Introduction to Stacked PCBs
Printed Circuit Boards (PCBs) are essential components in modern electronics, providing a platform for interconnecting electronic components. As technology advances and devices become more compact, the demand for high-density PCBs has increased. One solution to this challenge is the use of stacked PCBs.
What are Stacked PCBs?
Stacked PCBs, also known as multi-layer PCBs, are circuit boards that consist of multiple layers of conductive and insulating materials laminated together. These layers are interconnected through vias, which are small holes drilled through the board and plated with conductive material. By stacking multiple layers, designers can create more complex circuits in a smaller footprint, increasing the density and functionality of the PCB.
Advantages of Stacked PCBs
Stacked PCBs offer several advantages over single-layer boards:
- Increased Density: By stacking multiple layers, more components and traces can be accommodated in a smaller area, resulting in higher-density PCBs.
- Improved Signal Integrity: The use of ground and power planes in stacked PCBs helps to reduce electromagnetic interference (EMI) and improve signal integrity.
- Enhanced Thermal Management: Stacked PCBs allow for better heat dissipation through the use of thermal vias and dedicated cooling layers.
- Reduced Size and Weight: Stacking layers enables designers to create smaller and lighter PCBs, which is crucial for applications such as mobile devices and wearables.
PCB Stacking Techniques
There are several techniques used to stack PCB layers, each with its own advantages and limitations.
Multilayer PCBs
Multilayer PCBs are the most common type of stacked PCBs. They consist of multiple layers of copper foil separated by insulating material, typically FR-4. The layers are laminated together using heat and pressure, and the vias are drilled and plated to create interconnections between the layers.
Layers | Typical Applications |
---|---|
2-4 | Simple circuits, low-density designs |
6-8 | Moderate complexity, medium-density designs |
10-12 | High complexity, high-density designs |
14+ | Very high complexity, ultra-high-density designs |
HDI PCBs
High-Density Interconnect (HDI) PCBs are a type of stacked PCB that uses advanced manufacturing techniques to achieve even higher densities. HDI PCBs employ smaller vias, finer traces, and blind and buried vias to maximize the use of available space.
Feature | Conventional PCB | HDI PCB |
---|---|---|
Via Size | 0.3-0.5 mm | 0.1-0.2 mm |
Trace Width/Spacing | 0.1-0.15 mm | 0.05-0.1 mm |
Layers | 2-14 | 4-28 |
Rigid-Flex PCBs
Rigid-Flex PCBs combine rigid and flexible substrates in a single board. The rigid sections provide structural support and house most of the components, while the flexible sections allow the board to bend and fold, enabling unique form factors and improved reliability in applications subject to vibration or mechanical stress.
PCB Stacking Design Considerations
When designing stacked PCBs, several factors must be considered to ensure optimal performance and manufacturability.
Layer Stack-Up
The layer stack-up refers to the arrangement of conductive and insulating layers in a stacked PCB. Proper layer stack-up design is crucial for maintaining signal integrity, controlling impedance, and minimizing EMI. A typical 4-layer stack-up might consist of the following layers:
- Top Layer: Signal traces and components
- Ground Plane: Provides a low-impedance return path for signals
- Power Plane: Distributes power to components
- Bottom Layer: Signal traces and components
Via Types and Placement
Vias are essential for interconnecting layers in stacked PCBs. There are three main types of vias:
- Through Vias: Drilled through the entire board, connecting all layers
- Blind Vias: Connect an outer layer to an inner layer, but do not go through the entire board
- Buried Vias: Connect inner layers without reaching the outer layers
Via placement is critical for maintaining signal integrity and minimizing inductance. Vias should be placed as close to the components as possible, and their size and spacing should be carefully considered to avoid manufacturing issues.
Thermal Management
Stacked PCBs can generate significant heat due to the high density of components and traces. Proper thermal management is essential to ensure reliable operation and prevent premature failure. Techniques for improving thermal management in stacked PCBs include:
- Thermal Vias: Vias filled with thermally conductive material to transfer heat away from components
- Dedicated Cooling Layers: Layers designed specifically for heat dissipation, such as metal core PCBs
- Thermal Interface Materials: Materials applied between components and the PCB to enhance heat transfer
Signal Integrity and EMI
Maintaining signal integrity and minimizing EMI are critical challenges in stacked PCB design. High-speed signals can suffer from crosstalk, reflections, and other issues that can degrade performance. To mitigate these problems, designers can employ techniques such as:
- Controlled Impedance: Designing traces with specific impedance characteristics to minimize reflections
- Differential Signaling: Using paired traces with opposite polarity to cancel out EMI
- Shielding: Implementing ground planes and shielding cans to reduce EMI
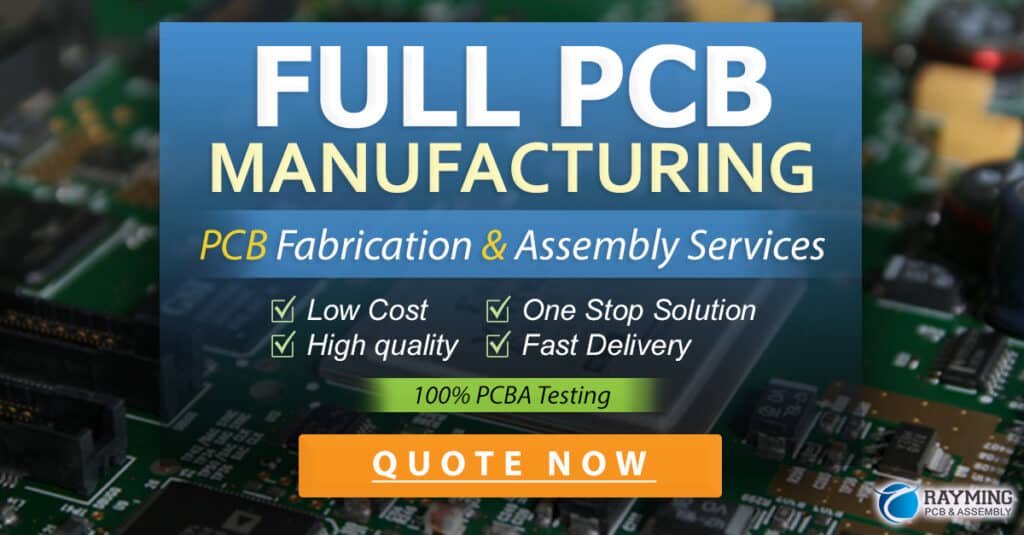
Manufacturing Considerations
Stacked PCBs require specialized manufacturing processes and equipment to ensure reliable and consistent results.
Lamination
The lamination process involves combining the individual layers of the PCB using heat and pressure. Proper lamination is crucial for ensuring good adhesion between layers and preventing delamination, which can lead to reliability issues.
Drilling and Plating
Drilling and plating vias is a critical step in stacked PCB manufacturing. The vias must be drilled accurately and plated with a sufficient thickness of conductive material to ensure reliable interconnections between layers. Improper drilling or plating can result in open or short circuits, compromising the functionality of the PCB.
Inspection and Testing
Thorough inspection and testing are essential for ensuring the quality and reliability of stacked PCBs. Automated optical inspection (AOI) systems can detect surface defects, while electrical testing can verify the continuity and isolation of the interconnections. Additional tests, such as thermal cycling and vibration testing, may be necessary for applications with demanding environmental requirements.
Frequently Asked Questions (FAQ)
1. What is the difference between stacked and multilayer PCBs?
Stacked PCBs and multilayer PCBs are often used interchangeably, as both refer to PCBs with multiple layers of conductive and insulating materials. However, some professionals use “stacked PCB” to refer specifically to boards with a very high layer count or those that use advanced techniques like HDI or rigid-flex construction.
2. How many layers can a stacked PCB have?
The number of layers in a stacked PCB can vary widely depending on the application and manufacturing capabilities. Typical multilayer PCBs can have anywhere from 4 to 14 layers, while advanced HDI boards can have up to 28 layers or more.
3. What are the challenges in designing stacked PCBs?
Designing stacked PCBs presents several challenges, including maintaining signal integrity, controlling impedance, minimizing EMI, and ensuring proper thermal management. Designers must also consider manufacturability factors, such as via placement and layer stack-up, to ensure the board can be reliably produced.
4. Are stacked PCBs more expensive than single-layer boards?
Yes, stacked PCBs are generally more expensive than single-layer boards due to the additional materials, processing steps, and specialized equipment required for their manufacture. However, the increased functionality and performance offered by stacked PCBs often justify the higher cost in applications that demand high density and reliability.
5. What industries commonly use stacked PCBs?
Stacked PCBs are used in a wide range of industries, including:
- Consumer electronics (smartphones, tablets, wearables)
- Automotive (infotainment systems, sensors, control modules)
- Medical devices (implantables, diagnostic equipment)
- Aerospace and defense (avionics, communications systems)
- Industrial automation (robots, control systems)
Conclusion
Stacked PCBs are a crucial technology for meeting the ever-increasing demands for high-density, high-performance electronics. By combining multiple layers of conductive and insulating materials, stacked PCBs enable designers to create complex circuits in a compact form factor, improving functionality and reliability.
However, designing and manufacturing stacked PCBs presents unique challenges that require careful consideration of factors such as layer stack-up, via placement, signal integrity, and thermal management. By understanding these challenges and employing appropriate design and manufacturing techniques, engineers can successfully leverage the benefits of stacked PCBs in a wide range of applications.
As electronic devices continue to evolve and push the boundaries of performance and functionality, the use of stacked PCBs will likely become even more prevalent. By staying up-to-date with the latest advancements in PCB stacking technology, designers and manufacturers can remain at the forefront of this exciting field and create innovative solutions for the electronics of tomorrow.
Leave a Reply