies can measure the effectiveness of their quality improvement efforts and identify areas that require further attention. This data-driven approach facilitates continuous improvement and helps organizations stay competitive in their respective markets.
-
Customer Satisfaction: Reducing CPL directly contributes to improved product quality and customer satisfaction. By minimizing defects, rework, and delays, companies can deliver high-quality products consistently, enhancing customer loyalty and brand reputation. This, in turn, can lead to increased sales, market share, and long-term business growth.
-
Operational Efficiency: Addressing the root causes of quality issues identified through CPL analysis can streamline production processes, reduce waste, and improve overall operational efficiency. By eliminating non-value-added activities and optimizing resource utilization, companies can achieve significant cost savings and boost productivity.
The Importance of BoM
-
Product Consistency: A well-structured and accurate BoM ensures that all necessary components are included in the production process, resulting in consistent product quality. By providing a clear and comprehensive list of required materials, the BoM minimizes the risk of errors, omissions, or variations that could lead to quality issues or production delays.
-
Inventory Management: The BoM serves as the foundation for effective inventory management. By accurately specifying the quantities and types of components needed for production, the BoM enables companies to maintain optimal inventory levels, avoiding stockouts or excess inventory. This helps reduce carrying costs, minimize obsolescence, and improve cash flow.
-
Procurement and Sourcing: The BoM provides essential information for procurement and sourcing activities. It helps identify the materials and components that need to be purchased, along with their specifications and quantities. This information enables companies to negotiate better prices with suppliers, establish long-term contracts, and ensure a stable supply of quality materials.
-
Production Planning and Scheduling: The BoM is a crucial input for production planning and scheduling. By knowing the exact components required for each product, production managers can effectively allocate resources, optimize production sequences, and minimize changeover times. This leads to improved production efficiency, reduced lead times, and better on-time delivery performance.
-
Cost Control and Estimation: An accurate BoM allows companies to precisely estimate the cost of producing a product. By considering the prices of individual components, along with labor and overhead costs, companies can develop accurate cost models and make informed pricing decisions. This helps maintain profitability, identify cost reduction opportunities, and remain competitive in the market.
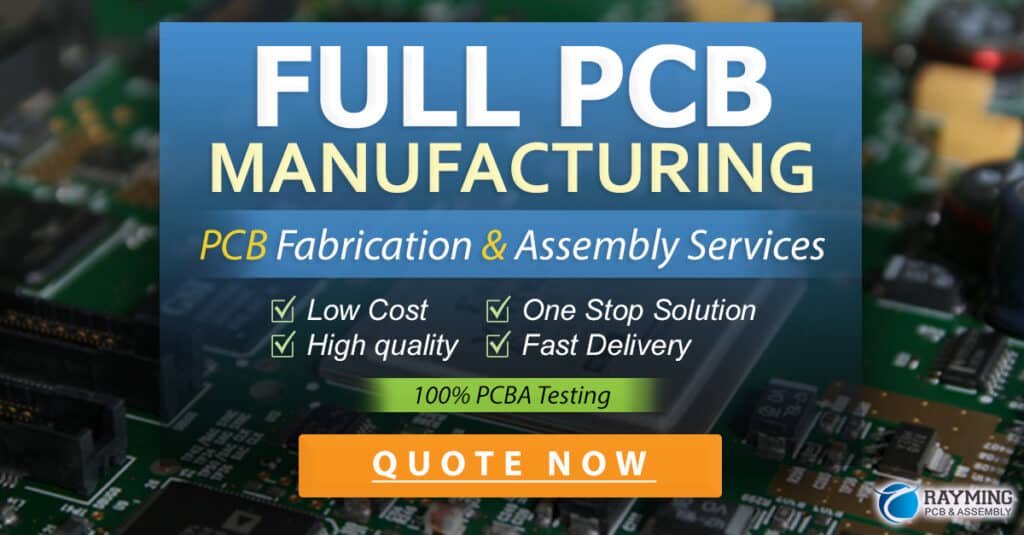
Integrating CPL and BoM for Optimal Results
While CPL and BoM serve different purposes, integrating them can lead to significant benefits for manufacturing organizations. By combining the insights gained from CPL analysis with the structured information provided by the BoM, companies can achieve a more holistic approach to quality management and operational excellence.
Here are some ways in which CPL and BoM can be integrated:
-
Quality-Driven BoM Design: When creating or updating the BoM, consider the insights gained from CPL analysis. Identify components or sub-assemblies that have historically contributed to quality issues and explore alternative designs or materials that could improve reliability and reduce defects. By proactively addressing quality concerns during the BoM design phase, companies can prevent costly quality issues down the line.
-
Supplier Quality Management: Use CPL data to evaluate and manage supplier performance. Identify suppliers whose components consistently contribute to quality issues and work closely with them to implement corrective actions. Incorporate supplier quality metrics into the BoM, enabling better visibility and control over the quality of purchased materials.
-
Continuous Improvement Initiatives: Leverage CPL analysis to identify areas for continuous improvement in the production process. Use the BoM as a reference to pinpoint specific components, sub-assemblies, or process steps that require attention. By focusing improvement efforts on these critical areas, companies can effectively reduce CPL and enhance overall product quality.
-
Integrated Quality and Production Planning: Incorporate CPL considerations into production planning and scheduling. Prioritize the production of high-quality components and sub-assemblies, as identified by the BoM, to minimize the risk of quality issues downstream. Allocate additional quality control resources to critical components and implement in-process inspections to catch defects early.
-
Cross-Functional Collaboration: Foster collaboration between quality, engineering, procurement, and production teams using the BoM as a common language. Encourage open communication and data sharing to ensure that quality considerations are integrated throughout the product development and manufacturing processes. This collaborative approach helps break down silos and promotes a quality-centric culture.
Frequently Asked Questions (FAQ)
-
What is the difference between prevention and appraisal costs in CPL?
Prevention costs are expenses incurred to prevent quality issues from occurring, such as quality planning and training. Appraisal costs, on the other hand, are associated with measuring and evaluating products or processes to ensure conformance to quality standards, such as inspection and testing. -
Can a BoM be changed after production has started?
Yes, a BoM can be revised or updated throughout the product lifecycle. Changes may be necessary due to design modifications, component obsolescence, or quality improvements. However, any changes to the BoM should be carefully controlled and communicated to all relevant stakeholders to ensure smooth production and avoid disruptions. -
How does CPL impact customer satisfaction?
High CPL indicates frequent quality issues, defects, and non-conformances, which can lead to customer dissatisfaction. By reducing CPL, companies can deliver higher-quality products consistently, meeting or exceeding customer expectations. This, in turn, enhances customer loyalty, brand reputation, and overall customer satisfaction. -
What is the role of the BoM in inventory management?
The BoM provides a detailed list of all components and their required quantities to produce a finished product. This information is crucial for effective inventory management. By accurately tracking and planning inventory based on the BoM, companies can maintain optimal stock levels, minimize stockouts, and reduce excess inventory, ultimately improving inventory turnover and reducing carrying costs. -
How can CPL and BoM be used together for continuous improvement?
CPL analysis helps identify areas where quality issues occur, while the BoM provides a structured view of the product’s components and sub-assemblies. By combining these insights, companies can focus continuous improvement efforts on specific components or processes that contribute to high CPL. This targeted approach helps prioritize resources, implement effective corrective actions, and drive ongoing quality enhancements.
Conclusion
In conclusion, CPL and BoM are two distinct but equally important concepts in manufacturing. CPL focuses on measuring and reducing the costs associated with quality issues, while BoM provides a comprehensive structure for product components and materials. Understanding the differences between CPL and BoM, as well as their respective roles in driving quality, efficiency, and profitability, is crucial for manufacturing organizations.
By leveraging CPL analysis to identify quality improvement opportunities and using the BoM as a foundation for product consistency, inventory management, and production planning, companies can optimize their operations and achieve sustainable business success. Integrating CPL and BoM through quality-driven design, supplier management, continuous improvement initiatives, and cross-functional collaboration further enhances the benefits of these powerful tools.
As manufacturing organizations strive to remain competitive in today’s dynamic market, effectively managing CPL and BoM becomes increasingly critical. By embracing these concepts and adapting them to their specific needs, companies can unlock the full potential of their operations, deliver exceptional products, and satisfy customers while maintaining a strong bottom line.
Leave a Reply