Introduction to PCB Buildup
PCB (Printed Circuit Board) buildup refers to the process of constructing a multilayer PCB by stacking and laminating multiple layers of conductive and insulating materials. The buildup process allows for the creation of complex and high-density PCBs that can accommodate a large number of components and interconnections in a compact space.
Key Components of PCB Buildup
The PCB buildup process involves several key components:
-
Core Layer: The core layer is the foundation of the PCB and provides structural support. It is typically made of a rigid insulating material such as FR-4 (Flame Retardant-4) or other glass-reinforced epoxy laminates.
-
Copper Layers: Copper layers are the conductive layers that carry electrical signals and power throughout the PCB. They are typically made of thin sheets of copper foil that are laminated onto the core layer and other insulating layers.
-
Insulating Layers: Insulating layers, also known as dielectric layers, are used to separate and isolate the copper layers from each other. They are made of non-conductive materials such as FR-4, prepreg (pre-impregnated fiberglass), or other polymer-based materials.
-
Vias: Vias are small holes drilled through the PCB layers to create electrical connections between different layers. They can be either through-hole vias that go through the entire thickness of the board or blind/buried vias that connect only certain layers.
-
Solder Mask: The solder mask is a protective layer applied over the outer copper layers to prevent accidental short circuits and improve the PCB’s durability. It also provides a surface for printing component labels and other markings.
-
Silkscreen: The silkscreen is a layer of text and symbols printed on the PCB surface to provide information about component placement, orientation, and other important details.
PCB Buildup Process
The PCB buildup process involves several steps that are carefully controlled to ensure the quality and reliability of the final product. Here’s an overview of the typical PCB buildup process:
Step 1: Core Layer Preparation
The core layer is the starting point of the PCB buildup process. It is typically a pre-fabricated board made of FR-4 or other suitable material. The core layer is drilled with holes for through-hole components and vias.
Step 2: Copper Deposition
The next step is to deposit a thin layer of copper onto the core layer. This is typically done using electroless copper plating, where the board is immersed in a copper solution and the copper is deposited onto the surface through a chemical reaction.
Step 3: Patterning and Etching
Once the copper layer is deposited, it needs to be patterned to create the desired circuit traces. This is typically done using photolithography, where a photoresist layer is applied onto the copper and exposed to light through a patterned mask. The exposed areas of the photoresist are then developed and removed, leaving the desired copper pattern. The unwanted copper is then etched away using a chemical etching process.
Step 4: Insulating Layer Lamination
After the copper layer is patterned and etched, an insulating layer is laminated onto the surface. This is typically done using prepreg, which is a pre-impregnated fiberglass material that is heated and pressed onto the board under high pressure.
Step 5: Via Drilling and Plating
Once the insulating layer is laminated, holes are drilled through the board to create vias that connect the different layers. The vias are then plated with copper to create electrical connections between the layers.
Step 6: Outer Layer Copper Deposition and Patterning
The outer copper layers are then deposited and patterned using the same process as the inner layers. This typically involves copper plating, photolithography, and etching.
Step 7: Solder Mask and Silkscreen Application
After the outer copper layers are patterned, a solder mask is applied to protect the copper and prevent short circuits. The solder mask is typically applied using a screen printing process and then cured using UV light or heat.
The silkscreen layer is then applied onto the solder mask to provide component labels and other markings. This is typically done using a screen printing process with a special ink that adheres to the solder mask.
Step 8: Surface Finish Application
The final step in the PCB buildup process is to apply a surface finish to the exposed copper areas. This is done to protect the copper from oxidation and improve solderability. Common surface finishes include HASL (Hot Air Solder Leveling), ENIG (Electroless Nickel Immersion Gold), and OSP (Organic Solderability Preservative).
Types of PCB Buildup
There are several types of PCB buildup that are used depending on the specific requirements of the application. Here are some of the most common types of PCB buildup:
1. Through-Hole Technology (THT)
Through-hole technology is the traditional method of PCB fabrication where components are inserted into holes drilled through the board and soldered onto the opposite side. THT is suitable for larger components and provides good mechanical stability, but it has limitations in terms of component density and signal integrity.
2. Surface Mount Technology (SMT)
Surface mount technology is a more modern method of PCB fabrication where components are mounted directly onto the surface of the board without the need for through-holes. SMT allows for higher component density and better signal integrity, but it requires more precise manufacturing processes and is more sensitive to thermal and mechanical stresses.
3. Mixed Technology
Mixed technology PCBs combine both THT and SMT components on the same board. This allows for the use of larger through-hole components for power and mechanical stability, while still taking advantage of the higher density and signal integrity of SMT components.
4. High Density Interconnect (HDI)
High density interconnect PCBs use advanced manufacturing techniques to create very fine pitch traces and vias, allowing for extremely high component density and signal integrity. HDI PCBs typically use microvias, which are very small vias that only connect a few layers, and buried or blind vias that do not go through the entire board thickness.
5. Flexible PCBs
Flexible PCBs use a flexible substrate material instead of the traditional rigid FR-4. This allows the PCB to bend and flex without breaking, making it suitable for applications where the board needs to conform to a curved or irregular surface. Flexible PCBs can be single-sided, double-sided, or multilayer, and can also be combined with rigid sections to create rigid-flex PCBs.
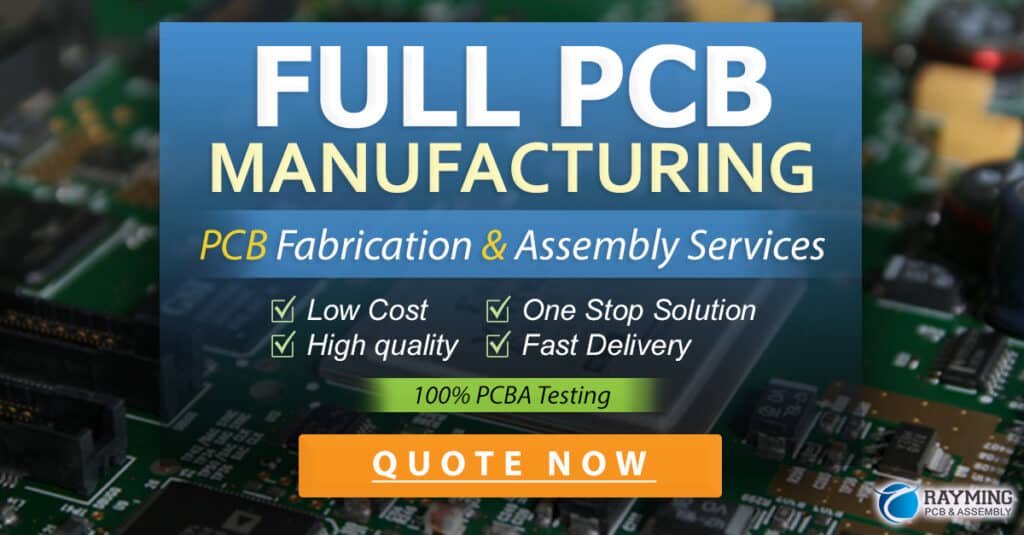
Benefits of PCB Buildup
PCB buildup offers several benefits over traditional PCB fabrication methods. Here are some of the key benefits of PCB buildup:
1. Higher Density
PCB buildup allows for much higher component density than traditional methods. By using smaller vias and finer pitch traces, designers can pack more components and functionality into a smaller space. This is particularly important for applications where size and weight are critical, such as in mobile devices and aerospace electronics.
2. Better Signal Integrity
PCB buildup allows for better control over signal integrity by using shorter trace lengths and reducing the number of vias. This helps to minimize signal reflections, crosstalk, and other sources of signal degradation, resulting in cleaner and more reliable signals.
3. Improved Thermal Management
PCB buildup allows for better thermal management by using thinner dielectric layers and more efficient heat spreading techniques. This helps to dissipate heat more effectively and prevent hot spots from forming on the board, which can lead to component failure and reliability issues.
4. Lower Cost
Although PCB buildup requires more advanced manufacturing processes and equipment, it can actually be more cost-effective than traditional methods in the long run. By reducing the size and weight of the board, designers can save on materials and shipping costs. Additionally, the improved reliability and performance of PCB buildup can help to reduce maintenance and repair costs over the lifetime of the product.
Challenges of PCB Buildup
Despite the many benefits of PCB buildup, there are also some challenges and limitations that designers need to be aware of. Here are some of the key challenges of PCB buildup:
1. Manufacturing Complexity
PCB buildup requires more advanced manufacturing processes and equipment than traditional methods. This can make it more challenging and expensive to manufacture, particularly for smaller quantities or prototype runs. Designers need to work closely with their manufacturing partners to ensure that the design is optimized for manufacturability and that the necessary processes and equipment are available.
2. Material Selection
PCB buildup requires careful selection of materials to ensure compatibility and reliability. The dielectric materials used in the buildup layers need to have the right electrical and thermal properties, while also being able to withstand the high temperatures and pressures of the lamination process. Copper foils also need to be carefully selected to ensure good adhesion and conductivity.
3. Via Reliability
Vias are a critical component of PCB buildup, but they can also be a source of reliability issues if not designed and manufactured properly. Microvias in particular can be prone to cracking or delamination if the aspect ratio is too high or the via is not properly filled with conductive material. Designers need to follow best practices for via design and work with their manufacturing partners to ensure that the vias are reliable and robust.
4. Signal Integrity Challenges
Although PCB buildup can improve signal integrity in many ways, it can also introduce new challenges related to impedance control, crosstalk, and electromagnetic interference (EMI). Designers need to carefully simulate and optimize the signal paths to ensure that they meet the required performance specifications, while also complying with relevant EMI and safety standards.
PCB Buildup Design Considerations
When designing a PCB using the buildup process, there are several key considerations that designers need to keep in mind. Here are some of the most important PCB buildup design considerations:
1. Layer Stack-up
The layer stack-up is a critical aspect of PCB buildup design, as it determines the number and arrangement of copper and dielectric layers in the board. Designers need to carefully choose the number of layers based on the complexity of the circuit and the required signal integrity and power distribution. They also need to specify the thickness and material properties of each layer to ensure compatibility and reliability.
2. Via Design
Via design is another critical aspect of PCB buildup, as it determines the electrical and mechanical properties of the interconnects between layers. Designers need to choose the appropriate via types (through-hole, blind, buried, or microvia) based on the layer stack-up and signal requirements. They also need to specify the via size, pitch, and pad size to ensure good manufacturability and reliability.
3. Impedance Control
Impedance control is essential for high-speed digital circuits to ensure good signal integrity and minimize reflections and crosstalk. Designers need to carefully choose the trace width, spacing, and dielectric thickness to achieve the desired characteristic impedance (typically 50 or 100 ohms). They also need to use appropriate termination and matching techniques to minimize signal distortion and ensure good power transfer.
4. Power Distribution
Power distribution is another important consideration in PCB buildup design, as it determines the voltage and current supplied to each component on the board. Designers need to carefully choose the power and ground plane layers and the decoupling capacitors to ensure good power integrity and minimize noise and ripple. They also need to use appropriate via stitching and copper balancing techniques to ensure good current distribution and prevent voltage drops.
5. Thermal Management
Thermal management is critical in PCB buildup design, as the high component density and power dissipation can lead to hot spots and reliability issues. Designers need to carefully choose the board materials and layer stack-up to ensure good thermal conductivity and heat spreading. They also need to use appropriate heat sinking and cooling techniques, such as thermal vias, copper planes, and heat spreaders, to dissipate heat effectively and prevent component failures.
FAQ
1. What is the difference between PCB buildup and traditional PCB fabrication?
PCB buildup is a more advanced fabrication process that allows for higher component density, better signal integrity, and improved thermal management compared to traditional methods. It involves stacking and laminating multiple layers of copper and dielectric materials, using smaller vias and finer pitch traces to achieve higher interconnect density.
2. What are the key benefits of PCB buildup?
The key benefits of PCB buildup include higher component density, better signal integrity, improved thermal management, and lower cost in the long run. By using advanced manufacturing processes and materials, designers can create more compact and reliable boards that meet the demanding requirements of modern electronics applications.
3. What are the challenges of PCB buildup?
The main challenges of PCB buildup include manufacturing complexity, material selection, via reliability, and signal integrity. PCB buildup requires more advanced equipment and processes, and designers need to carefully choose the right materials and optimize the design for manufacturability and reliability.
4. What are the key design considerations for PCB buildup?
The key design considerations for PCB buildup include layer stack-up, via design, impedance control, power distribution, and thermal management. Designers need to carefully choose the number and arrangement of layers, the via types and sizes, the trace widths and spacings, the power and ground planes, and the heat sinking and cooling techniques to ensure good performance and reliability.
5. What are the different types of PCB buildup?
The main types of PCB buildup include through-hole technology (THT), surface mount technology (SMT), mixed technology, high density interconnect (HDI), and flexible PCBs. Each type has its own advantages and limitations, and designers need to choose the appropriate type based on the specific requirements of the application.
Leave a Reply