What is a Surface-Mount PCB?
A surface-mount PCB is a printed circuit board designed to accommodate surface-mount devices (SMDs). SMDs are electronic components that are soldered directly onto the surface of the PCB, rather than being inserted through holes like through-hole components. This design allows for a more compact and efficient use of space on the PCB, enabling the creation of smaller and more complex electronic devices.
Advantages of Surface-Mount PCBs
Surface-mount PCBs offer several advantages over their through-hole counterparts:
-
Miniaturization: SMDs are significantly smaller than through-hole components, allowing for more components to be placed on a single PCB. This leads to smaller, more compact electronic devices.
-
Increased Functionality: With the ability to accommodate more components, surface-mount PCBs can support more complex and sophisticated electronic functions.
-
Improved Performance: SMDs have shorter lead lengths, reducing the risk of signal interference and improving overall circuit performance.
-
Cost-Effective: The automated assembly process for surface-mount PCBs is faster and more efficient, reducing manufacturing costs.
-
Reliability: Surface-mount PCBs are more resistant to vibration and mechanical stress, enhancing their reliability in various applications.
Surface-Mount Components
Surface-mount components come in a variety of package types, each designed to meet specific requirements. Some common SMD package types include:
Package Type | Description |
---|---|
Resistors | Small, rectangular components with two terminals, used to control current flow. |
Capacitors | Components that store electrical energy, available in various sizes and shapes. |
Inductors | Passive components that store energy in a magnetic field, used for filtering and power management. |
Diodes | Semiconductor devices that allow current to flow in only one direction. |
Transistors | Semiconductor devices used for amplification and switching, available in various package types. |
Integrated Circuits (ICs) | Complex circuits containing multiple components, available in a range of package types such as SOICs, QFNs, and BGAs. |
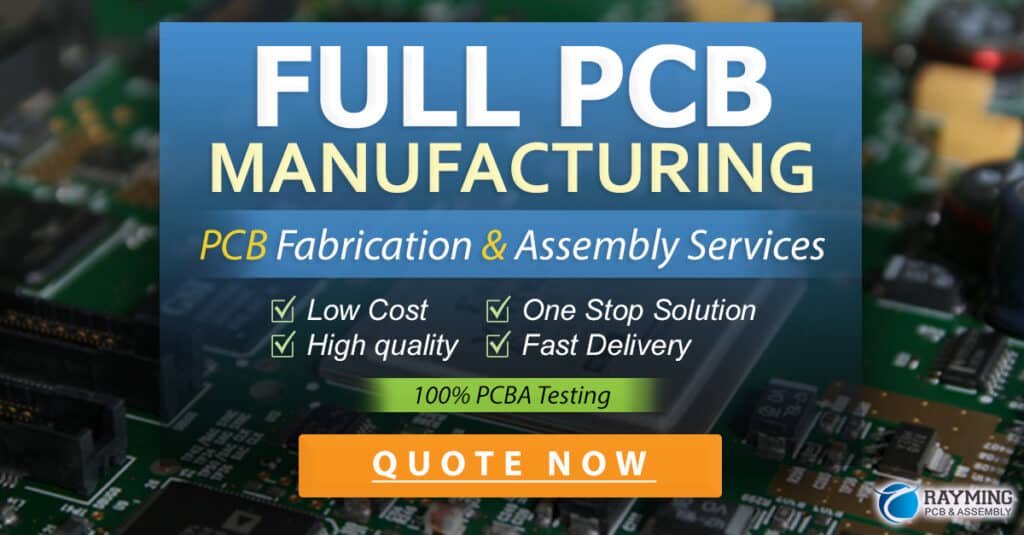
Surface-Mount PCB Manufacturing Process
The manufacturing process for surface-mount PCBs involves several key steps:
-
PCB Design: The circuit is designed using electronic design automation (EDA) software, which generates the necessary files for manufacturing.
-
PCB Fabrication: The bare PCB is fabricated using a multi-step process that includes printing the circuit pattern, etching, and applying a protective solder mask.
-
Solder Paste Application: A precise amount of solder paste is applied to the PCB’s surface using a stencil or screen printing technique.
-
Component Placement: SMDs are placed onto the solder paste using automated pick-and-place machines, ensuring accurate positioning.
-
Reflow Soldering: The PCB is heated in a reflow oven, melting the solder paste and forming a permanent electrical and mechanical connection between the components and the PCB.
-
Inspection and Testing: The assembled PCB undergoes visual inspection and electrical testing to ensure proper functionality and quality control.
Surface-Mount Soldering Techniques
There are two primary techniques used for soldering surface-mount components:
-
Reflow Soldering: This is the most common method for surface-mount PCB assembly. The PCB is heated in a reflow oven, causing the solder paste to melt and form a connection between the components and the PCB.
-
Wave Soldering: Although less common for surface-mount PCBs, wave soldering can be used for mixed-technology boards that contain both surface-mount and through-hole components. The PCB is passed over a wave of molten solder, which selectively solders the components to the board.
Design Considerations for Surface-Mount PCBs
When designing a surface-mount PCB, several factors must be considered to ensure optimal performance and manufacturability:
-
Component Selection: Choose SMDs that are compatible with the PCB’s design and manufacturing process, considering factors such as package type, size, and thermal requirements.
-
Footprint Design: Create accurate and standardized footprints for each SMD, ensuring proper spacing and alignment for efficient assembly.
-
Thermal Management: Consider the thermal requirements of the components and design the PCB to effectively dissipate heat, preventing performance issues and potential damage.
-
Signal Integrity: Minimize signal interference by carefully routing traces and maintaining appropriate spacing between components and traces.
-
Manufacturing Constraints: Ensure that the PCB design adheres to the capabilities and limitations of the manufacturing process, such as minimum trace widths and spacing, hole sizes, and solder mask requirements.
Applications of Surface-Mount PCBs
Surface-mount PCBs are used in a wide range of electronic devices and industries, including:
-
Consumer Electronics: Smartphones, tablets, laptops, and wearable devices.
-
Automotive Electronics: Engine control units, infotainment systems, and advanced driver assistance systems (ADAS).
-
Medical Devices: Implantable devices, diagnostic equipment, and patient monitoring systems.
-
Industrial Automation: Sensors, controllers, and communication modules.
-
Aerospace and Defense: Avionics, satellite systems, and military communication devices.
Frequently Asked Questions (FAQ)
-
Q: What is the difference between surface-mount and through-hole PCBs?
A: Surface-mount PCBs use components that are soldered directly onto the surface of the board, while through-hole PCBs use components with leads that are inserted into holes drilled through the board and soldered on the opposite side. -
Q: Can surface-mount and through-hole components be used on the same PCB?
A: Yes, mixed-technology PCBs can incorporate both surface-mount and through-hole components, although this may require additional manufacturing steps and considerations. -
Q: What are the challenges associated with surface-mount PCB assembly?
A: Some challenges include the need for precise component placement, the potential for tombstoning (when a component stands on one end due to uneven solder melting), and the difficulty of manual rework and repair. -
Q: How does the size of surface-mount components affect PCB design?
A: Smaller surface-mount components allow for more compact PCB designs but may require advanced manufacturing capabilities and more stringent design rules to ensure proper assembly and performance. -
Q: What is the role of solder paste in surface-mount PCB assembly?
A: Solder paste is a mixture of tiny solder particles suspended in a flux medium. It is applied to the PCB’s surface before component placement and acts as both an adhesive and a conductive material, forming the electrical and mechanical connection between the components and the PCB during the reflow soldering process.
Surface-mount technology has transformed the electronics industry, enabling the production of smaller, more complex, and more efficient electronic devices. By understanding the principles, components, and manufacturing processes involved in surface-mount PCBs, designers and engineers can create innovative and reliable electronic products that meet the demands of today’s rapidly evolving technological landscape.
Leave a Reply