Introduction to CTI Value in PCB
In the world of printed circuit board (PCB) manufacturing, various factors contribute to the overall quality and reliability of the final product. One critical aspect that designers and manufacturers need to consider is the Comparative Tracking Index (CTI) value. The CTI value is a measure of a material’s ability to resist electrical tracking and maintain its insulating properties under challenging environmental conditions.
What is Comparative Tracking Index (CTI)?
The Comparative Tracking Index (CTI) is a standardized method for evaluating the electrical tracking resistance of insulating materials used in PCBs. Electrical tracking occurs when a conductive path forms on the surface of an insulating material due to the degradation caused by electrical stress, moisture, and contamination. This phenomenon can lead to short circuits, arcing, and potential safety hazards.
The CTI value is determined through a series of tests outlined in the IEC 60112 standard. The test involves applying a voltage across a specified distance on the surface of the insulating material while gradually increasing the voltage until tracking occurs. The CTI value is expressed as a numerical value, with higher numbers indicating better resistance to electrical tracking.
Importance of CTI Value in PCB Design and Manufacturing
Considering the CTI value during PCB design and manufacturing is crucial for several reasons:
-
Safety: High CTI values ensure that the insulating materials used in PCBs can withstand electrical stress and maintain their insulating properties, reducing the risk of short circuits, arcing, and potential fire hazards.
-
Reliability: PCBs with appropriate CTI values are less likely to experience premature failure due to electrical tracking, thereby improving the overall reliability of the electronic device.
-
Environmental factors: The CTI value takes into account the material’s resistance to environmental factors such as humidity, dust, and pollutants, which can affect the insulating properties of the PCB over time.
-
Compliance: Many industries have specific requirements for the minimum CTI values of insulating materials used in PCBs. Adhering to these standards is essential for ensuring compliance and meeting customer expectations.
CTI Categories and Material Selection
The IEC 60112 standard defines several categories of CTI values, each corresponding to a specific range of tracking resistance. The table below shows the CTI categories and their respective ranges:
CTI Category | CTI Range |
---|---|
0 | <400 |
1 | 400-599 |
2 | 600-799 |
3 | 800-999 |
4 | 1000-1199 |
5 | 1200+ |
When selecting materials for PCB manufacturing, it is essential to choose those with CTI values appropriate for the intended application and environmental conditions. Some commonly used materials and their typical CTI values are:
Material | Typical CTI Value |
---|---|
FR-4 (Flame Retardant 4) | 175-300 |
Polyimide | 300-600 |
Epoxy | 300-500 |
Ceramic | 600+ |
Factors Affecting CTI Value
Several factors can influence the CTI value of insulating materials used in PCBs:
-
Material composition: The chemical composition and additives used in the insulating material can impact its tracking resistance. For example, adding flame retardants or fillers can enhance the CTI value.
-
Manufacturing process: The manufacturing process, including curing temperature, pressure, and duration, can affect the material’s CTI value. Proper process control is essential for achieving consistent CTI values across production batches.
-
Surface contamination: Contamination on the surface of the insulating material, such as dust, moisture, or chemical residues, can reduce its CTI value. Proper handling, storage, and cleaning procedures can help maintain the material’s tracking resistance.
-
Aging and environmental exposure: Prolonged exposure to harsh environmental conditions, such as high humidity, temperature fluctuations, and UV radiation, can degrade the insulating material’s CTI value over time. Selecting materials with appropriate CTI values and implementing protective measures can help mitigate these effects.
Designing PCBs with Appropriate CTI Values
When designing PCBs, it is crucial to consider the CTI value requirements for the specific application and operating environment. The following guidelines can help ensure the selection of appropriate CTI values:
-
Identify the application requirements: Determine the expected operating conditions, such as voltage levels, environmental factors, and safety standards applicable to the end product.
-
Consult industry standards: Refer to relevant industry standards, such as IPC-4101, IEC 60664-1, and UL 746A, for guidance on minimum CTI values for various applications and voltage levels.
-
Consider the operating environment: Evaluate the expected environmental conditions, including humidity, temperature, and the presence of contaminants, and select materials with CTI values that can withstand these conditions.
-
Collaborate with PCB manufacturers: Work closely with PCB manufacturers to discuss CTI value requirements and ensure that the selected materials and manufacturing processes can achieve the desired tracking resistance.
-
Conduct testing and validation: Perform CTI testing on prototype PCBs to validate the material selection and design choices. This can help identify potential issues early in the development process and allow for necessary adjustments.
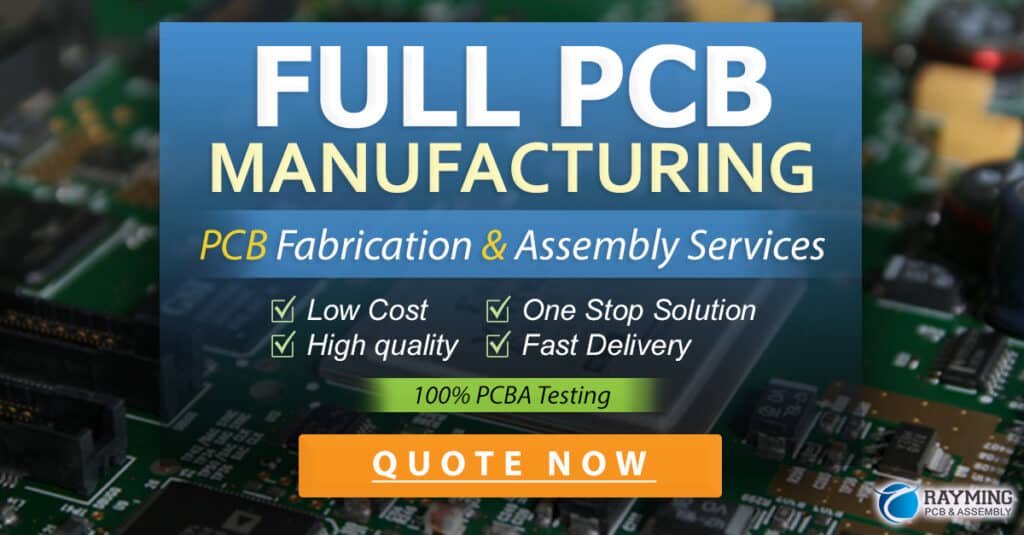
Frequently Asked Questions (FAQs)
1. What is the difference between CTI and PTI?
CTI (Comparative Tracking Index) and PTI (Proof Tracking Index) are both measures of a material’s resistance to electrical tracking, but they differ in the test methods used. CTI is determined using a standardized test method (IEC 60112), where the voltage is gradually increased until tracking occurs. PTI, on the other hand, involves applying a constant voltage for an extended period to determine the material’s tracking resistance over time.
2. Can the CTI value of a material change over time?
Yes, the CTI value of a material can change over time due to factors such as aging, environmental exposure, and surface contamination. Prolonged exposure to harsh conditions, such as high humidity or temperature fluctuations, can degrade the material’s tracking resistance. Proper handling, storage, and maintenance can help preserve the material’s CTI value.
3. How does the CTI value affect the safety of a PCB?
The CTI value is an essential factor in ensuring the safety of a PCB. Higher CTI values indicate better resistance to electrical tracking, which reduces the risk of short circuits, arcing, and potential fire hazards. By selecting materials with appropriate CTI values for the intended application and operating environment, designers can minimize safety risks and improve the overall reliability of the electronic device.
4. What are the consequences of using a material with an insufficient CTI value?
Using a material with an insufficient CTI value can lead to several negative consequences, including:
- Increased risk of electrical tracking, short circuits, and arcing
- Premature failure of the PCB due to degradation of insulating properties
- Potential safety hazards, such as fire or electric shock
- Non-compliance with industry standards and customer requirements
It is crucial to select materials with appropriate CTI values to mitigate these risks and ensure the long-term reliability and safety of the PCB.
5. How can I determine the required CTI value for my specific application?
To determine the required CTI value for a specific application, consider the following steps:
- Identify the applicable industry standards and regulations for your product, such as IPC, IEC, or UL standards.
- Evaluate the expected operating conditions, including voltage levels, environmental factors, and safety requirements.
- Consult the relevant standards and guidelines for recommendations on minimum CTI values based on the application and voltage levels.
- Engage with PCB manufacturers and material suppliers to discuss your requirements and obtain guidance on suitable materials and CTI values.
- Conduct testing and validation on prototype PCBs to ensure that the selected materials and CTI values meet the desired performance and safety criteria.
Conclusion
The Comparative Tracking Index (CTI) value is a critical factor in the design and manufacturing of high-quality, reliable printed circuit boards. By understanding the importance of CTI and selecting materials with appropriate tracking resistance, designers and manufacturers can ensure the safety, reliability, and compliance of their electronic products.
Considering factors such as the intended application, operating environment, and industry standards, PCB designers can make informed decisions when choosing materials and specifying CTI requirements. Collaborating with PCB manufacturers and conducting thorough testing and validation further enhance the chances of success in creating PCBs that meet the desired performance and safety criteria.
As technology advances and new materials emerge, staying up-to-date with the latest developments in CTI testing and material options is essential for maintaining a competitive edge in the electronics industry. By prioritizing the CTI value in PCB design and manufacturing, companies can deliver high-quality, reliable products that meet customer expectations and regulatory requirements.
Leave a Reply