Introduction
The dielectric constant, also known as the relative permittivity, is a critical property of the insulating materials used in printed circuit boards (PCBs). It plays a significant role in determining the electrical performance and signal integrity of PCBs, especially at high frequencies. In this article, we’ll dive deep into the concept of PCB dielectric constant, its importance, factors affecting it, and how it impacts PCB design and performance.
Understanding the Basics
What is a Dielectric Material?
A dielectric material is an electrical insulator that can be polarized by an applied electric field. When placed in an electric field, the electric charges within the dielectric material do not flow through the material as they do in a conductor but only slightly shift from their average equilibrium positions, causing dielectric polarization.
Definition of Dielectric Constant
The dielectric constant (Dk) is a measure of a material’s ability to store electrical energy in an electric field. It is the ratio of the permittivity of a substance to the permittivity of free space. The dielectric constant is a dimensionless quantity and is always greater than or equal to 1.
Mathematically, the dielectric constant is expressed as:
Dk = ε / ε₀
Where:
– Dk is the dielectric constant
– ε is the permittivity of the material
– ε₀ is the permittivity of free space (8.854 × 10⁻¹² F/m)
Importance of Dielectric Constant in PCBs
The dielectric constant is a crucial parameter in PCB design because it affects several aspects of the board’s performance, including:
- Signal propagation speed
- Characteristic impedance
- Capacitance
- Signal integrity
- Electromagnetic compatibility (EMC)
A lower dielectric constant results in faster signal propagation, lower capacitance, and better signal integrity, which are essential for high-speed and high-frequency applications.
Factors Affecting PCB Dielectric Constant
Several factors can influence the dielectric constant of a PCB substrate material. Understanding these factors is essential for selecting the appropriate material for a specific application.
Material Composition
The chemical composition of the dielectric material is the primary factor determining its dielectric constant. Different materials have varying dielectric constants due to their unique molecular structures and polarizability.
Some common PCB substrate materials and their typical dielectric constants include:
Material | Dielectric Constant (Dk) |
---|---|
FR-4 | 4.2 – 4.5 |
Rogers RO4003C | 3.38 |
Rogers RT/duroid 5880 | 2.20 |
Isola IS410 | 3.65 |
Polyimide | 3.5 |
PTFE (Teflon) | 2.1 |
Frequency
The dielectric constant of a material can vary with frequency, especially at high frequencies. This variation is due to the frequency-dependent polarization mechanisms within the material. As the frequency increases, some polarization mechanisms may not have enough time to respond, leading to a decrease in the dielectric constant.
Temperature
Temperature can also affect the dielectric constant of a PCB substrate material. As temperature increases, the thermal agitation of the molecules increases, which can lead to changes in the material’s polarizability and, consequently, its dielectric constant. The effect of temperature on dielectric constant varies depending on the material composition.
Moisture Content
Moisture absorption can significantly impact the dielectric constant of a PCB substrate material. Water has a much higher dielectric constant (approximately 80) compared to most PCB materials. As the substrate absorbs moisture, its effective dielectric constant increases, which can lead to changes in the board’s electrical performance.
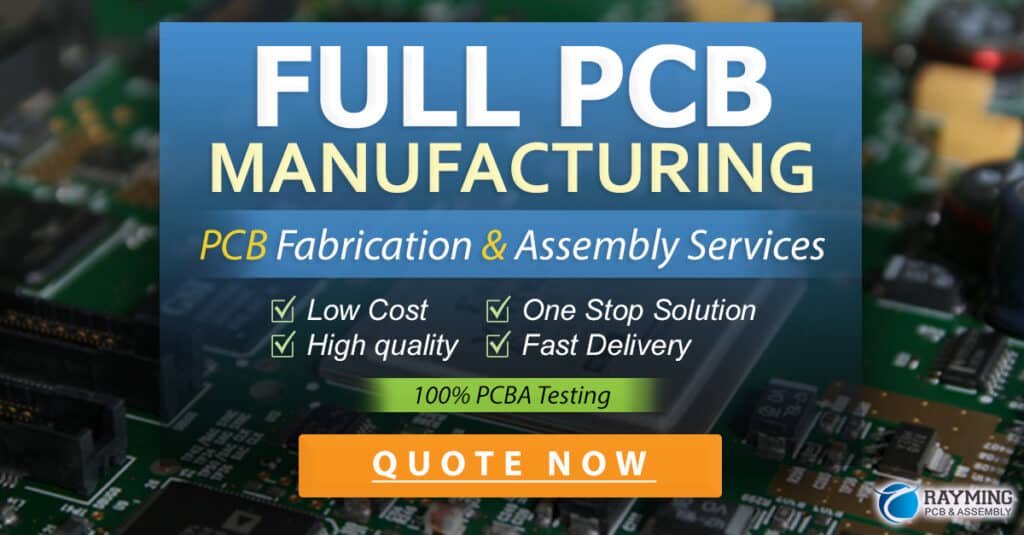
Measuring PCB Dielectric Constant
Accurately measuring the dielectric constant of a PCB substrate is crucial for designing and manufacturing high-quality boards. There are several methods for determining the dielectric constant, each with its advantages and limitations.
Parallel Plate Capacitor Method
The parallel plate capacitor method involves sandwiching the dielectric material between two conductive plates and measuring the capacitance. The dielectric constant can be calculated using the following equation:
Dk = (C × d) / (ε₀ × A)
Where:
– C is the measured capacitance
– d is the thickness of the dielectric material
– A is the area of the conductive plates
This method is simple and straightforward but requires precise thickness and area measurements.
Resonance Method
The resonance method involves creating a resonant structure, such as a cavity or a ring resonator, using the dielectric material. By measuring the resonant frequency and comparing it to the theoretical value, the dielectric constant can be determined.
This method is more accurate than the parallel plate capacitor method but requires specialized equipment and expertise.
Time Domain Reflectometry (TDR)
Time Domain Reflectometry (TDR) is a technique that involves sending a fast-rising voltage step through a transmission line and measuring the reflected signal. By analyzing the reflected signal, the dielectric constant of the PCB substrate can be determined.
TDR is a non-destructive method that can provide accurate results, but it requires specialized equipment and expertise.
Impact of Dielectric Constant on PCB Performance
The dielectric constant of a PCB substrate material has a significant impact on the board’s electrical performance, particularly at high frequencies.
Signal Propagation Speed
The signal propagation speed in a PCB is inversely proportional to the square root of the dielectric constant. A lower dielectric constant results in faster signal propagation, which is essential for high-speed applications.
The signal propagation speed (v) can be calculated using the following equation:
v = c / √(Dk)
Where:
– c is the speed of light in vacuum (3 × 10⁸ m/s)
– Dk is the dielectric constant of the substrate material
Characteristic Impedance
The characteristic impedance (Z₀) of a PCB transmission line is dependent on the dielectric constant of the substrate material. A lower dielectric constant results in a higher characteristic impedance, which is desirable for maintaining signal integrity and reducing reflections.
The characteristic impedance can be calculated using the following equation for a microstrip transmission line:
Z₀ = (87 / √(Dk + 1.41)) × ln(5.98 × h / (0.8 × w + t))
Where:
– h is the thickness of the dielectric material
– w is the width of the microstrip trace
– t is the thickness of the microstrip trace
Capacitance
The dielectric constant directly affects the capacitance of a PCB. A higher dielectric constant results in higher capacitance, which can lead to increased crosstalk and signal distortion.
The capacitance (C) between two parallel traces can be calculated using the following equation:
C = (ε₀ × Dk × A) / d
Where:
– A is the area of the overlapping traces
– d is the distance between the traces
Signal Integrity
Signal integrity refers to the ability of a signal to maintain its original shape and timing as it propagates through a PCB. A lower dielectric constant helps maintain signal integrity by reducing signal distortion, attenuation, and reflections.
Electromagnetic Compatibility (EMC)
Electromagnetic compatibility (EMC) is the ability of a PCB to function properly in its electromagnetic environment without causing or being susceptible to electromagnetic interference. A lower dielectric constant can help improve EMC by reducing the coupling between traces and minimizing electromagnetic radiation.
PCB Material Selection
Selecting the appropriate PCB substrate material is crucial for achieving the desired electrical performance and meeting the specific requirements of an application. When choosing a material, designers must consider several factors, including:
- Dielectric constant
- Dissipation factor (loss tangent)
- Thermal stability
- Mechanical properties
- Cost
Some common PCB substrate materials and their characteristics include:
FR-4
FR-4 is a popular and cost-effective PCB substrate material made from woven fiberglass cloth impregnated with epoxy resin. It has a dielectric constant of 4.2 to 4.5, making it suitable for general-purpose applications up to a few gigahertz.
Rogers RO4003C
Rogers RO4003C is a high-performance laminate material designed for high-frequency applications. It has a dielectric constant of 3.38 and a low dissipation factor, making it ideal for applications up to 20 GHz.
Rogers RT/duroid 5880
Rogers RT/duroid 5880 is a PTFE-based laminate material with a low dielectric constant of 2.20. It is suitable for high-frequency applications up to 40 GHz and offers excellent thermal stability and low moisture absorption.
Isola IS410
Isola IS410 is a low-loss, high-speed laminate material with a dielectric constant of 3.65. It is designed for applications up to 10 GHz and offers good thermal stability and mechanical properties.
Conclusion
The dielectric constant of a PCB substrate material is a critical parameter that significantly affects the electrical performance and signal integrity of a PCB, especially at high frequencies. Understanding the factors that influence the dielectric constant, such as material composition, frequency, temperature, and moisture content, is essential for selecting the appropriate material for a specific application.
Designers must carefully consider the dielectric constant, along with other material properties, when choosing a PCB substrate to ensure optimal performance, reliability, and cost-effectiveness.
FAQ
What is the difference between dielectric constant and dissipation factor?
The dielectric constant (Dk) is a measure of a material’s ability to store electrical energy in an electric field, while the dissipation factor (Df) is a measure of the material’s loss or energy dissipation. A low dielectric constant is desirable for high-speed and high-frequency applications, while a low dissipation factor is essential for minimizing signal attenuation and maintaining signal integrity.
Can the dielectric constant of a PCB change over time?
Yes, the dielectric constant of a PCB substrate material can change over time due to various factors, such as moisture absorption, thermal aging, and exposure to harsh environments. These changes can lead to variations in the board’s electrical performance and signal integrity.
How does the dielectric constant affect the impedance of a PCB trace?
The dielectric constant of the PCB substrate material directly affects the characteristic impedance of a PCB trace. A lower dielectric constant results in a higher characteristic impedance, which is desirable for maintaining signal integrity and reducing reflections. The characteristic impedance also depends on the geometry of the trace, such as its width and thickness.
What is the typical dielectric constant of FR-4?
FR-4 is a popular and cost-effective PCB substrate material made from woven fiberglass cloth impregnated with epoxy resin. It has a dielectric constant ranging from 4.2 to 4.5, making it suitable for general-purpose applications up to a few gigahertz.
How can I measure the dielectric constant of a PCB substrate?
There are several methods for measuring the dielectric constant of a PCB substrate, including the parallel plate capacitor method, resonance method, and Time Domain Reflectometry (TDR). Each method has its advantages and limitations, and the choice depends on factors such as accuracy, equipment availability, and material properties. Accurate measurement of the dielectric constant is crucial for designing and manufacturing high-quality PCBs.
Leave a Reply